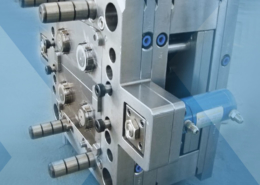
Injection Molding Contract Manufacturer I Artemis Plastics - contract injection
Author:gly Date: 2024-10-15
Using a platinum catalyst, a thermoset method called liquid silicone rubber moulding heat-cures a two-component compound in the mould to create the finished object.
Low Waste: In comparison to several other manufacturing techniques, injection moulding generates a very little amount of waste. Even if there is any leftover or trash plastic, it can be recycled and used again.
Micro molding is an advanced and highly specialized manufacturing method that can produce tiny plastic components with extreme intricate geometries. This process can manufacture parts weighing from 0.1gm to 1gm and tolerance levels of 10 to 100 microns.
Purchasing high-quality construction components, including injection moulded plastic building products and assemblies, is one of the keys to the success of architecture projects.
Most of the components used in the aircraft sector are manufactured using aerospace plastic injection moulding because of the number of advantages they provide.
Zeal 3D is an expert in injection molding and has the capacity to join fast prototyping procedures with ultimate ease. From high customization to complex design manufacturing, we do it all for you. We offer the best plastic mold manufacturing services for your every need. Search plastic injection molding companies near me and you will find Zeal to helping you about everything which you need to know about it.
In this process, engineers keep a fixed amount of rubber compound into the mold cavity and then compress it into the shape of the cavity by closing both sides of the mold. In this process, the pressure remains the same while the heat is added to cure the product. Once the process is complete, engineers remove the final product from the mold.
In rubber transfer molding, the rubber compound is placed at a specific part of a mold called a pot before being pushed against a cavity to get the desired shape. Once the curing process is done, the mold is split while relating the product.
Zeal 3D is a leading rubber and silicone injection molding company that brings in the complete range of molding across industries.
Next, the powder is molded utilising the same machine and tooling that engineers use in plastic injection molding. But in this method, the cavities are 20% larger to manage the part shrinkage during the sintering process. In the process, the machine first melts the feedstock and injects it into the mold cavity, where it cools and gets the desired shape.
Zeal 3D Services offers comprehensive services for prototyping and producing parts through a plastic injection molding process. We have advanced plastic moulding injection machines, skills, and experience to design and manufacture injection-molded plastic parts. Our plastic injection molding services are suitable for a variety of industries for designing and manufacturing high-quality plastic products for both high-volume and low-quantity parts production. We manufacture and supply durable, functional, and cost-effective plastic injection molded products defence, automotive, medical, aerospace, and consumer industries. We are among the best plastic injection molding companies that offer an amazing range of services for the Australian and overseas markets.
Grit and dry glass beads are used in D-grade finishes to provide a highly rough textured finish. Products might have a smooth or dull finish based on the type of material utilized.
While performing sintering, the MIM parts need robust support, or the parts will get distorted as they shrink during the process. Engineering can use standard flat support trays or use custom supports if required.
Even while using 3d printed injection mold for the MIM process, most of the rules are similar to the plastic injection molding. But, here are some additions that engineers need to follow:
Unlike the traditional plastic molding process, MPM parts don't require any draft. The polymer binder that is used in the powder material releases quickly from the mold.
This is a sample text. You can click on it to edit it inline or open the element options to access additional options for this element.
Michael Eiler not only keeps the ball in play with his bike, he also successfully brings exciting 1zu1 projects to the finish line. Never solo, always as part of a team!
One of the many industries that manufacture parts using the plastic injection moulding technique is defence. The injection moulding process is used in numerous applications in the defense sector for creating desired end-products.
Another benefit of leveraging this technology is that it's a very cost-effective molding process that produces robust products. With minimum warpage, the parts have superior durability.
Zeal is a leading company offering you on-demand plastic injection molding services. Regardless of your industry, Zeal offers you full-fledged plastic injection molding solutions to cater to all your manufacturing requirements.
