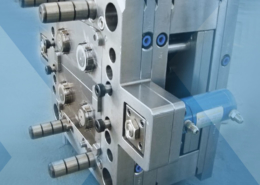
Injection Molding of ABS Air Conditioner Horizontal Vane - plastic molding for a
Author:gly Date: 2024-10-15
PVC (polyvinyl chloride) is easy to form under appropriate conditions, but it does require correct temperature, pressure, and mold design to ensure successful molding.
PVC has high dielectric strength, meaning it can withstand high voltages without dielectric breakdown. Combined with its flame-retardant and waterproof properties, PVC is an essential insulating material in electrical and electronic equipment, used in applications such as equipment housings and cable sheathing.
Upload your part drawings now, and our engineering experts will provide you with professional DFM feedback, helping you optimize product design to ensure its feasibility and efficiency during the injection molding process. Why go searching for a PVC injection machine when you can get expert DFM feedback and leverage BOYI capabilities?
Injection pressure depends on the size, shape, and gate opening size of the product. It is generally recommended to set the injection pressure between 80-120MPa (800-1200bar).
Acrylic is one of the most common plastics used in outdoor equipment. It’s favorable due to its UV-resistant, clarity, non-toxic, and scratch-proof properties. Its ability to evenly distribute additive applications such as colorants throughout the part during the injection molding process is also why it’s so valued when it comes to items like light fixtures, retail displays, reflectors, and colored lenses. However, the downsides to acrylic are that it’s brittle and inflexible – meaning it’s not ideal for parts undergoing high pressure – and it absorbs moisture, which requires drying the plastic.
Molding clear parts – such as water bottles or food-grade storage items – requires more focused attention to detail and stricter processing controls compared to non-transparent injection molding. Each transparent polymer has varying properties that can influence a company’s decision, including differing levels of strength needs, temperature requirements, and chemical resistance. Even environmental factors such as UV radiation can cause degradation in outdoor equipment utilizing clear plastics. That’s why it’s important to familiarize yourself with the best transparent plastic for your needs.
The following table contains typical physical, mechanical, electrical, processing, optical, and thermal properties of injection molded PVC.
BOYI offers both aluminum and steel molds for processing. Steel molds have a long lifespan, can be reused many times, and in some cases, can be repaired. For more information, please read this article on the differences between aluminum and steel molds: Aluminum vs. Steel Molds.
three disadvantages of polyvinyl chloride (PVC), PVC suffers from poor heat stability, making it prone to deformation at high temperatures. Over time, plasticizers migrate, affecting its properties. Additionally, flexible PVC has lower chemical resistance compared to rigid PVC.
Unlike the previous two plastics, polycarbonate is a highly impact-resistant – though more expensive – alternative. It shares the same transparency and UV resistance as acrylic, yet it’s stronger and far less affected by extreme temperatures. This plastic is used for products designed to handle a lot of stress, such as safety goggles, helmets, shields, heavy-duty containers, and safety windows. However, much like acrylic, this plastic tends to absorb moisture, making drying the resin necessary before the injection molding process.
Also known as PP, polypropylene is commonly used in containers, packaging, and textiles. Its high flexibility makes it an ideal choice for non-loadbearing parts, including working as a living hinge. You will also see it a lot in the textile industry, such as waterproof bags, totes, and gear. It doesn’t react easily with acids and bases, and it’s often used in containers for corrosive materials such as solvents. Likewise, it can be found within electronics due to its high electrical resistance.
Filed Under: Our blog Tagged With: acrylic, High-Density Polyethylene, injection molding, Polycarbonate, Polyetherimide, Polypropylene, thermoplastic, transparent plastic, UV resistance
PVC injection molding requires significant upfront costs for custom mold manufacturing. Mold costs can range from $1,500 to over $100,000. However, these costs can be amortized over the production of a large number of parts. If high volumes of identical parts are expected, PVC injection molding can be a cost-effective production method.
