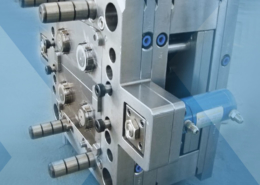
Injection Molding |Sanner | Device CDMO - medical device molding
Author:gly Date: 2024-10-15
PC-PBT (Polycarbonate-Polybutylene Terephthalate) is a blend that offers an excellent combination of properties from both Polycarbonate and Polybutylene Terephthalate. This alloy is known for its durability and excellent resistance to various chemicals and weathering.
Zinc is another metal widely used in injection molding, particularly for its excellent casting properties and durability. It’s favored for its ability to produce complex shapes with high precision.
Ceramics in injection molding are renowned for their high temperature resistance, excellent wear resistance, and electrical insulation properties. Unlike metals and plastics, ceramics are known for their hardness and ability to withstand harsh environments, making them ideal for specialized applications.
Polyphenylene Sulfide (PPS) is a high-performance thermoplastic known for its outstanding resistance to chemicals, heat, and flame. PPS is distinguished by its ability to maintain structural integrity and mechanical properties in harsh environments, making it ideal for demanding applications in various industries.
ABS Polycarbonate (PC-ABS) is a blend of Acrylonitrile Butadiene Styrene (ABS) and Polycarbonate (PC). This material combines the strength and heat resistance of PC with the flexibility of ABS, offering a balanced solution for demanding applications.
Polyethylene Terephthalate (PET) is a highly versatile and widely used thermoplastic polymer. Renowned for its strength, dimensional stability, and excellent resistance to moisture and various chemicals, PET is commonly used in both textile fibers (polyester) and packaging materials, particularly in the food and beverage industry.
Polybutylene Terephthalate (PBT) is a thermoplastic engineering polymer that is known for its durability and excellent machining properties. PBT is highly valued for its balance of chemical and heat resistance, mechanical strength, and electrical insulation properties. It is typically used in applications that require a robust material that can withstand harsh environments.
PMMA, commonly known as Acrylic, is a transparent thermoplastic often used as a lightweight, shatter-resistant alternative to glass. Its excellent clarity and ability to be molded into various shapes make it a popular choice in many industries.
They are typically used in environments that demand high wear resistance and thermal stability, such as in aerospace and automotive applications. Their unique blend offers an ideal solution for components that must endure extreme conditions while maintaining structural integrity.
PC-ABS is a blend that combines the strength and heat resistance of polycarbonate with the flexibility of ABS. This material is known for its excellent thermal properties and impact resistance, making it a go-to choice for complex parts and demanding applications.
Polyetherimide (Ultem) is known for its high heat resistance and strength. It offers exceptional mechanical, thermal, and electrical properties, making it a valuable material in high-performance applications.
High-Density Polyethylene (HDPE), a member of the polyethylene family, is known for its robustness and higher density compared to its counterparts. It stands out for its strength, resistance to impact, and versatility. HDPE’s rigidity and toughness make it a preferred choice for products that need to withstand rigorous use.
Materials like Polycarbonate (PC) and Polyamide (Nylon) are known for their high strength and durability, making them suitable for demanding injection molding applications.
We have explored the multifaceted world of injection molding materials, underscoring the importance of material selection in determining the quality, functionality, and sustainability of injection molded products. It’s evident that the right material choice is not just about matching physical properties but also about aligning with budget, environmental considerations, and future trends.
Thermoplastics are a category of polymers that become pliable or moldable at a specific elevated temperature and solidify upon cooling. Their ability to be reheated and reshaped multiple times without significant degradation is a key characteristic. This feature makes thermoplastics highly valuable in manufacturing processes like injection molding, where they are used to produce a vast array of products, from simple household items to complex automotive components.
Polysulfone (PSU) is a high-performance thermoplastic known for its toughness and stability at high temperatures. It offers excellent chemical and thermal resistance, making it ideal for demanding applications.
Specialty plastics, distinguished from standard plastics, are engineered for high performance and often tailored for specific industrial applications. These materials typically exhibit exceptional properties like high-temperature resistance, superior mechanical strength, and remarkable chemical stability. They are often chosen for applications where ordinary plastics may not suffice.
