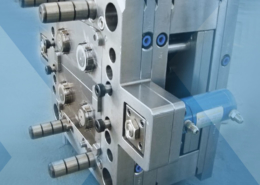
Injection Molding Company in Greater Noida/Unveiling ... - injection molding com
Author:gly Date: 2024-10-15
Molds are manufactured with our premier injection molding partners in China for the absolute best precision and pricing and then shipped to our Fictiv Mexico operation for nearshore production and fast, reliable, economical shipping.
Quick turnaround for steel tools with best part pricing for prototype to mid-level bridge production.
Fictiv does not charge any inventory fees for holding your molds, as long as you order off of the mold within 2 years. After 2 years of inactivity, Fictiv will ship/destroy the mold at the customer's direction.
Standards often require manufacturers to maintain proper records and traceability throughout the manufacturing process. This involves documenting details such as materials used, manufacturing procedures, inspections conducted, and testing outcomes. Comprehensive documentation is essential as it facilitates actions like product recalls, investigations, and quality audits if necessary.
Common applications: Because it is so robust, it is well suited for applications in the medical, nuclear, chemical processing, and aerospace industries.
Acrylonitrile Styrene Acrylate (ASA) is a thermoplastic polymer that serves as an excellent alternative to ABS, particularly in outdoor applications. ASA has superior weather resistance and can withstand prolonged exposure to UV radiation and extreme temperatures without degrading or losing its mechanical properties. Its exceptional durability makes it an ideal material for automotive parts, construction materials, and outdoor signage. Additionally, ASA is easily processed through injection molding, extrusion, and other manufacturing techniques, making it a versatile option for various industries.
Quick turnaround for aluminum or steel molds to provide fastest delivery at a competitive price for prototype tolow-volume production.
Styrene Acrylonitrile (SAN) resin is a popular alternative to Polystyrene due to its superior thermal and chemical resistance. SAN is made by combining styrene and acrylonitrile monomers through a process known as copolymerization. The resulting material has excellent mechanical properties, such as high rigidity, strength, and toughness. Additionally, SAN resin can withstand higher temperatures compared to polystyrene, making it ideal for applications that require resistance to heat and chemicals like automotive parts, medical equipment, and household appliances.
Polybutylene Terephthalate (PBT) is a type of polyester, similar to PET plastic. It is highly resistant to heat and chemicals, making it an ideal choice for applications that demand such properties. Due to its low molding and use temperatures, PBT is better suited for applications where the temperature range is not too high. It also exhibits excellent dimensional stability, good electrical insulation properties, and high impact resistance. These characteristics make it a popular choice in the automotive, electronics, and consumer goods industries. PBT is often used in the manufacturing of electrical connectors, switches, circuit breakers, automotive parts like bumpers and grilles, and household appliances like dishwasher parts.
Plastic injection molding simplifies the process of creating prototypes, allowing medical professionals and manufacturers to swiftly refine their designs. This speeds up the development cycle, resulting in quicker market entry for new medical devices and equipment.
International standards, like ISO 13485 (Medical Devices – Quality Management Systems), hold global recognition. Adhering to these standards allows medical device manufacturers to expand their market reach since numerous countries require compliance with internationally recognized benchmarks for importing and distributing products.
Polyethylene is a versatile material that boasts several desirable properties such as low melting point, high ductility, high impact strength, and low friction. Due to its low melting point, it can be easily molded into various shapes and sizes. Its high ductility means it can withstand deformation without losing its structural integrity. Moreover, its high impact strength makes it ideal for use in products that are subject to mechanical stress or potential damage. Its low friction property also makes it an excellent choice for applications where sliding or rubbing is involved, such as in bearings and gears. Overall, these properties make polyethylene a popular material in many industries, including packaging, construction, automotive, and medical devices.
Polycarbonate (PC): Polycarbonate, a durable and transparent thermoplastic material, finds widespread application in the medical industry. Its remarkable impact resistance and optical clarity make it ideal for medical device housings, connectors, and containers.
Common applications: Head/tail lights, light pipes, clear enclosures
Liquid Silicone Rubber (LSR): LSR is a biocompatible and flexible material that is extensively used in injection molding for various medical parts. It is particularly suited for applications that need soft-touch properties like gaskets, seals, and medical implants.
