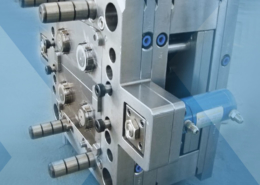
Injection Molding Machine small size 32, 42, 52, 72 Tons - small injection moldi
Author:gly Date: 2024-10-15
Automotive injection molding offers remarkable design flexibility for automotive part design. With a wide range of molds available, it becomes easier to create plastic components with intricate or unique shapes, without sacrificing production efficiency. This adaptability enables the development of innovative and distinctive automotive components.
What makes PP special? Well, it’s lighter than most plastics because it has a low density. So, it’s super useful when you want something that’s not too heavy. Plus, it’s tough against many chemicals and even water. That’s why you often see it used in stuff like food packaging.
High pressure is the name of the game here. We’re talking about pressures up to 1500 bars. But, here’s a fun fact: PP hates moisture. So, we need to keep it super dry, ideally below 0.2% moisture content. It’s like keeping your phone away from water; it just works better.
It might be difficult to choose the right materials for injection-molded automotive parts. Heat resistance, chemical compatibility, and structural specifications may all have an impact on the variety of materials that are available for a certain application.
Alternative manufacturing methods for automotive components offer distinct advantages and disadvantages compared to injection molding. Here are some notable alternatives:
Let’s break down the steps of molding polypropylene, or PP. First, we melt those tiny PP pellets. Then, we inject this melted goodness into molds. Next, we apply some serious pressure. And finally, we let it cool down. Sounds simple, right? But there’s more to it.
Stamping is a common method for shaping metal components in the automotive industry. It involves compressing a metal sheet between dies. Stamping is advantageous for its high-speed production, making it cost-effective for large quantities of components like body panels and structural parts. However, it may not be as versatile as injection molding for complex part geometries. Automobile manufacturers find value in employing metal stamping for components such as fenders due to the reusability of dies, ensuring the consistent production of parts.
Ever had toys that just won’t quit? Bet they had some PP components. This plastic’s got moves—it’s smooth, meaning things don’t wear out fast. Talking about its strength? Well, imagine a tireless runner. That’s PP for you, especially in the automotive industry. It’s perfect for automotive parts that face the hustle and bustle every day.
And you know what else? PP is super stretchy. Imagine a really, really stretchy rubber band, and that’s PP for you! It can stretch a whole bunch, sometimes even more than double. But it’s not just about stretching. If you bend it, it’s tough there too, with a strength of about 1.5 GPa.
This one’s an old friend. It’s the most common material, a polymer derived from propylene monomers. With its high flexural strength and fatigue resistance, it finds its place in numerous consumer products.
The automotive injection molding services provided by Xometry are evidence of our dedication to accuracy and quality in the manufacture of plastic parts for the automobile sector. We excel at mold design and have vast experience in precision custom molding for automobile parts. Our use of automotive-grade materials demonstrates our commitment to excellence and ensures that our products are durable and reliable.Â
Let’s paint a picture: Cars need parts that are light but also strong, right? PP is the go-to choice for this. Using the injection molding method, we get parts that are perfect for cars because they help save fuel.
The injection molding industry often defines molds by their class. This goes from Class 105, a prototype mold (e.g., a 100 piece one-and-done market test), to Class 101, which is built for extremely high production (e.g., making tens-of-millions contact lens cases). Xometry typically produces Class 104, 103, and 102 tools.
Many under-the-hood parts, including: intake manifolds, covers, and fluid reservoirs, are injection-molded for their heat resistance and durability. Injection molding is used for battery housing, ensuring secure placement and protection within the engine compartment. Components like air filter housings are often crafted using this process to optimize airflow and performance.
Nylon, a versatile synthetic polymer family, is favored in automotive injection molding. Comprising polyamides with amide links, it's a thermoplastic with a silky texture, ideal for crafting fibers, films, and various shapes. Automotive applications frequently involve using nylon to create components such as bushes and bearings, making it an essential material for durability and performance.
Now, temperature is a biggie. PP flows like honey when melted, thanks to its low melt viscosity. But, we need to keep things just right, between 200°C and 275°C. Too hot, and it might degrade. Too cold, and it won’t flow right.
Polypropylene, or PP, is a star when it comes to living hinges. Why? Its natural flexibility. But, to get it right, you need to focus on design. Aim for a wall thickness of about 0.5mm to 1mm. This ensures the hinge is flexible yet durable. And a tip? Make sure to reduce internal stresses; it helps in the long run.
A complex dance of propylene with other monomers results in block copolymers and random copolymers. They are generally more flexible and have better resistance to external conditions, making them ideal for certain applications where the homopolymer might falter.