PVC (Polyvinyl Chloride) has relatively low production costs, making it more economical compared to specialty plastics and polymer blends. Its widespread use has resulted in a well-developed supply chain, making it easily accessible with low minimum order quantities (MOQs), which is particularly advantageous for small and medium-sized enterprises.
The commercialization of PVC began in the 20th century, with the first large-scale production carried out by the American tire company BF Goodrich. PVC exists in two main forms: rigid and flexible. Rigid PVC can be further subdivided into unplasticized (PVC-U) and modified (PVC-M) grades.
PVC is a high-demand material, and BOYI possesses extensive knowledge and experience in PVC injection molding. BOYI can provide customized PVC injection molding solutions tailored to customer requirements, assisting clients in completing various PVC injection molding projects.
Soft PVC experiences a decline in material properties over time or when exposed to adverse conditions such as UV light and high temperatures. Although rigid PVC has better UV resistance, it can also degrade when exposed to sunlight for extended periods.
For any questions or inquiries regarding rapid prototyping, CNC machining, sheet metal fabrication, or vacuum casting, please contact coco at [email protected].
Despite its relatively low tensile strength and thermal resistance, PVC’s versatility and other excellent properties make it an ideal choice for injection molding. PVC exhibits high impact strength, is easy to mold, and possesses relatively low rigidity and good chemical resistance. These characteristics make PVC an economical and recyclable material that is environmentally friendly.
High-density polyethylene (HDPE) is a commonly used thermoplastic that is created by applying high heat and pressure to petroleum. Similar to acrylic, it has UV resistance, but it also sports versatility and can be easily molded into various shapes. These features, paired with its inexpensive nature, is why it’s used in mass production of popular items such as bottles, pipes, and containers. However, though more resistant to pressure than acrylic, it’s still susceptible to high-pressure damage.
BOYI boasts rich experience and a professional team capable of meeting your PVC parts needs across various applications.
PVC can be modified with pigments and additives to change its color and appearance, making it suitable for various applications and design requirements. PVC injection-molded parts have smooth surfaces that are easy to clean, maintaining their aesthetic appeal over time.
If you are considering applying PVC injection molding technology to your next project, please continue reading to learn more about PVC injection molding.
Injection molded rigid PVC is widely used in construction, industrial, and other fields due to its high density, excellent stiffness, flame retardant properties, and outstanding impact resistance. For example, in the construction industry, rigid PVC is commonly used to manufacture components such as doors, windows, pipes, and machine housings.
The heat distortion temperature of PVC is relatively low, generally between 55°C and 85°C, depending on its formulation and processing conditions. This means that PVC products can easily deform at high temperatures, which affects their performance.
Mold temperature should be adjusted according to the size, shape, and performance requirements of the product. It is recommended to set the water temperature to 70-100°F, with the ejector side temperature being 10-20°F lower.
PVC demonstrates excellent flow and filling properties during injection molding, easily filling complex mold cavities to produce intricate, high-precision products. Its low shrinkage rate helps maintain dimensional stability, ensuring consistent product quality.
The PVC injection molding process is a precise and demanding procedure. PVC, as a thermoplastic, can decompose and produce harmful substances if overheated or subjected to excessive shear. To achieve high-quality PVC injection molded products, here is a comprehensive guide to the PVC injection molding process.
Among the many industrial thermoplastics, PVC (polyvinyl chloride) has won the favor of numerous manufacturers due to its wide range of applications, excellent performance, and low injection molding cost. From pipes and medical equipment to cables and building wall panels, PVC is ubiquitous.
Compared to rigid PVC, injection molded flexible PVC is known for its flexibility and customizability. By adding different types and amounts of plasticizers, the softness and elasticity of flexible PVC can be precisely controlled. This material finds extensive applications in the medical, automotive, and gardening industries.
