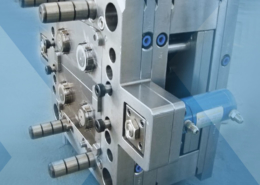
High Impact Polystyrene Injection Molding - CTG, Inc. - polystyrene injection mo
Author:gly Date: 2024-10-15
After cooling, the mold opens, and the newly formed plastic part is ejected. Depending on the complexity of the part and the requirements of the project, secondary operations such as trimming, machining, or assembly may be performed to achieve the final desired product.
By leveraging their accumulated experience and expertise over many years, they strive to provide superior quality products based on high-end technology while continuously investing in new technologies to stay ahead of the competition.
Consider the material requirements for your parts. Both low volume injection molding and thermoforming offer versatility in material selection, with a wide range of thermoplastic resins available. Evaluate factors such as material properties, performance requirements, and cost to determine the most suitable material for your application.
Japan is home to some of the world’s most innovative and advanced injection molding companies. These top 10 Japanese firms are renowned for their highly-precise manufacturing processes, cutting-edge technology, and unparalleled expertise in plastics production.
Navigating the realm of manufacturing processes can be a daunting task, especially when considering options like low volume injection molding or thermoforming. At Advanced Plastiform Inc., we understand the critical importance of choosing the right method for your project.
The low volume injection molding process begins with the creation of a custom-designed injection mold. The mold is then mounted onto an injection molding machine, where thermoplastic pellets are fed into a heated barrel within the machine, where they are melted to a liquid state. The molten plastic is then injected under high pressure into the mold cavity, conforming to its shape and intricacies.
FUJIGOUSEI Inc. has been producing precision plastic molded parts since 1941, providing reliable products that meet current societal expectations.
They also believe in providing individualized solutions for each customer, allowing them to find the most effective strategies for their specific needs. Additionally, they are continuously pushing the boundaries of technology to bring more value to their customers and the industry.
Moreover, they have extensive experience with nylon resin and hearable and malleable resins. All these features make Matex Co., Ltd. a reliable partner to provide high-quality products while meeting all the customer’s requirements on time.
Compare the tooling costs and lead times associated with each method. Low volume injection molding typically requires the fabrication of aluminum molds, which offer cost savings and shorter lead times compared to steel molds used in traditional injection molding. Thermoforming molds are also cost-effective and can be fabricated more swiftly due to their single-sided design and lightweight materials.
These injection molding manufacturers in Japan are committed to providing excellent customer service with outstanding customer satisfaction. They continue to innovate and develop cutting-edge technologies to help them remain at the forefront of this growing sector.
Low volume injection molding, also known as "short-run manufacturing," serves as the vital bridge between product prototyping and high-volume production, catering to orders typically fewer than 10,000 pieces.
Their expertise is evident in their use of advanced technologies as well as their own unique production system. They are also committed to supplying products with higher value added to customers worldwide, creating innovative solutions to meet their needs.
Matex Co., Ltd. has been a leader in designing and manufacturing planetary gears, gearboxes, and transmissions for many years. They have many achievements in developing custom solutions for appliances, machinery, automobile parts, and health equipment.
Choosing between low volume injection molding or thermoforming methods requires careful consideration of various factors to ensure the optimal manufacturing solution for your specific project requirements.
Get started today by receiving a free quote tailored to your project for plastic parts and products. Contact us now by calling us at 919-404-2080 or filling out the online contact form. Don't delay—unlock the potential of custom plastics manufacturing with us today.
Consider the anticipated production volume for your project. Low volume injection molding is typically suited for production runs of fewer than 10,000 pieces, making it ideal for smaller quantities. Thermoforming, on the other hand, offers flexibility for both low to mid-volume production runs, with the ability to scale up or down as needed.
They are constantly adapting to the changing technology and investing in training their younger members with the latest technological advancements.
Take into account the size and weight of the parts you need to produce. Thermoforming is well-suited for forming large parts with minimal material thinning, making it ideal for applications requiring lightweight yet durable components. Low volume injection molding can also accommodate a range of part sizes but may be more suitable for smaller, more intricate parts.
Whether you need 1,000 or 100,000 custom plastic components, the thermoforming experts at Advanced Plastiform Inc. will work with you to determine the best method of manufacturing to provide you with the durable, high-quality plastics you need. This includes prioritizing a low per-unit price with as quick a lead time as possible.
