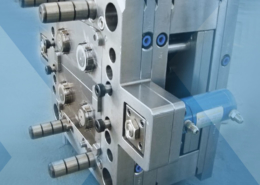
Exploring PPE Injection Molding: Revolutionizing Safety Equipment Production
Author:gly Date: 2024-06-08
Personal Protective Equipment (PPE) injection molding stands at the forefront of modern manufacturing, revolutionizing the production of essential safety equipment. With a combination of cutting-edge technology and innovative design, PPE injection molding ensures the creation of durable, reliable, and customizable protective gear. This article delves into the intricacies of PPE injection molding, exploring its process, applications, benefits, and future prospects.
Understanding PPE Injection Molding
PPE injection molding involves the manufacturing process of producing protective equipment, such as goggles, face shields, helmets, and respirators, through injecting molten material into a mold cavity. This method allows for the mass production of intricate and customized designs, catering to various industry needs.
Process Overview
The process begins with the selection of suitable materials, typically thermoplastics like polyethylene, polycarbonate, or polypropylene, known for their durability and flexibility. The chosen material is then heated to its melting point and injected into a mold cavity under high pressure. After cooling and solidification, the mold opens, releasing the finished product.
Material Selection
The choice of material is crucial in PPE injection molding, as it determines the strength, flexibility, and chemical resistance of the final product. Manufacturers often conduct thorough material testing to ensure compliance with safety standards and regulations.
Tooling and Mold Design
The design of molds plays a significant role in PPE injection molding, influencing product quality, efficiency, and production costs. Advanced CAD software enables precise mold design, incorporating features like cooling channels, ejector systems, and gating mechanisms to optimize the molding process.
Applications of PPE Injection Molding
PPE injection molding finds widespread applications across various industries, including healthcare, construction, manufacturing, and aerospace. From safety goggles and face masks to protective helmets and respiratory equipment, PPE injection molding caters to diverse safety needs, ensuring worker protection in hazardous environments.
Healthcare Sector
In the healthcare sector, PPE injection molding plays a critical role in producing essential protective equipment for medical professionals, including gloves, face shields, and surgical masks. The customizable nature of injection molding allows for the adaptation of PPE designs to meet evolving healthcare requirements.
Industrial Safety
In industrial settings, PPE injection molding addresses the need for robust and reliable safety gear to protect workers from occupational hazards. Equipment such as safety goggles, ear defenders, and respiratory masks undergo rigorous testing to withstand high-impact forces, extreme temperatures, and chemical exposure.
Benefits of PPE Injection Molding
The adoption of PPE injection molding offers numerous benefits, ranging from cost-effectiveness and efficiency to product customization and quality control.
Cost-Effectiveness
PPE injection molding enables the mass production of safety equipment at a lower cost per unit compared to traditional manufacturing methods. The high-speed production capabilities and minimal material wastage contribute to overall cost savings for manufacturers.
Customization
One of the key advantages of PPE injection molding is its ability to create customized protective gear tailored to specific user requirements. Manufacturers can easily modify designs, colors, and sizes to accommodate diverse preferences and applications.
Future Perspectives
Looking ahead, the future of PPE injection molding appears promising, with ongoing advancements in materials, technology, and design capabilities. Emerging trends such as 3D printing integration, smart PPE development, and sustainable materials usage are poised to reshape the landscape of safety equipment manufacturing.
Integration of 3D Printing
The integration of 3D printing technology into PPE injection molding processes holds the potential for enhanced design flexibility, reduced lead times, and improved product performance. By combining the strengths of both manufacturing methods, manufacturers can achieve greater efficiency and innovation in PPE production.
Smart PPE Development
The development of smart PPE incorporating sensors, IoT connectivity, and data analytics presents new opportunities for enhancing workplace safety and monitoring. These innovative solutions offer real-time insights into environmental conditions, wearer health status, and equipment performance, fostering a proactive approach to risk mitigation.
Conclusion
In conclusion, PPE injection molding represents a cornerstone of modern safety equipment production, offering unparalleled efficiency, customization, and quality. From healthcare facilities to industrial sites, the widespread adoption of injection molding technology continues to drive innovation and ensure the protection of workers worldwide. As we embrace emerging trends and technologies, the future of PPE injection molding holds immense potential for shaping a safer and more resilient workforce.
Through a comprehensive exploration of its process, applications, benefits, and future prospects, this article aims to underscore the significance of PPE injection molding in safeguarding lives and promoting occupational health and safety. By leveraging the capabilities of this transformative manufacturing method, we can address evolving safety challenges and pave the way for a safer, more secure future.
GETTING A QUOTE WITH LK-MOULD IS FREE AND SIMPLE.
FIND MORE OF OUR SERVICES:
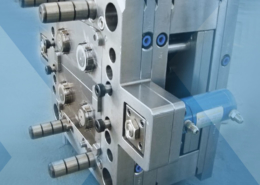
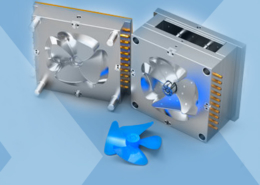
Plastic Molding

Rapid Prototyping
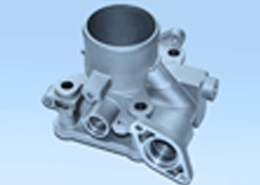
Pressure Die Casting
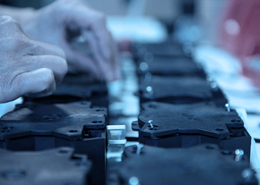
Parts Assembly
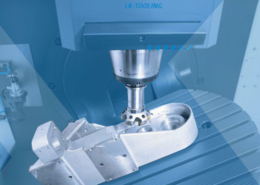