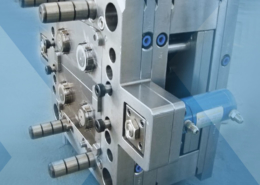
Exploring Small Injection Molding: Precision in Miniature
Author:gly Date: 2024-06-08
Small injection molding, despite its size, plays a significant role in modern manufacturing, offering precision, efficiency, and versatility in producing miniature plastic components. In this article, we delve into the world of small injection molding, uncovering its applications, advantages, challenges, and future prospects.
Introduction: The Power of Miniaturization
Small injection molding, also known as micro molding, micro injection molding, or miniaturized injection molding, caters to the growing demand for precise and intricate plastic components in various industries. From medical devices and electronics to automotive and consumer goods, small injection molding enables the production of complex geometries with tight tolerances, opening doors to innovation and efficiency.
Applications in Diverse Industries
Medical Devices
In the medical industry, small injection molding is indispensable for manufacturing miniature components such as catheters, syringes, implants, and surgical instruments. The ability to produce intricate designs with biocompatible materials allows for the development of advanced medical devices that improve patient outcomes and quality of care.
Electronics
In the electronics sector, small injection molding is utilized for producing miniaturized components such as connectors, switches, sensors, and microfluidic devices. The compact size and high precision of these components are crucial for electronic devices' functionality and performance, driving innovation in consumer electronics, telecommunications, and automotive electronics.
Automotive
In automotive manufacturing, small injection molding contributes to the production of miniature parts such as sensors, connectors, and interior components. These components play a vital role in vehicle safety, performance, and comfort, highlighting the importance of small injection molding in the automotive industry's pursuit of lightweighting and miniaturization.
Advantages of Small Injection Molding
Precision and Accuracy
Small injection molding offers unparalleled precision and accuracy in producing miniature components with intricate geometries and tight tolerances. Advanced molding techniques, tooling technologies, and process controls enable manufacturers to achieve sub-micron precision in small-scale plastic parts, ensuring consistent quality and performance.
Cost-effectiveness
Despite the complexities involved, small injection molding can be cost-effective for producing small batches or high-volume production runs of miniature components. The ability to mold multiple parts simultaneously, minimize material waste, and optimize cycle times contributes to overall cost savings and competitiveness in the market.
Design Flexibility
Small injection molding provides designers with greater flexibility in realizing their creative vision and functional requirements for miniature components. With the ability to mold complex shapes, intricate details, and overmolded features in a single operation, designers can push the boundaries of innovation and differentiation in product development.
Challenges and Considerations
Tooling Complexity
The complexity of tooling design and fabrication presents a significant challenge in small injection molding. Miniature molds require precise machining, EDM (Electrical Discharge Machining), and surface treatments to achieve the desired surface finish, dimensional accuracy, and mold longevity, adding complexity and cost to the manufacturing process.
Material Selection
Material selection is critical in small injection molding to meet the performance requirements and regulatory standards of the end-use application. Factors such as material compatibility, mechanical properties, biocompatibility, and sterilization resistance must be carefully considered to ensure the integrity and reliability of miniature components in demanding environments.
Process Control
Maintaining tight process control is essential in small injection molding to achieve consistent quality, dimensional stability, and repeatability in miniature parts. Factors such as temperature control, injection speed, packing pressure, and cooling time require meticulous monitoring and optimization to prevent defects such as sink marks, warpage, and flash in small-scale plastic components.
Future Directions and Innovations
Advanced Materials
Advancements in material science are driving the development of new materials tailored for small injection molding applications. High-performance polymers, bioresorbable materials, and conductive polymers are expanding the possibilities for miniaturized components in medical, electronics, and automotive industries, offering enhanced properties and functionality.
Additive Manufacturing Integration
The integration of additive manufacturing technologies, such as 3D printing and microfabrication, with small injection molding holds promise for accelerating product development and customization of miniature components. Hybrid processes combining additive and subtractive manufacturing techniques enable rapid prototyping, design iteration, and small-scale production of complex geometries with minimal tooling costs.
Industry 4.0 Integration
Industry 4.0 technologies, including IoT (Internet of Things), AI (Artificial Intelligence), and data analytics, are transforming small injection molding operations into smart, connected manufacturing systems. Real-time monitoring, predictive maintenance, and digital twin simulations optimize process efficiency, quality control, and resource utilization, driving productivity and competitiveness in the small-scale manufacturing sector.
Conclusion: Navigating the Realm of Miniaturization
In conclusion, small injection molding represents a cornerstone of modern manufacturing, enabling the production of precise, miniature components with diverse applications across industries. By understanding the advantages, challenges, and future trends in small injection molding, manufacturers can harness its full potential to drive innovation, efficiency, and sustainability in the production of miniature plastic parts.
As we look towards the future, continued research, innovation, and collaboration will shape the evolution of small injection molding technologies, paving the way for new materials, processes, and applications in the ever-expanding realm of miniaturization. Through strategic investments and partnerships, we can unlock new opportunities and address emerging challenges, ensuring that small injection molding remains at the forefront of advanced manufacturing in the years to come.
GETTING A QUOTE WITH LK-MOULD IS FREE AND SIMPLE.
FIND MORE OF OUR SERVICES:
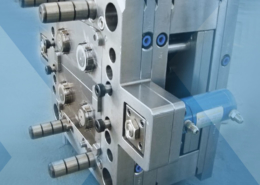
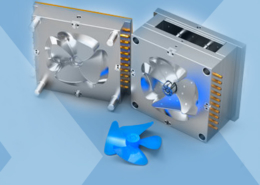
Plastic Molding

Rapid Prototyping
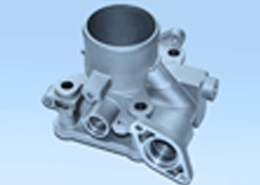
Pressure Die Casting
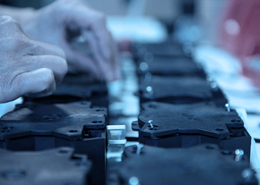
Parts Assembly
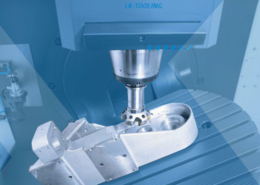