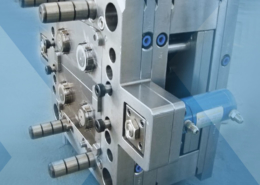
Injection Molding Prototyping | Fast and Low-cost - Quote - rapid prototyping pl
Author:gly Date: 2024-10-15
Through UnitedHealthcare, UMR creates and publishes the Machine-Readable Files on behalf of Crescent Industries, Inc. To link to the Machine-Readable Files, please click on the URL provided: https://transparency-in-coverage.uhc.com/
Polypropylene is derived from substituting the ethylene monomer with a methyl group (CH3). It is harder than PE and offers better resistance to moisture and gases, so it's suitable for storing fluid drugs. PP is also autoclavable and chemically robust, expanding its utility for storing sterile drug products.
PVC is derived from substituting a hydrogen atom with chlorine in the ethylene monomers, which reduces its reactivity to nonpolar liquids. It is also transparent and flexible, making it a strong choice for storing glucose and saline solutions.
PE consists of ethylene monomer units linked through addition polymerization. Its variants offer distinct mechanical properties suited for various applications:
Biocompatibility involves assessing how materials interact with living tissues. Medical devices often come into direct and prolonged contact with bodily fluids or tissues, making biocompatibility a top priority.
Sterilization compatibility is also crucial to maintaining the hygiene and safety of medical devices. Injection molded parts must have high heat resistance to withstand various sterilization methods such as autoclaving, gamma radiation, or harsh chemical agents.
Medical injection molding utilizes various types of plastic materials. Thermoplastics and thermosetting materials are prominent in this field. Thermosetting plastics have high melting points, chemical resistance, and mechanical strength due to the strong covalent bonds between polymer strands. However, these covalent linkages cannot reform once broken, resulting in permanent deformation. These properties make thermosetting plastics useful as adhesives and protective coatings.
PCTFE is derived from replacing all remaining hydrogen atoms on the monomers with fluorine. The resulting material is ideal for pharmaceutical packaging thanks to its excellent strength, impact resistance, and moisture resistance.
Plastics, also known as polymers, consist of repeating monomers forming homopolymers or copolymers. These materials are arranged into linear or branched polymers, resulting in diverse plastics with unique features.
Industry standards are essential guidelines that ensure end-users are safeguarded from undue risks associated with medical molded products. Regulatory bodies like the EU MDR (Medical Device Regulation) and the U.S. FDA (Food and Drug Administration) categorize medical devices into three classes, each correlating with a distinct level of risk. They include:
Join us as we explore different types of medical-grade plastics and the critical factors in injection molding material selection.
Thermoplastics also feature weaker intermolecular forces, allowing them to melt and reform multiple times without permanent alteration. The material’s versatility and ability to withstand the remolding processes make it ideal for medical device plastic injection molding.
Plastic medical products have revolutionized and improved the quality of patient management globally, but not all materials are created equal. Choosing suitable plastic materials for your medical device manufacturing is essential, as it impacts the success and safety of your final product.
Usability involves factors like handling ease and comfort. Silicone, prized for flexibility and skin comfort, is common in wearable medical devices. Plastic mold technology provides the design flexibility to create intricate and ergonomic designs, enhancing the overall usability of medical devices.
As your partner, Crescent Industries can provide expertise in injection molding manufacturing and uphold ISO standards, ensuring high-quality medical plastic products. Contact us for unparalleled quality, speed, and value in medical injection molding.
Medical-grade plastics like polyethylene, polypropylene, PVC, polystyrene, and silicone offer exceptional durability and biocompatibility. Understanding these properties and the material standards for each ensures you produce durable, reliable devices.
The mechanical and chemical attributes of plastics significantly influence the durability and functionality of medical devices. Some important mechanical properties include:
To adhere to these tight tolerances and standards, injection molders must implement rigorous procedures at every production stage. Some of these standards include:
PEEK is celebrated for its unique biomimetic qualities and fatigue resistance. It's commonly used for orthopedic implants and prosthetics.
Thermoplastics can be hard yet highly flexible. They can resist bending but offer excellent tensile strength that protects them from breaking.
Selecting the right materials for your medical devices is critical for determining the final product’s performance, safety, and efficacy. Here are a few key factors guiding the intricate injection molding material selection process.
Chemical resistance is crucial for devices exposed to cleaning agents and bodily fluids, ensuring longevity and reliability. Understanding and utilizing these properties to their best advantage is essential for maximizing device performance in medical applications.
With the rapid advancements in healthcare, plastic has emerged as the favored material for prototyping crucial medical components:
Medical device aesthetics and usability contribute significantly to patient experience and acceptance. Visible prosthetics benefit from appealing, durable molding materials like colorable polycarbonate.
Applications:Chemical processing – production, storage and transfer of corrosive fluidsElectronics – protective sheathing, plenum and wiring insulationSemi-conductor industryFood stuff and Healthcare industriesTransportation – fuel line and pipe, thermoformed body componentsInformation provided by Arkema Inc.
GETTING A QUOTE WITH LK-MOULD IS FREE AND SIMPLE.
FIND MORE OF OUR SERVICES:
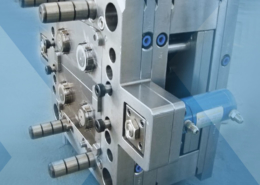
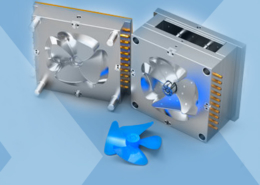
Plastic Molding

Rapid Prototyping
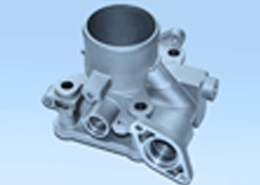
Pressure Die Casting
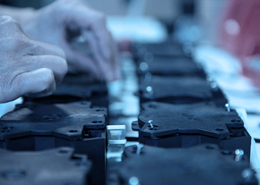
Parts Assembly
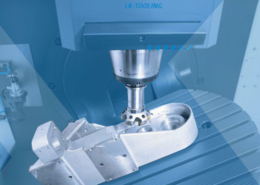