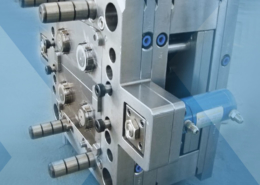
Injection Molding Design for Dummies - China Metal Parts, Corp. - injection mold
Author:gly Date: 2024-10-15
If you disable this cookie, we will not be able to save your preferences. This means that every time you visit this website you will need to enable or disable cookies again.
When creating custom plastic enclosures, whether for electronics, consumer products, or industrial equipment, the manufacturing process you choose profoundly impacts design requirements. One of the most widely used manufacturing methods for plastic enclosures is injection molding. However, the injection molding process has its considerations that designers must navigate to achieve functional and aesthetically pleasing results. […]
Molten material—typically thermoplastic polymer—is injected into a mold to create a solid shape. Examples: plastic combs and three-dimensional objects with openings, such as crates. Injection molding typically has a higher initial cost given the complexity of the mold structure, but the process creates a finished piece that doesn’t require assembly or secondary processing.
Think structural foam molding is an alternative solution for you? We encourage you to contact us to discover how structural foam molding can benefit your business.
Secondary operations complement our extrusion operation. Secondary operations include forming, notching, punching, piercing, drilling, tight tolerance sawing and other assembly capabilities.
Extrusion is ideal when a variety of lengths of a constant cross-section is required. By producing stock with a continuous production process, setup and die costs are lower when compared to injection molding where a unique mold would be required for each length.
Structural foam molding also scales well, allowing large or bulky parts to be manufactured while still retaining the superior production speed offered by injection molding. Regardless of size, structural foam parts are able to be worked post-production in a manner similar to parts constructed of wood or metal. The surface of a finished part is smooth offering the potential of easy cleaning, and can be painted over.
Material is heated and forced through an opening cut into series of metal plates with a shape similar to the final product, creating a continuous form that can be stretched and then cooled to shape before cutting to length. Examples: tubing and window profiles.
We’ve been busy putting structural foam molding through its paces to build a variety of parts, including gas pump front fascia. Results have been everything we could have hoped for. Along with the durability offered by the new parts, the material options available for structural foam molding also means a finished product can be chemical resistant, offer electrical or thermal insulation, and can be developed for outdoor applications.
This website uses cookies so that we can provide you with the best user experience possible. Cookie information is stored in your browser and performs functions such as recognising you when you return to our website and helping our team to understand which sections of the website you find most interesting and useful.
Traditional injection molding is typically done in two stages. There’s an injection stage where melted thermoplastic is injected into a mold, and a packing stage where pressure is built and the plastic is formed into the shape of the mold. In structural foam molding, the injection stage is basically the same, but the packing stage is augmented by a chemical blowing agent mixed with the material. That chemical blowing agent is triggered by heat and expands the material by creating a microcellular structure at the core with an integral outer skin.
Extrusion creates continuous linear part with a constant cross-section; injection molding produces three-dimensional shapes. The final shape required for a part dictates the process used, but both extrusion and injection molding have their benefits.
An additional benefit to parts manufactured using structural foam molding is part durability. As a result of the difference in process, parts built employing structural foam molding are sturdy while remaining rigid, and possess greater internal flexibility than parts built using traditional injection molding.
Here at Ferriot, we’ve been proud to be a leader in thermoplastic injection molding since the 1940s. Our clients turn to us for professional assistance with contract manufacturing, custom injection molding, painting and assembly. Structural foam molding is another capability we offer when traditional injection molding may not meet part design requirements. The structural foam process creates parts with a high strength-to-weight ratio and is often used for large parts and in metal to plastic replacement.
Crafted Plastics has served the plastics extrusion needs of manufacturers and distributors worldwide since 1982. Whether it’s a basic extruded profile or a more complex profile, our commitment is to produce custom extrusions that meet your specifications.
Timely Delivery of Injection Molded Parts From safety helmets to children’s toys, or syringe barrels to ATM’s, the universe of parts that rely on injection molding keeps growing. The injection molding process gives companies the capability to create complex shapes and to incorporate vibrant colors or intricate details into a final product, all for a […]
Creating plastic parts for commercial and medical applications requires different processes, dependent on shape and usage requirements.
Crafted Plastics has built its reputation on producing extruded plastic profiles and plastic tubing that meet the specifications and quality standards of our customers. We offer single extrusion, co-extrusion, and tri-extrusion production along with many value-added processes either in-line or off-line.
Structural foam parts generally weigh less and aren’t as dense as similar parts manufactured using other processes. The actual weight savings can vary, but parts built using structural foam molding can be 10% – 30% lighter than other parts. The integral skin contributes to added strength and the entire process creates parts with low stress.
Ferriot’s experienced engineers are here to guide you through every critical step in your injection molding journey, from concept to completion.
This website uses Google Analytics to collect anonymous information such as the number of visitors to the site, and the most popular pages.
Crafted Plastics offers in-house engineering to help with material selection and tool design. Most of our extrusion dies and tooling are made onsite by our team.
Creating a successful injection molded component requires collaboration and the expertise of a skilled team. One of the most critical aspects of the design for manufacturing (DFM) process is selecting the appropriate resin. Choosing the right injection molding resin not only meets design goals and performance specifications but also aligns with budget constraints. By working […]
GETTING A QUOTE WITH LK-MOULD IS FREE AND SIMPLE.
FIND MORE OF OUR SERVICES:
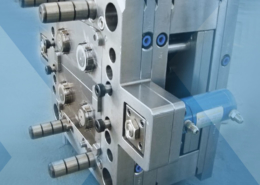
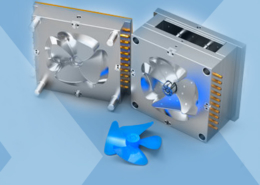
Plastic Molding

Rapid Prototyping
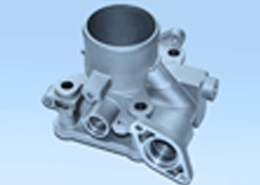
Pressure Die Casting
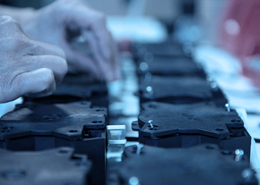
Parts Assembly
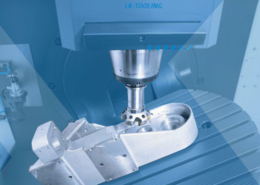