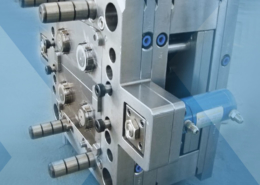
Injection Molding - pp injection molding
Author:gly Date: 2024-10-15
Efficiency: High-speed production allows for thousands of identical parts to be produced in a single day. Complex Shapes: Advanced mold designs enable intricate and complex geometries that are challenging to achieve through other manufacturing processes. Material Versatility: A wide range of thermoplastic materials can be used, making it suitable for various industries. Cost-Effectiveness: While initial mold-making can be expensive, the per-unit cost decreases significantly as production volume increases, making it economical for large runs.
Quality should be a top priority. A reliable plastic injection molding service provider will adhere to strict quality control processes, conducting thorough inspections to ensure every part meets standards.
Bespoke Solutions: Custom molding allows for the development of parts engineered for specific uses or environments, ensuring optimal performance. Material Selection: Manufacturers can choose from a myriad of plastics and composites tailored to the application, enhancing product performance. Increased Competitive Edge: Customized solutions can differentiate products in the marketplace, giving businesses an edge over competitors.
The medical industry demands high standards in terms of design and compliance. Plastic injection molding can produce critical components such as syringes, surgical instruments, and medical housing that meet stringent regulatory requirements.
The most successful parts are created when there is constant communication between a part designer, tool designer and manufacturer.
Consistent quality parts start with a quality, well-made and maintained mold. What expectations should you have for the care of your investment?
A skilled mold manufacturer should be able to offer innovative mold design services, ensuring that the mold facilitates efficient and accurate production. This includes considerations for cooling channels, ejection mechanisms, and design for manufacturability (DFM).
In electronics, the assembly of complex circuitry requires precision components that can be seamlessly integrated with other parts. Injection molding provides the reliability and consistency needed for these applications.
Plastic injection molding service is an invaluable asset in modern manufacturing. Whether you are a startup looking to develop a new product or an established company seeking to improve manufacturing efficiencies, understanding the landscape of plastic injection molding, including the significance of injection molding companies and plastic injection mold manufacturers, is essential. Selecting the right partners is crucial to achieving your production goals, ensuring quality, and maintaining your competitive edge.
Regular injection mold maintenance can help your mold last longer, run with less interruptions & will ultimately save you time, money & frustration.
Plastic injection mold companies play a critical role in the process, designing and manufacturing the molds used in injection molding. The quality and design of these molds directly impact the finished product. Key factors to consider include:
Design is one of the most important factors in avoiding part defects. Avoid mistakes that can be costly both in regard to time and budget later on.
From toys to kitchen utensils, plastic injection molding allows for mass production of consumer goods that are both cost-effective and tailored to consumer preferences.
Plastic injection molding is a cornerstone of modern manufacturing, playing a pivotal role in producing everything from household items to intricate components for the automotive and aerospace industries. As businesses seek efficient and cost-effective production methods, understanding the nuances of plastic injection molding services is more crucial than ever. This article will delve into what plastic injection molding is, the key players in the industry, and the importance of choosing the right injection molding companies for your needs.
Having a general understanding of how to calculate press size is a good first step in determining what injection molding partners are available to you. Strong partners will make recommendations on how to appropriately tweak your part to ensure the final design fits your manufacturing needs and reduces upfront tooling costs. Nicolet Plastics has press sizes up to 610 tons.
Melting: Plastic pellets are fed into a heated barrel where they melt and form a viscous material. Injection: The melted plastic is injected into a closed mold at high pressure. Cooling: The molten plastic cools and solidifies, taking the form of the mold. Ejection: Once cooled, the mold opens, and the finished part is ejected.
Strong communication is vital throughout your project. Consider working with injection molding companies that demonstrate excellent customer service and are willing to guide you through every phase of the production process.
Different projects require different types of plastic. A reputable supplier will offer a variety of materials to meet your needs, whether you're producing automotive parts or consumer goods.
Pressure plays a significant role in the overall quality of a plastic part. Pressure keeps the mold closed during the injection process. Too much or too little pressure can cause various issues such as flashing and viscosity. One important consideration in regard to pressure is that plastic compounds react differently from one another based on their Melt Flow Index (MFI). MFI measures the ease of flow of a thermoplastic polymer and the higher the MFI, the higher pressure needed to create a successful part.
By working with reputable plastic injection molding service providers and leveraging custom injection molding capabilities, businesses can bring innovative and reliable products to market efficiently. If you’re considering leveraging plastic injection molding for your next project, take the time to research and choose the best injection molding companies and mold manufacturers that align with your needs. By doing so, you’ll position your business for success in an ever-evolving marketplace.