The final step of this process includes sintering the remaining part at high temperatures (up to 1350°C) to reduce the space by around 1% to 5%, and it results in a high-density metal part. The furnace leverages inert gas to attaint's temperature of about 85% of the metal's melting point. This process helps remove pores and causes the part to shrink by 80% of its molded volume. The final part retains the original shape with higher tolerance levels.
The foam injection molding process is a low-pressure injection molding process in which the machine introduces inter gases into the melted polymer to reduce the density of the product. The structural foam molding creates products that have cellular cores surrounded by integral and rigid skin. While making the homogenous mixture of polymer and gas, engineers use foaming agents, including NI, CO2, or CBA.
Injection molding is also an important step towards a solution for your project: for prototyping and small series. The injection molded parts are produced with aluminum molds manufactured by us.
Automobile plastic injection moulding is a crucial production technique in the automotive sector, where reliability, stability, and quality are of the highest importance. It is used to produce auto parts like,
B-grade parts have a slightly rougher polish than A-grade parts due to the application of grit sandpaper. B-grade finished custom-moulded plastic components have quite a matte surface texture.
With Zeal 3D services, we can support any of your injection molding needs and provide you with the best service and products at every step of your project. This ranges from design assistance to prototype verification or full-scale production, all by the highest quality standards.
Klaus Pichler spends his free time in the saddle – he and his road bike conquer Austria’s mountains with endurance and the right pedal stroke.
Extensive Material Support: Zeal 3D offers specialized 3D engineering services that cater to the client's needs and requirements using more than 45 different materials.
Speed, precision, technological diversity - that's what 1zu1 offers its customers. For more accurate, more meaningful prototypes and for series parts in record time.
We have a wide range of materials available for injection molding. The selection of material from the wide range of different grades of these materials can be a challenging task but our team of expert engineers will help you to select the most suitable material for your application.
High Detail: Under extremely high pressure, molten plastic is injected into the mould during the procedure. This forces the plastic firmly against the moulds, enabling the creation of detailed and complex shapes with lots of detail.
Injection molding, an important manufacturing process at 1zu1. How does it work? The chosen material is liquified and injected into a mold under pressure. In this way, we as a manufacturer can produce prototypes from original material and small series up to 100,000 pieces and more.
Our Boy, Arburg, Demag and Sumitomo Demag injection-molding machines generate clamping forces ranging from 10 to 160 metric tons.
This process is ideal for producing high-volume small metal parts with complex geometric designs. Metal injection molding can efficiently create objects with thin walls. Engineers can use a variety of ferrous and non-ferrous alloys and get the desired material properties. Our metal injection molding machine offers a tolerance level of up to ± 0.005 in and Max wall thickness of 0.04 to 0.25 in.
Metal injection molding process consists of four significant production steps that turn powder from raw materials into a robust solid object. The process has the following steps:
It is an ideal method for producing tiny components with higher design precision and accuracy. This mini injection molding begins with creating smaller cavities to form the desired shape. Resin or thermoplastics are rapidly injected into the cavity to form components at a higher speed.
We are proud of being one of the top custom injection molding suppliers for manufacturers whose injection molding cost is lower than any market. Our team is skilled in producing high-precision and durable plastic injection molded parts. We work with advanced machines to handle our customers' needs for injection-molded parts from low to moderate, and large quantities in any 2D and 3D shapes. Whether you want to turn concepts into reality, enhance product design, or conduct injection molding and testing, we can provide a high degree of precision and aesthetic appearance to meet international standards.
C-grade finishes provide a rough, uneven surface using grit sanding stones. C-grade finished injection plastic components have a matte surface texture.
Australia Wide Fastest Delivery: In Australia, including Melbourne, Perth, Sydney, Brisbane, Canberra, Adelaide, Tasmania, and New Zealand, Zeal 3D offers the quickest delivery options for 3D metal printing.
Zeal 3D is among the leading metal injection molding companies that cater to all your bespoke manufacturing requirements with ease.
