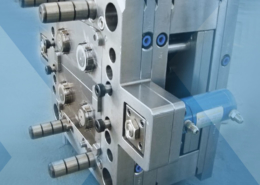
Exploring the Efficiency and Innovation of Polyethylene Injection Moulding
Author:gly Date: 2024-06-08
Introduction
Polyethylene injection moulding stands as a cornerstone of modern manufacturing, offering a versatile and cost-effective solution for producing a wide range of plastic components. With its ability to create intricate shapes with precision and efficiency, polyethylene injection moulding has become indispensable across various industries. This article aims to delve into the intricacies of polyethylene injection moulding, highlighting its applications, advantages, challenges, and future prospects.
Understanding Polyethylene Injection Moulding
Polyethylene Composition:
Polyethylene, a thermoplastic polymer, is derived from ethylene monomers and is renowned for its versatility, durability, and chemical resistance. In the injection moulding process, polyethylene pellets are melted and injected into a mould cavity under high pressure, where they cool and solidify to form the desired shape.
Injection Moulding Process:
The injection moulding process involves several key steps, including material preparation, injection, cooling, and ejection. Polyethylene pellets are fed into a hopper, where they are heated to their melting point and then injected into a mould cavity using a reciprocating screw or plunger. Once the material has cooled and solidified, the mould opens, and the finished part is ejected.
Applications and Industries
Packaging Industry:
One of the primary applications of polyethylene injection moulding is in the packaging industry, where it is used to produce a wide range of containers, bottles, and caps. Polyethylene's lightweight nature, durability, and versatility make it an ideal choice for packaging applications, offering manufacturers a cost-effective solution for protecting and preserving their products.
Automotive Sector:
In the automotive sector, polyethylene injection moulding is used to produce a variety of interior and exterior components, including dashboard panels, door trims, and bumpers. Polyethylene's ability to withstand harsh environmental conditions, such as temperature fluctuations and exposure to chemicals, makes it well-suited for automotive applications.
Advantages and Challenges
Advantages of Polyethylene Injection Moulding:
Polyethylene injection moulding offers several key advantages, including high production efficiency, design flexibility, and cost-effectiveness. The ability to produce complex shapes with tight tolerances allows manufacturers to create innovative and aesthetically pleasing products while minimizing waste and reducing production costs.
Challenges and Considerations:
Despite its many advantages, polyethylene injection moulding also presents certain challenges, particularly in terms of environmental sustainability. Polyethylene is derived from fossil fuels and is not biodegradable, leading to concerns about plastic pollution and resource depletion. Addressing these challenges requires a concerted effort to develop sustainable alternatives, improve recycling infrastructure, and implement circular economy practices.
Future Prospects and Innovations
Technological Advancements:
Looking ahead, technological advancements in polyethylene injection moulding are poised to revolutionize the manufacturing landscape. Innovations such as 3D printing, advanced mould design software, and sustainable materials development hold the potential to enhance efficiency, reduce waste, and expand the scope of applications for polyethylene-based products.
Sustainability Initiatives:
Furthermore, sustainability initiatives will play a crucial role in shaping the future of polyethylene injection moulding. Manufacturers, policymakers, and consumers must collaborate to develop and implement strategies that promote resource conservation, waste reduction, and the adoption of eco-friendly materials. By embracing sustainability as a guiding principle, the industry can mitigate its environmental impact while driving innovation and growth.
Conclusion
In conclusion, polyethylene injection moulding stands as a testament to human ingenuity and technological innovation in the manufacturing industry. Its versatility, efficiency, and reliability make it a cornerstone of modern production processes, serving diverse applications across various sectors. As we navigate the challenges of the 21st century, embracing sustainable practices and fostering technological innovation will be essential in unlocking the full potential of polyethylene injection moulding and shaping a more sustainable future for generations to come.
GETTING A QUOTE WITH LK-MOULD IS FREE AND SIMPLE.
FIND MORE OF OUR SERVICES:
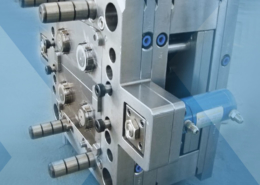
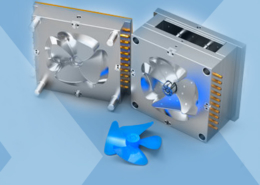
Plastic Molding

Rapid Prototyping
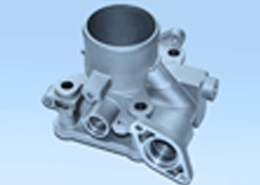
Pressure Die Casting
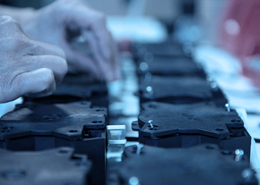
Parts Assembly
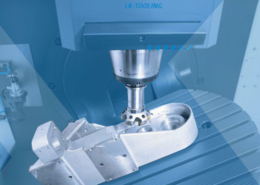