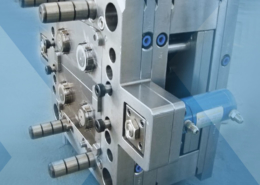
Injection molding of isotactic polypropylene - polypropylene injection molding
Author:gly Date: 2024-10-15
By signing up, you agree to our Terms of Use and Privacy Policy. We may use the info you submit to contact you and use data from third parties to personalize your experience.
Polystyrene is a commonly used injection molding plastic, but a good plan and skilled production partner are critical to avoid the added costs and risks that come with inadequate drying or improper processing methods. Fictiv has the global manufacturing network and production experts you need to get quality injection molded parts, no matter how complex your designs. And we have the skills and know-how to support you from part design through prototyping and production.
Equipped and experienced to satisfy your short-run, low-volume needs. Our quick-mold-change systems and Master Unit Dies enable us to make efficient mold changes, saving you time and money. We use proprietary batch molding procedures to optimize every aspect of short-run work. From purchasing and drying small lots to resource scheduling and shop floor sequencing, we provide unparalleled value from start to finish during short-run projects.
Injection molded polystyrene should have a wall thickness between 0.76 and 5.1 mm. If the change between sections is gradual, a wall thickness variation of 25% can be achieved.
Injection pressures for polystyrene can range from 100 to 200 Bar, and maintaining the pressure after injection can reduce overall shrinkage rates.
By signing up, you agree to our Terms of Use and Privacy Policy. We may use the info you submit to contact you and use data from third parties to personalize your experience.
Polystyrene has a low viscosity. This makes it ideal for injection molded parts with small features since material moves more easily throughout the mold. Different grades of polystyrene have different viscosities, however, and temperatures should be adjusted accordingly.
By signing up, you agree to our Terms of Use and Privacy Policy. We may use the info you submit to contact you and use data from third parties to personalize your experience.
Access a wide breadth of capabilities through our highly vetted network.
Polystyrene has a kilogray (kGy) value of 10,000, which means it absorbs very little radiation. This radiation resistance is due to the benzene ring in polystyrene’s molecular formula. Consequently, polystyrene can be subjected to radiation for sterilization purposes and won’t suffer a significant degradation of mechanical properties.
Injection molded polystyrene has low shrinkage values, typically between 0.4% and 0.7%. In some cases, however, it’s possible to achieve shrinkage less than 0.4%, such as near the sprue where there are high follow-up pressures. Only 10% of total shrinkage occurs after part ejection.
By signing up, you agree to our Terms of Use and Privacy Policy. We may use the info you submit to contact you and use data from third parties to personalize your experience.
If you’re looking for more injection molding design tips and insights for polystyrene and a variety of other materials, download the Fictiv Injection Molding Design Guide.
Polystyrene is a lightweight plastic, which is why it’s often used in food containers, consumer packaging, and even ceiling-mounted smoke detectors.
Our trained employees ensure your parts will be delivered on time and to spec.
By signing up, you agree to our Terms of Use and Privacy Policy. We may use the info you submit to contact you and use data from third parties to personalize your experience.
Polystyrene is relatively easy to injection mold, but it’s still important for part designers to follow guidelines in the following areas:
Polystyrene has a relatively high melting point of around 217°C, depending on the material grade. This is higher than other common injection molding plastics, such as polyethylene. Despite its high melting temperature, polystyrene begins to soften between 70°C and 106°C.
Plastic injection molding with polystyrene successfully requires choosing the right processing parameters. Here are some of the most important ones to consider:
Table 1 below lists some average physical, mechanical, and molding properties of various polystyrene injection molding grades:
Grades of polystyrene include GPPS and HIPS. General purpose polystyrene (GPPS) is naturally transparent and relatively brittle. High impact polystyrene (HIPS) contains additives that increase toughness but with a loss of transparency. When polystyrene is produced as a foam, types include extruded polystyrene (XPS) and expanded polystyrene (EPS).
By signing up, you agree to our Terms of Use and Privacy Policy. We may use the info you submit to contact you and use data from third parties to personalize your experience.
Polystyrene has a low shrinkage rate and is highly rigid. To ensure part ejection, apply draft angles between 0.5 and 1% and a polished finish to your molds to aid in part ejection.
Accelerate development with instant quotes, expert DFM, and automated production updates.
By signing up, you agree to our Terms of Use and Privacy Policy. We may use the info you submit to contact you and use data from third parties to personalize your experience.
By signing up, you agree to our Terms of Use and Privacy Policy. We may use the info you submit to contact you and use data from third parties to personalize your experience.
