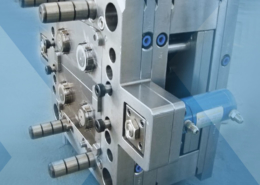
Unveiling the Potential of Small Run Injection Molding: Tailored Solutions for E
Author:gly Date: 2024-06-08
Small run injection molding has emerged as a game-changer in the manufacturing industry, offering flexible and cost-effective solutions for low to medium volume production requirements. As industries increasingly prioritize customization and quick turnaround times, the significance of small run injection molding cannot be overstated. This article aims to explore the nuances of small run injection molding, delving into its capabilities, advantages, challenges, and future prospects.
Understanding Small Run Injection Molding
Small run injection molding, also known as low-volume production molding, involves the manufacturing of plastic parts in quantities ranging from a few hundred to several thousand units. Unlike traditional high-volume production methods, small run injection molding caters to niche markets, prototype development, and limited production runs. Its versatility and efficiency make it an ideal choice for businesses seeking customized solutions without the constraints of mass production.
Advantages of Small Run Molding
The advantages of small run injection molding are manifold. Firstly, it allows for rapid prototyping and product development, enabling companies to iterate designs quickly and bring products to market faster. Additionally, small run molding offers cost savings compared to traditional manufacturing methods, as it eliminates the need for expensive tooling and setup costs associated with high-volume production. Moreover, it provides flexibility in meeting fluctuating demand and reducing inventory overhead.
Applications Across Industries
Small run injection molding finds applications across a wide range of industries, including automotive, aerospace, medical, and consumer electronics. In the automotive sector, it facilitates the production of custom components and prototypes for concept vehicles and specialty models. Similarly, in the medical field, small run molding enables the manufacturing of precision parts for medical devices and equipment, meeting strict regulatory standards and quality requirements.
Challenges and Considerations
Despite its advantages, small run injection molding presents certain challenges that must be addressed. One key challenge is ensuring consistency and quality across small batch production runs. Maintaining tight tolerances and meeting customer specifications require meticulous attention to detail and robust quality control measures. Additionally, managing costs and optimizing production efficiency are ongoing considerations in small volume manufacturing.
Future Directions and Innovations
Looking ahead, the future of small run injection molding is promising, driven by advancements in technology and evolving market demands. Emerging trends such as additive manufacturing, 3D printing, and digital twin simulation are poised to revolutionize small volume production processes, offering greater flexibility, speed, and cost-effectiveness. Moreover, the integration of Industry 4.0 technologies such as automation and real-time monitoring promises to further enhance efficiency and quality in small run molding operations.
Conclusion
In conclusion, small run injection molding represents a pivotal shift in the manufacturing landscape, offering tailored solutions for diverse production needs. Its advantages in rapid prototyping, cost-effectiveness, and flexibility make it indispensable across various industries. While challenges in consistency and cost management persist, ongoing innovations and advancements hold the promise of overcoming these hurdles. By embracing technological advancements and staying abreast of market trends, small run injection molding is poised to continue driving innovation and reshaping the future of manufacturing.
GETTING A QUOTE WITH LK-MOULD IS FREE AND SIMPLE.
FIND MORE OF OUR SERVICES:
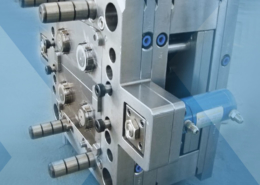
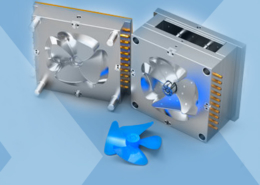
Plastic Molding

Rapid Prototyping
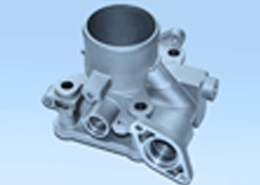
Pressure Die Casting
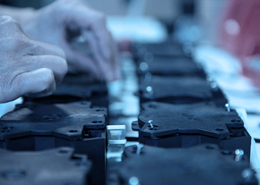
Parts Assembly
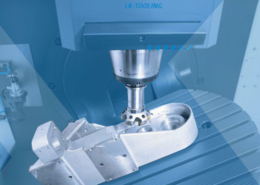