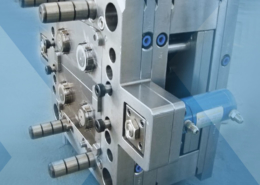
How Rapid Prototype Injection Molding Benefits Plastics ... - rapid prototyping
Author:gly Date: 2024-10-15
Contact one of our sales representatives todayto inquire about a quote from Trident Components or call us today at 888-312-0745. Typical volumes start at 2500 pieces, average orders are usually 10,000 - 20,000 pieces.
HDPE has poor UV resistance as the carbon-hydrogen bonds are attacked by UV radiation. The breaking of these bonds ultimately causes photo-oxidation which degrades the material over time. Additives like UV stabilizers can be incorporated into the HDPE formulation to improve its UV resistance.Â
Plastic bottles are one of the most popular uses for HDPE. While most bottles are formed using blow molding techniques, the blank tubes used to make these bottles must be injection molded. HDPE does not leach into the stored liquid and is highly moisture-resistant, making it ideal for bottling applications.Â
Choose from millions of possible combinations of materials, finishes, tolerances, markings, and certifications for your order.
Hard hats must be able to withstand sudden impacts and must also absorb as much of the impact energy as possible. As such, HDPE is an excellent choice for hard hats as it is a highly durable and impact-resistant material.Â
HDPE is a popular material for garden furniture due to its low cost. The strength and toughness of HDPE make it possible to produce lightweight and low-cost furniture without compromising mechanical strength. HDPE can also be downcycled for use in imitation lumber that can be used to produce low-cost furniture.Â
HDPE is highly resistant to moisture and is relatively flexible. As such, it is widely used for piping to transport large volumes of water. Individual pipe sections are welded together to eliminate potential leaks. These pipes are often buried underground.Â
HDPE is susceptible to environmental stress cracking. When exposed to long-term tensile loads, cracks can form in the material. This is further exacerbated if the HDPE is exposed to a corrosive environment. These cracks can develop at loads much lower than the tensile strength of the material.Â
HDPE is a thermoplastic. It can be remelted and reused if properly processed at a recycling plant. Most recycling plants will accept HDPE due to its widespread use, in addition to HDPE being one of the easiest plastics to recycle. HDPE can also be downcycled, i.e., reused on lower-value items like imitation plastic lumber.Â
Get custom HDPE injection molded prototypes and production parts in as few as five business days. Dozens of materials and finishes are available. ISO 9001:2015, ISO 13485, IATF 16949:2016, and AS9100D certified.
Xometry offers the highest quality HDPE injection molding service and is able to assist with the design of the part and tooling to ensure it follows DFM (Design for Manufacturing) best practices. This will help ensure the product can be successfully manufactured with no defects. Thereafter, Xometry can facilitate manufacturing with one of our trusted partners to ensure the parts are produced to the required specifications. HDPE is a popular injection molding material as it has excellent processability. HDPE also has a low moisture absorption rate and is lightweight, making it ideal for a wide range of applications.Â
Trident Components has extensive experience in high density polyethylene, or HDPE injection molding. Commonly favored for its strength, low cost, and impact resistance, HDPE can be molded into a variety of shapes and products. At Trident, we pride ourselves on our custom production capabilities, cutting-edge facilities, and warehousing services to accurately and cost-effectively meet the demands of any sized project.
Injection molding HDPE requires a large amount of initial capital investment as the tooling can be very expensive. It is only cost-effective for larger production volumes. Listed below are two potential alternatives to HDPE injection molding:
High-Density Polyethylene (HDPE) is a thermoplastic polymer supplied in pellet form for injection molding. HDPE is widely used for injection molding due to its low cost, chemical resistance, high tensile strength, impact resistance, and low moisture absorption. In addition to its physical properties, HDPE has excellent processability due to its relatively low melt temperature and low viscosity.Â
HDPE is considered a commodity plastic and is relatively low-cost when compared to other plastics like polypropylene, for example. This makes it a cost-effective material to use for injection molded products. It must, however, be noted that the tooling required for injection molding is often the largest contributor to initial set-up cost.Â
HDPE is considered food-safe and is approved by the FDA. It is widely used for both single-use and long-term food storage applications. In addition, HDPE is very tough and can protect the food contents during transportation.Â
Each HDPE formulation will have a unique set of material properties depending on their intended application. Table 1 below lists some common material properties of standard HDPE:
HDPE is highly resistant to moisture ingress. Also, with the addition of UV (ultraviolet) stabilizers, HDPE can be made resistant to UV radiation, making it an ideal material for outdoor applications.Â
HDPE is considered food-safe by the FDA (Food and Drug Administration) and is widely used to store food items. HDPE is highly inert and stable and as such does not leach dangerous chemicals into food products.Â
HDPE has a density of around 960 kg/m3. This is lightweight compared to metals and even some plastics. HDPE also has a high strength-to-weight ratio which means it can be used to produce thin-walled products like bottles or chemical tanks but still maintain high levels of strength and rigidity.
HDPE has low thermal conductivity. If cooling is too quick or uneven, this can result in the part warping or shrinking during injection molding. HDPE can have a shrinkage rate of between 1.5% and 4.0%.
GETTING A QUOTE WITH LK-MOULD IS FREE AND SIMPLE.
FIND MORE OF OUR SERVICES:
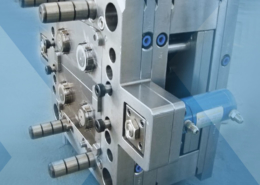
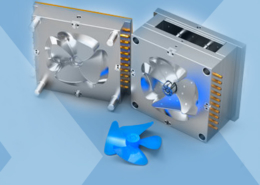
Plastic Molding

Rapid Prototyping
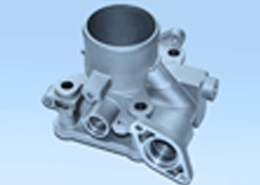
Pressure Die Casting
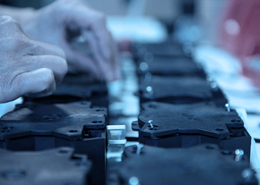
Parts Assembly
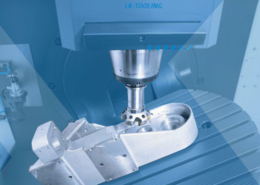