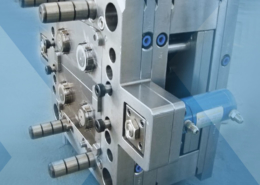
Injection Molding Services for Custom Parts - plastic injection molding part
Author:gly Date: 2024-10-15
Aluminum evenly dissipates heat, which provides dimensional stability in tooling. This significantly reduces deformation and produces less waste during the production process. It is important to note that aluminum is not as strong as steel, so it has a shorter life cycle and is less useful in high-volume processes.
Steel is a sturdy, solid, high-quality tooling material, though it is not suitable for all applications. Steel molds have a longer life cycle than aluminum and are therefore ideal for high-volume production. Steel can also be used to produce molds from engineering-grade plastics that are resistant to abrasion and corrosion.
Most thermoplastics can benefit from the use of gas assisted moulding including Polypropylene (PP), ABS, HIPS, Polycarbonate (PC), PPC and Nylon (including glass filled grades).
Developments over the past years in Gas Assisted Moulding or (Gas Assisted Molding to use the US spelling or Gas Injection Moulding being a common reference term) have resulted in advances in the way in which injection moulded components are manufactured. Enhanced quality, reduced cycle times and component weight reductions can be achieved by the process.
Although we had to invest more for the mold, we now save 70% compared with urethane casting, and we can use UV-resistant ABS to keep the color stable. Overall, I am very happy with the solution.
Most plastic injection moulded components can benefit from the use of gas assisted moulding. Applications from consumer goods to automotive parts benefit from the process. External Gas Assisted Moulding Applications:
Though it features multiple benefits, steel is a more expensive tooling material than aluminum and requires more turnaround time to produce molds and prototypes.
At a point in the moulding cycle, the material at the gate feed point solidifies (freezes) precluding any further packing. In thick components the shrinkage of the material from the mould surface is more pronounced.
Every quarter, we order approximately 20 sets of plastic enclosures for our device from 3ERP. The enclosures were initially made by urethane casting, but Ronan came back to me with the idea of using an aluminum mold, which allowed me to get a few hundred moldings. We decided to move to this process. The T1 samples weren’t good enough, as we got some shrink marks, but this was quickly sorted out when we received the T2 samples.
Creating a more efficent mould process During the 'normal' injection moulding process of packing a mould cavity with plastic material, stresses are introduced into the component. Often these are along the line of flow of the packing material. In service these will result in the moulding warping and changing its dimensions. By using the gas medium, transmission of pressure throughout the moulding is more efficient and therefore less pressure is required. By injecting a gas into the material the cavity pressures are lower and being derived from within the component will considerably minimise the risk of warping In addition, with the material being pressed against the mould surface by the gas until it solidifies, the moulding will have better surface definition and will be more likely to be dimensionally correct. Enhanced Surface Definition External gas injection provides an enhanced surface definition of the component. Weight and Cost Reduction The combined benefits of not packing a moulding are less material is used. By not having to pack the material, and in thicker components the resultant hollow core, can save as much as up to 30% on the material used. Another major benefit is the reduction in machine cycle times that can be achieved. With no molten core to solidify, the material in the mould cavity solidifies quicker thus enabling the component to be ejected sooner. Quality Better dimensional control, and increased surface quality are major benefits of using gas injection. Sink marks caused by local thick/thin deviations in wall section can be eliminated.
Two months ago, I was super stressed by an urgent plastic molding project. Our customer desperately wanted 100 sets at very short notice in order to run testing with real materials, even though normal production would have taken more than six months. None of our preferred moldmaking suppliers could help us, given the deadline. Luckily, one of my friends recommended 3ERP to us by chance.
Techniques have been developed whereby inert gas nitrogen is injected into the still molten plastic in the mould cavity. Acting from within the component shape, the gas inflates the component and counteracts the effects of the material shrinkage. The effect is to keep an internal pressure on the material until it solidifies and skins at the mould cavity surface. This is independent of any gate freezing.
3ERP has a fantastic mold design team. They managed to finish the mold design within 10 days and started to fabricate the molds right after that. I was surprised that more than 60 items, including some big parts, were completed to a decent standard within two months. Our customers eventually received the moldings to run their testing. 3ERP saved our business!
For this tail light project, we needed to fabricate a housing, reflector, light guide, bezel, an outer lens, and other components in a short period of time. The overall assembly size was about 600 x 400 x 150 mm, which is relatively large and the customer wanted to test real materials. In this case, 3D printing, CNC machining, and vacuum casting were not suitable, so prototype molding was the only option. Click to view this case
The rapid tooling process involves the creation of a mold using aluminum or soft steel, a stocked mold base, and hand-load inserts. Rapid tooling is one of the best methods for fulfilling small batch orders meant for use in marketing samples, product evaluations, and process design.
An ideal choice for prototyping, aluminum mold tooling provides a cost-effective way to produce molded parts. Since they are easy to cut, aluminum molds can reduce tooling costs by 15–25% compared to other mold materials and reduce cycle times by up to 40%. This translates to a faster turnaround for our customers.
The Cinpres Gas Injection Company have developed a range of gas generation and control equipment to cover any manufacturing need. Some patented process variants are offered under licence.
When cooling, the material shrinks away from the mould cavity surface. To counteract this, more plastic material is injected (packing) into the cavity to try to maintain the surface contact.
Traditional tooling is often prohibitively expensive for small projects. Our custom rapid tooling service is a cost-effective, low-volume alternative in situations where large volumes of the part won’t be needed in the future. The rapid production tooling process is commonly used in industrial settings for prototyping solutions or for diagnosing design issues, providing an easy introduction to mold making.
At 3ERP, we typically create rapid molds by CNC machining and EDM, though we also sometimes use additive methods such as 3D printing technologies.
To mould thermoplastic materials, they have to be heated to their melt temperature and injected into a closed metal mould. Cooling channels built into the mould act to cool the mould and in turn extract heat from the material.
Can you imagine attempting to make prototype tools for over 30 components in just two months? Our customer desperately needed 200-300 sets of tail lights for testing, but mass production tools wouldn’t have been ready for eight months. They needed a solution to get good quality moldings by their deadline and at a much lower cost than production tools.
GETTING A QUOTE WITH LK-MOULD IS FREE AND SIMPLE.
FIND MORE OF OUR SERVICES:
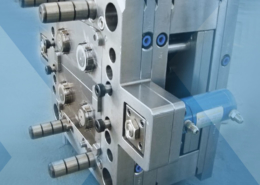
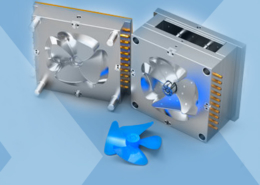
Plastic Molding

Rapid Prototyping
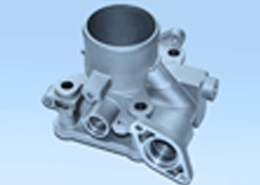
Pressure Die Casting
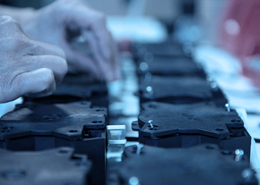
Parts Assembly
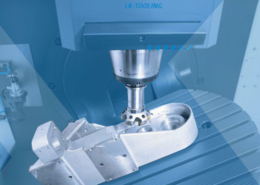