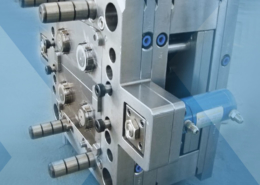
Injection Molding Finish Options | Polishing and Texturing - injection mold poli
Author:gly Date: 2024-10-15
Selecting specific materials, such as high-performance plastics, often results in increased expenses. However, optimizing designs and manufacturing processes to reduce material wastage can significantly lower overall costs. While incorporating recyclable materials might lead to a modest increase in initial expenses, it paves the way for more sustainable practices and could prove economically beneficial over time.
In contrast, simpler mold designs with fewer complex features result in lower tooling costs, making them a more cost-effective choice, especially for applications where intricate features are not essential. Striking a balance between design requirements and cost considerations is essential in optimizing injection molding expenses.
Injection molding costs are a focal point for plastic product manufacturers utilizing this process. This article delves into the intricacies of injection molding costs, shedding light on various factors that contribute to the overall expense. By unraveling these elements, you can gain valuable insights into optimizing costs for your specific project.
Recognizing the fluctuating nature of pricing and the vital role injection molding cost estimates play in projects, we have crafted an illustrative example to help better understand the cost estimation process.
The extremely high level of precision needed within the aerospace industry makes CNC machining a suitable manufacturing process for the sector.
Part inspection costs can be specialized or standard. On the one hand, standard inspection is an internal process that requires trained personnel to check for part defects (cosmetic or critical) and a quality verification team to identify the probable cause. On the other hand, specialized inspection involves inviting specialized engineers to inspect the product. Thus, specialized certification costs more, and sometimes injection service providers offer the certification at a cost.
You can count on us to help bring your project to market. We will create a clear project management plan and ensure that you are kept informed about your project at every stage of the process.
The equipment used in the molding process is unique. The cost of a machine depends on the size and its level of sophistication (often measured in terms of automation), and it ranges from $10000 (small) or less suitable for low-volume injection molding to $200,000 (large) suitable for high-volume injection molding. Medium molding machines ($50,000 or more) can also be tailored for medium-level molding. Also, you need to consider the following types of injection molding machines and how they affect the cost:
We have several plastic materials chosen using a stringent and streamlined selection process and an engineering team that can provide professional design suggestions and material selection. Our highly sophisticated manufacturing capabilities and network allow us to ensure high-quality molds and plastic parts. Upload your design today and get instant quotes and free DfM analysis at a competitive price.
Rutland Plastics is 65 years old and to celebrate we made a video. We certainly look different today from when the company first started out injection moulding in 1956. Expansion has continued on the site in Oakham and now exceeds 6130 square metres, we employ over 150 staff with an approximate turnover of £15million. Today Rutland Plastics is still a family run custom injection moulder for a wide variety of industries. Throughout the company’s history we have retained a steadfast dedication to building strong partnerships with both customers and suppliers while consciously investing across the business.
Note: not all parts will require surface finishing or other secondary services. As a result, you should ensure you need such services to increase overall production efficiency and less material wastage.
The production volume affects the amount of raw injection molding material required, the sophistication of the injection molding machine, and the injection mold’s strength/durability/other mechanical properties. The volume of production is divided into three major categories:
More complex molds, characterized by intricate features, undercuts, or intricate geometries, generally involve higher tooling costs due to increased manufacturing complexity. These molds require specialized machining and longer production times, contributing to elevated upfront expenses.
The choice of mold material influences both the upfront investment and the overall efficiency of the manufacturing process. Mold materials vary in cost and durability, with aluminum and 3D-printed molds offering lower upfront expenses suitable for low-volume production.
Part packaging costs depend on whether the packaging is consumer-facing (i.e., recognizable and short-span) or more costly shipping packaging. Consumer-facing packaging is suitable for products that are ready to use. However, larger manufacturers can use automatic packaging, which reduces damage and incurs fewer errors.
This approach simplifies the mold design, leading to lower manufacturing costs as complex molds are more expensive to produce. Furthermore, reducing part complexity translates to decreased material usage, offering direct savings. Additionally, simpler designs can shorten the molding cycle, boosting productivity and cutting down on labor and energy expenses. This also results in molds that are less demanding in terms of maintenance. Importantly, such streamlined designs often yield parts with improved structural integrity and consistent quality, reducing the likelihood of defects.
On the other hand, smaller mold cavities are generally more cost-effective due to reduced material usage and simpler mold construction. The choice of mold cavity size should align with production requirements, as optimizing for the right balance between cavity size and part dimensions can result in cost savings in both material consumption and tooling expenses.