Cost-Effective: Numerous copies of the same products can be produced. When you require parts with tight tolerances and high levels of dependability, injection moulding is the best option.
An injection moulded part's shiny and glossy surfaces are produced by A-grade finishes, which are created by involving a buffing process.
Metal injection molding is an advanced variation of conventional plastic injection molding that allows engineers to perform fabrication of solid metal parts. In this metal molding process, the raw material called feedstock is the powder of metal and polymer.
By using this form you agree with the storage and handling of your data by this website. And agreed to get promotional emails.
Zeal 3D's engineering department uses state-of-the-art CAM programming equipment to send tool path instructions to our machines that will produce your desired part accurately. The quality is tested using automatic testers that ensure dimensional specifications are maintained right on target without any change.
“At 1zu1, rapid prototyping means being really fast, even faster, the fastest to find solutions that work. But we take our time on the consulting side.”
Zeal 3D Services excels in plastic injection moulding, offering high-quality, cost-effective parts for industries like defence, automotive, medical, and aerospace. With advanced machines and expert skills, we provide comprehensive services, including free design assistance and instant online quotes. Trust Zeal 3D for all your injection moulding needs.
The rubber molding machine creates molded rubber parts by hard pressing a rubber's block into a molding metal cavity. When the rubber is exposed to heat, it activates a chemical reaction, and there are several variations in this process to achieve the desired quality. The most popular variation methods are compression molding, transfer molding, and injection molding.
The foam injection molding machine then injected the material through the nozzle into the mold in a lower volume than the amount required to mold an object. Injection expansion and pressure of the polymer and gas then fills the mold. A porous surface is formed when the melt comes in contact with the cold surface of the mold. Then the foam injection molding expanding polymer mixture forms the cellular core.
There is a wide range of rubber molding materials available in the market to accomplish different tasks. Some of the popular ones are:
Accuracy of final injection molded products depends upon the various factors like material, tooling, the geometry of the product, and surface finishes. The possible tolerance of most thermoplastic is ±0.2 to 0.5mm.in few specialized applications tolerances are low as ±5 µm on both diameters and linear features are achieved in mass production Surface finishes of 0.0500 to 0.1000 µm or better can be obtained. Rough or pebbled surfaces are also possible.
The production of the injection molded parts is carried out exclusively with the aluminum molds manufactured by us. These are manufactured using high-quality, reliable processes that meet the highest demands for precision of plastic parts, shape, material and surface structures. When the injection-molding machine is in a vertical position, we can insert a wide variety of parts into the mold and overmold them. This means we can overmold cables. Make plug parts with insert pins. Injection-mold multi-component parts.
The foam molding process is an ideal process for producing high-strength, lightweight parts. Many large-sized objects require thick walls than conventional injection molding, making the production more accessible. The structural foam brings a quick turnaround while working with thicker parts.
The first step of metal injection molding is to form a powder mixture of metal and polymer, and the metal used in this process is much more refined (under 20 microns). The powdered metal is mixed with a heated thermoplastic binder, cooled, and then pulverised into a feedstock in pellets. The end feedstock consists of 60% of metal and 40% polymer.
If you are launching a new automobile and need custom product designs, we have the best custom injection molding expertise and services. Our industrial plastic parts designs are also utilized by building and construction, food packaging, and medical industries. Whenever think about Injection Molding services, think of the largest plastic injection molding company in the world i.e Zeal 3D.
Michael Eiler not only keeps the ball in play with his bike, he also successfully brings exciting 1zu1 projects to the finish line. Never solo, always as part of a team!
Several industries including, medical, automotive, and electronics manufacturing, require small injection molding processes to create minuscule parts. Following are some of the sectors using micro molding:
You may be wondering why you keep encountering a falcon at 1zu1 and what prototyping and production have to do with the agile bird of prey. It's simple: the falcon perfectly represents our company with its special abilities.
Efficient High Production: The cost per part for large volume production runs is quite cheap. By employing plastic moulds rather than metal ones, you may save costs even for medium volumes, or between 10,000 and 25,000 pieces.