Are you a product designer or engineer that is looking for more information on how to make your plastic part design more efficient in regard to cost and production time? One important consideration during the part design process is to have a good understanding of plastic injection press basics including the size of machine needed for your part.
Designing a plastic part for manufacturability from the outset involves several considerations that can have a significant impact on key variables
The lifespan of a mold can affect the overall production costs. Companies that prioritize high-quality materials and craftsmanship in their molds can provide more durable options, reducing downtime and costs over time.
When determining press size for your plastic part, it’s important to calculate the total projected shut-off area. This area consists of only the space that is 90 degrees to the direction of the injection molding machine platens. Thickness does not have any implication on the clamp tonnage and the general rule is to have 2 to 5 ton of clamp tonnage per square inch of projected area.
Additionally, smaller presses have tie bar spacing too narrow to accommodate larger products. If the mold doesn’t fit between them horizontally or vertically, you must move up in press size. Many injection molders offer press sizes ranging from 68 tons up to 400 tons.
Custom injection molding services are vital when standard solutions do not meet specific project requirements. These services enable businesses to create unique parts tailored to their applications.
In automotive applications, precision and durability are pivotal. Injection molded parts can be found in dashboard components, bumpers, and numerous internal parts, ensuring that they withstand harsh conditions and provide longevity.
Look for companies with extensive experience in custom injection molding. Expertise in your specific industry can be a significant advantage and ensure that the parts produced meet your stringent specifications.
Plastic injection molding is a manufacturing process wherein molten plastic is injected into a pre-designed mold to create a specific shape or part. This technique allows for the rapid production of plastic parts in large quantities, making it highly sought after in various industries. The process generally involves the following steps:
“Bigger the better” is not always the case when determining the press size needed. In the molding process, plastic is injected into the mold at an exceptionally high-pressure rate, which creates a natural pull to force the mold open. A press is designed to keep the mold shut with larger parts requiring more tonnage and force, and smaller parts requiring less. A general calculation for determining press size needed is as follows:
Many plastic injection mold companies offer rapid prototyping services, which allow clients to test designs before committing to large-scale production. This can save time and reduce the risk of costly mistakes.
Your plastic injection molder should help you determine the size of the machine needed to help you achieve the best result for your product. Knowing an approximate size of what will be needed can help you determine the best injection molding partner based on the press capacity they have available. For example, larger presses cannot accommodate smaller molds because they can’t close far enough and the injection process will not work.
Modern injection molding requires advanced machinery and technology. Companies equipped with state-of-the-art machines and capabilities for complex part designs ensure better accuracy and efficiency in production.
Calculating shot volume to make sure your barrel has enough capacity can be accomplished by working with your injection molder to run a mold flow analysis. On some engineered materials, the increased residence of the material in the barrel can cause the material to degrade, resulting in poor part quality. Mold flow analysis will help you determine the volume of your part and runner while determining any factors that would cause safety issues.
In order to streamline your process, consider these questions before requesting an accurate quote for your part design, development and production.
“Safety factor” is an additional percentage added to your calculation as a buffer to help reduce defects in your part. Most injection molders will recommend 2.5 times the surface square inches of the part and an additional 10% as a safety factor. If you have a part that is 120 square inches, you would need a press size with 300 tons of pressure. When you add the 10% safety factor, the required press size would have 330 tons of clamping force.
When seeking plastic injection molding services, it's crucial to work with reputable injection molding companies. Here’s what to consider when evaluating potential partners:
If you have any need for plastic injection tooling and molding, you are most welcome to contact us via Joyce Wang, info@gbmmould.com;
Injection molding parts are used across numerous sectors, underscoring the versatility of this manufacturing technique. Here’s a brief look at some of these industries:
GETTING A QUOTE WITH LK-MOULD IS FREE AND SIMPLE.
FIND MORE OF OUR SERVICES:
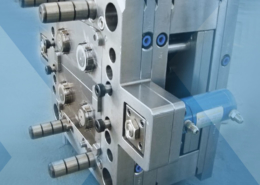
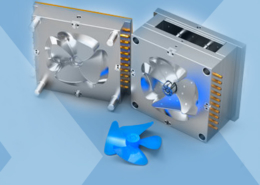
Plastic Molding

Rapid Prototyping
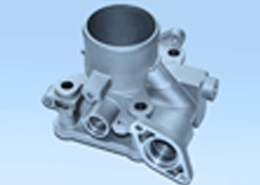
Pressure Die Casting
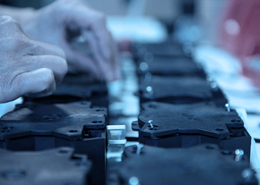
Parts Assembly
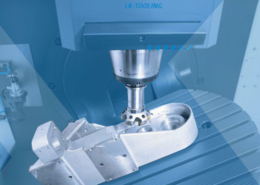