Knowing about the injection molding cost can help in optimizing the manufacturing process. This is achievable by understanding different factors and elements, and this article discussed everything you need to know about costs in injection molding and how to use it. Looking for a quality-focused injection molding service provider? At RapidDirect, we offer the best at a competitive price.
Our extensive range of state of the art injection moulding machines means that most custom moulding requirements can be met.
ITG (Induction Technology Group) are manufacturers of high performance air filters for motorsport and road car applications. Rutland Plastics has worked closely with ITG for some time manufacturing various different products.
Quality injection molded parts and a cost-effective process are achievable by trusting the right injection molding services. At RapidDirect, we offer custom plastic injection molding services to help you make different plastic prototypes or real parts based on your requirements.
Maximizing the lifespan of molds is a cost-effective approach in injection molding. Reusing molds for multiple production runs helps distribute tooling costs across a larger production volume, reducing the per-part cost. Regular maintenance and careful handling of molds can extend their life, providing long-term cost benefits for manufacturers.
Larger mold cavities, capable of accommodating higher material volumes and producing more significant parts in each cycle, typically necessitate more substantial and, consequently, costlier molds.
Please navigate to our online quotation platform and upload an injection molding CAD file to get a quick quotation. Our quotation process is comprehensive from start to finish and involves configuring different materials, finishes, quantities, etc. Furthermore, we will confirm the DFM analysis of the mold so that you get the most accurate part possible.
Surface finishing includes processes such as annealing, sandblasting, powder coating, etc., in which the part is subjected to increase its aesthetic appeal or functionality. They are separate from the injection molding process itself. However, many service providers will give a discount to clients using them for both injection molding and surface finishing. Also, there are secondary services which can be manufacturing processes(e.g., machining and drilling), assembly services (e.g., sonic welding), and decorating (e.g., pad printing), which can increase the injection molding cost.
This will require a strong injection mold made from steel due to its long life expectancy, many materials, and, if possible, a sophisticated machine. This should increase the injection molding cost. However, the high cost will be distributed among the parts, reducing the cost per part manufactured. It is important to note that there is a higher cost distribution per part in high-volume production than in medium-volume production. As a result, they have a lower cost per part manufactured.
Despite this, the overall manufacturing cost decreases as production scales up. Hence, plastic injection molding is widely considered a cost-effective solution for mass-producing plastic parts, with the price per part decreasing as quantities increase.
“Rutland Plastics have provided support and expertise throughout the whole design and manufacturing process and it’s great to work with a team who share the same values as us".
In contrast, high-volume production often demands molds made from robust materials like steel, incurring a higher initial cost but providing extended tool life and minimizing the cost per unit produced. The selection of mold material, therefore, becomes a strategic decision balancing short-term expenditure with long-term efficiency and cost-effectiveness in injection molding operations.
To effectively reduce unnecessary features, a thorough design review is essential, focusing on optimizing part geometry for both functionality and manufacturability. This might involve reevaluating the necessity of certain aesthetic elements, consolidating multiple components into a single, more efficient design, or modifying part dimensions to eliminate redundant or non-critical aspects. The goal is to achieve an optimal balance between the part’s functional requirements and the cost-effectiveness of its production.
You will benefit from expert guidance and support in every aspect and we will do so collaboratively with the promise that you will be able to speak to our technical team whatever your enquiry.
Offering you a full range of plastic injection moulding services from design, including mouldflow, prototyping and mould making to injection moulding and a wide range of additional services such as machining and assembly.
Instead of buying a machine, businesses outsource their project to injection molding service providers. So they no longer incur the heavy cost of purchasing the machine but are subject to the service provider’s service cost.
We were therefore ideally placed to assist quality audio equipment specialists Rega. When the company decided to move production of their clear acrylic turntable dust covers back to the UK, they specifically sought a manufacturer with combined expertise in both plastic injection moulding and tool making, who would be able to meet their exacting standards.
While high-performance plastics may offer specific advantages, they often come with a higher price tag. Analyzing the functional requirements of the part and selecting a cost-effective material that meets those needs can lead to substantial cost savings without compromising quality.
"We are engineers, we look for equally skilled supply partners for difficult and advanced manufacturing. Partners that possess the expertise and the same passion for perfection are essential to our development projects”.
The tooling cost incurred during injection molding depends on the machining process used in making the mold, the material used, mold complexity, and mold cavity size.
There are several best practices to minimize injection molding costs without compromising quality. By strategically implementing these practices, businesses can achieve cost-effective production and enhance overall efficiency.