Manufacture At Any Scale: Zeal 3D works with manufacturers to create tools and equipment in any quantity, from 1 to 10,000 pieces, enabling high or low-volume manufacturing at the most competitive pricing.
Two-part injection moulding techniques called overmolding and insert moulding combine one material with a secondary substrate part or metallic insert to produce a single component. Our overmolding process shortens assembly time and increases the strength and flexibility of your parts by covering plastic, metal, and rubber over one another via chemical bonding.
This process offers several advantages to manufacturers. To begin with, it is a highly versatile process for manufacturing all kinds of plastic parts. It is ideal for producing items that range in size from fractions of millimetres up to several metres in length and creating them with amazing intricacy and detail.
High-end Service Provider: Zeal 3D, a provider of 3D engineering and modern digital manufacturing services, is dedicated to constantly providing products and customized services that satisfy customers' expectations and adhere to regulatory requirements.
Did you know that the peregrine falcon can accelerate to over 300 km/h in a dive? That its eye has a high temporal resolution? And that it has mastered the technique of shaking flight, which allows it to remain in one place in the air?
Armin Huber enjoys roaring through the Alps on his motorcycle. Just like at 1zu1, it’s a hobby in which speed and technology must come together.
In this process, manufacturers utilize a standard injection molding machine, and the powder is melted before injecting into the mold. The powder cools down and solidifies into the desired shape during this process. After this, the heating process removes the unnecessary polymer to produce high-density metal objects.
In this step, the machine removes the polymer binder from the metal, and in many cases, engineers use solvent debinding to dissolve most of the binder. Once this step is complete, engineers perform the thermal debinding process. In this process, the molds are heated at a low temperature, and it helps in removing the polymer binder through evaporation.
Plastic injection molding is a faster and low-cost manufacturing process for quality and functional plastic products for a variety of uses across all industries. Our designers are experts in creating 3D CAD models with complex features and using laser-based rapid prototyping methods. We recommend all our clients to get injection molding to test fitting and functionality before going for production. Easy testing, assembling, and manufacturing are various advantages of rapid prototyping.
Needs Less Post-Production: Since the parts typically have good aesthetic post-production, you will typically need very little post-production. You can create an injection moulding tool with a unique finish that will be immediately visible on the finished product.
No MOQ Needed: Without needing a minimum order quantity, our staff will make the required effort to locate the supplies if you need manufacturing services utilizing materials that are not on the material list.
High-Quality Assurance: In order to reach the highest level of customer satisfaction, Zeal 3D makes a significant effort to ensure quality assurance and continuously delivers high-quality goods with strict tolerances.
At 1zu1, we help you find the perfect solution by combining the best technology with a wide range of materials. And this is implemented in the shortest possible time and with the highest technical precision.
We are there for you Monday - Friday from 8:00 a.m. to 5:00 p.m. and help to bring your products faster to the market. Exceptions during the year are the Austrian holidays. We are also fully available in the summer – we do not take a company vacation.
We have more than 1,000 different plastic materials that we keep in stock. If your plastic component requires a different or special material, you are welcome to provide this material yourself instead of requesting us to procure it. And without any problems whatsoever.
By using this form you agree with the storage and handling of your data by this website. And agreed to get promotional emails.
Rubber molding is a molding process that manufactures usable rubber items produced from uncured elastomers or rubber. Elastomer is any rubber molding materials that have good resilience for returning to the original shape when applied.
By using this form you agree with the storage and handling of your data by this website. And agreed to get promotional emails.
Injection molding is a robust manufacturing process used to make an enormous variety of products. It is a large-scale production method that is cost-effective for mid-volume production runs. In addition, it gives the manufacturer the ability to create complex items with fine detail accurately and efficiently. It is why injection molding has become so popular recently, as manufacturers are increasingly looking towards innovative processes to stay competitive in today's global market.