Polyethylene terephthalate, commonly referred to as PET, is a widely used plastic material in the production of water and other beverage containers. It also has applications in the textile industry as it is used to produce synthetic fibers. PET is lightweight, strong, and durable, making it an ideal choice for packaging products that require protection from external factors such as moisture and air. Additionally, PET is recyclable, making it an eco-friendly option for manufacturers looking to reduce their environmental impact. However, it is important to note that improper disposal of PET bottles can have detrimental effects on the environment and wildlife. Therefore, proper recycling or disposal methods should be implemented to ensure responsible use of this material.
Polyvinyl Chloride (PVC) is a synthetic polymer that possesses exceptional properties such as high hardness, excellent mechanical strength, and electrical insulation. Its ability to resist chemicals makes it suitable for use in various industries such as construction, healthcare, and automotive. Additionally, PVC's resistance to liquids, including oils and acids, further enhances its versatility. Due to these properties, PVC is widely used in manufacturing pipes, wire insulation, flooring materials, roofing membranes, and medical devices.
Polyphthalamide (PPA) is a high-performance thermoplastic material that shares similarities with nylon. However, PPA offers superior stiffness, strength, and thermal properties compared to nylon. It also boasts excellent creep resistance and dimensional stability, making it an ideal choice for applications that require long-term performance under high-stress conditions. Its ability to withstand extreme temperatures and harsh chemical environments makes it a popular choice in the automotive, aerospace, and electronics industries. Additionally, PPA has low moisture absorption rates, which helps maintain its mechanical properties even in humid conditions.
Standards in plastic injection molding establish the specifications and requirements that medical devices must meet to ensure patient safety. Complying with these standards minimizes the risk of defects, malfunctions, and adverse events, guaranteeing that medical devices perform as intended and do not endanger patients.
Fictiv now provides automated DFM feedback for injection molding during the initial quoting process. Log In now to give it a try! With automated DFM feedback for your injection molding project you’ll now receive immediate feedback on
Plastic injection molding for medical parts requires materials that adhere to strict regulatory and safety standards, while also possessing the required properties for specific medical applications. Here are several commonly employed materials in plastic injection molding for medical components:
APQP full program planning, PPAP, Scientific Molding, Tooling inspection, and Automation. Access to ISO 9001:2015 quality certification and manufacturing partners certified to AS9100 Rev D, ISO 13485:2016, and IATF 16949:2016
Glass-filled PEEK is a reinforced version of standard PEEK that offers greater stiffness and tensile strength. The glass fibers added to the polymer matrix enhance its mechanical properties, making it an excellent material for high-performance applications in industries such as aerospace, automotive, and medical devices. Glass-filled PEEK also has excellent chemical resistance, thermal stability, and wear resistance, making it a popular choice for demanding engineering applications.
Liquid Silicone Rubber (LSR) Molding: Liquid Silicone Rubber (LSR) molding is a commonly used manufacturing technique for producing medical products that require biocompatibility, flexibility, and heat resistance. It involves injecting liquid silicone into a mold cavity and curing it to create a solid, elastic component. Some examples of medical applications using LSR molding include the production of medical-grade seals, gaskets, and silicone catheters.
Acrylic is a highly versatile and transparent polymer that exhibits excellent tensile and flexural strength. It is also known for its cost-effectiveness, making it an attractive alternative to polycarbonate. Acrylic boasts several other advantages, including its optical clarity, scratch resistance, and weatherability. Additionally, it can be easily molded into various shapes and sizes, making it a popular material in many industries such as automotive, construction, and consumer goods. Its low weight and durability make it an ideal choice for applications where safety is paramount, such as aircraft windows or protective shields.
Polycarbonate is a versatile material that boasts exceptional strength and durability. It is commonly used in the manufacturing of various products, including eyeglasses, safety helmets, and electronic components. Despite being incredibly strong, polycarbonate can also be transparent, making it an ideal choice for applications where clarity is essential. Its transparency combined with its toughness makes it a popular choice for outdoor signage and protective barriers. Additionally, polycarbonate is known for its ability to withstand high temperatures, making it an excellent material for use in harsh environments.
