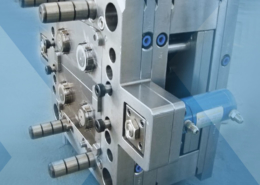
High Impact Polystyrene Injection Molding - CTG, Inc. - polystyrene injection mo
Author:gly Date: 2024-10-15
Quality lies at the core of everything Sussex Injection Molding does, underpinned by rigorous quality assurance processes and stringent adherence to industry standards. From material selection to final inspection, every step of the manufacturing process is meticulously monitored and controlled to uphold the highest standards of quality and consistency. This unwavering commitment to excellence has earned the trust and loyalty of clients across a myriad of industries.
Perforated surfaces that enable the metal to communicate through integrated light controls or sensor technology. When switched off, both the elements and the perforated surface are invisible. Integrated effects such as illuminated icons, logos, symbols or lettering, only become visible in the ‘on’ mode.
In addition, various forms of pre- and post-treatment are possible, for example brushing, grinding, blasting, polishing, special pickling and lasering.
We anodise the surfaces of previously back-moulded metal components in the highest optical and haptic quality, in accordance with your design concepts. To best support you, we have our own anodising plant complete with the following finishing processes:
At the heart of Sussex Injection Molding lies a commitment to leveraging advanced technology to streamline processes and enhance efficiency. The company boasts a comprehensive suite of injection molding machines, ranging from small-tonnage to large-tonnage presses, capable of accommodating a diverse range of production requirements. Additionally, its utilization of automated robotic systems ensures precision and consistency in every molded component, minimizing defects and maximizing productivity.
Please take into account that our production is geared towards medium to large series production. We are therefore unable to process requests for very small quantities for economic reasons.
Our pull-out rails and mechanical and electromechanical hinges bring movement to numerous application areas, for example for the convenient sensor-controlled opening and closing of (oven) doors or refrigerators.
In metal processing, we design and manufacture your required metal mould from sheet material or extruded profiles in medium to large series, finishing them as desired. Our service portfolio ranges from mechanical pre-treatment to anodising and powder coating to various laser, etching and printing technologies.
One of the hallmarks of Sussex Injection Molding is its ability to provide custom solutions tailored to meet the unique needs of each client. Whether it's prototyping, design optimization, or full-scale production, the company works closely with clients to develop bespoke solutions that align with their specifications and objectives. This personalized approach not only fosters strong partnerships but also ensures the delivery of superior-quality products that exceed expectations.
We back-inject metals and metal foils with specific plastics and integrate electronics, lighting elements and/or sensors as desired. Even the anodising of previously back-moulded components is possible. The optimal design of our tools avoids distortion caused by shrinkage and different linear expansions. Products:
Division Surfaces: Company* First and last name* E-Mail* Phone [cf7mls_step cf7mls_step-1 "Next" ""] Street and number ZIP and town Your message [cf7mls_step cf7mls_step-2 "Back" "Next" "Step 2"] Data upload (max. 8 MB, jpg, pdf, png, zip, docx, stp) We process your data exclusively for the purpose of responding to your enquiry. Data protection information Anti-Spam * 5 − 1 = [cf7mls_step cf7mls_step-3 "Back" "Step 3"]
In accordance with the individual requirements of our customers, we develop and manufacture complete products in series as an ODM and OEM device manufacturer and also manage the processes of certification, packaging design and logistics.
Injection molding stands as a cornerstone in the realm of plastic manufacturing, with Sussex Injection Molding emerging as a beacon of innovation and excellence within this domain. Founded in 1977, Sussex Injection Molding has carved a niche for itself by consistently delivering high-quality, precision-engineered plastic components across various industries. This article endeavors to explore the intricate workings of Sussex Injection Molding, shedding light on its processes, capabilities, and contributions to the field of plastic manufacturing.
Sussex Injection Molding traces its roots back to humble beginnings, founded with a vision to revolutionize plastic manufacturing. Established in Sussex, Wisconsin, the company embarked on a journey fueled by a commitment to quality, innovation, and customer satisfaction. Over the years, it has evolved from a modest operation into a state-of-the-art facility equipped with cutting-edge technology and a team of skilled professionals dedicated to pushing the boundaries of possibility.
Assemblies combine individual components, which have different shapes and are made from different materials. These are permanently joined together using appropriate technologies such as laser welding or bonding. Depending on the components and the required joint, this is done manually or using robot-assisted semi- or fully-automatic systems in our plants.
In conclusion, Sussex Injection Molding stands as a testament to the transformative power of innovation and dedication. From its humble beginnings to its status as a trailblazer in the industry, the company exemplifies excellence in every facet of its operations. As it continues to push the boundaries of possibility and redefine the standards of plastic manufacturing, Sussex Injection Molding serves as an inspiration to aspiring entrepreneurs, industry professionals, and environmental advocates alike.
In an era where environmental sustainability is paramount, Sussex Injection Molding stands at the forefront of environmentally conscious manufacturing practices. The company is dedicated to minimizing its ecological footprint by implementing eco-friendly materials, optimizing energy usage, and reducing waste generation. By embracing sustainable solutions, Sussex Injection Molding not only fulfills its corporate responsibility but also sets a precedent for eco-friendly manufacturing practices.
The impact of Sussex Injection Molding extends far beyond the confines of its facilities, reverberating throughout the plastic manufacturing industry. Through its relentless pursuit of innovation and excellence, the company has not only elevated industry standards but also catalyzed advancements in material science, process optimization, and product development. Its contributions have not only reshaped the landscape of plastic manufacturing but also empowered businesses to thrive in an increasingly competitive market.
Looking ahead, Sussex Injection Molding is poised to continue its legacy of innovation and leadership in the plastic manufacturing industry. With a steadfast commitment to technological advancement, customer satisfaction, and environmental sustainability, the company remains primed to tackle the challenges and opportunities that lie on the horizon. By staying true to its core values and embracing emerging trends, Sussex Injection Molding is well-positioned to shape the future of plastic manufacturing for generations to come.
We join components using a wide variety of methods. In bonding, we use liquid adhesives, adhesive tapes and also adhesive die-cuts, which we apply manually or robotically. Optionally, different types of pre-treatment are possible, including plasma, primer, scarfing or pyrosil as well as different rapid curing methods (UV light, infrared, heat radiation).
GETTING A QUOTE WITH LK-MOULD IS FREE AND SIMPLE.
FIND MORE OF OUR SERVICES:
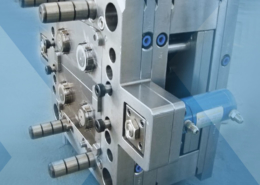
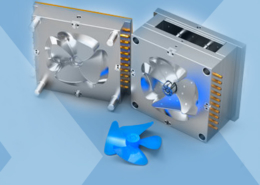
Plastic Molding

Rapid Prototyping
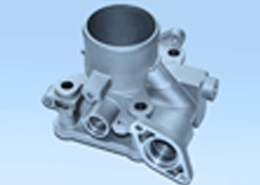
Pressure Die Casting
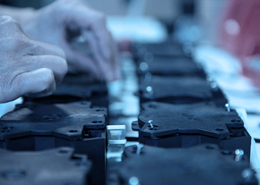
Parts Assembly
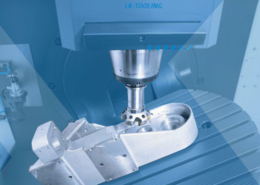