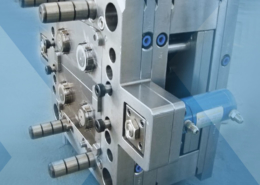
Exploring the World of Plastic Part Molding
Author:gly Date: 2024-06-08
Plastic part molding stands as a cornerstone of modern manufacturing, shaping the way we produce a multitude of products across various industries. From intricate components in electronics to durable housings in automotive engineering, plastic part molding plays a pivotal role in bringing design concepts to life. In this article, we embark on a journey to unravel the complexities and nuances of plastic part molding, delving into its processes, applications, challenges, and future prospects.
1. The Art of Plastic Part Molding
Plastic part molding encompasses a diverse range of techniques aimed at shaping molten plastic into desired forms. Injection molding, perhaps the most widely used method, involves injecting molten plastic into a mold cavity under high pressure. This process offers unparalleled precision, repeatability, and scalability, making it ideal for mass production of intricate components. Other methods such as blow molding, compression molding, and rotational molding cater to specific design requirements and production volumes, offering versatility and cost-effectiveness.
The evolution of plastic part molding has been marked by advancements in materials science, mold design, and process automation. Today, manufacturers leverage cutting-edge technologies such as computer-aided design (CAD), computer-aided manufacturing (CAM), and real-time monitoring systems to optimize production workflows and ensure consistent part quality.
2. Applications Across Industries
Plastic part molding finds applications across a myriad of industries, driving innovation and progress in fields ranging from healthcare to consumer electronics. In the automotive sector, plastic molded components contribute to weight reduction, fuel efficiency, and enhanced safety features. From interior trim panels to engine components, plastic parts play integral roles in modern vehicles, offering durability, aesthetics, and functionality.
Similarly, in the medical industry, plastic part molding enables the production of sterile, biocompatible components used in diagnostic devices, surgical instruments, and drug delivery systems. The ability to achieve precise geometries and tolerances makes plastic molding indispensable in applications where accuracy and reliability are paramount.
3. Engineering Challenges and Solutions
While plastic part molding offers numerous advantages, it also presents unique engineering challenges that require innovative solutions. Designing molds capable of accommodating complex geometries while ensuring efficient material flow and cooling is a critical aspect of the molding process. Additionally, optimizing cycle times, minimizing part defects, and reducing environmental impact are ongoing priorities for manufacturers.
Advanced simulation tools, such as mold flow analysis software, facilitate the optimization of mold designs and process parameters, enabling manufacturers to identify potential issues and mitigate risks before production begins. Furthermore, the integration of sustainable materials and recycling initiatives into the molding process is essential for minimizing waste and promoting environmental responsibility.
4. Future Perspectives and Innovations
Looking ahead, the future of plastic part molding is ripe with possibilities, driven by advancements in materials, technology, and sustainability initiatives. The emergence of bio-based polymers, recyclable materials, and additive manufacturing techniques promises to revolutionize the way we approach plastic molding, offering greener alternatives and novel design possibilities.
Moreover, the integration of artificial intelligence, robotics, and machine learning algorithms into molding processes holds the potential to optimize production efficiency, reduce costs, and enhance product quality. By embracing digitalization and automation, manufacturers can streamline operations, respond to changing market demands, and stay ahead of the competition in an increasingly dynamic landscape.
In summary, plastic part molding stands as a testament to human ingenuity and innovation, enabling the creation of complex shapes and structures with precision and efficiency. From its humble beginnings to its current state of technological sophistication, plastic molding continues to shape the world around us, driving progress and innovation across industries. By embracing sustainability, embracing emerging technologies, and fostering collaboration, the future of plastic part molding holds immense promise for creating a more efficient, resilient, and sustainable world.
GETTING A QUOTE WITH LK-MOULD IS FREE AND SIMPLE.
FIND MORE OF OUR SERVICES:
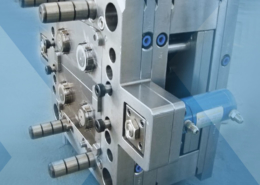
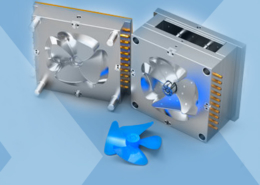
Plastic Molding

Rapid Prototyping
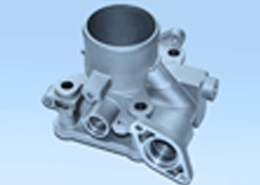
Pressure Die Casting
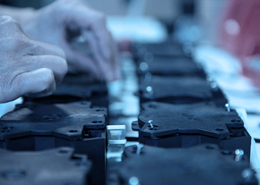
Parts Assembly
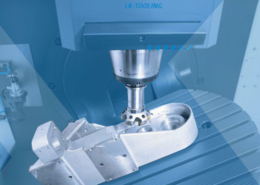