ABS or Acrylonitrile Butadiene Styrene is a thermoplastic polymer that is produced using emulsion. It is an incredibly versatile material, known for its excellent resistance to corrosive chemicals, making it useful in various applications such as automotive parts, toys, and electronic housings. ABS is also easy to machine and has a relatively low melting temperature, which means it can be molded and shaped with ease. Its high impact resistance makes it ideal for use in products that may undergo significant stress or force. Due to its unique properties, ABS is widely used in many industries worldwide.
Due to the delicate nature of medical devices, the medical industry uses various intricate injection molding techniques alongside conventional ones. These include micro injection molding, two-shot injection molding, Liquid Silicone Rubber injection molding and reaction injection molding.
“Regardless of what facet of the project we were working on (prototyping, tooling, finishing) I had the confidence in Fictiv’s expertise and knew I was in good hands.”
Fictiv does not conduct mold flow analysis as a standard DFM analysis for injection molding, however, it can be done as an additional service upon request.
Fictiv can mold any commercially available thermoplastic. Please reach out with your specific resin needs.
Plastic injection molding supports a wide range of medical-grade plastics, each with unique properties suitable for various medical applications. These materials offer tailored solutions to cater to different medical needs, ranging from biocompatible options for implants to transparent plastics used in medical packaging and durable polymers utilized in surgical tools. The versatility of the materials enables healthcare professionals to address specific requirements effectively.
The production time for a custom-made medical device using plastic injection molding can vary based on the complexity and volume. Typically, it ranges from a few weeks to a few months.
Standards play a vital role in providing clear guidelines and fostering innovation. By establishing frameworks for new technologies and materials, they create opportunities for manufacturers to push the boundaries of medical device development while still adhering to the set standards.
"Fictiv was a crucial partner in that they were able to get the mold up and running within three to four weeks, whereas our other partners were taking six, eight weeks just to get first-off tool parts."
Thermoplastic polyurethane (TPU) is a versatile material that possesses elastic properties and can withstand exposure to oil, grease, and abrasion. TPU is commonly used in the manufacturing of products such as phone cases, footwear, and automotive parts due to its durability and flexibility. Additionally, TPU is resistant to chemicals and UV radiation, making it an ideal material for outdoor applications. Its ability to be molded into different shapes also makes it a popular choice for 3D printing.
Common applications: Enclosures, large panels; widely used in many applications
Nylon 6/6 Nylon 6/6 has high mechanical strength and rigidity. It is resistant to chemicals and is stable at high temperatures. Price: $ Common applications: Automotive applications, gears, bushings Glass-Filled Nylon Glass-Filled Nylon is much stiffer and has greater tensile strength than standard Nylon. It also has a low coefficient of friction and high thermal resistance. Price: $$ Common applications: Bearings, washers, a lightweight substitute for metals where appropriate
Access a wide breadth of capabilities through our highly vetted network.
Common applications: Automotive applications, household appliances, sealing applications
Silicone is a versatile material that is known for its flexibility and low toxicity. It also boasts low thermal and chemical conductivity, making it an ideal choice for a wide range of applications. Silicone products are commonly used in the medical industry due to their biocompatibility and ability to withstand high temperatures. They are also used in the construction, automotive, and electronics industries for their durability and resistance to harsh environments. With its unique properties, silicone has become an essential material in modern manufacturing.
Common applications: Electronic components, automotive applications, aerospace, glasses/safety eyewear.
Low-density polyethylene (LDPE) is a versatile plastic that exhibits several desirable properties. It is known for its softness, flexibility, toughness, and lightweight. LDPE also boasts excellent corrosion resistance, making it an ideal material for a wide range of applications. This plastic is commonly used in the production of packaging materials, disposable bags, and tubing systems. Its unique combination of properties makes it a popular choice across various industries such as food and beverage, healthcare, and agriculture. Additionally, LDPE is recyclable which adds to its appeal as an eco-friendly material.
To ensure regulatory compliance, you must adhere to applicable standards like ISO 13485. This involves rigorous testing and documentation of the manufacturing process. Additionally, seeking necessary approvals from health authorities such as the FDA is essential for entering the global market.
