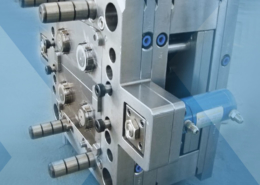
High Precision & Thin Wall Injection Molding - high precision injection molding
Author:gly Date: 2024-10-15
4.deformation of the ejector plate or injection molding machine top stick length, resulting in unbalanced ejections and pull white.
Mould Cavity: Different number of cavities will affect the choice of gate position, usually the number of cavities will be selected according to the size of the injection molding machine.
The fast pace of injection molding technology, constant staff training and adoption of new manufacturing methods helps FirstMold to remain in the lead of injection molding business. We constantly explore and investigate new materials and methods to cater to the demand for the latest technology by our clients.
1.The holding pressure is too large, the internal stress is large, and the deformation is large within 24h after leaving the mold.
Our meticulous approach and advanced knowledge position us at the forefront, ensuring exceptional quality and precision in POM injection molding projects. Choose FirstMold, where excellence is not just achieved but guaranteed.
POM is widely used in industrial manufacturing due to its metal-like properties, self-lubrication, fatigue resistance, thermal stability, and wear resistance, serving a multitude of industries.
When injecting ABS plastic into general injection molding machine, each injection volume is only 75% of the standard injection volume. In order to improve the quality and dimensional stability of the parts, surface gloss and uniformity of color, it is appropriate to require an injection volume of 50% of the standard injection volume.
The molding temperature of ABS is relatively high, and the mold temperature is also relatively high. When producing parts with large projection area, the fixed mold temperature should be 70~80℃ and the moving mold temperature should be 50~60℃. In order to shorten the production cycle and maintain the relative stability of mold temperature, cold water bath, hot water bath or other mechanical shaping method can be used to compensate for the time of cold fixing in the cavity after the parts are taken out.
At FirstMold, our understanding of POM plastics far exceeds that of our rivals. We excel in working with a broad array of Delrin’s modified materials, including but not limited to, enhanced toughness, wear resistance, and UV protection POM variants.
ABS Material Type: Different ABS material, the MFI is different, which will affect the size and position of the gate runner.
Clients of FirstMold are granted updates as frequent as they would need and they also have access to a project manager who can provide answers to their questions and progress reports. We value transparency in communication, which all the while maintains you as an informed and satisfied customer.
The core difference between our injection molding and plastic injection molding service, however, lies in the scope of materials involved and the processes utilized. The scope of our injection molding service covers the special category of plastic injection molding, along with other varieties of injection molding. In other words, although FirstMold’s injection molding services comprise of a variety of materials and methods (like LSR molding of silicones, etc), plastic injection molding services of FirstMold focus on manufacturing parts explicitly from plastics. This classification allows us to develop wide range of solutions to various project demands that we may specialize in the area of injection molding.
FirstMold's custom hair trimmer manufacturing meets stringent customer requirements for appearance and performance. This is a case.
The viscosity of ABS molten parts is higher than that of polystyrene or modified polystyrene, so a higher injection pressure is used during injection. Of course, not all ABS parts need to be injected at high pressure, but small, simple and thick parts can be injected at a lower pressure. During the injection process, the pressure in the cavity at the moment of gate closure often determines the surface quality of the product and the degree of silver wire defects. If the pressure is too low, the plastic shrinks and has a greater chance of disengaging from the cavity surface, resulting in a hazy surface. Pressure is too large, the plastic cavity surface friction is strong, easy to cause sticky mold.
It is not easy to do a good job of ABS injection molding products, need years of experience in mold and injection molding, in product design and mold design need to do a lot of analysis, especially mold flow analysis must be done, only the design of the product in line with the mold production requirements, mold design in line with the requirements of injection molding production, so that the products made to achieve the expected results, even if the product injection are normal, but also need to do a good job in time mold Maintenance, such as checking whether the waterway is blocked, whether there is leakage of ABS material, whether the mold is touched in the production process, etc. This series of problems are well controlled to ensure that the production of ABS products is smooth, so it is very important to find a qualified ABS injection molding manufacturer.
According to the complexity of the structure of the ABS product mold to do different processing arrangements, if the mold structure is simple, as long as the CNC milling, EDM processing can be completed mold, if the mold structure is more complex, will carry out a series of processing technology. For example, CNC, EDM, Deep hole Drill, Lathe, Grinding Machine, Wire-Electrode Cutting, CMM, Polish and Injection.
