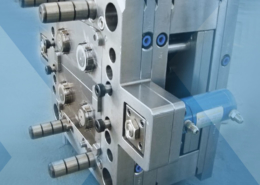
Injection Molded and Machined PEEK Components - peek injection molding
Author:gly Date: 2024-10-15
3ERP has a fantastic mold design team. They managed to finish the mold design within 10 days and started to fabricate the molds right after that. I was surprised that more than 60 items, including some big parts, were completed to a decent standard within two months. Our customers eventually received the moldings to run their testing. 3ERP saved our business!
Aluminum evenly dissipates heat, which provides dimensional stability in tooling. This significantly reduces deformation and produces less waste during the production process. It is important to note that aluminum is not as strong as steel, so it has a shorter life cycle and is less useful in high-volume processes.
Though it features multiple benefits, steel is a more expensive tooling material than aluminum and requires more turnaround time to produce molds and prototypes.
Can you imagine attempting to make prototype tools for over 30 components in just two months? Our customer desperately needed 200-300 sets of tail lights for testing, but mass production tools wouldn’t have been ready for eight months. They needed a solution to get good quality moldings by their deadline and at a much lower cost than production tools.
Although we had to invest more for the mold, we now save 70% compared with urethane casting, and we can use UV-resistant ABS to keep the color stable. Overall, I am very happy with the solution.
An ideal choice for prototyping, aluminum mold tooling provides a cost-effective way to produce molded parts. Since they are easy to cut, aluminum molds can reduce tooling costs by 15–25% compared to other mold materials and reduce cycle times by up to 40%. This translates to a faster turnaround for our customers.
Two months ago, I was super stressed by an urgent plastic molding project. Our customer desperately wanted 100 sets at very short notice in order to run testing with real materials, even though normal production would have taken more than six months. None of our preferred moldmaking suppliers could help us, given the deadline. Luckily, one of my friends recommended 3ERP to us by chance.
For this tail light project, we needed to fabricate a housing, reflector, light guide, bezel, an outer lens, and other components in a short period of time. The overall assembly size was about 600 x 400 x 150 mm, which is relatively large and the customer wanted to test real materials. In this case, 3D printing, CNC machining, and vacuum casting were not suitable, so prototype molding was the only option. Click to view this case
The rapid tooling process involves the creation of a mold using aluminum or soft steel, a stocked mold base, and hand-load inserts. Rapid tooling is one of the best methods for fulfilling small batch orders meant for use in marketing samples, product evaluations, and process design.
Traditional tooling is often prohibitively expensive for small projects. Our custom rapid tooling service is a cost-effective, low-volume alternative in situations where large volumes of the part won’t be needed in the future. The rapid production tooling process is commonly used in industrial settings for prototyping solutions or for diagnosing design issues, providing an easy introduction to mold making.
We have been indulged in manufacturing and supplying a wide range of Plastic Ampoule Tray. This tray is ideal for packaging medical products such as vial and injections. It can easily store five vial bottles of one ml, while it is designed using quality plastic material which is procured from market vendors. This tray is crafted using innovative machines under the supervision of deft professionals. It is also available in different sizes as well as finishes to meet clients' demand. Plastic Ampoule Tray is best known in market due to its anti-leakage as well as tamper proof frame.
Every quarter, we order approximately 20 sets of plastic enclosures for our device from 3ERP. The enclosures were initially made by urethane casting, but Ronan came back to me with the idea of using an aluminum mold, which allowed me to get a few hundred moldings. We decided to move to this process. The T1 samples weren’t good enough, as we got some shrink marks, but this was quickly sorted out when we received the T2 samples.
Steel is a sturdy, solid, high-quality tooling material, though it is not suitable for all applications. Steel molds have a longer life cycle than aluminum and are therefore ideal for high-volume production. Steel can also be used to produce molds from engineering-grade plastics that are resistant to abrasion and corrosion.
At 3ERP, we typically create rapid molds by CNC machining and EDM, though we also sometimes use additive methods such as 3D printing technologies.
GETTING A QUOTE WITH LK-MOULD IS FREE AND SIMPLE.
FIND MORE OF OUR SERVICES:
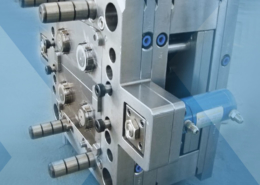
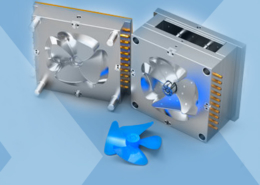
Plastic Molding

Rapid Prototyping
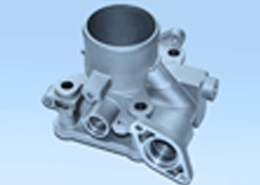
Pressure Die Casting
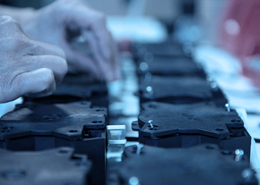
Parts Assembly
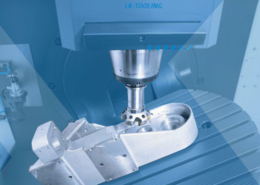