Being a leading provider of injection molding service, we offer a wide range of manufacturing services to OEMs. From gears to brackets, enclosures, knobs, pulleys, automobile parts, toy parts, robot parts, etc., we make thousands of molded plastic parts. We also offer an online injection molding service for which you just need to load your 2D or 3D CAD file on our website for an instant free quote. We provide free design assistance for our clients who needs alteration in the design of their product for Injection Molding.
Industries use several rubber molding solutions to accomplish respective structure and properties in the final product. There are majorly three types of rubber molding that are:
Zeal 3d is a leading micro injection molding company that caters to all industrial requirements with higher accuracy and shorter turnaround time.
Zeal Injection Molding Services and plastic molding manufacturing services additionally offer its clients an extensive variety of auxiliary administration alternatives that incorporate machining, powder covering, silk screening, painting, and ultrasonic welding. Zeal Injection Molding Services utilizes the most recent machines to deliver high-quality plastic products.
The production of the injection molded parts is carried out exclusively with the aluminum molds manufactured by us. These are manufactured using high-quality, reliable processes that meet the highest demands for precision of plastic parts, shape, material and surface structures.
Be it automotive, construction, computing, electrical, and electronics, Zeal offers clients a wide variety of molding processes to produce the best quality plastic products. We have a proven track record of supplying high-quality parts that meet each client's distinct requirements in terms of design, dimensions, and surface finish.
Sichern Sie sich einen Wissensvorsprung! Mit dem 1zu1 Newsletter erhalten Sie spannende Neuigkeiten, Informationen zu Messen und Veranstaltungen, zum Produktprogramm und zu besonderen Angeboten.
Typically, the mould's surface preparation is finished throughout the manufacturing process. After the injection moulding is accomplished, we will give the end product-specific surface treatments in accordance with your specifications. Some of the high-end surface finishes are,
Exciting news will fly to you with the 1zu1 newsletter. For more success with your plastic products. Secure your knowledge advantage now!
In this process, the rubber is heated to a liquid stage before injecting it into the mold. The final product is obtained by opening the mod and then closing it to get the following injection process for producing molding rubber.
Our quality standards cover two aspects: technology and processes. Only by combining these two aspects can we ensure reliable and efficient quality management.
When the injection-molding machine is in a vertical position, we can insert a wide variety of parts into the mold and overmold them.
The wall thickness should be minimal, and it should be uniform throughout the part production. Minimising the wall thickness helps in reducing material volume and sintering times.
Several industries including automotive, aerospace, and medical use robust metal parts manufactured using the metal injection molding process. Below are some of the commonly used metals used in MIM parts:
In the manufacturing process known as plastic injection moulding, plastic in a barrel is heated until it melts, at which point it is shot into a mould to create a finished thermoplastic item suitable for production. We are experts at designing and producing a variety of plastic injection moulds tailored to specific tolerance and budget with our expertise and cutting-edge equipment.
GETTING A QUOTE WITH LK-MOULD IS FREE AND SIMPLE.
FIND MORE OF OUR SERVICES:
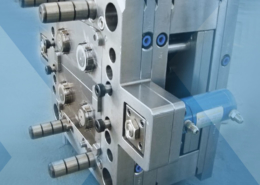
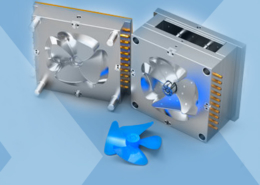
Plastic Molding

Rapid Prototyping
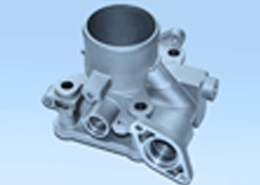
Pressure Die Casting
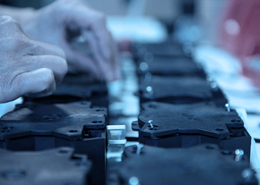
Parts Assembly
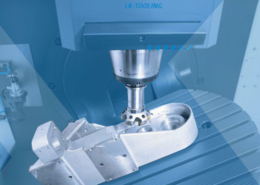