Create high quality custom mechanicals with precision and accuracy.
A faster alternative to custom plastic injection molding. Ideal for prototyping and low-volume production, our 3D-printing capabilities give us the ability to manufacture durable, high-precision, high-quality parts in small runs. Learn more about our 3D-printing services.
We exist to eliminate bottlenecks in new product development by integrating the people, processes, and platform you need to source custom parts.
Injected molded polystyrene has excellent dimensional stability. This is due, in part, to its amorphous nature, which reduces shrinkage after injection molding. Also, because polystyrene doesn’t absorb water, it won’t swell and increase in size.
Polystyrene resists moisture and generally does not need to be dried prior to molding. However, in cases where the resin may contain recycled material, or if the environment has high humidity, then pre-drying is recommended.
In its pure form (GPPS), polystyrene is transparent with 90% light transmissibility. It provides a relatively inexpensive alternative to other transparent plastics, such as polycarbonate or acrylic. GPPS can be brittle, however, and that’s why HIPS is sometimes used instead.
Polystyrene is highly resistant to moisture, which makes it a good choice for plastic cutlery, and laboratory and scientific products such as test tubes and petri dishes.
Many complex, high-precision industrial applications are small run by nature. As specialists in custom plastic injection molding these types of components, we are committed to providing the same level of dedicated customer service on short-run programs as on our longer-running work.
Part tolerances can be either commercial or fine, with fine tolerances having tighter values. For example, a .125-inch-thick part that’s 1 inch long can be held to a commercial length tolerance of ±.003 in/in. A fine tolerance would be ±.002 in/in.Tighter tolerance requirements increase the cost of the mold and of injection molded parts, however.
We exist to eliminate bottlenecks in new product development by integrating the people, processes, and platform you need to source custom parts.
Polystyrene is used in a wide range of applications because this injection molding material is lightweight, relatively inexpensive, and moisture resistant. Provided that proper part design and processing guidelines are followed, PS is relatively easy to injection mold.
By signing up, you agree to our Terms of Use and Privacy Policy. We may use the info you submit to contact you and use data from third parties to personalize your experience.
Increased temperature may improve moldability, but can have a negative effect on glossiness and material strength. In addition, higher temperatures result in longer cycle times since molded parts need more time to cool before ejection. For best results, keep temperatures below 250°C.
Although GPPS has relatively low impact strength, HIPS is strong enough to be used for protective packaging and in repeated-use applications such as cafeteria food trays.
HIPS polystyrene contains between 5% and 10% butadiene rubber so that it’s tougher and more rigid. Applications include automotive instrument panels and computer housings.
Polystyrene (PS) is a commodity thermoplastic with an amorphous structure. It has excellent resistance to gamma rays and, therefore, supports sterilization by radiation. Polystyrene plastics can be either transparent or opaque, and unmodified polystyrene is clear, rigid, brittle and moderately strong. Also, polystyrene is cost-effective and supports injection molding.
Polystyrene has a number of advantages that make it an ideal material for applications ranging from injection molded automotive parts to medical products. This thermoplastic has the following characteristics:
The recommended radius depends on the type of polystyrene — because GPPS is more brittle than HIPS, a radius that’s too small is a potential source of failure. In general, a minimum radius of 25% of the wall thickness is recommended. For high-strength parts, use a radius of up to 75% instead.
Create your free Fictiv account and request an injection molding quote today — we mold complex parts at ridiculous speeds!
GETTING A QUOTE WITH LK-MOULD IS FREE AND SIMPLE.
FIND MORE OF OUR SERVICES:
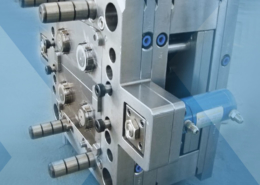
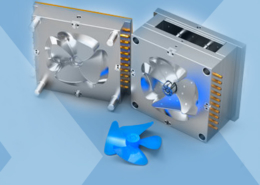
Plastic Molding

Rapid Prototyping
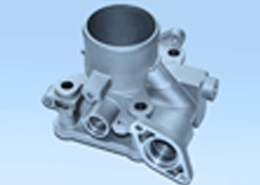
Pressure Die Casting
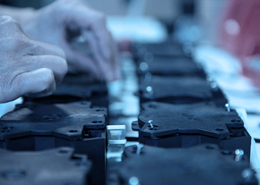
Parts Assembly
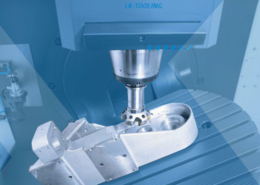