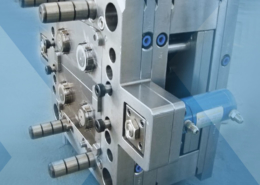
High Temperature Plastic Injection Molding services - thermal molding plastic
Author:gly Date: 2024-10-15
Yes, polyethylene (PE) can be injection molded. It is one of the most commonly used thermoplastics in injection molding due to its versatility, flexibility, and cost-effectiveness. Both high-density polyethylene (HDPE) and low-density polyethylene (LDPE) are frequently used in various applications, from packaging to industrial products.
Keep reading to discover the key insights on PE injection molding, explore its unique properties, and learn why it’s the go-to material for countless industries.
PE is also prominent in medical devices, where its low toxicity and sterilization capabilities make it suitable for products like catheters and other components.
With its versatility across industries from consumer goods to industrial components, PE remains a key material in modern manufacturing.
HITOP is committed to assisting customers by offering a comprehensive one-stop solution, encompassing product design enhancement, initial sample creation, mold fabrication, injection molding, and product assembly.
Plastic bottles, from water bottles to detergent containers, are often made of PE, particularly HDPE, due to their moisture resistance and strength.
It offers excellent flexibility, chemical resistance, and electrical insulation, which makes it ideal for applications in harsh environments.
Polyethylene (PE) is a thermoplastic polymer derived from the polymerization of ethylene, a by-product of petroleum refining.
In agriculture, PE plays an essential role, particularly through products like irrigation tubes, which require the material’s weather resistance and flexibility.
Hi, I am Sparrow Xiang, COO of the HiTop company, me and my team would be happy to meet you and learn all about your business, requirements and expectations.
Contact us today to learn more about our customized solutions and how we can help bring your ideas to life efficiently and affordably!
Its soft nature and high elongation also allow it to absorb impact without breaking, although its mechanical strength varies depending on its density.
Another common issue is flow marks, which appear as lines or patterns on the surface of the part, often caused by improper injection speed or cooling inconsistencies.
The cooling system must also be optimized to prevent variations in part density, especially when working with LDPE, which has higher flexibility but lower rigidity than HDPE.
Polyethylene comes in different grades, such as LDPE (Low-Density Polyethylene), HDPE (High-Density Polyethylene), and other variants, each having unique properties.
In the medical field, PE tubing is commonly used in various medical settings, thanks to its flexibility, chemical resistance, and sterilizability.
Its broad application scope stems from its flexibility, chemical resistance, and ease of processing, making it a go-to material across industries.
Storage containers made from PE provide excellent chemical resistance, making them ideal for handling various industrial liquids.
When considering injection molding materials, it’s essential to compare polyethylene (PE) with other commonly used thermoplastics like polypropylene (PP) and nylon.
Below is a comparison of PE with PP and nylon, covering key factors such as cost, flexibility, strength, and common uses:
The key difference between polypropylene (PP) and polyethylene (PE) injection molding lies in their properties and applications. Polyethylene is more flexible and has better chemical resistance, making it ideal for containers, packaging, and films. On the other hand, polypropylene is stiffer and has higher heat resistance, making it more suitable for automotive parts, textiles, and household goods.
Yes, polyethylene can be molded using various methods, with injection molding being the most popular. Its ability to melt and flow easily when heated makes it an excellent choice for creating a wide range of products. The flexibility of LDPE and the strength of HDPE allow for diverse applications, from everyday items to specialized industrial components.
For HDPE, molds must account for the higher shrinkage rates of up to 4%, which can lead to warping or dimensional inaccuracies.
Polyethylene injection molding offers flexibility, durability, and cost-efficiency, making it one of the most popular methods for producing a wide range of products.
Polyethylene (PE) injection molding is a crucial process used to create versatile, durable plastic products across various industries.
In the industrial sector, PE is used to manufacture pipes, which are valued for their corrosion resistance and flexibility.
The temperature range for polyethylene injection molding varies based on the type of polyethylene. For LDPE, the melt temperature typically ranges from 180°C to 240°C, while HDPE is molded at temperatures between 246°C and 280°C. The mold temperature also varies, typically around 20°C to 60°C for LDPE and 45°C to 65°C for HDPE.
We are committed to helping you elevate quality standards, fostering enterprise growth, and actualizing your internationalization strategy.
Polyethylene (PE) injection molding is widely utilized in various industrial applications due to its versatility and durability.
In packaging, films, and wraps made from LDPE offer excellent moisture barriers and durability, making them ideal for food and product packaging.
GETTING A QUOTE WITH LK-MOULD IS FREE AND SIMPLE.
FIND MORE OF OUR SERVICES:
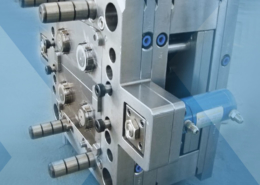
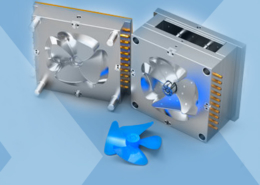
Plastic Molding

Rapid Prototyping
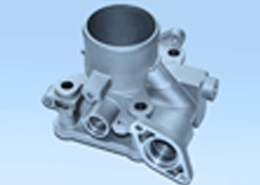
Pressure Die Casting
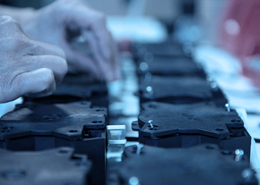
Parts Assembly
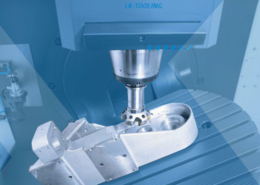