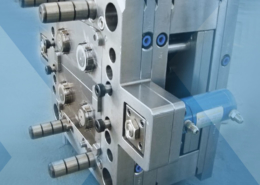
Injection molding of isotactic polypropylene - polypropylene injection molding
Author:gly Date: 2024-10-15
Insert molding and overmolding are both processes for using the injection molding process to mold plastic around something. The key difference is that overmolding is typically molding a rubber-like plastic over the top of another plastic component, while insert molding involves molding plastic around a non-plastic component.
After working through the above two steps (understanding your part function and optimizing your part design for manufacturing), you should have a solid set of parameters for material selection. The challenge with material selection is that there are literally thousands of overmolding materials to choose from, and new ones are developed practically every week. That’s why when we are evaluating a new overmolding project, we go straight to our suppliers and make sure we have the best materials for the job.
Overmolding is an injection molding process used to mold one plastic (commonly a rubber-like plastic called TPE) over top of another component (substrate). The substrate is usually an injection-molded plastic part, but it could also be made from various other materials. Overmolding is used across several industries and serves a wide array of purposes. Below are a few examples of overmolding applications:
Most plastics manufacturers have application engineers to evaluate each application and stay in touch with the latest developments. There is no reason not to leverage their experience and knowledge. At the same time, we want to understand some general factors in material selection, like adhesion. We also want to have a solid grasp of material properties, like hardness and friction.
With a manual operation, the substrate is injection molded via a traditional injection molding process. The substrates are then hand-loaded into another mold for the overmolding operation. The operator will also remove the finished part from the mold, provide an inspection, and package the parts. Manual overmolding is the most common procedure for low to mid-volume overmolding.
Material properties are important for applications requiring specific functions (like vibration absorption or grip). For overmolding TPE materials, there are a few properties that are key:
Generally speaking, the overmolding process is the same as an injection molding process, except that the plastic is molded over another component. The difference lies in operation. With overmolding, the substrate is loaded into the mold on each cycle. In addition, how the substrate is loaded creates two different overmolding operations:
ABS plastics provide a balanced combination of mechanical toughness, wide temperature range, good dimensional stability, chemical resistance, electrical insulating properties, and ease of fabrication.
ABS plastic is available in a wide range of grades including medium and high-impact, heat-resistant, plateable fire-retardant, and both low and high gloss varieties.
ABS Chimei PA-746H, Natural (High flow ability) ABS Chimei 777D, Natural (Super heat resistance) ABS Chimei PA-757, Natural (General purpose) ABS Chimei PA-758, Clear (Transparent grade) ABS Chimei PA-765A, Natural (UL94-V0) ABS Chimei 777B (Heat resistance grade) ABS Chimei PA-717C (High impact) ABS Chimei PA-737, Natural ABS LG -AF312A ABS Sabic Cycolac AS35, Snowy White (UV grade) ABS Sabic Cycolac FR15U, Natural ( indoor UV properties, UL94 V-0/5VA rated) ABS Terlux 2822HD (Good resistance to chemicals) ABS+10%GF Lupos-GP2100 (Flame retardant)
The advantage of manual overmolding is simplicity. The tooling required for the substrate and overmold is simple (when compared to two-shot tooling), and there is no secondary equipment required. The downside is the labor allocation and potential for inconsistent cycle times created by operators. As annual order volumes increase, the labor involved can become significant enough to justify investment in automation systems or a two-shot molding operation.
Note: Material properties are for general reference purpose only. Actual values may vary based on specific material brand selected.
Designing for overmolding can be difficult. However, ensuring your part is correctly designed for the overmolding process is critical. The design process starts with understanding the function of the part. Here are some good questions to ask upfront:
Once you clearly understand the function of your part, you want to look at the design of the part and make sure it’s optimized for the manufacturing process. Other design considerations include wall thickness, gate location, shrink, sealing features, and mechanical interlock features.
When selecting material, both the substrate and the overmold material should be considered. TPE plastic comes in several variations based on physical properties like elasticity and hardness, as well as its ability to adhere to other plastics. For example, one TPE could “feel” the same as another but may not adhere well to a polypropylene substrate. Here are some factors to consider:
GETTING A QUOTE WITH LK-MOULD IS FREE AND SIMPLE.
FIND MORE OF OUR SERVICES:
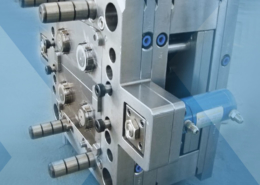
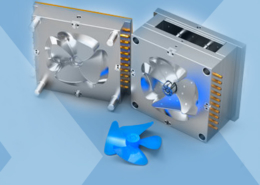
Plastic Molding

Rapid Prototyping
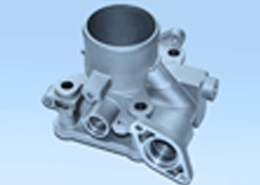
Pressure Die Casting
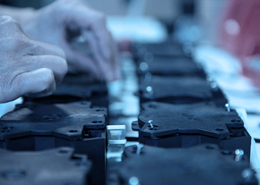
Parts Assembly
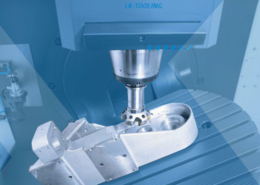