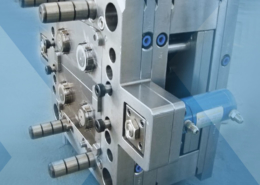
How Prototype Tooling in Injection Molding Accelerates ... - prototype tooling p
Author:gly Date: 2024-10-15
Kaysun has carried the MedAccred Plastics accreditation since 2020, demonstrating our ongoing commitment to excellence and assuring medical OEMs of an unparalleled benchmark of production and quality standards.
Mold life affects mainly the tooling cost. Prototype molds use regular steels such as P20 or 718H. For production molds at higher volume, hardened steel would be required, like NAK 80 or H13.
Kaysun is experienced with medical product design, production, and assembly. We are ISO 13485:2016 certified and MedAccred Plastics accredited.
Portable medical devices are a mainstay in hospitals, emergency vehicles, and outpatient environments. The devices must remain accurate and functional; however, drops, bumps, and excessive vibration are inevitable as equipment is transported from place to place.Overmolding is a proven solution for shock and vibration reduction, sound dampening, electrical insulation, improved chemical/UV resistance, effective oxygen and moisture barrier protection, and color infusion.
“Kaysun exceeded our expectations in all areas. They made a complex, gigantic program easy from an engineering standpoint. Working with the Kaysun engineering team is like a hot knife through butter.”
Earning accreditation is a rigorous process, and only a small fraction of medical injection molding companies receive the distinction.
Medical device performance is largely dependent on the characteristics of the materials used and application needs such as strength, flexibility, transparency, biocompatibility, safety-enhancing microbe resistance, and temperature and chemical resistance. With thousands of engineered materials to choose from, it's important to work with experts in medical device injection molding.
The rapid advancement of the medical industry necessitates constant innovation and complexity in medical device design. Smaller sizes, more intricate geometries, progressive functionalities, and portability are among the greatest needs in today’s medical equipment — and among the biggest challenges for design and engineering teams.
Leveraging the experience and knowledge of medical injection molders during the design phase of complex applications can help overcome the unique challenges of medical injection molding and improve outcomes.
There are many factors that can affect the cost on making an mold and running molding production. Here we show you three examples how the various pricing might have. Please note that the price can vary depending on your parts size, weight and complexity.
The part color is the factor that designers and product engineers will neglect, as they assume piece pricing of all colors is the same.
Medical OEMs are tasked with providing consistent, high-performance solutions to the challenges posed by a variety of complex applications. Partnering with a custom injection molder that has the experience, knowledge, technical expertise, and certifications needed to adhere to the exacting standards of the medical industry is imperative.Not every molder is qualified, but those who are — like Kaysun — can move your business forward with confidence.
“How much does the China injection molding cost to make my product?”; “Is there any way to lower the mold cost in China?”. These are the most common questions we hear from our customers, especially start-ups. It’s quite understandable that the injection molding cost of a new plastic part is critical and sensitive, particularly when your budget is tight for a new design.
Mirror polishing adds cost to injection molding, which requires hardened steels (NAK 80 Steel) to create the molds and cleaner injection molding condition. Also, a higher texturing requirement is another reason to cost increases.
However, if your part is white or transparent, the molding price will be higher than other regular colors. A cleaner molding condition adds cost for molding factories.
The plastic molding material you selected will affect both tooling cost and piece pricing, which varies from different types of materials.
Complexity plays a vital role in molding costs. It adds extra works to mold making and more steps on molding production. Tolerance requirements, fine detailing, or the number of undercuts are the main reasons.
As medical device design evolves to provide ever-improving healthcare outcomes, manufacturers are partnering with full-service, experienced custom injection molders to gain increased design freedom and process efficiencies.Partnering with Kaysun — one of the few injection molders in the country to hold MedAccred Plastics accreditation — is a consistent value-add from part and tooling design through material selection and process control. It empowers many medical OEMs to address issues before they impact production or the bottom line.
MedAccred is a Performance Review Institute medical device industry-managed supply chain oversight program dedicated to reducing patient safety risk. It focuses on critical manufacturing processes compliance and device quality and consistency.
GETTING A QUOTE WITH LK-MOULD IS FREE AND SIMPLE.
FIND MORE OF OUR SERVICES:
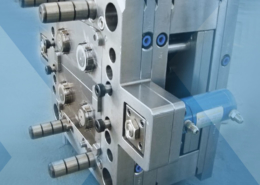
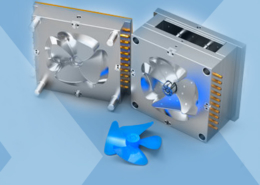
Plastic Molding

Rapid Prototyping
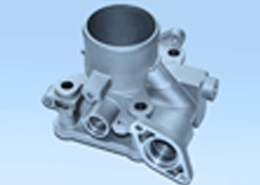
Pressure Die Casting
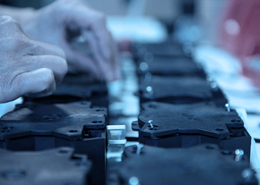
Parts Assembly
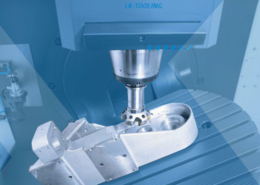