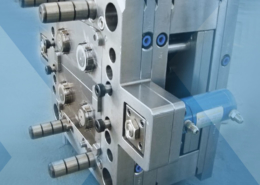
Injection Molding Services for Custom Parts - low cost injection molding
Author:gly Date: 2024-10-15
(3) the temperature control of the working oil must change the high oil temperature, resulting in the fluctuation of injection pressure. We must use the closed loop heating and cooling device to stabilize the oil temperature at 50~55 degrees.
B. PA and glass fiber reinforced PA66, its characteristics: strong impact resistance and wear resistance, good flow performance, can form a 0.4mm wall thickness products. Glass fiber reinforced PA66 has heat resistance (melting point 250 C), its disadvantage is that it is hygroscopic, and it should be humidified after general molding.
No matter what kind of precision injection molding machine, it must be able to control the repeatability accuracy and quality repeatability of the product in a stable way.
The hydraulic system of D. precision injection molding machine should fully reflect the integration of mechanical and electrical apparatus.
The first is the repetition precision of the product size, and the two is the repeatable precision of the product quality.
The mold is demoulding, and the mold should take less cavity number, less and shorter runner as far as possible, and have higher smoothness than ordinary mold, so it is good for demoulding.
360 Quadrants is a scientific research methodology by MarketsandMarkets to understand market leaders in 6000+ micro markets
The precision of the mold mainly depends on the high precision of the mold cavity size, accurate positioning of the cavity or whether the precision of the parting surface meets the requirements. The dimensional tolerances of the general precision injection moulds should be controlled below 1/3 of the dimensional tolerance of the products.
In addition, the barrel temperature should also be accurately controlled, now screw and barrel temperature control by PID (proportional integral differential), the precision can be controlled within l degrees, which can meet the requirements of precision injection molding, if the FUZZY control method is more suitable for precision injection molding.
B. requires the protection of the low pressure die and the control of the precision of the clamping force. Because the size of the clamping force will affect the degree of the deformation of the die, it will ultimately affect the dimensional tolerance of the parts.
In this paper, the precision injection molding is mainly described from the repetition precision of the product size. However, because of the different properties and processing technology of various materials, the precision of the plastic parts can not be equated with the precision of the metal parts. The mold of molded products is an important condition to decide whether the product can meet the design requirements, and the precision injection
The most important technical indicators for evaluating products are the accuracy of the injection products (dimensional tolerances, geometric tolerances and the smoothness of the surface of the products). For injection molding of precision plastic products, we must strictly control 4 factors, including material selection, mold design, injection molding process and operator’s technology level. Precision injection molding machine precision requirements of the products within 0.01 ~ 0.001mm, many also require precision injection molding injection molding machine with high injection pressure, injection speed high requirements; clamping system has enough rigidity and high precision locking, the so-called locking precision refers to the clamping force uniform and adjustable stable and high repeatability, high position precision mold; requirements for pressure, flow, temperature and measurement can accurately control the corresponding precision, using multi-stage or stepless injection molding process to ensure the reproduction conditions and product size precision etc..
The material of precision mould is to choose alloy steel with high mechanical strength. The materials for making cavity and runner must undergo strict heat treatment, and select materials with high hardness (forming parts to reach HRC52), good wear resistance and strong corrosion resistance.
D. PC and GFPC. Features: good wear resistance, enhanced rigidity, good dimensional stability, weatherability, flammability and good molding.
The 360 Quadrant efficiently maps the Injection Molding Machine Companies based on criteria such as revenue, geographic presence, growth strategies, investments, channels of demand, and sales strategies for the market presence of the Injection Molding Machine quadrant. While the top criteria for product footprint evaluation included Materials (Plastic, Rubber, Metal, Ceramic), Type of Machines (Hydraulic, All-Electric, Hybrid), End-Use Industry (Automotive, Consumer Goods, Packaging, Healthcare, Electronics, Others).
A. because the injection pressure of the precision injection machine is high, it is necessary to emphasize the stiffness of the clamping system. The parallelism of the moving and fixed templates is controlled within the range of 0.05 to 0.08mm.
