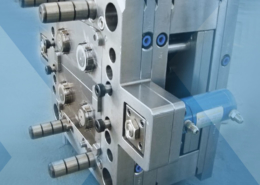
Injection Molding Machine and Mold Design - sumitomo injection
Author:gly Date: 2024-10-15
Gas assist plastic injection molding produces parts without compromising appearance or functional performance. Other benefits include:
PVDF has particularly good weather resistance and superior mechanical strength than other fluorinated resins. According to the different polymerization and post-treatment process, as well as different applications, PVDF resin can be divided into coating grade, injection molding grade, extrusion grade, wire cable and film application grade. Grade HD9106 is for PVDF extrusion molding, please see the table below for some typical parameters of this material.
PVDF is a homopolymer of VDF, which is a partially fluorinated polymer initiated by a free radical initiator, with 59.4% fluoride, 3% hydrogen (mass fraction). It is a partially crystallized polymer, long-term service temperature and chemical resistance slightly inferior to FEP. Recommended service temperature range from -60℃to 150℃.
PVDF(Polyvinylidene Fluoride)is a melt processable engineering thermoplastic. It has the characteristics of fluorine resin and general resin. Because of its excellent weather resistance, good mechanical properties and can be used to prepare solvent based coatings, PVDF is mainly used in weather resistant coatings, extrusion molding, injection molding and other processing technology. PVDF Extrusion Molding Grade HD9106 is available in pellet or powder, showing the following properties: <1> MFR: 1-8 g/10min; 8-15 g/10min; 15-24 g/10min; above 24g/10min <2> Tensile Strength:≥36 Mpa <3> Elongation at Break: ≥25% <4> Melting Point: 165-176℃ <5> Relative Gravity: 1.77-1.79
EVCO Plastics has employed gas assist molding technology for plastic injection molding in a wide range of applications for over 25 years, providing OEMs with numerous advantages for custom plastic injection molded plastic parts and products. Gas assist injection molded plastics are a great option for companies looking to reduce time and cost without sacrificing quality or design options.
Gas assist molding is a low-pressure plastic injection molding process where pressurized nitrogen gas is injected into the mold, pushing the plastic into the mold extremities, while hollowing out thicker sections in the part.
PVDF Extrusion Molding Grade HD9106 is suitable for producing products such as PVDF pipes, PVDF rods, PVDF tubes, boards and fittings by injection and extrusion molding process. The finished products has excellent mechanical strength, good durability and flexibility, stability in wide temperature range.
In the gas assist molding process, the plastic material is melted and injected into the mold cavities via the conventional plastic injection molding process. Plastic material in contact with the mold walls begins to solidify first. As this happens, nitrogen gas is injected into the mold through strategically designed and placed gas channels, providing pressure that pushes the plastic material into the mold extremities. Once the plastic cures, the nitrogen is vented and the gas assist injection molded plastic parts are removed from the mold.
GETTING A QUOTE WITH LK-MOULD IS FREE AND SIMPLE.
FIND MORE OF OUR SERVICES:
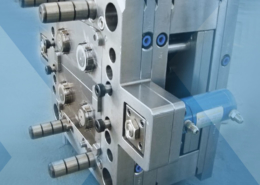
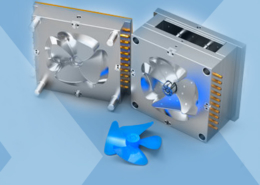
Plastic Molding

Rapid Prototyping
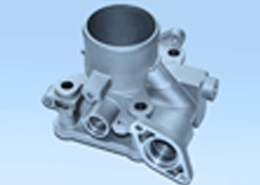
Pressure Die Casting
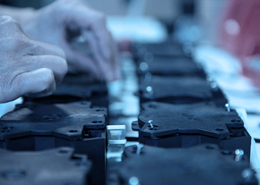
Parts Assembly
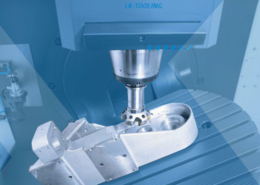