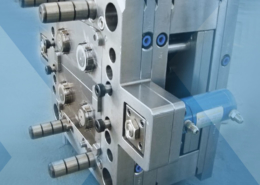
Plastic Prototype Manufacturing: Bridging Ideas to Reality
Author:gly Date: 2024-06-08
Introduction
Plastic prototype manufacturing serves as a crucial bridge between concept and production in various industries, ranging from automotive and aerospace to consumer electronics and healthcare. This article delves into the realm of plastic prototype manufacturing, exploring its significance, methodologies, applications, and future prospects.
Understanding Plastic Prototyping
Plastic prototyping involves the fabrication of functional or visual models of a product using various plastic materials and manufacturing techniques. These prototypes serve multiple purposes, including concept validation, design verification, market testing, and investor pitches. By allowing stakeholders to visualize and interact with a physical representation of their ideas, plastic prototyping accelerates the product development process and mitigates risks associated with design flaws and manufacturing issues.
Methodologies and Technologies
Plastic prototype manufacturing encompasses a diverse range of methodologies and technologies, each suited to specific design requirements, production volumes, and budget constraints. Common techniques include 3D printing (additive manufacturing), CNC machining, injection molding, vacuum casting, and thermoforming. Advancements in additive manufacturing, such as stereolithography (SLA), selective laser sintering (SLS), and fused deposition modeling (FDM), have revolutionized the prototyping landscape, enabling rapid iteration, complex geometries, and cost-effective small-batch production.
Applications Across Industries
Plastic prototypes find applications across a myriad of industries, driving innovation, efficiency, and competitiveness. In the automotive sector, prototypes enable engineers to test new vehicle designs, components, and safety features before mass production, thereby reducing time-to-market and development costs. Similarly, in the medical field, prototypes facilitate the development of cutting-edge devices, implants, and instruments, fostering advancements in patient care and treatment outcomes. From consumer electronics and household appliances to aerospace and defense, plastic prototypes play a pivotal role in shaping the products and technologies of tomorrow.
Challenges and Future Directions
Despite its numerous benefits, plastic prototype manufacturing faces challenges such as material selection, surface finish, accuracy, and scalability. Addressing these challenges requires ongoing research and development efforts aimed at enhancing material properties, refining manufacturing processes, and optimizing cost-performance ratios. Additionally, emerging trends such as digital twin technology, generative design, and sustainable materials offer exciting opportunities to further improve the plastic prototyping workflow and outcomes. By embracing these trends and collaborating across disciplines, the plastic prototyping industry can continue to push the boundaries of innovation and drive meaningful impact across sectors.
Conclusion
In conclusion, plastic prototype manufacturing serves as a cornerstone of modern product development, facilitating innovation, iteration, and validation in diverse industries. Through a combination of advanced technologies, interdisciplinary collaboration, and continuous improvement, plastic prototyping enables stakeholders to translate ideas into tangible solutions efficiently and effectively. As we look to the future, investing in research, education, and infrastructure will be essential to overcome challenges, seize opportunities, and unlock the full potential of plastic prototyping in driving progress and prosperity.
GETTING A QUOTE WITH LK-MOULD IS FREE AND SIMPLE.
FIND MORE OF OUR SERVICES:
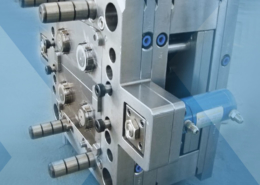
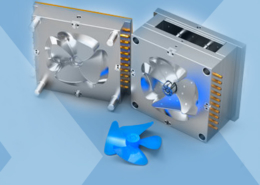
Plastic Molding

Rapid Prototyping
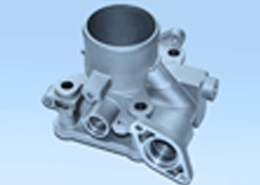
Pressure Die Casting
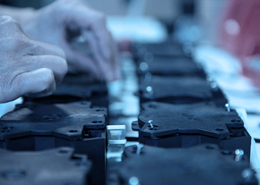
Parts Assembly
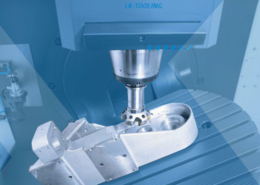