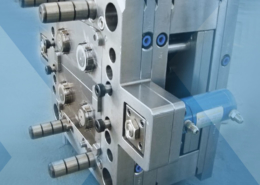
Exploring the World of POM Injection: Precision and Performance
Author:gly Date: 2024-06-08
POM injection molding, also known as polyoxymethylene injection molding, stands as a cornerstone in the realm of plastic manufacturing, offering unparalleled precision, durability, and performance. This article delves into the fascinating world of POM injection, unraveling its significance, applications, advantages, and future prospects.
Introduction: Captivating Curiosity
In the ever-evolving landscape of plastic manufacturing, POM injection molding captivates engineers, designers, and manufacturers with its remarkable properties and diverse applications. From automotive components to consumer electronics, POM injection plays a vital role in shaping modern products with its exceptional mechanical strength, chemical resistance, and dimensional stability. As industries seek innovative solutions to meet evolving demands, POM injection emerges as a versatile and reliable manufacturing process that combines precision engineering with cost-effectiveness.
Properties and Characteristics of POM
Mechanical Strength
POM, commonly referred to as acetal or polyacetal, boasts outstanding mechanical strength, making it an ideal material for applications requiring high load-bearing capacity and impact resistance. Its inherent stiffness and toughness enable the production of durable components capable of withstanding rigorous use in demanding environments.
Chemical Resistance
POM exhibits excellent resistance to a wide range of chemicals, including fuels, oils, solvents, and cleaning agents. This chemical inertness ensures long-term performance and reliability in applications exposed to harsh operating conditions, such as automotive fuel systems, industrial machinery, and medical devices.
Dimensional Stability
One of the key advantages of POM injection molding is its superior dimensional stability, which allows for the production of precise and intricate components with tight tolerances. This stability minimizes the risk of deformation or warping during manufacturing processes and ensures consistent product quality and performance.
Applications Across Industries
Automotive Industry
In the automotive sector, POM injection molding is widely used for manufacturing various components, including gears, bearings, bushings, and interior trim parts. Its low friction coefficient, wear resistance, and thermal stability make it suitable for critical applications where reliability and durability are paramount.
Consumer Electronics
In consumer electronics, POM injection molding finds applications in the production of casings, connectors, switches, and mechanical components. Its excellent electrical insulation properties, coupled with its ability to withstand high temperatures and moisture, make it an ideal material for electronic devices requiring reliability and longevity.
Healthcare and Medical Devices
In the healthcare industry, POM injection molding is utilized for producing medical devices, surgical instruments, and drug delivery systems. Its biocompatibility, sterilizability, and resistance to bodily fluids make it suitable for use in critical healthcare applications where safety and performance are essential.
Advantages of POM Injection Molding
High Precision and Complexity
POM injection molding offers unparalleled precision and complexity, allowing for the production of intricate parts with consistent quality and dimensional accuracy. Its ability to replicate complex geometries and fine features ensures optimal functionality and aesthetics in finished products.
Cost Efficiency and Scalability
POM injection molding is a cost-effective manufacturing process that enables high-volume production of parts with minimal material waste and labor costs. Its scalability and efficiency make it suitable for mass production of components across various industries, thereby reducing overall production costs and time-to-market.
Design Flexibility and Versatility
One of the key advantages of POM injection molding is its design flexibility and versatility, which allow for the customization of parts to meet specific application requirements. From geometric shapes to surface finishes, designers have the freedom to optimize product designs for performance, aesthetics, and functionality.
Future Directions and Innovations
As technology continues to advance, the future of POM injection molding holds exciting possibilities for innovation and optimization. From the development of bio-based polymers and sustainable manufacturing practices to the integration of additive manufacturing and digital twin technologies, the industry is poised to unlock new capabilities and efficiencies that will shape the next generation of plastic products. By embracing these trends and investing in research and development, manufacturers can stay ahead of the curve and meet the evolving needs of a dynamic market landscape.
Conclusion: Embracing Precision and Performance
In conclusion, POM injection molding represents a pinnacle of precision and performance in plastic manufacturing, offering a versatile, reliable, and cost-effective solution for a wide range of applications across industries. With its exceptional mechanical properties, chemical resistance, and dimensional stability, POM injection enables the production of high-quality components that meet the stringent requirements of modern engineering and design. As industries continue to innovate and evolve, POM injection molding will remain at the forefront of technological advancement, driving progress and shaping the future of manufacturing in the global marketplace.
GETTING A QUOTE WITH LK-MOULD IS FREE AND SIMPLE.
FIND MORE OF OUR SERVICES:
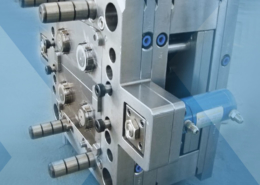
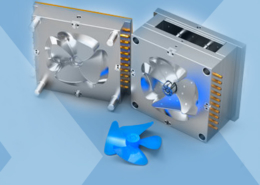
Plastic Molding

Rapid Prototyping
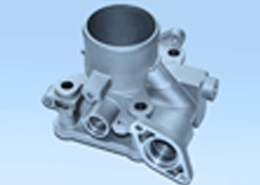
Pressure Die Casting
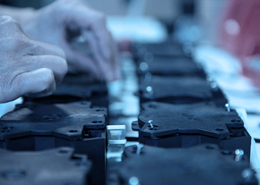
Parts Assembly
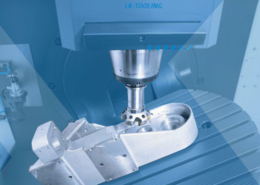