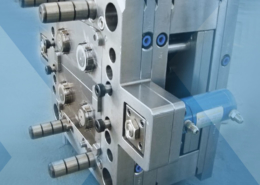
Exploring the Precision of Polycarbonate Injection Molding
Author:gly Date: 2024-06-08
Introduction
Polycarbonate injection molding stands as a pinnacle of precision and efficiency in modern manufacturing. From electronic enclosures to automotive components, polycarbonate injection molding offers unparalleled versatility and performance. In this article, we delve into the intricacies of polycarbonate injection molding, exploring its applications, advantages, and the transformative impact it has on various industries.
Unveiling the Process of Polycarbonate Injection Molding
Polycarbonate injection molding is a sophisticated process that involves injecting molten polycarbonate resin into a mold cavity under high pressure. This method allows for the precise replication of intricate geometries and features, ensuring consistent quality and dimensional accuracy in the final products.
The versatility of polycarbonate injection molding is exemplified by its ability to produce a wide range of components, from small, intricate parts to large, structural elements. The process can be tailored to meet the specific requirements of different industries, offering flexibility in design and production.
Applications Across Industries
The applications of polycarbonate injection molding span across diverse industries, showcasing its adaptability and versatility. In the electronics sector, polycarbonate is utilized for manufacturing housings, bezels, and display panels for smartphones, laptops, and other electronic devices. Its excellent optical clarity, impact resistance, and heat resistance make it an ideal choice for demanding electronic applications.
In the automotive industry, polycarbonate injection molding is instrumental in the production of interior trim components, lighting assemblies, and exterior body panels. The lightweight nature of polycarbonate, coupled with its exceptional strength and durability, contributes to fuel efficiency and vehicle performance.
Moreover, the medical sector leverages polycarbonate injection molding for manufacturing medical devices, such as surgical instruments, drug delivery systems, and diagnostic equipment. The biocompatibility and sterilizability of polycarbonate make it suitable for applications requiring stringent safety and hygiene standards.
Advantages and Innovations
The widespread adoption of polycarbonate injection molding is driven by its myriad advantages, including high strength-to-weight ratio, chemical resistance, and design flexibility. Unlike traditional materials such as metal or glass, polycarbonate offers greater design freedom, allowing for the creation of complex shapes and features without sacrificing performance.
Furthermore, ongoing innovations in material science and molding technology continue to enhance the capabilities of polycarbonate injection molding. The development of reinforced polycarbonate grades, advanced surface finishes, and rapid prototyping techniques opens new possibilities for applications in aerospace, consumer goods, and industrial sectors.
Sustainability and Future Directions
As the global emphasis on sustainability grows, polycarbonate injection molding is evolving to meet the demands of eco-conscious consumers and regulatory standards. The recyclability of polycarbonate materials and the adoption of recycled content in molding processes offer a pathway towards reducing environmental impact and promoting circular economy principles.
Moreover, research efforts are underway to explore alternative materials and manufacturing techniques that further enhance the sustainability of polycarbonate injection molding. Bio-based polymers, additive manufacturing, and closed-loop recycling systems hold promise for shaping the future of plastic molding towards a more sustainable and resilient industry.
Conclusion
In conclusion, polycarbonate injection molding represents a cornerstone technology in modern manufacturing, offering unparalleled versatility, performance, and sustainability. From electronics to automotive to medical applications, its impact spans across diverse industries, driving innovation and shaping the future of materials engineering.
As we look towards the future, the continued advancement of polycarbonate injection molding holds immense potential for addressing global challenges and driving sustainable development. By embracing innovation, collaboration, and responsible manufacturing practices, we can harness the full potential of polycarbonate injection molding to create a brighter, more sustainable future for generations to come.
GETTING A QUOTE WITH LK-MOULD IS FREE AND SIMPLE.
FIND MORE OF OUR SERVICES:
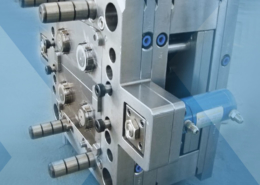
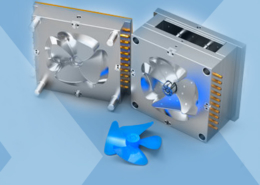
Plastic Molding

Rapid Prototyping
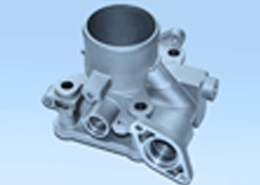
Pressure Die Casting
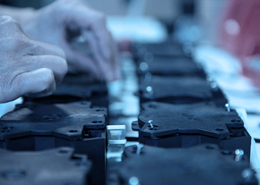
Parts Assembly
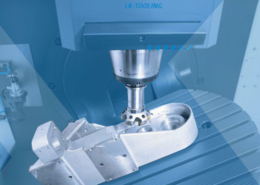