D. plasticizing parts: screw, screw head, check ring, material barrel, etc., should be designed into a structural form with strong plasticizing ability, good homogenization degree and high injection efficiency. The screw drive torque is large and can be continuously variable.
Machinability and rigidity, in mold structure design, the number of cavity should not be too much, while the bottom plate, supporting plate and cavity wall should be thicker, so as to avoid the severe elastic deformation of parts under high temperature and high pressure.
(1) to improve the precision and quality of the precision products, the injection pressure has the most obvious effect on the shrinkage rate of the product. When the injection pressure is up to 392MPa, the molding shrinkage of the product is almost zero. At this time, the precision of the product is only influenced by the control of the mold or the environment. The experiment showed that the mechanical strength increased by 3% ~ 33% after the injection pressure increased from 98MPa to 392MPa.
(4) effects of pressure, pressure has great influence on the precision of plastic parts, precisely, the pressure can effectively reduce feeding, plastic deformation, control precision plastic parts, pressure stability determines the forming precision of plastic parts, screw the end position unchanged is the determinants of insurance pressure effect.
(1) high demand for repeated precision (reproducibility) of injection molding parameters, and multistage injection feedback control should be adopted.
The accuracy of displacement sensor is up to 0.1mm, so that we can strictly control the metering stroke, injection stroke and the thickness of the rest pad (shooting monitoring point), so as to ensure the accuracy of each injection and improve the molding accuracy of products. The temperature control of the barrel and nozzle is accurate, the overshoot is small and the fluctuation of temperature is small when heating up. PID control should be adopted in precision injection molding, so that the temperature accuracy is between 0.5 and C.
(2) the thickness of the precision products can be reduced and the length of the molding can be improved. Taking PC as an example, the injection pressure 177MPa of ordinary machine can form 0.2 to 0.8mm wall thickness products, while the injection pressure of precision machine can form products with thickness between 0.15 and 0.6mm when 392MPa is injected. The ultra high pressure injection machine can obtain more products with a larger flow ratio.
An injection molding machine consists of a heated barrel equipped with a reciprocating screw (driven by hydraulic or electric motor) which feeds the molten polymer into a temperature controlled split mold via a channel system of gates and runners. The screw units (plasticizes) the polymer and acts as a ram during the injection phase. The screw action also provides additional heating by virtue of shearing action on the polymer. The polymer is injected into a mold tool that defines the shape of the molded part.
(5) if the cooling time is the same for the mold temperature control, the thickness of the product with low mold cavity temperature is larger than that of the product with higher temperature. For example, POM and PA materials, the products with a thickness of 50~100 u m at 50 degrees centigrade temperature decrease to 20~40 m at 80, and only 10 m at 100. Room temperature also affects the dimensional tolerance of precision products.
C. mold is good and rigid, the dimension precision of the cavity, the degree of finish and the precision of the positioning between the templates are high.
The Injection Molding Machine Companies quadrant is a comprehensive industry analysis that provides valuable insights into the global market for Injection Molding Machine. This quadrant offers a detailed evaluation of key market players, technological advancements, product innovations, and industry trends. MarketsandMarkets 360 Quadrants evaluated over 60 Injection Molding Machine Companies of which the Top 15 Injection Molding Machine Companies were categorized and recognized as the quadrant leaders.
Precision injection is a kind of injection molding method which is difficult to meet the requirements of injection molding machine and conventional injection molding process. The concept of precision injection molding is mainly different from “conventional injection molding”. It is based on the rapid development of polymer materials, and uses precise plastic parts to replace high-precision metal parts in the instrument and electronics field.
Compression shrinkage and elastic reduction, the general plastics have compressibility. That is, the specific volume changes significantly at high pressure. Under the general temperature, the specific volume of the molded products will be reduced, the density will increase, the expansion coefficient decreases, and the shrinkage rate will decrease significantly. Corresponding to the compressibility, the molding material has the effect of elastic reduction, which reduces the shrinkage of the products. The factors affecting the molding shrinkage of the products are related to the forming conditions and operating conditions.
The phase change contraction is called phase change contraction due to the crystallization of the crystalline resin and the crystallization of the polymer during the orientation process, due to the reduction of the specific volume. The mold temperature is high, the crystallinity is high, the shrinkage rate is large. But on the other hand, the increase of crystallinity will increase the product density, decrease the linear expansion coefficient and reduce the shrinkage rate. Therefore, the actual shrinkage rate is determined by the combination of the two.