Common applications: Medical components, battery cases, everyday uses
Polyphenylsulfone (PPSU) is a high-performance polymer with unique properties that make it suitable for a variety of applications. It exhibits exceptional heat and chemical resistance, making it ideal for use in harsh environments. One of the most remarkable features of PPSU is that it has no melting point, which means it can withstand high temperatures without degrading or losing its structural integrity. Due to its excellent mechanical strength and dimensional stability, PPSU is widely used in the aerospace, medical, and electronics industries. Additionally, its transparency and ability to withstand sterilization make it an ideal choice for medical equipment and devices.
Standards serve as essential guidelines for the manufacturing process, materials used, and quality control procedures of medical devices. Adhering to these standards ensures consistent and dependable production, maintaining a high level of product quality. The importance of consistency becomes paramount in mass production scenarios, where it guarantees that every device performs reliably and consistently.
Absolutely. As long as you are able to supply project requirements and part specifications, Fictiv is happy to provide a no-obligation quotation.
The medical industry’s integration of plastic mold injection technology has produced numerous advantages that surpass conventional manufacturing methods. This innovative technique facilitates rapid prototyping, reducing the time required for product development and enhancing the efficiency of the design process. This means that medical professionals can promptly refine and optimize their product designs, ultimately leading to safer and more effective medical solutions.
Common applications: Medical, nuclear, chemical processing, and aerospace industries.
Injection molding could absolutely be used for prototyping, but it depends on the project requirements. Typically, for projects that require less than 10 prototypes, injection molding may not be the most cost-effective option. We are happy to meet with you to discuss your needs and help determine if injection molding is the correct process for you.
Plastic mold injection has revolutionized various industries, including the medical sector. This innovative technology has transformed the production of medical devices and equipment, bringing about significant benefits that have reshaped healthcare practices.
TPE, or thermoplastic elastomer, is a material that possesses the appearance and texture of rubber but has thermoplastic properties, meaning that it can be melted and re-molded. TPE also boasts excellent thermal properties and can maintain stability across a wide temperature range. It is commonly used in various industries such as automotive, medical, and consumer goods for its versatility and durability. Additionally, TPE is often preferred over traditional rubber materials due to its ease of processing, recyclability, and cost-effectiveness. Fictiv can also source custom materials upon request, including thermoset materials for applications that require a more rigid and heat-resistant material.
Now on the Fictiv Platform, powered by ChatGPT and Fictiv’s manufacturing database, get help navigating the complex landscape of plastic and metal parts.
Thermoplastic Elastomers (TPE): TPEs, or thermoplastic elastomers, are a versatile family of materials that possess the combined properties of rubber and plastic. These unique materials find extensive usage in various medical applications where flexibility is crucial. They are commonly employed for creating grips, seals, and medical tubing.
Injection molding often produces fully formed parts without needing additional assembly or secondary operations. This streamlined manufacturing process minimizes the risk of contamination and human error during assembly, making it more efficient and reliable.
After completing prototyping, your tooling can be used to make thousands more parts! We'll validate your tooling and provide bridge production for your designs.
Polyethylene Terephthalate (PET): PET is a durable and see-through thermoplastic material that has widespread use in the field of medical packaging. It is commonly used for creating blister packs and medication bottles.
Plastic injection molding has several benefits. However, it is important to note some limitations, including design complexity, high initial tooling costs, and material selection challenges for specific medical applications.
At Fictiv, we know how critical information security is, especially when working with high-value design IP. That's why we designed our platform with elite-level security and confidentiality as a top priority. From log in to file upload to part fulfillment, you can rest easy knowing that your IP is safe within our secure Digital Manufacturing Ecosystem. Read More about it here.
Once the materials and molds are prepared and in place, the injection molding process allows for the production of several hundreds of molded parts per day.
Injection molding is a tricky process, and one that we want to work through with our customers. This means that while we offer draft, thickness, and sink analysis on-platform for every quotation, we often provide advanced DFM in the forms of parting line visualization, side action analysis, and mold-flow analysis upon request.
Yes. Plastic injection molded parts find widespread usage in surgical procedures. They are essential components of surgical instruments, implantable devices, and various medical equipment.
