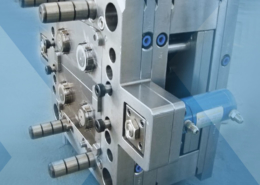
Exploring Polycarbonate Injection Molding: Unveiling Versatility and Durability
Author:gly Date: 2024-06-08
Introduction
Polycarbonate injection molding stands at the forefront of modern manufacturing, offering a versatile and robust solution for producing a wide range of components and products. As one of the most widely used thermoplastics, polycarbonate exhibits exceptional mechanical properties, optical clarity, and heat resistance, making it a preferred choice for applications spanning automotive, electronics, aerospace, and consumer goods. This article delves into the realm of polycarbonate injection molding, uncovering its significance, techniques, applications, advancements, and challenges.
Significance of Polycarbonate Injection Molding
Versatility in Design
Polycarbonate injection molding enables the creation of intricate geometries, complex features, and precise details, empowering designers to realize their creative visions and push the boundaries of product innovation. From sleek automotive components to ergonomic consumer electronics, the versatility of polycarbonate molding caters to diverse design requirements and aesthetic preferences.
Durability and Impact Resistance
With its exceptional strength-to-weight ratio and impact resistance, polycarbonate is renowned for its ability to withstand harsh environments and mechanical stress. Injection molding processes further enhance the durability and performance of polycarbonate components, ensuring reliability and longevity in demanding applications such as automotive interiors, protective eyewear, and industrial enclosures.
Optical Clarity and Transparency
Polycarbonate's optical clarity and transparency make it an ideal choice for applications requiring clear or tinted components, such as lighting fixtures, display panels, and medical devices. Injection molding techniques preserve polycarbonate's optical properties, enabling the production of high-quality parts with minimal distortion or blemishes.
Techniques in Polycarbonate Injection Molding
Precision Molding
Precision molding techniques, such as hot-runner systems and advanced mold designs, optimize the injection molding process for polycarbonate, ensuring consistent part quality, dimensional accuracy, and surface finish. These techniques minimize defects such as warping, sink marks, and flash, resulting in superior parts with tight tolerances and exceptional aesthetics.
High-Speed Molding
High-speed injection molding technologies leverage advanced machine capabilities, rapid cooling systems, and optimized process parameters to achieve shorter cycle times and higher productivity in polycarbonate molding. By reducing production lead times and enhancing throughput, high-speed molding facilitates cost-effective mass production of polycarbonate components for various industries.
Gas-Assisted Molding
Gas-assisted injection molding enhances the design flexibility and performance of polycarbonate parts by introducing nitrogen gas into the mold cavity during the injection process. This technology creates hollow sections, ribs, and complex geometries within the part, reducing material usage, minimizing sink marks, and improving structural integrity.
Challenges and Future Directions
Heat Management
Managing heat during polycarbonate injection molding is crucial to preventing thermal degradation, flow instabilities, and part defects. Advancements in mold design, cooling systems, and process monitoring technologies are essential to optimize heat transfer, maintain melt consistency, and ensure uniform filling of mold cavities.
Material Innovation
Continued research and development in polycarbonate formulations aim to enhance material properties, such as impact strength, chemical resistance, and flame retardancy, to meet evolving industry standards and regulatory requirements. Innovations in bio-based polycarbonates, recycled materials, and sustainable additives further promote environmental sustainability and circularity in injection molding processes.
Integration of Smart Technologies
The integration of smart sensors, real-time monitoring systems, and predictive analytics into polycarbonate injection molding processes enables data-driven decision-making, process optimization, and quality assurance. Future research may focus on implementing artificial intelligence, machine learning, and digital twin technologies to enhance process control, reduce variability, and ensure consistency in part production.
Conclusion
In conclusion, polycarbonate injection molding stands as a cornerstone in modern manufacturing, offering unparalleled versatility, durability, and optical clarity across diverse industries and applications. By harnessing advanced molding techniques, precision engineering, and material innovation, manufacturers can unlock the full potential of polycarbonate to create innovative products that meet the demands of today's dynamic marketplace. As technology continues to evolve and industry trends shift towards sustainability, the future of polycarbonate injection molding holds promise for continued innovation, efficiency, and environmental stewardship. Embracing challenges, fostering collaboration, and embracing emerging technologies will ensure that polycarbonate injection molding remains at the forefront of manufacturing excellence for years to come.
GETTING A QUOTE WITH LK-MOULD IS FREE AND SIMPLE.
FIND MORE OF OUR SERVICES:
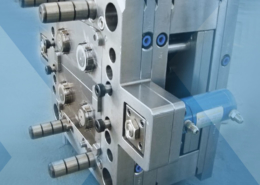
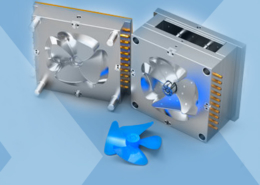
Plastic Molding

Rapid Prototyping
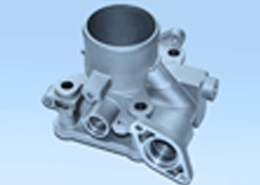
Pressure Die Casting
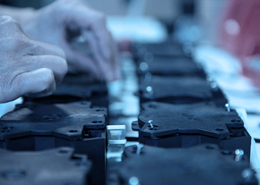
Parts Assembly
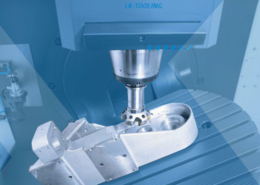