Yes, PVC can be injection molded. As a thermoplastic, PVC possesses excellent processing capabilities. During injection molding, PVC material is melted at high temperatures and then injected into molds to produce the desired plastic products after cooling. This method is suitable for manufacturing plastic products of various complex shapes and sizes.
To meet the vast market demand for PVC products, manufacturers are continually seeking more refined and efficient production methods. One such method is PVC injection molding, a technique that involves precisely controlling temperature and pressure to inject PVC material into molds, producing parts of various shapes and sizes. This process fully leverages the non-hygroscopic and chemical-resistant properties of PVC, resulting in products that not only exhibit excellent performance but also offer high cost-effectiveness.
Barrel temperature is a critical factor affecting the flow of the PVC melt and product quality. It is recommended to set the temperatures for the feed zone, rear zone, middle zone, and front zone to 30-60°C, 160-180°C, 150-170°C, and 140-160°C respectively. These temperatures are for reference only and should be adjusted according to the actual conditions of the machine and materials, possibly exceeding the recommended range.
PVC injection-molded parts typically have high durability and strength, resisting everyday wear and tear. By adjusting the formulation and processing conditions, the physical properties of PVC injection-molded parts, such as hardness and toughness, can be further optimized to meet specific application needs.
The cushion of PVC remaining between the screw tip and the barrel after the mold cavity is fully filled should be adjusted based on the model of the injection molding machine and the requirements of the injection molded product, generally within the range of 2-3mm.
Due to the low thermal stability of PVC, the shutdown process is crucial. Before shutdown, the barrel should be thoroughly cleaned to prevent residual PVC from decomposing at high temperatures. Other thermoplastics with high thermal stability and no adverse reactions with PVC, such as PMMA, PP, LDPE, or GPPS, can be used for cleaning. Do not mix materials like POM and UPVC in the same barrel, as this can cause chemical reactions that damage the machine.
By following this PVC injection molding process guide, you will be able to produce high-quality PVC injection molded products that meet specifications. However, specific parameters and settings may vary depending on the machine, material, and product, so adjustments should be made based on actual conditions.
To optimize the molding cycle, the gate design should be as short as possible with a circular cross-section. It is recommended to use a conical nozzle with a diameter of 6mm and an internal angle of 5 degrees, equipped with a cold slug well to prevent poorly melted material from entering the cavity. The mold draft angle should be between 0.5° and 1° to ensure adequate mold venting. Common vent sizes are 0.03-0.05mm deep and 6mm wide, or a clearance of 0.03-0.05mm around each ejector pin. The mold should be made of stainless steel or hard chrome-plated for durability.
Back pressure is a key parameter in PVC injection molding for controlling the quality of the PVC melt and preventing overheating and decomposition. It should be controlled around 1MPa. Excessive back pressure generates too much shear force, leading to PVC overheating and decomposition. Multi-stage back pressure control should be used during plasticization to minimize the risk of shear force and thermal decomposition.
This article was written by engineers from the BOYI team. Fuquan Chen is a professional engineer and technical expert with 20 years of experience in rapid prototyping, mold manufacturing, and plastic injection molding.
Affordable high precision plastic molds and machined parts available for any order size | Contact our experts or engineers now for a quote!
PVC needs to be dried before injection molding to remove any trace moisture. It is recommended to dry at 75-90°C for 1.5-2.5 hours to minimize the impact of moisture on product quality.
Determining which of these is the best transparent plastic for your needs mostly depends on the functional performance requirements for your industry. There are many thermoplastic properties you need to consider when evaluating the conditions your part will be subject to. Here at Midstate Mold & Engineering, we can help you determine the right type of transparent thermoplastic for your part and can assist with prototype development to ensure integrity. If you have questions about transparent plastic resins or injection molding in general, contact us today.
PVC exhibits excellent chemical stability, resisting corrosion from many acids, bases, salts, fats, and alcohols. While it has poor tolerance to strong concentrated acids at temperatures above 60°C, PVC maintains its performance and appearance in various chemical environments.
