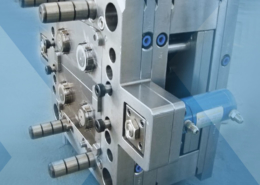
Unraveling the Innovation of PT Injection Molding
Author:gly Date: 2024-06-08
In the realm of modern manufacturing, PT injection molding emerges as a revolutionary technique, offering unparalleled precision, efficiency, and versatility. This article embarks on a journey to explore the intricacies of PT injection molding, unveiling its significance, applications, and future prospects, captivating readers with its transformative potential.
Introducing PT Injection Molding
Precision at Its Core
PT injection molding, or precision thermoplastic injection molding, represents a pinnacle of manufacturing excellence, where intricate plastic components are produced with utmost precision and accuracy. This technique involves injecting molten thermoplastic material into a meticulously designed mold cavity, resulting in the creation of complex geometries with tight tolerances.
Evolution of Technology
Over the years, advancements in machinery, materials, and process control have propelled PT injection molding to new heights. From high-speed injection molding machines equipped with advanced robotics to sophisticated mold design software, technology continues to redefine the boundaries of what is achievable in plastic manufacturing.
Meeting Industry Demands
In an era characterized by rapid technological advancements and evolving consumer preferences, PT injection molding emerges as a solution to meet the ever-growing demands of various industries. Whether it's automotive components, medical devices, or consumer electronics, PT injection molding offers the flexibility and precision required to produce high-quality plastic parts that meet stringent performance criteria.
Applications Across Diverse Industries
Automotive Sector
In the automotive industry, PT injection molding plays a critical role in the production of interior and exterior components, such as dashboards, door panels, and bumpers. The ability to produce lightweight yet durable plastic parts with intricate designs and superior surface finishes makes PT injection molding indispensable for automotive manufacturers striving for excellence.
Medical Devices and Healthcare
Precision is paramount in the production of medical devices and equipment, where even the slightest deviation can have significant implications for patient safety and treatment efficacy. PT injection molding enables the fabrication of sterile and high-precision components, ranging from syringes and surgical instruments to implantable devices, ensuring compliance with rigorous regulatory standards and industry requirements.
Consumer Electronics
The consumer electronics sector relies heavily on PT injection molding for the production of casings, enclosures, and connectors for smartphones, laptops, and other electronic devices. The ability to achieve precise dimensions, intricate details, and aesthetic appeal is essential for meeting consumer expectations in this competitive market segment.
Driving Innovation and Quality Excellence
Material Advancements
Advancements in material science have expanded the range of thermoplastic materials suitable for PT injection molding. From traditional polymers to engineered resins and bio-based plastics, manufacturers now have access to a diverse array of materials with enhanced properties, such as strength, durability, and chemical resistance, enabling them to meet the evolving needs of various industries.
Quality Assurance and Process Optimization
Ensuring product consistency and reliability is paramount in PT injection molding. Advanced quality assurance techniques, such as real-time monitoring of process parameters, automated inspection systems, and statistical process control, enable manufacturers to identify and rectify potential defects before they impact production output, ensuring that every part meets the highest quality standards.
Customization and Personalization
The versatility of PT injection molding allows for the customization and personalization of plastic components to meet specific customer requirements. Whether it's color matching, texture replication, or geometric complexity, manufacturers can tailor their products to suit diverse applications and market preferences, offering a competitive edge in today's dynamic business landscape.
Conclusion: Pioneering the Future of Manufacturing
In conclusion, PT injection molding stands as a testament to the ingenuity and innovation driving modern manufacturing. Its ability to produce intricate plastic components with unparalleled precision, efficiency, and quality has revolutionized industries across the globe. As technology continues to evolve and new materials emerge, the potential of PT injection molding remains limitless. By embracing sustainability practices, fostering innovation, and investing in research and development, manufacturers can unlock new opportunities and propel the industry towards a brighter, more sustainable future.
GETTING A QUOTE WITH LK-MOULD IS FREE AND SIMPLE.
FIND MORE OF OUR SERVICES:
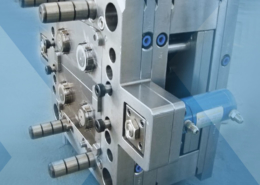
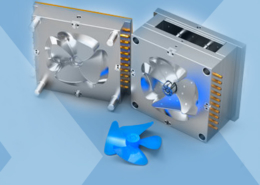
Plastic Molding

Rapid Prototyping
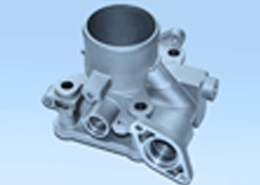
Pressure Die Casting
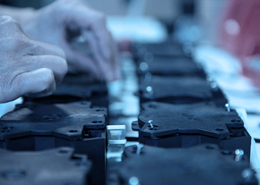
Parts Assembly
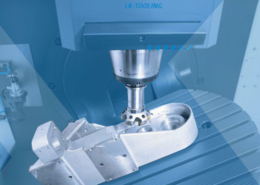