Polycarbonate, a group of polymers with carbonate structures, stands out in automotive injection molding. Its unique structure enables transparency, transmitting light akin to glass. Automotive applications often leverage polycarbonate, crafting components like tail light housings, in which its optical properties and durability shine.
Okay, think of PP plastic as the everyday hero in the world of plastics. It’s like your daily coffee—it’s everywhere, and it won’t empty your wallet. In fact, using PP can make things cost up to 20% less. And the best part? No waiting around! It’s always there when you need it. Making products with it? It’s a total win.
Remember those advantages of PP we talked about? Here’s where they shine. In the food industry, PP is like the unsung hero. Those storage containers in your kitchen? Probably made of PP. It’s not just about being cost-effective. Its chemical and moisture resistance means your food stays fresh and safe. Imagine a container that can handle your hot soup and cold ice cream without a fuss. That’s PP for you.
Die casting is another alternative method used in the automotive industry, primarily for manufacturing parts from metals like aluminum and zinc. It is favored for its ability to create highly detailed and complex parts with tight tolerances. Metal injection molding is ideal for intricate small parts and large-scale production but involves many steps. Conversely, die casting, with fewer steps, is cost-effective for both small and large runs. Die casting is integral to the automotive sector, serving various roles like crafting engine components and producing brackets for stepper and electric motors.
Choose from millions of possible combinations of materials, finishes, injection molding tolerances, markings, and certifications, including ISO 13485, for your order.
In the world of PP injection molding, understanding the gating system is key. This is the pathway that guides the melted polypropylene into the mold, and it’s crucial for a successful molding process.
Moldmaker's choice of finish. Typically SPI B-3 to D-3 depending on geometry and drafts. Interior, non-cosmetic faces, are typically as-machined.
Medium production mold. This is a very popular mold for low to medium production needs. Most common price range. Also known as a Class III tool.
The Automotive Injection Molding Process at Xometry is a meticulously structured journey from tooling design to production. Our knowledgeable team carefully coordinates the design of the tooling and controls the mold-making process. The efficiency of molding cycles is improved without sacrificing quality. To ensure that automobile components meet the highest requirements and create products that excel in durability and precision, strict quality control methods are used throughout the process.
Prototype only. This mold will be constructed in the least expensive manner possible to produce a very limited quantity of prototype parts. Also known as a Class V tool.
Due to its distinct material properties, ABS (Acrylonitrile Butadiene Styrene) is a popular option in automotive injection molding. It combines acrylonitrile's chemical and thermal stability, butadiene's toughness and strength, and styrene's glossy sheen. Because ABS has a low melting point and is simple to shape, it is appropriate for many automotive applications, including coverings and dashboards that must be resilient and aesthetically pleasing.
The process of automotive injection molding comes with certain limitations, particularly when molding complex automotive parts. Designers must consider factors such as wall thickness uniformity and the filling performance of injection molding, which can influence the manufacturability and quality of the components.
Medium to high production, good for abrasive materials and/or parts requiring close tolerance. This is a high quality, fairly high priced mold. Also known as a Class II tool.
Do you recall playing with those modeling clays as a child? Imagine a slightly more sophisticated version of that. Plastic injection molding is where plastic materials (in this case, polypropylene) are melted and then injected under high pressure into molds. Once they solidify, we have our desired plastic parts. A process I’ve come to respect and admire for its precision and efficiency.
Polypropylene, a key player in automotive injection molding, is a synthetic resin renowned for its polymerization of propylene. As part of the polyolefin resin family, it excels in creating plastic products that demand lightweight properties, toughness, and flexibility. Automotive applications benefit from its usage in crafting external components like bumpers, as well as for cable insulation, highlighting its versatile role in the industry.
Now, let’s step into a hospital. Those medical devices and components? A lot of them trust PP. Why? Because it can be sterilized and stands strong against chemicals. It’s like having a reliable soldier in the medical battlefield. And don’t get me started on automotive parts. With its endurance, PP is often the go-to for parts that face daily wear and tear.
Applications of automotive injection molding encompass a wide array of components, enhancing the functionality and aesthetics of vehicles. Some of these applications are listed below:
Here’s something neat: PP plastic doesn’t let water or chemicals bully it. It has top-notch chemical resistance. So, when you’re thinking of food containers that don’t get all mushy with your lunch, or medical devices that stay strong, you’re thinking of polypropylene. It’s like the superhero cape for your spicy curry storage containers.
Next up, the runner. Think of this as the hallways in our house, branching out from the main entrance. The runner’s job? Distributing the molten PP to various parts of the mold. Now, here’s where things get interesting. Cold runner molds are commonly used in the plastic industry, especially for PP products. Their size? Often ranging between 3mm to 5mm in diameter. This size ensures a balance between material flow and cooling time, essential for product manufacturing with excellent resistance to defects.