Determining whether injection molding is expensive isn’t a straightforward answer. While the process proves cost-effective for mass production of plastic parts, the initial setup costs can be substantial due to high machine prices.
In some applications, the cosmetic appearance of a part may not be critical to its functionality. Choosing to forego intricate cosmetic details can result in faster production cycles and reduced tooling complexity, ultimately contributing to lower costs. This practice is particularly relevant for parts where aesthetics are secondary to functionality.
Larger parts require more material, leading to higher raw material expenses. They also necessitate bigger, more energy-consuming machines with longer cycle times, reducing production efficiency. As part size increases, maintaining precision becomes more challenging, possibly requiring advanced, costlier processes. Additionally, larger parts can produce more waste, especially in the runner system where excess material is generated, further elevating costs.
Several factors directly impact your costs, and understanding these key elements is crucial for optimizing your project’s financial aspect.
As our customer. your plastic injection mouldings will be manufactured using the most cost effective production methods.
Complex designs often require intricate molds with finer details, increasing initial tooling expenses. They may also necessitate advanced machinery and tighter tolerances, leading to higher operational costs and longer production times. Complex plastic molded parts often result in increased cycle times due to additional cooling and setting requirements, reducing overall manufacturing efficiency. Furthermore, the potential for defects rises with complexity, leading to higher rates of waste and rework.
Whether it is low volume or pre-production tooling or even high speed, multi-cavity stack tools, we are able to specify and manufacture the most appropriate mould tools for our customers.
A well-designed part can reduce material usage, simplify mold design, and shorten cycle times, all of which lower manufacturing expenses. Optimizing wall thickness, incorporating uniformity, and minimizing undercuts can lead to more efficient production processes and less material waste. Conversely, complex geometries and poor DFM can lead to increased tooling adjustments, higher defect rates, and prolonged production cycles.
Insert molding involves placing pre-formed components or inserts into the mold before injection. This technique allows for the integration of multiple parts into a single molding process, reducing the need for additional assembly steps. Naturally, a single-step process would mean a lower machine run-time and a lower number of repetitions and cycles. Furthermore, you won’t be assembling separately designed parts together as well and that again would save time. By consolidating manufacturing steps, insert molding can lead to time and cost savings.
Using the toughest 3D-printing materials ever created, Rutland Plastics has the capability to produce rapid fully functional prototypes in-house for you to confidently test the functionality of your products prior to committing to the investment in a mould tool. Our additive manufacturing capacity means that we can create jigs and fixtures with speed and efficiency at a far lower cost than traditional manufacturing methods.
This category necessitates a straightforward mold, often crafted from cost-effective materials like aluminum or 3D-printed materials. Additionally, it requires minimal raw materials and less advanced machinery, resulting in an overall low injection molding cost. However, the cost per unit part tends to be higher in low-volume production scenarios.
Streamlined tool designs contribute to shorter cycle times in the molding process, enhancing production efficiency and reducing manufacturing costs. They also minimize material waste by lowering rejection rates and decreasing scrap material. Additionally, simpler molds are easier to maintain, which prolongs their lifespan and lessens the frequency and costs of repairs and replacements.
To simplify mold designs, it’s crucial to eliminate unnecessary features, optimize part geometry, and consider using standardized components. Utilizing CAD and CAM tools can help in identifying and removing superfluous elements, ensuring efficient mold design without compromising product quality.
If you want to produce high-quality machined parts with a sleek appearance, it’s essential to consider some critical factors related to CNC machining.
GETTING A QUOTE WITH LK-MOULD IS FREE AND SIMPLE.
FIND MORE OF OUR SERVICES:
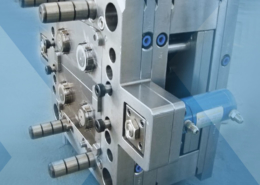
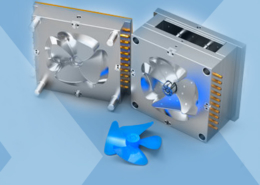
Plastic Molding

Rapid Prototyping
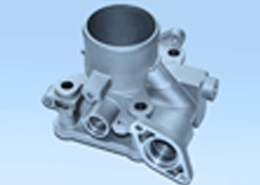
Pressure Die Casting
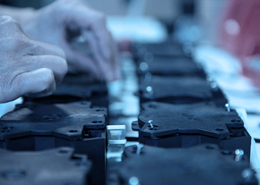
Parts Assembly
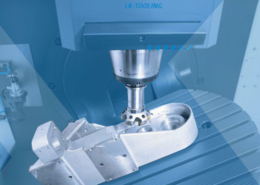