Consider your project timeline and production speed requirements. Thermoforming typically offers faster lead times and shorter production cycles compared to low volume injection molding, making it a preferred choice for rapid prototyping and quick-turn projects. However, if precision and tight tolerances are critical, low volume injection molding may be the better option despite longer lead times.
These businesses offer various services, from small-scale operations to more significant industrial makers, including component design, tool production, quality control, and molding services. With years of experience and expertise, these Japanese companies have become leaders in the injection molding industry.
Vacuum forming involves suctioning out the air between the plastic sheet and the tool to ensure a snug fit, ideal for larger pieces with less intricate details. Conversely, pressure forming utilizes highly pressurized air to blast the plastic sheet while simultaneously applying vacuum suction, allowing for sharper angles and finer details, making it a compelling alternative to injection molding.
Traditional plastic injection molding is renowned for its high-volume manufacture but entails significant upfront costs, primarily due to tooling expenses. Injection molds, usually crafted from steel or copper alloy, endure the intense pressures of the injection process, necessitating intricate and heavyweight designs, thereby escalating fabrication costs and lead times.
They also employ advanced technologies such as robotics, 3D printing, and Automated Visual Inspection (AVI) to ensure maximum efficiency in the manufacturing process.
Japan is one of the leading countries in injection molding technology. Its top 10 injection molding companies are some of the most respected and innovative in the industry.
Advantages: They continuously update their equipment, have cultivated expert skills through years of experience, and strive for absolute “quality”, “speed”, and “global perspective” when creating products. This makes them an ideal partner for customers seeking reliable and trustworthy services.
We proudly serve the Mid-Atlantic and Southeast, including North Carolina, South Carolina, Pennsylvania, Maryland, Tennessee, Georgia, and Virginia.
Over the years, they have become an integrated manufacturer of injection molding (mainly medical device parts), and medical products (original and OEM). They are ISO 9001 and ISO 13485 certified, which stresses their commitment to quality control and management to meet international standards.
Tanaka Die & Mold Works Co., Ltd. was founded in 1967 and has provided customers with high-quality, precise plastic mold manufacturing.
With a strong background in producing quality plastic molded products, Shinwakogyo Co., Ltd. is well-equipped to meet the demanding needs of customers in the pharmaceutical and medical device industries.
With a global outlook and presence, FUJIGOUSEI Inc. is well-equipped to remain at the forefront of the industry for many years.
Thermoforming is a versatile manufacturing process involving the heating of large plastic sheets until pliable, which are then shaped around a custom-fabricated aluminum tool.
With a team of highly experienced professionals in the plastic industry, they have gained the trust of customers from around the globe.
The Yasuda Mold Manufacturing Co., Ltd. Has a long history of faithful growth with the Japanese economy since the postwar era. They have developed into an international supplier of quality molds, working hard to meet tight deadlines, cost, and quality standards.
These companies offer a wide range of services, from design to production and quality assurance, ensuring that their customers receive high-quality products.
NISSEI PLASTIC INDUSTRIAL CO., LTD’s experience allows them to develop innovative processes and technologies that maximize customer efficiency and quality.
Evaluate the complexity of the parts you need to manufacture. Low volume injection molding excels in producing parts with intricate details, tight tolerances, and complex geometries, making it suitable for applications requiring high precision. Thermoforming is better suited for larger parts with simpler geometries, although pressure forming techniques can achieve finer details compared to traditional vacuum forming.
By leveraging its deep knowledge base of accumulated skill and knowledge, Shibaura can offer top-notch customer service and products that meet customer expectations.
Their team of experts in mechatronics engineering, machine design, and research and development is dedicated to finding the best solutions for each customer’s needs.
Their capabilities include contracted development and manufacturing mechanical components such as actuators, power units, pumps, and plastic injection molding and assembly.
In contrast, low volume injection molding often employs aluminum molds, operating at lower pressures to safeguard against mold damage. This strategic choice significantly reduces tooling costs by 5 to 25 percent, with aluminum's malleability facilitating quicker mold creation, thereby expediting the overall injection molding process timeline.
Thermoforming boasts several advantages that make it an attractive plastic manufacturing method for low- to mid-volume production:
Low volume injection molding finds application across a wide range of industries where precision, flexibility, and cost-effectiveness are paramount. Some of the key industries utilizing low volume injection molding include medical, telecommunications, consumer packaging, and more.
