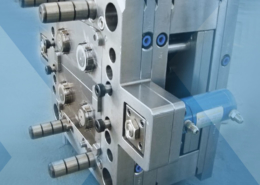
Exploring the World of Polyethylene Molding
Author:gly Date: 2024-06-08
Polyethylene molding stands at the forefront of modern manufacturing, offering versatile solutions for creating a wide array of products. This article delves into the intricacies of polyethylene molding, providing readers with insights into its applications, advantages, challenges, and future prospects.
Polyethylene, a thermoplastic polymer, has garnered immense popularity in the manufacturing industry due to its excellent properties such as flexibility, durability, chemical resistance, and ease of processing. Polyethylene molding encompasses various techniques including injection molding, blow molding, and rotational molding, each offering unique advantages depending on the desired end product.
Understanding Polyethylene Molding
Polyethylene molding refers to the process of shaping polyethylene resin into desired forms using heat and pressure. Injection molding, one of the most common techniques, involves injecting molten polyethylene into a mold cavity under high pressure, followed by cooling and solidification. This method is ideal for producing intricate and high-volume parts with consistent quality and precision.
Types of Polyethylene
Polyethylene exists in various forms, including high-density polyethylene (HDPE), low-density polyethylene (LDPE), and linear low-density polyethylene (LLDPE), each with distinct properties and applications. HDPE, known for its strength and stiffness, is often used in applications requiring structural integrity such as pipes, containers, and automotive components. LDPE, on the other hand, offers flexibility and impact resistance, making it suitable for film packaging, squeeze bottles, and toys. LLDPE combines the advantages of both HDPE and LDPE, offering improved flexibility and puncture resistance, commonly used in flexible packaging and agricultural films.
Applications of Polyethylene Molding
Polyethylene molding finds widespread applications across various industries including packaging, automotive, construction, and healthcare. Its versatility, cost-effectiveness, and durability make it an ideal choice for manufacturing a diverse range of products.
Packaging Industry
In the packaging industry, polyethylene molding plays a crucial role in the production of bottles, containers, bags, and films. Its excellent barrier properties, lightweight nature, and ability to be recycled make it a preferred choice for packaging food, beverages, pharmaceuticals, and household products.
Automotive Sector
Polyethylene molding finds extensive use in the automotive sector for producing interior and exterior components such as bumpers, dashboards, door panels, and fuel tanks. Its lightweight nature, impact resistance, and corrosion resistance contribute to fuel efficiency, vehicle safety, and aesthetic appeal.
Challenges and Future Perspectives
Despite its numerous advantages, polyethylene molding faces challenges such as environmental concerns regarding plastic waste and the need for sustainable solutions. Future research and development efforts focus on enhancing recyclability, reducing energy consumption, and exploring bio-based alternatives to conventional polyethylene.
In conclusion, polyethylene molding represents a cornerstone of modern manufacturing, offering limitless possibilities for creating innovative products across various industries. By understanding its applications, advantages, challenges, and future prospects, manufacturers can harness the full potential of polyethylene molding to drive efficiency, sustainability, and innovation in the global marketplace.
GETTING A QUOTE WITH LK-MOULD IS FREE AND SIMPLE.
FIND MORE OF OUR SERVICES:
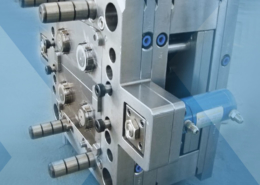
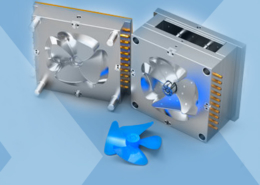
Plastic Molding

Rapid Prototyping
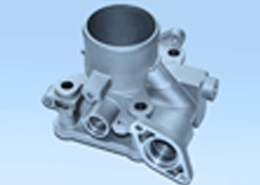
Pressure Die Casting
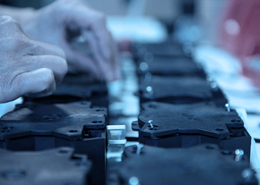
Parts Assembly
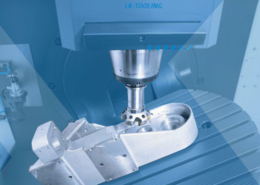