ABS plastic is hygroscopic and sensitive to moisture, sufficient drying and preheating before processing, not only to eliminate water vapor caused by the surface of the product smoky bubble, silver, but also help plasticization, reduce the surface color of the parts and cloud pattern. ABS raw materials to control the moisture below 0.13%. The drying conditions before injection are: 2~3h at 75~80℃ during the dry season or winter, 4~8h at 80~90℃ during the rainy days in summer, and longer drying time of 8~16h if the parts have to achieve a particularly good gloss or the parts themselves are complicated. It is advisable to convert the hopper of the machine into a hot air hopper dryer so that the dried ABS does not reabsorb moisture in the hopper, but this type of hopper should be monitored for humidity to prevent overheating of the material in case of occasional interruptions in production. The proportion of recycled material should not exceed 30%, and recycled material should not be used for plating grade ABS.
Tonnage of Machine: When injecting ABS plastic, the injection volume per shot is only 75% of the standard injection volume.
ABS material drying temperature : ABS material is hygroscopic and must be dried, drying conditions 80-90°C, 3hrs or more,
ABS is composed of acrylonitrile, butadiene and styrene. Acrylonitrile mainly provides chemical resistance and thermal stability; butadiene provides toughness and impact strength; and styrene provides hardness and processability for ABS. The combination of the three materials forms a comprehensive plastic.
If you have no knowledge and experience in molding and interested in the basics of injection molding, look no further as we will give you the answers. The injection molding is definitely a versatile and widely used manufacturing process, as it is perfect for producing parts needed in large quantities. To find out how it works, about its benefits, and on its applications of it in detail, we invite you to find out our well explained guide. This link will direct you to further information on injection molding: WHAT IS INJECTION MOLDING?
Injected Molded ABS Parts have become more and more common in life. Most plastic housings are made of ABS, such as household appliances, electronic products, game consoles, water purifiers, as well as industrial exterior parts, automotive interior parts, high-end garden planters, supermarket shelves, etc.
Firstmold’s objective is to provide small businesses and startups with the easy access to the needed materials by offering flexible order quantities, competitive prices, and personalized service. We deliver expertise through designing and production processes so parties without injection molding experience can bring their products in the market.
We have post-processing techniques such as silk screening, etching, laser engraving, and spraying. Additionally, we have professional partners specializing in electroplating and anodizing, with whom we have cooperated for over ten years.
Indeed, we can carry out material certifications and give quality reports comprehensive as needed for your injection molded parts on demand. These documents are intended to confirm the material specifications and prove the compliance of the product against your quality specifications.
The relationship between temperature and melt viscosity of ABS plastic is different from that of other amorphous plastics. Once it reaches the plasticization temperature (the temperature range suitable for processing, such as 220-250℃), if we continue to raise the temperature blindly, it will lead to the thermal degradation of ABS, which is not very heat resistant, and increase the melt viscosity, make injection more difficult, and decrease the mechanical properties of the parts. Therefore, although the injection temperature of ABS must be higher than that of polystyrene and other plastics, it cannot have a more relaxed temperature range like the latter. In some injection molding machines with poor temperature control, when a certain number of ABS parts are produced, more or less yellow or brown coke particles are found embedded in the parts, and it is difficult to remove them by adding new material to the empty injection. The reason for this is that ABS plastics contain butadiene, which causes degradation and carbonization when a plastic particle adheres firmly to some hard-to-wash surface in the screw tank at high temperatures and is subjected to prolonged high temperatures. Since high temperature operation can be a problem for ABS, it is necessary to limit the furnace temperature in each section of the barrel. Of course, the applicable furnace temperature varies for different types and compositions of ABS. For example, for plunger type machines, the furnace temperature is maintained at 180-230°C; for screw machines, the furnace temperature is maintained at 160-220°C. In particular, it is worth mentioning that ABS is sensitive to changes in various process factors due to its high processing temperature. Therefore, the temperature control of the front end of the barrel and the nozzle part is very important. It has been proven that any small change in these two parts will be reflected in the part. The greater the temperature variation, the greater the defects such as fusion seam, poor gloss, flying edge, sticky mold, and color change.
Yes, FirstMold is a team of experts at undertaking and completing operational high-volume injection molding projects with ease and precision. With the latest machinery that we posses on our premises, we are capable of producing high volumes without reducing quality. We can handle the requirements of tens of thousands parts to millions, thanks to the capabilities and capacity of our team, making sure you receive the delivered goods on time and the quality of the products.
Standard plastic injection molding machine can be used (screw L/D ratio 20:1, compression ratio more than 2, injection pressure more than 150MPa). If the use of color masterbatch or product appearance requirements are high, the use of a smaller diameter screw. The clamping force is determined according to 4700~6200t/m2, depending on the plastic grade and product requirements.