By signing up, you agree to our Terms of Use and Privacy Policy. We may use the info you submit to contact you and use data from third parties to personalize your experience.
Common applications: Synthetic fibers, electrical susulation, membranes, packaging
In the medical industry, seamless collaboration between different devices and components is crucial. Standards play a vital role in ensuring that medical devices are designed and manufactured with compatibility and interoperability in mind. This approach simplifies the integration of these devices into existing systems and workflows for healthcare professionals.
Common applications: Automotive applications, Fire-retardant applications
We exist to eliminate bottlenecks in new product development by integrating the people, processes, and platform you need to source custom parts.
Polyethylene (PE): Polyethylene, a commonly used thermoplastic material in the medical industry, offers excellent biocompatibility, flexibility, and chemical resistance. It finds extensive applications in medical tubing, bags, and containers.
Our trained employees ensure your parts will be delivered on time and to spec.
Plastic mold injection is a precise and efficient process used to manufacture complex medical components and devices. It involves injecting molten plastic into a pre-designed mold. This technique enables the creation of intricate and customized products that meet the specific requirements of medical applications. From simple syringes to sophisticated surgical instruments and implantable devices, plastic mold injection plays a crucial role in producing high-quality medical equipment.
Glass-filled Polycarbonate is a highly durable and sturdy material that finds extensive use in various industrial applications. It is known for its excellent impact resistance, making it ideal for manufacturing products that require high strength and toughness. Additionally, this material has excellent dimensional stability, which means it can maintain its shape even under extreme temperatures or humid conditions. The glass fibers added to the polycarbonate matrix enhance its mechanical properties such as stiffness, tensile strength, and creep resistance. These characteristics make glass-filled polycarbonate an ideal choice for manufacturing industrial components like gears, bearings, pump impellers, and electrical insulators.
Common applications: Medical containers, constuction, piping, cables
Create high quality custom mechanicals with precision and accuracy.
Many plastics used in medical-grade injection molding are designed to be compatible with the human body, ensuring safety. Additionally, these materials can withstand various sterilization processes without compromising their properties. This guarantees that medical devices remain hygienic and safe for patient use.
The injection molding process ensures an exceptional level of consistency in the final products. Each molded part exhibits near-perfect similarity, thereby minimizing variations and mitigating the risk of defects. This unwavering consistency proves to be crucial, particularly in medical applications where precision and utmost quality play a pivotal role in ensuring patient safety and reliable performance.
Common applications: Medical devices, food grade applications, O-rings, seals
Finding a manufacturing partner offering a full-suite of capabilities and expertise to take her design from prototype to full production.
We exist to eliminate bottlenecks in new product development by integrating the people, processes, and platform you need to source custom parts.
Accelerate development with instant quotes, expert DFM, and automated production updates.
Polypropylene (PP): Polypropylene is a thermoplastic material known for its versatility. It offers excellent chemical resistance and boasts a low density. This makes it highly suitable for various medical applications including syringes, test tubes, and medical packaging.
We believe in getting our customers the best possible parts the first time. Therefore, Fictiv does not charge for DFM and we ensure that you have all of the assurances you need before you place your injection molding order.
Once the initial mold is created, producing medical devices in large quantities significantly reduces the cost per part. This cost-effectiveness has numerous advantages for both healthcare providers and patients as it enhances accessibility and affordability of these devices.
Compliance with regulations and standards is crucial for medical injection molding companies seeking FDA approval or clearance for their devices. It not only enables market access but also builds trust among healthcare professionals and patients. Adhering to these guidelines allows companies to reliably produce safe and high-quality medical products, enhancing patient care and the overall healthcare sector.
A part manufactured through 3D printing is orders of magnitude more expensive than the same part manufactured through injection molding, assuming the design is a fit for injection molding. As long as you produce enough of that part to offset the mold cost, it would be worth it to pursue injection molding. Fictiv provides you with DFM on your design and options for mold architecture to give you the best cost-benefit balance. Request an injection molding quote for your 3D-printed part design to get a no-obligation quotation and DFM and assess your options at no cost to you. It is recommended that you get an expert involved early on in the design process if you intend to use injection molding for production. Many customers invest significant time in creating 3D-printed prototypes and making revisions without taking into account the specific manufacturing constraints associated with injection molding. This oversight can lead to wasted resources, both in terms of money and time. By providing Design for Manufacturability (DFM) guidance tailored to injection molding, Fictiv can help you avoid such pitfalls, resulting in significant savings in time and costs.
