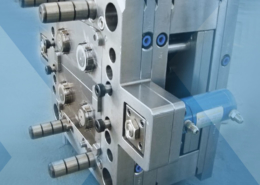
Injection Molding | Medbio, LLC - Medical & Biotechnology ... - medical injectio
Author:gly Date: 2024-10-15
Plastic offers a lightweight alternative to metal in automotive applications. One of the benefits of plastic is that it reduces the vehicle’s overall weight. This improves energy efficiency. As a result, plastic components are increasingly being installed in modern cars. Such parts can be found under the hood, in the car’s interior and on its exterior.
Viewmold company provides injection molding services for your part with PA6 plastic material. PA6 nylon injection molding processing condition Generic Class PA6 (Polyamide 6, or Nylon 6, or Polycaprolactam) Applications Used in many structural applications because of its good mechanical strength and rigidity. It is used in bearings because of its good wear resistance. Injection Molding processing conditions Drying Since PA6 absorbs moisture readily, care should be taken to ensure its dryness prior to molding. If the material is supplied in watertight packaging, the containers should be kept closed. If the moisture content is >0.2%, drying in a hot air oven at 80 C (176 F) for 16 hours is recommended. If the material has been exposed to air for more than 8 hours, vacuum drying at 105 C (221 F) for more than 8 hours is recommended. Melt Temperature 230 - 280 C (446 - 536 F); 250 - 300 C (482 - 572 F) for reinforced grades Mold Temperature 80 - 90 C (176 - 194 F). Mold temperature significantly influences the crystallinity level which in turn affects the mechanical properties. For structural parts, a high degree of crystallization is required and mold temperatures of 80 - 90 C (176 - 194 F) are recommended. High mold temperatures are also recommended for thin-wall parts with long flow lengths. Increasing the mold temperature increases the strength and hardness, but the toughness is decreased. When the wall thickness is greater than 3 mm, a cold mold is recommended (20 - 40 C / 68 - 104 F), which leads to a higher and more uniform degree of crystallinity. Glass reinforced materials are always processed at mold temperatures greater than 80 C (176 F). Material Injection Pressure Generally between 75 - 125 MPa (depends on material and product design) Injection Speed High (slightly lower for reinforced grades) Runners and Gates The gate location is important because of very fast freeze-off times. Any type of gate may be used; the aperture should not be less than half the thickness of the part. When hot runners are used, the size of the gates can be smaller than when cold runners are used, because premature freeze-off is prevented. When using submarine gates, the minimum diameter of the gate should be 0.75 mm. If you need high quality plastic extrusion services, Pls contact us sales@viewmold.com If you need high quality sheet metal parts, Pls contact us sales@viewmold.com Chemical and Physical Properties The molecular structure of polyamides consist of amide (CONH) groups joined by linear aliphatic sections (based on methylene groups). The toughness, rigidity, crystallinity, and thermal resistance of polyamide materials are due to the strong interchain attraction caused by the polarity of the amide groups. The CONH groups also cause a lot of moisture absorption. Nylon 6 is produced by polymerization of caprolactam. The chemical and physical properties are similar to that of PA66. However, its melting point is lower than PA66 and it has a wider processing temperature range. Its impact strength and solvent resistance are better than PA66, but its moisture absorption is higher. Many properties are affected by moisture absorption, which must be taken into account when designing with this grades. Various modifiers are added to improve mechanical properties; glass is one of the most commonly used fillers. Addition of elastomers such as EPDM or SBR improves impact resistance. For unfilled grades, shrinkage is of the order of .01 - .015 mm/mm (1 - 1.5%). Addition of glass fibers reduce the shrinkage to as low as 0.3% in the flow direction (but could be as high as 1% in the cross-flow direction). The post-molding shrinkage is affected mainly by the crystallinity level and moisture absorption. The actual shrinkage is a function of part design, wall thickness, and processing conditions. If you need to look for more plastic resin injection molding processing condition, could you please click it. If you need ABS injection molding Pls contact us sales@viewmold.com If you need high quality injection mold tooling, Contact us. The following is other plastic processing condition: ABS injection molding processing condition, HDPE injection molding processing condition, LDPE injection molding processing condition, PA12 injection molding processing condition, PA6 injection molding processing condition, PBT injection molding processing condition, PC-ABS injection molding processing condition, PC-PBT injection molding processing condition, PEI injection molding processing condition, PETG injection molding processing condition, PMMA injection molding processing condition, POM injection molding processing condition, PPE injection molding processing condition, HDPE injection molding processing condition, PP injection molding processing condition, PS injection molding processing condition, PVC injection molding processing condition, SAN injection molding processing condition,
Plastic components manufactured using injection molding offer greater options in terms of materials and colors. A wide range of polymers can be used, giving the designer more options and increasing the options for using plastics rather than metal.