Although FirstMold can fully implement the intricate designs of injection molding with its well equipped CAD/CAM, qualified engineers, and upgraded machine tools, the company’s lead in this characteristic is its advanced technique in CAD/CAM and the experienced personnel. We carry on design consultation services to improve manufacturability of your product, so that even the most complex designs would be made with fantastic precision and efficiency.
6.The ejector structure is unreasonable, the ejector pin is not under the maximum clamping force, and the ejector is deformed.
Draft Angle: ≥1.5°, the draft angle not only affects the mold release, but also the appearance and assembly of the product. The side wall of plastic parts with skin pattern, sandblasting and other appearance treatment should take a draft angle of 2°~5° according to the specific situation.
Yes, FirstMold provides an all inclusive assembly and packaging service which considers client’s needs and offers an entirely finished product. We provide an array of services, encompassing assembly of multi- parts and different packaging options, that make your components fit for distribution and direct sale.
The assurance of quality is fundamental in our injection molding services. FirstMold uses a strict quality control process that includes design review, material inspection, in-process monitoring and final inspection to make sure each component is up to the standards stated and your specific requirements. Our ISO-certified processes and skilled quality control team assisted by the most advanced measurement and testing devices produce the defect-free parts that meet your requirements .
ABS material with medium injection speed is better. When the injection molding speed is too fast, the plastic is easy to scorch or decompose and precipitate vaporized products, so that defects such as fusion seam, poor gloss and redness of plastic near the gate appear on the parts. However, in the production of thin-walled and complex parts, it is still necessary to ensure a high enough injection molding speed, otherwise it is difficult to fill.
Advanced testing equipment and scientific product inspection protocols have propelled us to become industry leaders in the POM injection molding field.
The lead time for our injection molding service might vary for more complex projects with a higher volume of parts. Usually most of the projects fall into the range from a few weeks to several months. We give priority to project management and communication for smooth and timely execution of the project. For a better estimate customized to your own personal project, contact our team for more information regarding your specific project.
The confidentiality of FirstMold is beyond any doubt. We guarantee that all our customers sign non-disclosure agreements (NDAs) with us, which will legally protect the confidentiality of the details of your project. We have also developed our internal protocols which are designed to protect the security of your information during the production process.
You need to decide whether injection mold services is a good fit for your business basing on the complexity of the parts you need and the volume too. FirstMold’s injection molding services can be used to produce parts with the required large volume and accurately specified quality and precision. If your project includes complex geometries, high tolerances, and material options from plastic to silicone, we provide value engineering and innovative services.
2. the syringe needle is too high, resulting in local glue bit is too thin, the periphery of the first fill, to the center of the intersection to produce fusion line.
With the detailed mold flow analysis results, the mold making and injection molding will not be much different, saving the production time and reducing the cost of production.
ACIS®, Autodesk Inventor®, CATIA® V5,Creo™ Parametric, IGES, Parasolid®, Pro/ENGINEER®,Siemens PLM Software’s NX™, SolidEdge®, SolidWorks®, STEP
Shrinkage: The shrinkage rate of different sizes of ABS products will be a little different, the common range is 0.4-07%, 0.5% is recommended.
For small quantities, we offer prototype mold solutions or can utilize CNC prototyping for POM material products. For large quantities, we are capable of mass injection molding. No minimum order quantity requirement.
For we know projects may undergo possible changes in requirements. FirstMold is flexible and works the best by aligning with the clients to consider the changes in design or quantity and to minimize the delay and costs. It is important to talk, and we encourage clients to have the discussion as soon as possible regarding changes.
GETTING A QUOTE WITH LK-MOULD IS FREE AND SIMPLE.
FIND MORE OF OUR SERVICES:
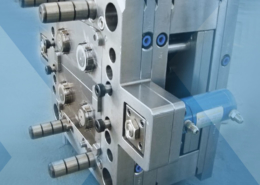
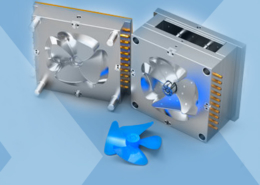
Plastic Molding

Rapid Prototyping
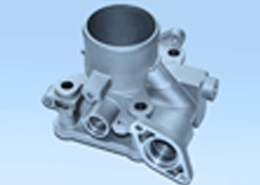
Pressure Die Casting
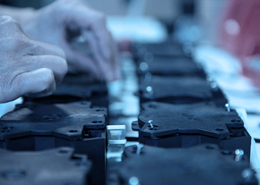
Parts Assembly
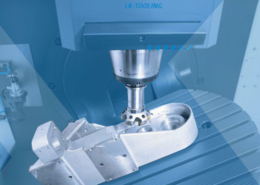