Common applications: Automotive, oil and gas, plumbing components
Common applications: Automotive applications, household appliances
Polypropylene is a versatile thermoplastic polymer that offers excellent resistance to both chemical and electrical factors at high temperatures. This makes it an ideal choice for applications that require material with good dimensional stability, chemical resistance, and electrical insulation properties. Additionally, polypropylene can be easily processed using various manufacturing techniques such as injection molding, blow molding, and extrusion. Its low density and low water absorption property make it suitable for use in food packaging, laboratory equipment, automotive components, and medical devices.
Standards play a crucial role in ensuring the safety of medical devices during their design and production phases. Manufacturers are obligated to carefully assess potential risks associated with their products and take proactive measures to minimize them. This diligent approach not only helps prevent any hazards but also safeguards patients from potential harm.
In the field of manufacturing, plastic mold injection stands out as an economically viable method. It proves to be cost-effective when producing medical devices in large quantities. This advantageous technique enables a seamless increase in production without compromising on quality. Consequently, it promotes greater accessibility to essential medical equipment worldwide, ultimately reducing healthcare costs and enhancing patient care on a global scale.
Common applications: Automotive, aerospace, plumbing applications
Reaction Injection Molding (RIM): Reaction injection molding involves the use of a reactive liquid mixture that undergoes polymerization and solidification inside a mold. This method, often referred to as RIM, is commonly employed for manufacturing robust and impact-resistant medical equipment and components. Examples include wheelchair parts and housing for medical devices.
Polyphenylene oxide, also known as PPO, is a thermoplastic polymer that offers excellent dimensional stability and electrical properties. Due to its high resistance to heat and chemical degradation, it finds applications in various industries like automotive, electrical and electronics, and medical devices. Its unique combination of properties makes it an ideal choice for manufacturing components that require high dimensional accuracy and stability. It also provides good electrical insulation, making it suitable for applications where electrical conductivity needs to be avoided.
Our network of high quality injection molding partners spans the globe, with production available in the US, Mexico, and China -- so you can optimize production for costs, lead time, or both as needed. And with elite Fictiv operations personnel located in each region, you can trust that you'll get high-quality parts no matter where they're produced.
We partner with you to do cost down analysis to meet your requirements. Our global network enables Fictiv to optimize for "landed costs" of the product.
PEEK, also known as Polyetheretherketone, is a high-performance polymer that boasts exceptional resistance to high temperatures, chemicals, and radiation. It is commonly used in industries such as aerospace and medical devices where extreme conditions are present. Its unique properties make it an ideal material for applications that require durability and reliability in harsh environments. Furthermore, PEEK has excellent mechanical properties such as stiffness and strength which can be further enhanced with the addition of reinforcing materials such as carbon fiber or glass fiber.
Fictiv’s IM service provides custom quality parts quickly and accurately in conformance to customer requirements. Every IM project has a dedicated global team that gives each customer visibility into the entire process and ensures projects run smoothly—from DFM to production to final delivery.
Common applications: Instrument housings, electrical components
We do! Not only are you able to access your DFM through the Fictiv platform, but you will receive 3D visualization of the DFM feedback and be able to comment on, annotate, and discuss this feedback with a Fictiv technical project lead. All of this happens before you place your order.
High-Density Polyethylene (HDPE) is a thermoplastic manufactured from petroleum and is known for its exceptional strength and durability. With high tensile strength, HDPE can withstand heavy loads with ease. It also has excellent impact resistance, making it ideal for outdoor applications that are exposed to harsh weather conditions. Additionally, HDPE has a high melting point, which enables it to withstand high temperatures without degrading. Due to these properties, HDPE is widely used in various industries, including packaging, construction, and automotive. Its robustness and versatility make it an excellent choice for products that require both strength and flexibility.
