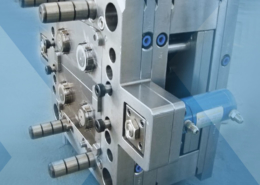
Husky Technologies | Injection Molding Packaging Solutions - molding company
Author:gly Date: 2024-10-15
Ripley Dynamics' injection molding services are defined by our commitment to precision, customization, and innovation. Our expertise in plastic injection molding, combined with our state-of-the-art facilities and dedication to client satisfaction, makes us a preferred partner for businesses seeking top-quality injection molding solutions. Whether you're looking for a reliable injection molding supplier or need assistance with a complex project, Ripley Dynamics is here to help.
This blog series is for inventors and new businesses looking at creating a new product using the process of plastics injection molding. It’s aimed at anyone with limited experience in launching a new injection molded product.
As a custom molder Accurate offers a wealth of experience in metal to plastic conversions as well as reengineering parts to eliminate gluing and other secondary operations. Accurate is experienced with over molding and the use of blowing agents for thicker walled parts. We would be happy to speak with you about the specifics of your project.
In addition to material selection, our injection molding customization capabilities include a range of finishing options. From textured surfaces to high-gloss finishes, we can achieve the exact look and feel that our clients desire. This attention to detail is what makes our personalized molding solutions stand out.
Innovation is at the core of Ripley Dynamics' injection molding services. Our injection molding techniques are continually refined to incorporate the latest advancements in the field. This commitment to innovation allows us to offer cutting-edge solutions that address the evolving needs of the injection molding industry.
Our plastic injection moulding services encompass the entire process, from design to production. We work closely with clients to understand their specific requirements, ensuring that every aspect of the project aligns with their objectives. The journey begins with design consultation, where our team of experts collaborates with clients to refine their product concepts. This stage is critical in custom injection moulding, as it sets the foundation for the entire process.
In summary, with a new product you will likely spend a few weeks and a few thousand dollars on design to start, a few thousand to tens of thousands for a mold that will take a month or more to build, then finally a few thousand dollars and a couple weeks for your first production run. Accurate recommend starting a new project at least one quarter before you plan to begin production.
The injection molding technology allows us to handle complex designs with ease. Our advanced machines are capable of producing intricate shapes and fine details, making them ideal for projects that require a high level of precision. This capability is a significant advantage in the competitive world of injection molding manufacturers.
Parts production and secondary operations will be quoted in conjunction with your mold quote. Upon approval of sample parts from your mold, the molder will be able to fulfill your orders. The pricing of parts include: mold setup and take down, materials, labor, and machine hours. For example: Mold setup and take down might be $300, materials may be $.50/part, labor might be $20/hr, and machine hours might be $50/hr. If your part has a cycle time of 30 seconds and is a 2 cavity mold then you make 2 parts each 30 seconds. Thus over 10 hours you make 2400 parts. The cost per part for an operator assisted production run would be: $300 for setup + $200 for 10hrs of labor + $500 for 10 machine hours + $1200 for materials which is a total of $2200 or a per part price of $0.917. If your order was for 600 parts your per part price would rise as the setup fee would remain the same thus your per part price goes to $1.00 for a production time of 2.5 hours.
At Ripley Dynamics, we understand that every project is unique, and our custom injection molding solutions reflect this belief. Our tailored injection molding approach allows us to adapt our services to fit the specific requirements of each client, whether it's a small batch of specialized components or large-scale production runs. This flexibility is a hallmark of our molding company services, setting us apart from other plastic molding firms.
Our team works closely with clients to identify cost-saving opportunities without compromising on quality. This could involve optimizing the design for more efficient production, selecting cost-effective materials that meet the project's requirements, or advising on the most economical production volumes. Additionally, Ripley Dynamics invests in advanced technology and efficient processes to minimize waste and reduce production time, further optimizing costs.
Businesses seeking to make informed decisions about their manufacturing processes need to understand the complexities of plastic injection molding cost. At Ripley Dynamics, we recognize that cost is a significant factor for our clients, and we strive to provide transparent and comprehensive insights into how these costs are structured. The cost of plastic injection molding is influenced by various factors, including the complexity of the design, the type of material used, the quantity of parts produced, and the level of customization required. For instance, intricate designs that require specialized molds or unique materials may increase the overall cost. Similarly, the economies of scale play a significant role – higher quantities often reduce the cost per unit, making large production runs more cost-effective.
The process of creating a new product can be a very time consuming and costly process. Here we will cover 3 basic aspects of launching a new product addressing an anticipated timeline and budget for each:
Accurate has an in-house tool shop and can quote your mold for tooling both in-house or made in China. Tooling quotes usually take 5 business days due to the complexity of quoting a new mold. We quote all large molds (for machines larger than 300 tons) using our Chinese supplier. All other molds are quoted in-house unless requested. Lead time on a mold varies greatly according to the current workload in the shop and the complexity of the mold. In general lead times are 4-12 weeks and include the 1-2 weeks it will take to sample your mold. Shop hours for mold makers are in the $80/hr - $125/hr range. Molds can take 30-80 hours to build, or longer.
In Part 3, join us to learn more about how to make your parts and mold cost less, and how to ensure you have enough cash flow to start you project.