Ah, the world of polypropylene injection molding. Brings back memories, doesn’t it? Of course, for some, it may seem like an intricate web of terminologies and processes. But don’t fret, dear reader. As a woman of experience, I’ll take you down the nostalgic alleys of my past where injection molding held my hand through various projects.
Automotive injection molding stands out as a cost-efficient solution for component production. Many metal parts are costlier to manufacture than their plastic counterparts. Scarce resources often drive up the price of metals used in automotive components like wheel rims and chassis, making plastics a more economical choice.
Injection molding yields lightweight and impact-resistant bumpers, safeguarding both aesthetics and safety. Vehicle grilles are often molded, combining design intricacies with functionality. Exterior mirror housings are frequently produced using this method for their durability and design flexibility.
Curves and angles are key in PP projects. For radii, aim for at least 0.5 times the wall thickness. It helps in reducing stress points. And for draft angles? A 1° to 2° angle is a good rule of thumb. It ensures the molded parts pop out smoothly without any hitches.
Injection molding is a highly automated process, which reduces labor costs significantly. This automation contributes to cost efficiency, especially for large-scale production.
Xometry's injection molding service has decades of experience making plastic parts used in automotive applications. Our strength is in saying "yes" - we help our customers make parts that others can't make. Automotive companies large and small have found value in our highly customized services including:
Imagine the sprue as the front door of a house. It’s the primary channel where our molten polypropylene, a popular thermoplastic polymer, makes its grand entrance. Typically, the sprue’s diameter is designed to ensure a smooth flow, but it’s essential to remember that its size can influence the plastic injection molding speed. A larger sprue might speed things up, but it could also lead to wastage.
One little thing to note: after you mold it, PP likes to shrink a tiny bit as it cools. Think of it like that shirt that gets a bit smaller after you wash it the first time. So, if you’re making something with it, just remember this, so everything fits perfectly. Neat, huh?
So, you’ve heard of polypropylene, right? Most folks just say PP. It’s light, weighing in at around 0.895 to 0.92 g/cm^3. But here’s the cool part: even though it’s light, it’s super strong. We’re talking about handling big-time pressure, like around 30 MPa kind of strong.
For your free quote and design-for-manufacturability feedback, please upload your CAD file, or download our Injection Molding Design Guide. We want to earn your business. If you get a lower injection molding quote, send it to us and we will try to beat it.
Think of PP molding like making pancakes. Too thick, and it won’t cook evenly; too thin, and it might tear apart. For PP, a consistent wall thickness, ideally between 1mm to 4mm, works best. And watch out for those sink marks; they can sneak up if the design isn’t spot on.
And guess what? Making stuff with PP is super fast. Sometimes it takes just a few seconds for one cycle, depending on what we’re making. So, it’s great for making lots of things quickly, which saves money in the long run.
The speed of automotive injection molding machinery, coupled with the efficient thermoplastic molding process, enables rapid production of automotive components. This swift manufacturing process makes it possible to mass-produce parts quickly, meeting the industry's demands for timely supply.
Elements like: instrument panels, air vents, and glove-box doors are efficiently manufactured through injection molding. Door handles, armrests, and panel trim are often produced using this process, ensuring precision and durability. Seat-belt parts, clips, and various interior trim pieces are injection-molded for seamless integration into the vehicle's interior.
Built for extremely high production. This is the highest-priced mold and is made with only the highest quality materials. Also known as a Class I tool.
Automotive injection molding stands out for its exceptional material efficiency. The process minimizes waste generation, as it precisely shapes components with minimal excess material. This efficiency not only translates into cost savings but also promotes environmental sustainability by reducing material waste and the associated environmental impact, aligning with modern eco-conscious manufacturing practices.
The expensive tooling required for automotive injection molding is a major drawback. Each injection molded part needs a unique tool, which increases the cost of the initial setup. Compared to huge, sophisticated molds made for full-scale manufacturing, tooling for simple designs and small production runs may cost between $2,000 and $5,000. To minimize these costs, working in partnership with an injection molding manufacturing partner can assist in optimizing the budget and improving mold designs.
CNC automotive machining refers to a broad range of operations that can be successfully used on a variety of materials, including: metals, polymers, and composites. These operations include: CNC turning, milling, and drilling. It is particularly well suited for the production of complex automotive components, including: lighting systems, engines, and gearboxes because of its adaptability and versatility. Contrasting with injection molding's strength in mass manufacture of plastic parts, CNC machining is often chosen for custom or low-volume production as well as the creation of prototypes, in which precision and customization are important.
Low production mold. Use only for limited production preferably with non-abrasive materials. Low to moderate price range. Also known as a Class IV tool.
If you’re venturing into the world of injection molding, remember, choosing the right partner can make all the difference. ACO Mold makes over 300 mold on various products annually. With its expertise and commitment to quality, we can be the ally you need to bring your visions to life.