For unfilled grades, shrinkage is of the order of .01 - .015 mm/mm (1 - 1.5%). Addition of glass fibers reduce the shrinkage to as low as 0.3% in the flow direction (but could be as high as 1% in the cross-flow direction). The post-molding shrinkage is affected mainly by the crystallinity level and moisture absorption. The actual shrinkage is a function of part design, wall thickness, and processing conditions.
Injection molding offers a number of benefits. One of the biggest advantages is the ability to produce a part consistently at a very high quality. Quality is essential to a vehicle’s safety and reliability. Plastic injection molding using ensures consistent and repeatable tolerances and a high level of precision.
No matter where they’re located, plastic components need to be high quality and robust. One of the most reliable methods for producing high-quality plastic components is injection molding.
Used in many structural applications because of its good mechanical strength and rigidity. It is used in bearings because of its good wear resistance.
We offer customers the same high quality regardless of the molded part’s complexity. We are a global solution provider, with locations in Europe, the US and China. So customers can be sure of getting the same high quality around the world.
The molecular structure of polyamides consist of amide (CONH) groups joined by linear aliphatic sections (based on methylene groups). The toughness, rigidity, crystallinity, and thermal resistance of polyamide materials are due to the strong interchain attraction caused by the polarity of the amide groups. The CONH groups also cause a lot of moisture absorption.
Injection molding offers a reliable and economical option for producing high-quality automotive components. forteq has been a leader in precision engineering and plastic molding for more than five decades.
With injection molding it is also possible to rapidly develop and test prototypes. forteq has its own in-house tooling center and can develop its own molds, thus reducing costs and time to production.
Injection molding is one of the most widely used processes for making plastic components. It’s an optimal solution for producing precise, high-quality parts.
The gate location is important because of very fast freeze-off times. Any type of gate may be used; the aperture should not be less than half the thickness of the part. When hot runners are used, the size of the gates can be smaller than when cold runners are used, because premature freeze-off is prevented. When using submarine gates, the minimum diameter of the gate should be 0.75 mm.
Nylon 6 is produced by polymerization of caprolactam. The chemical and physical properties are similar to that of PA66. However, its melting point is lower than PA66 and it has a wider processing temperature range. Its impact strength and solvent resistance are better than PA66, but its moisture absorption is higher. Many properties are affected by moisture absorption, which must be taken into account when designing with this grades. Various modifiers are added to improve mechanical properties; glass is one of the most commonly used fillers. Addition of elastomers such as EPDM or SBR improves impact resistance.
GETTING A QUOTE WITH LK-MOULD IS FREE AND SIMPLE.
FIND MORE OF OUR SERVICES:
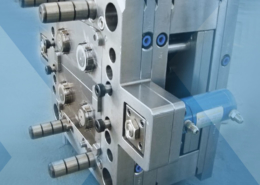
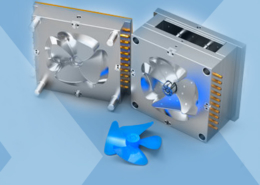
Plastic Molding

Rapid Prototyping
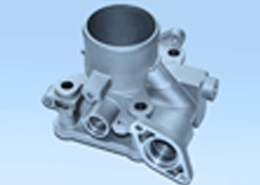
Pressure Die Casting
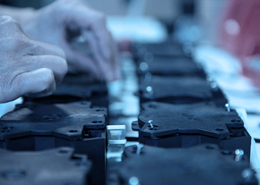
Parts Assembly
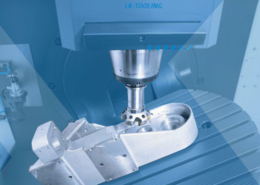