With a 3D part design in hand along with a proof of concept prototype you are ready to quote a mold. The mold designer will need your 3D design files and will take those and may need to make some small adaptations to the part that will reap benefits when molded. The mold designer will need approval for these changes and you can verify the impact on your parts with your industrial designer before approving the changes requested.
Ripley Dynamics stands at the forefront of the plastic injection moulding industry, offering state-of-the-art injection moulding in Sydney, Brisbane and the Gold Coast that caters to a diverse range of client needs. Our expertise in plastic injection moulding stems from a deep understanding of the plastic moulding process, combined with advanced injection moulding techniques. This blend of knowledge and technology positions us as one of the leading injection moulding companies, specializing in custom injection moulding solutions that meet and exceed client expectations.
In addition to our technological prowess, our expertise in the injection molding process itself sets us apart. Our team has extensive experience in various molding techniques, enabling us to tackle challenges that others might find daunting. Whether it's dealing with difficult-to-mold materials or achieving tight tolerances, we have the skills and knowledge to deliver exceptional results.
One area where our innovation shines is in the efficiency of our injection molding production. By optimizing our processes, we can achieve faster turnaround times without sacrificing quality. This efficiency is particularly beneficial for clients looking into injection molding outsourcing, as it ensures that their projects are completed within the desired timeframe.
Prototyping generally takes two forms: 3D printing or short-run injection mold prototyping. Accurate can both 3D print and create short-run tooling. 3D printing is a great medium for prototyping runs of 1-10 parts generally. For prototyping runs of 50-100 or more parts, short-run injection molding tends to be more cost effective. 3D prints can have a turnaround time as little as 1-2 business days. Short-run molds tend to have a lead time of 2-3 weeks minimum. The advantages of a short-run injection mold are that it can be used for initial production and as well will offer much larger quantities of parts at a lower rate than 3D printing.
Industrial Design rates run from approx. $85/hr to $125/hr. Most designers need at least 2 weeks to turn around a design with the number of hours required varying greatly according to the project and the number of revisions after an initial design. Expect that your designer will need a few business days to quote your design work and to pay at least a 50% deposit to get started. The balance will be due before you will obtain your design files. Please note that you should obtain transferable files upon payment in full. These are files with your design that can be revised by another designer if necessary and of which you have full rights to the design.
In summary ensure you have a few thousand dollars set aside for design and prototyping. In addition expect a timeline minimum of 2-3 weeks plus revisions.
Terms usually include 50% due at the time of placing an order, 25% on mold completion, and 25% due upon approval of sample parts.
The initial phase of creating a 3D design will mean employing an Industrial Designer who can turn your idea into a 3D rendering that can be passed along to a toolmaker for mold design. At this time you may also look to take advantage of 3D printing technology to get a proof of concept.
Our commitment to customization extends to our support services as well. We offer comprehensive assistance throughout the project lifecycle, from initial consultation to post-production support. Our goal is to ensure that every aspect of our injection molding services aligns with the client's vision, providing a seamless and satisfying experience.
The next step involves the creation of moulds, which are the heart of injection moulding. Our precision plastic moulding techniques ensure that these moulds are crafted with the highest accuracy, reflecting the intricacies of the design. This precision is vital in custom plastic moulding, where even the slightest deviation can impact the functionality and aesthetics of the final product.
Once the moulds are ready, we move to the production phase. Our injection moulding machines, equipped with cutting-edge technology, precisely control every parameter of the moulding process. This level of control is essential for maintaining consistency and quality across all units produced. Our rigorous quality assurance protocols further ensure that each product meets our high standards, as well as those of our clients.
Custom injection molding requires a deep understanding of both the material and the process. Our team of experts selects the most suitable materials for each project, considering factors like strength, flexibility, durability, and aesthetic appeal. This material selection process is crucial in achieving the desired outcome, especially in precision plastic molding where the material's properties directly impact the performance of the final product.
Accurate can also offer some basic assembly and finishing services. As a custom molder we can do assembly, decorating, inserting, drilling, and other services. These services would be quoted on a per part basis upon request, usually at the same time as quoting the production of parts.
GETTING A QUOTE WITH LK-MOULD IS FREE AND SIMPLE.
FIND MORE OF OUR SERVICES:
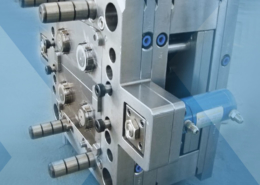
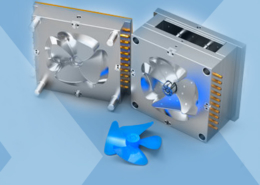
Plastic Molding

Rapid Prototyping
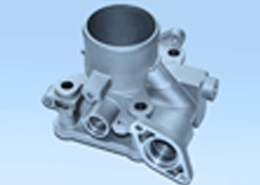
Pressure Die Casting
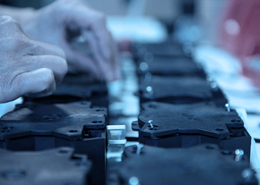
Parts Assembly
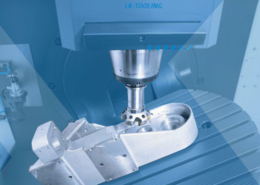