This approach not only reduces initial investment but also enhances the overall flexibility and scalability of the thermoforming process, making it well-suited for low to mid-volume production runs.
Juken Kogyo Co., Ltd. has been a leader in plastic injection molding since its establishment in 1965. They have continuously developed new technologies and applications for their manufacturing processes, building on the state-of-the-art technology of the time.
With a commitment to precision, efficiency, and cost-effectiveness, our injection molding company specializes in providing comprehensive solutions tailored to your unique plastic part needs. Whether you're aiming for intricate details with low volume injection molding or seeking the versatility of thermoforming, our expertise ensures that you can make informed decisions to propel your project forward with confidence.
Additionally, Shinwakogyo is one of the few plastic molding manufacturers that have acquired ISO13485 certification in Japan, making them an ideal choice for customers seeking reliable, high-quality products.
Low volume injection molding offers several distinct advantages that make it a preferred choice for small to medium-sized production runs:
With their motto of “Going Specific, Deeper, and Unlimited”, they have been continuously researching and developing state-of-the-art injection molding machines, molds, molding support systems, and mold processing technologies.
Furthermore, Tsutawa’s commitment to globalization is evident from its overseas affiliates in Hong Kong. Their high-quality products and professional customer service have enabled them to become one of the most trusted names in the plastic machine industry.
They specialize in mold design/manufacture, molding/assembly, and coating these parts for use in various industries such as communication, electronics, medical care, and automobiles.
Advanced Plastiform offers guidance on the optimal manufacturing process to maximize efficiency and cost-effectiveness for low run, plastic parts.
They have established a system of long-term results and experience-gained perception that ensures their success despite rapid technological development. With an efficient, focused team, they provide excellent results and knowledge that is highly valued in the industry.
In addition, Shibaura works closely with customers through every stage of their projects to ensure that the machines they create are optimized for maximum efficiency and productivity.
Twin sheet forming is an advanced technique where two plastic sheets are heated simultaneously and formed together to create a hollow, double-walled structure, offering enhanced strength, insulation, and structural integrity for applications such as automotive components, farming equipment, outdoor furniture, and more.
Thermoforming often utilizes lightweight aluminum molds, minimizing both tooling costs and lead times. Thermoforming molds are typically single-sided and can be fabricated more swiftly due to the material's malleability, making it an efficient and cost-effective alternative to traditional injection molding.
Since 1988, Advanced Plastiform, Inc., has been providing superior custom plastic molding and fabrication services to companies in North Carolina, South Carolina, Maryland, Georgia and Pennsylvania. Contact us to make an appointment Mon-Fri 8-5.
Their Juken System can produce reliable micro parts for consumer electronics, cameras, watches, and automobile parts with precision and efficiency. Juken Kogyo Co., Ltd. boasts a wealth of experience in plastic injection molding that goes back over 50 years.
With multiple state-of-the-art facilities throughout Japan and global expansion initiatives, Shibaura provides customers with unbeatable quality and reliability.
In addition, they strive to bring Made in Japan quality to the world’s markets, assuring customers that their products are safe, effective, and comply with all applicable laws and regulations.
Yasui Co., Ltd. has a long and illustrious history, tracing its origins back to 1930 in Osaka when it began as a printing company.
GETTING A QUOTE WITH LK-MOULD IS FREE AND SIMPLE.
FIND MORE OF OUR SERVICES:
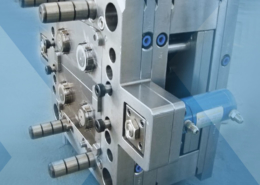
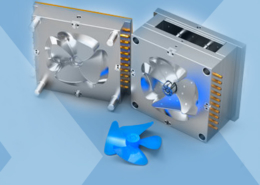
Plastic Molding

Rapid Prototyping
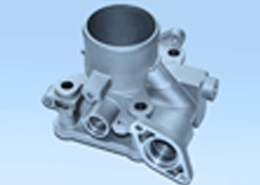
Pressure Die Casting
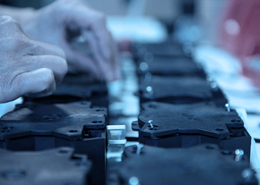
Parts Assembly
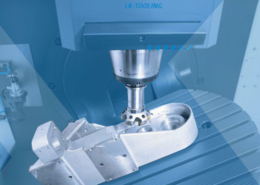