(2) the plasticizing quality requirements, uniform plastic plastic not only affects the quality of injection parts, but also affect the melt through the gate by force, in order to get uniform plasticizing, for design and use of special screw plasticizing technology is essential.
The Injection Molding Machine Companies quadrant is a comprehensive industry analysis that provides valuable insights into the global market for Injection Molding Machine. This quadrant offers a detailed evaluation of key market players, technological advancements, product innovations, and industry trends. MarketsandMarkets 360 Quadrants evaluated over 60 Injection Molding Machine Companies of which the Top 15 Injection Molding Machine Companies were categorized and recognized as the quadrant leaders. An injection molding machine consists of a heated barrel equipped with a reciprocating screw (driven by hydraulic or electric motor) which feeds the molten polymer into a temperature controlled split mold via a channel system of gates and runners. The screw units (plasticizes) the polymer and acts as a ram during the injection phase. The screw action also provides additional heating by virtue of shearing action on the polymer. The polymer is injected into a mold tool that defines the shape of the molded part. The 360 Quadrant efficiently maps the Injection Molding Machine Companies based on criteria such as revenue, geographic presence, growth strategies, investments, channels of demand, and sales strategies for the market presence of the Injection Molding Machine quadrant. While the top criteria for product footprint evaluation included Materials (Plastic, Rubber, Metal, Ceramic), Type of Machines (Hydraulic, All-Electric, Hybrid), End-Use Industry (Automotive, Consumer Goods, Packaging, Healthcare, Electronics, Others). Key trends highlighted in 360 Quadrants: The injection molding machine industry has seen steady growth in recent years. By 2027, the global market is expected to reach USD 12.4 billion, growing at a CAGR of 4.50% from USD 10.4 billion valuation in 2023. This growth can be attributed to rising demand across end-use sectors like automotive, consumer goods, packaging, healthcare, and electronics. Key drivers fostering the growth of the market include increasing healthcare needs, rapid industrialization in developing economies, and growing use of plastic molds in electric vehicle manufacturing. Asia Pacific currently leads the global market in both volume and value, followed by Europe and North America. The growth in Asia Pacific region is majorly due to the increased demands from the emerging economies in the region that are witnessing high demand from the automotive, consumer goods, packaging, medical, and other industries. Owing to this the Asia Pacific region is expected to largest and fastest growing market for injection molding machine market. This high growth in the emerging economies provides a multitude of opportunities for injection molding machine companies. Plastic was the dominant material, accounting for nearly 85.2% of the market in 2023. This is due to the versatility and cost-effectiveness of plastic injection molding for high-volume production of automotive, packaging, consumer goods, healthcare, and electronics parts. With the widespread and growing use of plastic globally, the plastic segment is expected to see the fastest growth rate from 2023 to 2027. Meanwhile, rubber injection molding holds a smaller but substantial share of the overall market, as the second largest segment in 2023, mostly because of continued demand for rubber components and products. While plastics lead the market now, there are growth opportunities across all injection molded material types as injection molding machine companies want to produce diverse components through this high-efficiency process. Hydraulic injection molding machines have historically dominated the global market due to their lower costs, longer service life, technical advantages, and widespread use. However, all-electric injection molding machines are expected to see the fastest growth at a CAGR of nearly 4.00% over the forecast period. This can be attributed to its ability to provide higher clamping force for larger parts, increased repeatability, enhanced precision, reduced downtime, and energy-efficient features. The primary hurdle lies in the substantial initial investment required. For injection molding machine companies, this shift implies a need to adapt to the evolving market demands. Injection Molding Machine Companies that have traditionally focused on hydraulic machines may face challenges in maintaining their market share unless they invest in and integrate all-electric technologies. Embracing