Thermoplastic Vulcanizates (TPV) are part of the thermoplastic elastomer family. TPV is known for its excellent compression set, heat resistance, and fluid resistance, making it suitable for applications that demand the durability of vulcanized rubber combined with the processing ease of thermoplastics.
Polypropylene (PP) is a versatile plastic that balances workability and performance. Known for its excellent chemical resistance and toughness, PP is widely used in both consumer goods and industrial applications. It is available in various grades, including homopolymer, copolymer, and impact-modified.
Metals in injection molding are significant due to their strength, durability, and specific properties that make them irreplaceable in certain applications. Unlike plastics, metals often bring enhanced mechanical strength, thermal resistance, and electrical conductivity.
While injection molding is a fantastic process for the reasons mentioned above, there are certain limitations and drawbacks. A few of these drawbacks include:
Engineered Thermoplastic Polyurethane (ETPU) is a specialized form of TPU that combines the elasticity of rubber with the toughness and durability of thermoplastics. ETPU is known for its excellent wear and tear resistance, flexibility, and ability to withstand extreme temperatures and environmental conditions, making it highly suitable for both industrial and consumer products.
Polyphenylene Oxide (PPO) / PPE-PS is a blend of polyphenylene oxide and polystyrene. This material offers a unique balance of thermal performance, dimensional stability, and electrical properties. It is particularly valued in electrical and electronic applications for its low moisture absorption and excellent dielectric properties.
Injection molding materials are the backbone of the injection molding process, a method widely used in manufacturing for producing parts in large volumes. These materials, which vary widely in their properties and applications, can be broadly categorized into thermoplastics, thermosets, and elastomers. Each category has its unique characteristics and suitable applications, making the material selection a pivotal decision in the injection molding process.
Polyethylene and Polypropylene are typically the most cost-effective injection molding options, offering a good balance of properties at a lower price point.
Thermoplastics are a major category in injection molding materials, known for their versatility and recyclability. They become pliable or moldable at a certain elevated temperature and solidify upon cooling. This reversible process makes thermoplastics a popular choice in various industries.
Thermoplastic Polyurethane (TPU) is renowned for its outstanding combination of flexibility, durability, and resistance to oils and greases. It bridges the gap between rubbers and plastics, offering both elasticity and processability. TPU’s versatility makes it an excellent choice for a wide range of applications, especially where elasticity and toughness are required.
Polystyrene (PS), another prominent amorphous plastic, is favored for its ease of molding and excellent aesthetic properties. It’s particularly noted for its clarity and rigidity, making it suitable for a wide range of applications, particularly in packaging and disposable consumer goods.
Polylactic Acid (PLA) is a biodegradable thermoplastic derived from renewable resources such as corn starch or sugar cane. It is widely used in additive manufacturing and packaging due to its low environmental impact and good mechanical properties.
Polyoxymethylene (POM), also known as acetal, is a high-performance engineering plastic known for its strength, rigidity, and excellent friction and wear properties. POM exists in two variants: copolymer and homopolymer, each offering slightly different properties. Delrin, a homopolymer form of POM, is particularly noted for its high tensile strength and rigidity.
Thermoplastic Rubber (TPR) is a blend of plastic and rubber. TPR possesses both thermoplastic and elastomeric properties, making it an ideal material for applications requiring flexibility and durability. It is also recyclable, contributing to its popularity in various manufacturing processes.
The injection molding industry continues to evolve, driven by technological advancements and emerging market demands. This section delves into future developments, exploring how they could reshape the landscape of injection molding.
Semi-crystalline plastics are characterized by their orderly molecular structure that forms crystalline regions within an amorphous matrix. This structure imparts these materials with higher melting points, better chemical resistance, and increased rigidity compared to amorphous plastics.
Nylon Polyamide is a versatile and widely used semi-crystalline material. Known for its excellent combination of strength, durability, and flexibility, nylon is used in a vast array of applications. It comes in various grades, including Nylon 6 and Nylon 66, each having distinct properties.
