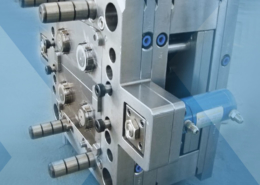
Unveiling the Versatility of PVC Injection Molding
Author:gly Date: 2024-06-08
Introduction
PVC injection molding stands as a cornerstone in the realm of plastic manufacturing, offering unparalleled versatility, durability, and cost-effectiveness. From piping systems to consumer goods, automotive components to medical devices, PVC injection molding caters to diverse industries and applications, shaping the products we use in our daily lives. This article delves into the intricacies of PVC injection molding, unraveling its significance, processes, properties, applications, and future prospects.
Significance of PVC Injection Molding
Ubiquitous Presence in Everyday Products
PVC injection molding plays a vital role in the production of a wide range of everyday products, including pipes, fittings, window profiles, bottles, toys, and packaging materials. Its versatility, affordability, and ease of processing make PVC a preferred choice for manufacturers seeking reliable and cost-effective solutions for diverse applications.
Durability and Weather Resistance
One of PVC's key attributes is its exceptional durability and weather resistance, making it suitable for both indoor and outdoor applications. PVC products exhibit resistance to corrosion, moisture, UV radiation, and chemical exposure, ensuring long-term performance and reliability in harsh environments such as construction sites, automotive interiors, and outdoor signage.
Recyclability and Sustainability
PVC's recyclability and sustainability credentials contribute to its appeal as an environmentally friendly material option for injection molding applications. With advancements in recycling technologies and growing awareness of sustainability issues, manufacturers are increasingly adopting recycled PVC resins and implementing closed-loop recycling systems to minimize waste and environmental impact.
Processes and Techniques in PVC Injection Molding
Material Preparation and Melting
PVC injection molding begins with the preparation of PVC resin pellets, which are dried and preheated to remove moisture and enhance flow properties. The resin pellets are then fed into the injection molding machine's hopper, where they are heated and melted to a homogeneous molten state suitable for injection into the mold cavity.
Injection Molding Process
The injection molding process involves injecting molten PVC resin into a pre-designed mold cavity under high pressure, where it cools and solidifies to form the desired shape of the final product. Injection molding machines with precise temperature control, pressure monitoring, and injection speed adjustment capabilities ensure consistent part quality and dimensional accuracy.
Mold Design and Cooling System
The design of the mold cavity and cooling system is critical to the success of PVC injection molding. Mold designers optimize the geometry, gating, and venting of the mold to minimize defects such as warping, sink marks, and flash. Efficient cooling systems, including water channels and cooling sprays, ensure uniform cooling and efficient cycle times.
Applications of PVC Injection Molding
Building and Construction
PVC injection molding finds extensive use in the building and construction industry for the production of pipes, fittings, profiles, and other structural components. PVC's properties such as corrosion resistance, thermal insulation, and fire retardancy make it ideal for applications ranging from plumbing and drainage systems to window frames and roofing materials.
Automotive Components
In the automotive sector, PVC injection molding is employed in the manufacturing of interior and exterior components, including dashboards, door panels, trim, and seals. PVC's low cost, lightweight, and customizable properties make it a preferred choice for automotive manufacturers seeking to reduce vehicle weight, enhance fuel efficiency, and improve aesthetic appeal.
Consumer Goods and Packaging
PVC injection molding caters to the production of a diverse range of consumer goods and packaging materials, including bottles, containers, packaging films, and household products. PVC's versatility, clarity, and barrier properties make it suitable for applications requiring packaging of food, beverages, personal care products, and household chemicals.
Challenges and Future Prospects
Environmental Concerns and Regulation
Addressing environmental concerns related to PVC manufacturing and disposal poses challenges for the industry. Future prospects may involve the development of bio-based PVC alternatives, adoption of eco-friendly additives, and implementation of circular economy initiatives to minimize PVC's environmental footprint and promote sustainable practices.
Technological Advancements and Innovation
Advancements in PVC formulation, processing technologies, and additive manufacturing techniques offer new avenues for innovation in PVC injection molding. Future prospects may include the development of PVC composites, foamed PVC materials, and 3D printing technologies tailored to specific industry needs, enabling enhanced performance, functionality, and design flexibility.
Market Expansion and Globalization
The growing demand for PVC products in emerging markets and the expansion of global supply chains present opportunities and challenges for PVC injection molding manufacturers. Future prospects may involve strategic partnerships, market diversification, and investments in research and development to capitalize on emerging trends and meet evolving customer needs on a global scale.
Conclusion
In conclusion, PVC injection molding stands as a versatile, durable, and cost-effective solution for a wide range of industrial and consumer applications. By leveraging advanced technologies, sustainable practices, and innovative materials, PVC injection molding manufacturers continue to drive progress, enable innovation, and shape the future of plastic manufacturing. Looking ahead, addressing environmental challenges, embracing technological advancements, and exploring new market opportunities will be key to unlocking the full potential of PVC injection molding and ensuring its continued relevance and impact in the years to come.
GETTING A QUOTE WITH LK-MOULD IS FREE AND SIMPLE.
FIND MORE OF OUR SERVICES:
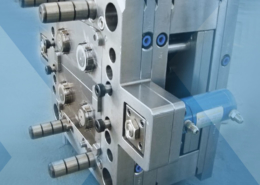
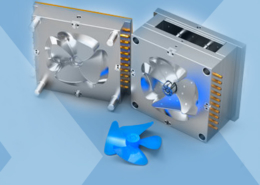
Plastic Molding

Rapid Prototyping
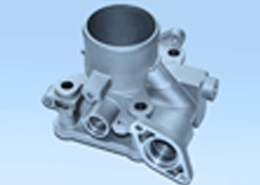
Pressure Die Casting
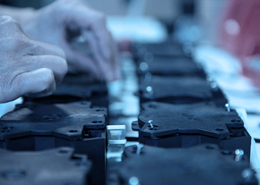
Parts Assembly
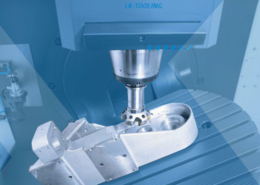