For automobile injection molding, Xometry only uses sophisticated thermoplastic materials and plastics of the highest quality. The selection of these materials ensures that the produced components fit the stringent requirements of the automobile sector thanks to their remarkable durability, chemical resistance, and lightweight qualities. We use the following materials for injection molding:
When manufacturing parts in bulk, automotive injection molding's cost-effectiveness clearly shows. The method is a favorite for high-production runs in the automobile sector due to its effectiveness and low cost per unit. High tooling costs are a considerable disadvantage for lesser volumes, though, leading to the consideration of alternative manufacturing processes that are more cost-effective for smaller-scale production.
Injection molding excels in achieving precision for automotive part manufacturing. The process allows for intricate and accurate designs, ensuring that components meet exacting specifications, resulting in high-quality and consistent products.
Range of finishes including matte, swirls, lines, and patterns. Finishes include: MoldTech - MT11010 MoldTech - MT11020 MoldTech - MT11030 MoldTech - MT112XX MoldTech - MT114XX MoldTech - MT116XX
So, let’s wrap this up. We’ve dived deep into this plastic stuff called polypropylene. It’s super cool how it doesn’t let water or chemicals mess with it. This makes it great for things like food boxes and even car parts. Plus, it’s friendly to our wallets. It’s more than just making stuff – it’s thinking ahead and being smart. Here’s to the rockstar of plastics, polypropylene, and its big future!
Now, There are various types of gates available, choosing the right gate is like picking the perfect outfit. It needs to be just right. For PP, we often use pin gates. Why? Because they offer a good balance between flow control and minimizing stress on the material. The diameter of a pin gate is usually about half of the wall thickness of the part being molded. This ensures a fast injection molding speed while also preventing defects.
Multiple-cavity steel tooling with full automation and overnight production workcenters for dedicated part manufacturing.
Lastly, the gate. This is the last stop before our PP fills the mold cavity. It’s like the doorway to a room. The gate’s depth and type play a pivotal role. For instance, a depth of the gate that’s about half of the wall thickness ensures optimal flow.
We are ISO 9001:2015 certified and AS9100D compliant. Only the top machine shops that apply to become suppliers make it through our qualification process.
Ever noticed how some plastics shrink a bit after cooling? That’s PP for you. It can shrink by about 1-2.5%. So, when designing, always account for this little quirk. Think of it like buying a cotton shirt a size bigger because you know it’ll shrink after the first wash.
We have a reputation for taking on difficult projects and providing services like: thorough design for manufacturing (DFM) reviews, production part approval process (PPAP) submissions, a variety of material choices, and adaptable tooling solutions. We have received certification that our quality management systems meet the exacting requirements of IATF 16949 and the VDA. The talented experts at Xometry will expertly lead you through the injection molding procedure to provide premium car components.
Range of finishes from Grade 3 diamond / high polish to 320 stone low polish. Finishes include: SPI A-1 SPI A-2 SPI A-3 SPI B-1 SPI B-2 SPI B-3 SPI C-1 SPI C-2 SPI C-3 SPI D-1
Designing automotive parts for injection molding can be complex. Achieving the desired geometry, tolerances, and surface finishes while adhering to manufacturing limitations can be challenging. Designers must carefully navigate these complexities to ensure that the final components meet both functional and aesthetic requirements.
You know, polypropylene (or PP for short) is pretty cool in the world of plastics. It’s a type of plastic polymer that can melt and be remolded without getting ruined. Imagine something that melts between 160°C to 220°C, and that’s PP for you! That’s why many industries love it for high-heat work.
GETTING A QUOTE WITH LK-MOULD IS FREE AND SIMPLE.
FIND MORE OF OUR SERVICES:
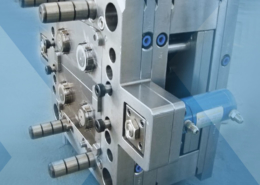
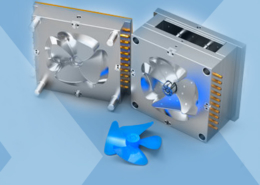
Plastic Molding

Rapid Prototyping
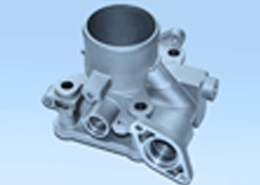
Pressure Die Casting
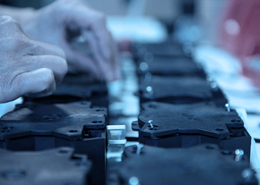
Parts Assembly
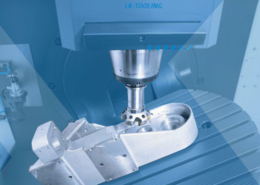