Zirconia, or Zirconium Oxide, is a ceramic material known for its remarkable toughness and resistance to crack propagation, often used in applications where high fracture toughness is required.
Stainless steel in injection molding is prized for its corrosion resistance and strength. It’s a versatile material suitable for both industrial and consumer applications. The ability to withstand high temperatures and resist corrosion makes stainless steel ideal for products that endure harsh environments or require a high degree of sanitation, such as medical devices and kitchenware.
Aluminum is known for its lightweight yet strong nature. It’s a go-to metal for applications requiring high strength-to-weight ratios. The material is also appreciated for its excellent thermal conductivity and corrosion resistance.
Alumina, or Aluminum Oxide, is one of the most commonly used ceramic materials in injection molding. It is known for its high hardness, excellent electrical insulation, and good thermal stability.
Thermoplastics like ABS and Polypropylene are easy to mold due to their excellent flow properties and wide processing windows.
Liquid-crystal Polymer (LCP) is a unique type of thermoplastic known for its high strength, chemical resistance, and excellent thermal stability. LCP’s distinctive molecular structure offers remarkable mechanical properties and dimensional stability, even in ultra-thin applications, making it a preferred material for precision parts in high-tech fields.
Polypropylene (PP) and Polyethylene (PE) are among the most commonly used injection molding materials due to their versatility, durability, and cost-effectiveness.
In the end, when selecting a molding process for your parts, it’s always recommended to speak with a thermoset composite or thermoplastics engineer. After reviewing your needs, they’ll be best able and equipped to make a recommendation for your job that will produce the highest quality piece at the most reasonable cost.
Polyether Ether Ketone (PEEK) is a high-performance engineering thermoplastic known for its outstanding mechanical and chemical resistance properties. PEEK is renowned for its ability to maintain its structural integrity in harsh chemical environments and at high temperatures, making it an ideal choice for advanced engineering applications.
Polyvinyl Chloride (PVC) is a widely used synthetic plastic polymer. It comes in both rigid and flexible forms and is known for its durability, chemical resistance, and versatility in various applications.
Ceramic-metal composites, also known as cermet, are produced through injection molding for specialized applications. These materials combine the hardness and heat resistance of ceramics with the toughness of metals.
ABS is a widely recognized amorphous plastic, known for its robustness and adaptability. This material is a polymer blend that uniquely balances strength, gloss, and toughness. Its ability to be easily molded and its superior surface finish make it a preferred choice in numerous applications.
Polyethylene (PE), one of the most common plastics, is known for its excellent chemical resistance and flexibility. It is available in various densities, including high-density and low-density versions, each offering distinct properties suitable for different applications.
Composite materials in injection molding are engineered by combining fibers such as fiberglass, carbon fiber, or natural fibers with a matrix of thermoplastics or thermosetting resins. This amalgamation results in materials that exhibit enhanced mechanical properties like increased strength, reduced weight, and improved resistance to environmental factors.
The different molding processes are used to create different pieces. In this article, we’ll be weighing the pros and cons of the injection molding process for thermoset composites.
Low-Density Polyethylene (LDPE) is softer, more flexible, and has a lower melting point compared to HDPE. It is known for its excellent chemical resistance and electrical properties, making it ideal for a broad range of applications, particularly where flexibility is key.
Magnesium stands out for being the lightest structural metal, offering an exceptional strength-to-weight ratio. It is increasingly popular in applications where weight reduction is critical without compromising strength.
Amorphous plastics are a significant category in the realm of injection molding materials. Unlike their crystalline counterparts, these materials lack a precise, ordered molecular structure. This characteristic imparts unique properties to amorphous plastics, such as enhanced dimensional stability, lower shrinkage rates, and better transparency. Commonly used in various applications, these materials are pivotal in the industry due to their versatile nature.
The world of manufacturing is continually evolving, and at the forefront of this innovation is injection molding. A critical aspect that determines the success of this process is the selection of the right material. Understanding the nuances of different injection molding materials is not just a matter of technicality but a cornerstone of quality and efficiency in production.