the growing demand for all-electric machines with their advantages in higher clamping force, increased repeatability, enhanced precision, reduced downtime, and energy efficiency could be crucial for staying competitive. The injection molding machine market is highly competitive, with both global and regional injection molding machine companies holding a substantial share. The key injection molding machine companies profiled in the quadrant include Haitian International Holdings Limited (China), Chen Hsong Holdings Limited (China), Sumitomo Heavy Industries Ltd. (Japan), ENGEL Austria GmbH (Austria), Hillenbrand, Inc. (USA), and others. They consistently employ developmental strategies such as expansions, product launches, acquisitions, and contracts & agreements to strengthen their positions in the injection molding machine market. For example, in May 2023, KraussMaffei introduced a special edition of its proven CX series. The special edition, named "#185," included a package of attractive additional features that would normally incur charges but were integrated at no extra cost. This allowed users to enhance the quality and efficiency of injection molding applications in the clamping force range from 500 to 4200 kN, simultaneously achieving an immediate and noticeable reduction in operating costs. The healthcare industry is rapidly adopting injection molding technology to manufacture medical devices and products. This growth is driven by the benefits injection molding provides for producing disposable and durable goods like drug delivery systems, blood glucose tests, and mobility aids. As the population ages, the demand rises for convenient, lightweight, and cost-effective medical products. Injection molding allows mass production of these goods with consistency. The process is ideal for items used frequently in hospitals and homes. With more disposable and durable medical goods, injection molding machine companies see increasing opportunities in the healthcare sector. This rising demand from healthcare therefore promises growth for the injection molding machine market.
The proportion system of proportional pressure valve, proportional flow valve or servo variable pump should be adopted in the
High mechanical strength, good dimensional stability, good vermicular resistance, and wide range of environmental adaptation.
There are four factors that affect the shrinkage: heat contraction, phase change contraction, orientation contraction and compression contraction.
C. because of the high speed of the precision injection molding machine, it is necessary to emphasize the speed of the reaction of the hydraulic system.
Due to the forced stretching of the molecular chain in the flow direction, the macromolecules in the cooling direction will have the trend of rewinding and recovery, and the contraction will take place in the orientation direction. The degree of molecular orientation is related to injection pressure, injection speed, resin temperature and mold temperature. But the main thing is the injection speed.
360 Quadrants is a scientific research methodology by MarketsandMarkets to understand market leaders in 6000+ micro markets
Thermal shrinkage is the thermal physical characteristic of the molding material and the mold material. The mold temperature is high, the temperature of the product is high, the actual shrinkage rate will increase, so the precision injection mold temperature should not be too high.
Abstract: Precision Injection Molding is a kind of plastic injection molding method which requires precision mold and requires precision machines. The content of this blog include concept, characteristic, influential factors, selection of plastic material, precision molds, selection and characteristic of precision plastic injection machines.
A. POM and carbon fiber reinforced (CF) or glass enhancement (GF). This material is characterized by good creep resistance, fatigue resistance, weatherability, good dielectric properties, difficult to burn, and easy release of lubricants.
(3) improve the efficiency of injection rate. In order to achieve the rated injection rate, there are only two ways: one is to improve the maximum injection pressure of the system, and the two is to transform the screw parameters and increase the length to diameter ratio. The injection rate of the precision injection machine is high.
GETTING A QUOTE WITH LK-MOULD IS FREE AND SIMPLE.
FIND MORE OF OUR SERVICES:
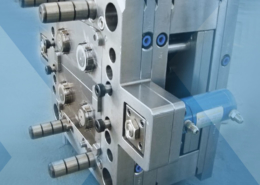
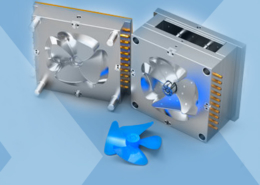
Plastic Molding

Rapid Prototyping
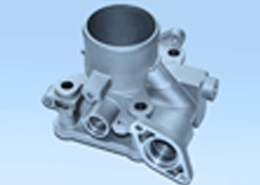
Pressure Die Casting
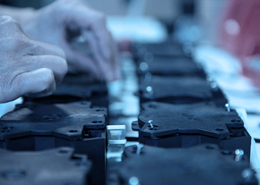
Parts Assembly
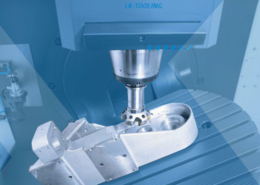