PVC degrades easily at high temperatures. When heated, the unstable chlorine atoms in PVC start to detach, producing harmful substances like hydrogen chloride (HCl). To improve PVC’s thermal stability, heat stabilizers such as basic lead salts and metal soaps are commonly added during processing.
The screw speed should be adjusted based on the screw diameter and the performance of the injection molding machine. For screws with a diameter less than 60mm, the speed should be 50-70rpm; for screws with a diameter greater than 70mm, the speed should be controlled at 20-50rpm.
The L/D ratio is the ratio of the screw’s length to its outer diameter or nominal diameter. Generally, a screw L/D ratio of 20:1 is optimal, with a compression ratio between 1:1.6 and 1:1.2, to achieve good melt flow and product quality.
PVC is an amorphous white powder polymer with a glass transition temperature ranging from 77 to 90°C and begins to decompose around 170°C, demonstrating instability to light and heat. When exposed to high temperatures above 100°C or prolonged sunlight, PVC decomposes and releases hydrogen chloride, which further accelerates the decomposition process, leading to color changes and a rapid decline in physical and mechanical properties.
For any questions or inquiry about Mold manufacturing/Injection molding/Over molding/Insert Molding/Die casting , please contact one of our knowledgeable applications engineers at [email protected]
Polyetherimide (PEI) is a common plastic used in industrial, chemical, and mechanical parts. Aside from UV resistance, this thermoplastic is capable of withstanding intense pressure and heat and maintains its chemical stability when in contact with acids. This transparent material is often seen in the automotive, electrical, and medical industry due to its ability to tolerate extreme temperatures and repetitive forces. You’ll find its application in heat shields, temperature sensors, aerospace engine components, and various electrical parts and covers.
PVC, or polyvinyl chloride, is a polymer formed by the polymerization of vinyl chloride monomers (VCM) through a free radical polymerization mechanism, under the action of specific initiators (such as peroxides and azo compounds) or external conditions (such as light and heat). Due to its excellent performance and wide range of applications, PVC has become the third most produced synthetic plastic polymer globally.
In PVC injection molding, drying is typically not required, with the melting temperature ranging between 185-205°C and mold temperatures between 20-50°C. Additionally, if the temperature is not properly controlled during the heating process, PVC can degrade and release harmful gases, making precise temperature control critical in PVC injection molding.
PVC is recyclable, and with proper processing, it can be reused to manufacture new products, thereby reducing environmental impact. However, it’s important to handle and recycle PVC with care to mitigate the release of harmful substances, necessitating appropriate environmental measures.
The injection speed should be slow to avoid PVC degradation and then increased for large-scale production. When producing extremely smooth thick-walled products with UPVC, a multi-stage injection speed should be used. If light brown streaks radiate from the gate, it indicates that the injection speed is too fast.
GETTING A QUOTE WITH LK-MOULD IS FREE AND SIMPLE.
FIND MORE OF OUR SERVICES:
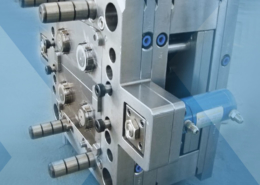
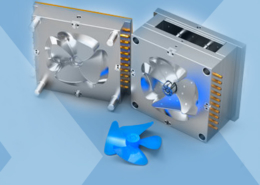
Plastic Molding

Rapid Prototyping
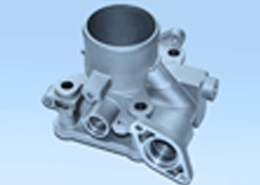
Pressure Die Casting
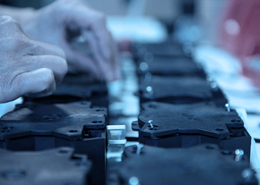
Parts Assembly
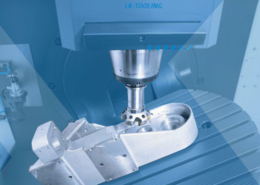