Weighing the pros and cons of the molding process for your composites can help you determine whether it's the right choice for your project needs. Creating a plastic or composite part requires raw material to be heated and poured into a mold that has been created specifically for that part. The four most common types of molding processes are:
Thermoplastic Elastomer (TPE) combines the properties of rubber with the processing advantages of plastics. TPE is known for its flexibility, durability, and ability to be stretched to moderate elongations and return to its near original shape, creating a longer life and better physical range than other materials.
Thermosets and elastomers stand in contrast to thermoplastics. Once they are set, typically through a chemical reaction, they cannot be remelted. This irreversible setting gives them different properties and applications. Thermosets are known for their dimensional stability and heat resistance, while elastomers are recognized for their flexibility and elasticity, resembling rubber.
Specialize in CNC machining, 3D printing, urethane casting, rapid tooling, injection molding, metal casting, sheet metal and extrusion
Low alloy steel in injection molding offers a balance of strength, toughness, and wear resistance at a more economical price point than some other metals. This material is often used in applications where structural integrity is paramount. Its molding process allows for the creation of complex shapes and designs, making it a go-to for automotive parts, machinery components, and tools where durability and strength are crucial.
Titanium and its alloys are known for their high strength-to-weight ratio and excellent corrosion resistance. In injection molding, they are typically used for specialized applications where weight reduction is critical without compromising strength. This includes aerospace components, medical implants, and high-performance automotive parts. Titanium’s biocompatibility also makes it an ideal choice for medical applications.
Linear Low-Density Polyethylene (LLDPE) is a variation of polyethylene with significant flexibility, toughness, and impact resistance. LLDPE is known for its superior tensile strength and higher resistance to puncture compared to LDPE, making it suitable for more demanding applications.
This category covers a range of plastics that are less common but equally important in specific applications. Each of these materials brings unique properties to the table, making them ideal for certain uses where general-purpose plastics might not be sufficient.
This process involves injecting molten wax into a mold to form a pattern, which is then coated with a refractory material to create a mold for metal casting. The versatility of wax allows for the creation of complex shapes with excellent surface finish, making it an indispensable resource in precision casting processes.
High Impact Polystyrene (HIPS) is a modified version of polystyrene that offers enhanced impact strength. It combines the easy processability of polystyrene with improved toughness, making it suitable for a wide range of applications.
Polycarbonate (PC) is renowned for its impressive combination of transparency and impact resistance. This amorphous plastic is highly regarded for its strength and its ability to withstand extreme temperatures and impacts, making it ideal for use in challenging environments.
Choosing the right material for an injection molding project is crucial for the success of the product. This step-by-step guide will provide insights into the key considerations and practical aspects of material selection, ensuring the best match for your project’s specific requirements and constraints.
Material selection in injection molding is a complex process influenced by various factors, each contributing to the final product’s performance, appearance, and cost. Understanding these factors helps in making informed decisions tailored to specific applications.
Wax, although not a conventional injection molding material, plays a crucial role in the casting industry. Wax injection molding is primarily used to create detailed and accurate patterns for investment casting.
GETTING A QUOTE WITH LK-MOULD IS FREE AND SIMPLE.
FIND MORE OF OUR SERVICES:
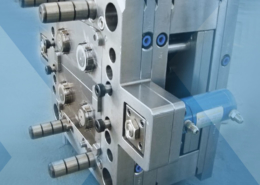
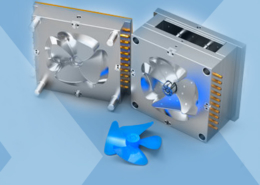
Plastic Molding

Rapid Prototyping
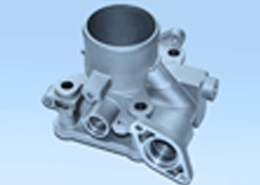
Pressure Die Casting
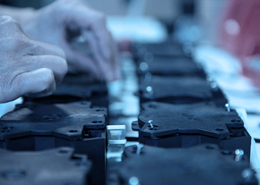
Parts Assembly
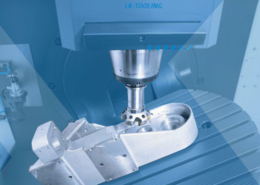