ISO standards, with ISO 13485:2016 and ISO 9001:2015 being particularly significant, govern the quality management systems for medical devices. When manufacturers comply with ISO standards, they adhere to globally recognized best practices that include risk management, traceability, and process validation.
Among the various materials in the TPE family, Thermoplastic Vulcanizates (TPV) stands out for its unique properties. TPV has a high-temperature resistance and excellent elasticity, which makes it an ideal choice for applications that require both flexibility and durability. It is also known to have good chemical and weather resistance, making it suitable for outdoor applications. TPV closely resembles EPDM rubber in terms of properties, but with the added advantage of being easily moldable using conventional thermoplastic processing techniques. Its versatility and ease of processing make it a popular choice across multiple industries, including automotive, consumer goods, and medical devices.
Of course! Fictiv will maintain your mold for 2 years after your most recent order and allow you to re-order parts for the duration of the mold life.
Acetal is a versatile thermoplastic that is known for its low-friction properties, lightweight construction, and resistance to chemicals and liquid absorption. It can be machined with ease but can also be injection molded for more complex shapes and designs. Its high strength-to-weight ratio makes it an excellent choice for applications that require durability and reliability, such as automotive components, bearings, and gears. Additionally, its ability to withstand high temperatures and resist deformation under pressure makes it an ideal material for use in industrial settings.
Common applications: Medical device applications, mobile electronic devices
Which aluminum alloy is ideal for your needs? What 3D printing material has excellent tensile strength? Try Materials.AI to find out.
Common applications: Automotive applications, gears, electrical components
PC/ABS is a blend of two materials, polycarbonate and ABS. It is a combination that combines the best features of both components, leading to improved mechanical properties such as heat resistance and flexibility. Not only does this blend offer superior performance, but it is also easier to process during injection molding than either base material alone. The PC/ABS blend has become a popular choice in various industries like automotive manufacturing, electronics, and household appliances due to its excellent balance between strength and toughness.
Thank you for submitting your information. Your submission has been received, and we will get in touch with you shortly.
Environmental concerns can arise due to the generation of plastic waste during manufacturing. To avoid this, manufacturers should adopt recycling and sustainable practices in order to minimize their environmental impact.
By signing up, you agree to our Terms of Use and Privacy Policy. We may use the info you submit to contact you and use data from third parties to personalize your experience.
Plastic injection molding provides design flexibility, enabling medical professionals and engineers to develop innovative and user-friendly medical devices. By incorporating textured surfaces, grips, and multi-component assemblies, it enhances the usability and performance of medical products.
“Fictiv enabled us to save millions of dollars in infrastructure, people and time costs when compared to traditional development and supply chain strategies.”
Two-Shot Injection Molding: Two-shot injection molding, also referred to as overmolding, combines two different materials into a single mold. This technique enables the production of medical devices with multiple colors, textures, or material properties within one manufacturing cycle. It finds common application in creating ergonomic grips for medical instruments and incorporating soft-touch components onto rigid devices.
Manufacturing Engineers, Technical Program Mgt, SQE, Tooling Engineers, Logistics Supervisors assigned to each production program.
Standards in plastic injection molding for medical devices play a crucial role in guaranteeing the safety, quality, and reliability of medical equipment used in healthcare settings. When it comes to medical applications, where patients’ lives and well-being are at stake, adhering to high standards becomes essential. Some key reasons why these standards are indispensable in the field of plastic injection molding for medical devices include:
Complying with FDA regulations and ISO standards is vital in medical injection molding. This ensures the safety, effectiveness, and quality of medical devices and components. The U.S. Food and Drug Administration (FDA) regulates medical devices under the Federal Food, Drug, and Cosmetic Act (FD&C Act). Manufacturers must adhere to the FDA’s Current Good Manufacturing Practices (CGMP) requirements. These guidelines cover various aspects including design, manufacturing, labeling, and quality control.
EPDM, also known as rubber, is a popular synthetic material used in compression molding. It has excellent chemical and heat resistance properties, making it an ideal choice for many industrial applications. Due to its outstanding durability and versatility, it is commonly used in the automotive industry for sealing components like windows and doors. Additionally, EPDM is often utilized in the construction industry for waterproofing roofs and other structures due to its ability to withstand extreme weather conditions. Its resistance to UV radiation and ozone also makes it suitable for outdoor use. As a result of its unique properties, EPDM has become a staple material in several industries, from automotive to construction.
Polyetherimide is a versatile semi-transparent plastic that exhibits excellent high-temperature resistance and boasts very high dielectric strength. These properties make it an ideal material for manufacturing medical instrument components as well as electrical insulation parts. Its unique combination of mechanical and thermal properties allows it to withstand harsh environments, making it a popular choice for various industrial applications. Moreover, its inherent flame retardancy and chemical resistance provide enhanced safety and durability, making it a go-to material for many manufacturers.
Common applications: Medical instrument components and electrical insulation parts.
Glass-filled Polybutylene Terephthalate (PBT) is an enhanced version of standard PBT that offers improved mechanical properties. With greater tensile strength and stiffness, it is better suited for applications that require durability and longevity. Additionally, PBT can withstand high temperatures and chemical exposure, making it a popular choice in the automotive and electronics industries. Its lower molding and use temperatures also make it easier to process than other materials with similar properties. Overall, Glass-filled PBT is a reliable option for applications that require high-performance thermoplastics.
Plastic injection molding offers many benefits for medical applications, making it the preferred manufacturing method for producing medical devices and equipment. Here are some of the key advantages:
By signing up, you agree to our Terms of Use and Privacy Policy. We may use the info you submit to contact you and use data from third parties to personalize your experience.
Micro Injection Molding: Micro injection molding is a process used to create highly precise and tiny medical components, often with features that are smaller than a millimeter. This technique finds its strength in manufacturing miniature medical parts like microfluidic devices and micro-needles. The production requires specialized equipment and precision tooling to attain the desired outcomes.
Medical devices must adhere to strict regulatory requirements set by health authorities, such as the United States Food and Drug Administration (FDA) or the European Medicines Agency (EMA) in the European Union. Compliance with relevant standards is vital in securing regulatory approvals, certifications, and market clearance for these devices.
The tooling lead time can vary depending on the complexity of the part. In some cases, it can be as quick as 10 days, while in a more complex design, it may extend to around 21 days (calendar days). For parts larger than 300mm, the lead time might be further extended due to the additional complexities involved in manufacturing larger components.
Plastic injection molding is a highly efficient process for producing intricate and complex medical components with exceptional precision. By using accurately designed molds, the manufacturing of medical devices can achieve tight tolerances and intricate geometries while ensuring adherence to exact specifications.
Common applications: Enclosures, large panels; Automotive parts
Polyphenylene Sulfide (PPS) is a thermoplastic material that exhibits exceptional resistance to both chemicals and heat. It also boasts good flow characteristics and dimensional stability, making it a popular choice in demanding applications. Due to its excellent properties, PPS is commonly used in the automotive, electrical and electronics, and aerospace industries. Its high performance in extreme conditions makes it an ideal choice for components that require stability and reliability.
GETTING A QUOTE WITH LK-MOULD IS FREE AND SIMPLE.
FIND MORE OF OUR SERVICES:
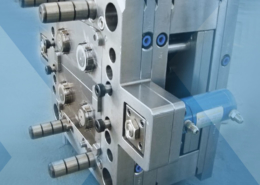
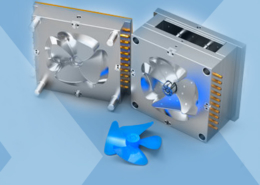
Plastic Molding

Rapid Prototyping
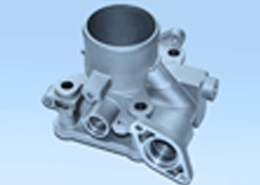
Pressure Die Casting
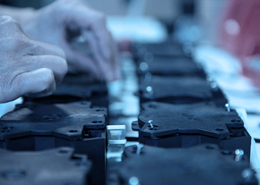
Parts Assembly
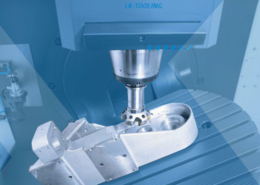