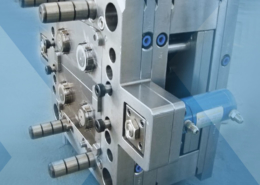
Ford has a McDonald's caffeine fix for plastic parts - mcdonalds plastic molding
Author:gly Date: 2024-10-15
Since you’re well aware of everything about the plastic injection molding equipment, the types of plastics used in the process, and the characteristics of the mold used during a plastic injection molding service, it’s time to explore the products that are manufactured through this standard and highly trusted process and their applications.
Custom plastic injection molding is the best way to make a large number of different plastic parts quickly and with good results. Since this manufacturing process can make complex plastic parts, it is the most common process that is highly trusted by many different industries. Compared to other manufacturing solutions, it is also a reliable and cheaper way to manufacture plastic products. But are the benefits of plastic injection molding services just as substantial as their process and product outcomes? Definitely! Here are a few of the most common benefits of plastic injection molding you can consider:
This type of plastic employed in the plastic injection molding process belongs to the thermoplastic family. Having said that, it is one of the two most prominent types of materials that manufacturers most frequently choose for plastic injection molding.
Yes, we offer a production tooling option called on-demand manufacturing. This tooling option provides several benefits: lower piece part price, multi-cavity capabilities, guaranteed tooling for the life of the project (we will cut a new tool if it wears out), and first article inspections.
For a more precise idea, below are the characteristics of a plastic injection mold that should be considered for attaining quality outcomes through the plastic injection molding process.
The plastic injection molding process’s efficiency and speed are the most substantial advantages over other production methods. Because of this, they can create the bulk of material quickly. As a result, plastic injection molding service produces high-complexity plastic and larger molds in approx. 15-120 seconds.
Proto Labs, Inc. 5540 Pioneer Creek Dr. Maple Plain, MN 55359 United States P: 877-479-3680 F: 763-479-2679 E: [email protected]
No Minimum Order Quantities (MOQs)Procuring parts on demand, without MOQs, helps you manage market or demand volatility and provides a cost-effective source for bridge production, line-down emergencies, end-of-life production, or product customization.
There is a wide array of equipment involved in the injection molding process. And when it comes to injection molding, whether it is of plastic or metal, the types of equipment used in this process are pretty similar. However, if any of the essential equipment isn’t present, it can be said that the plastic injection molding processing may not proceed efficiently and produce the ideal plastic product that you need. Needless to say that professional injection molding service-providing companies do comprise all the essential types of equipment for handling the production process as per your demands.
Get machined parts anodized and chromate plated with our quick-turn finishing option. Eligible materials include aluminum 6061/6082 and 7075.
That’s all to the detailed guidelines on the basics, usage, and advantages of a plastic injection molding process. If you have any further queries, we are always available to help you out.
Above all, injection molding machine usage is also cost-effective. From assembly through finishing, every phase keeps costs down and boosts efficiency.
6. Finally, the rear half of the mold base contains the ejection system and a support plate. Here, the ejector bar activates the ejection system, whereas the clamping unit separates mold halves. Apart from this, the mold channels are also injection molding equipment that allows molten plastic to flow into mold cavities.
With the vast amount of beneficial properties of plastic, the usage of plastic in different industries is widespread today. Every other product we use or see around us is made of plastic. But did you know that there is not one but a total of 7 plastic types that are commonly used in the production processes of different products nowadays?
Unmatched Lead TimesReduce your product development cycle by weeks—sometimes months—and bridge to production with injection-molded parts within days. Some injection molding orders can ship in as fast as 1 day.
Design for Manufacturing FeedbackEvery quote includes real-time pricing and design analysis. We evaluate your 3D CAD and help identify any features that may pose challenges during the molding process such as difficult to machine undercuts and insufficient draft.
3. As the plastic injection mold and molding equipment, additional molds are constructed with steel or aluminum. The mold comprises numerous components but may be divided in half. Each half is joined within the plastic injection molding machine, and the rear half is left to slide so that the mold can be opened and closed along the parting line. Additionally, the mold’s two primary components are the mold core and the mold cavity.
In most cases, we can maintain a machining tolerance of +/- 0.003 in. (0.08mm) with an included resin tolerance that can be greater than but no less than +/- 0.002 in./in. (0.002mm/mm).
Lastly, nylon is the fourth type of plastic that is frequently selected for custom plastic injection molding. Nylon, or, to be more specific, polyamide, is known to be an extremely tough semi-crystalline plastic. As per the chemical features of this plastic, it comes from a group of robust materials with exceptional thermal qualities.
As complicated as it may appear to the average customer, plastic injection molding processing is a typical manufacturing technique used to make a wide range of commonplace objects. Various plastic injection molding companies like Prototool offer this service to assist in the manufacturing of plastic objects that have become a part of our daily lives, regardless of their complexity, craftsmanship, size, or dimensions.
Overmolding and insert molding are two-part injection molding processes where one material is overlaid onto a second substrate part or metal insert to create a single component.
Injection molding is plastic manufacturing process that can produce high quality parts at scale. It's typically used for low- to high-volume production but our aluminum tooling can also make prototyping runs economical.
Injection molding is widely used for plastic part production in medical, consumer, and automotive industries. Typical parts include:
Now for anyone opting to invest in such a service without any know-how about plastic injection molding, this detailed guide will enlighten you with all the essential details. So without further ado, let’s dive into the details of this efficient manufacturing process.
5. The mold base is also considered an injection molding equipment that serves as a mounting point for the plastic mold core and cavity.
Nave ISK-8, Parque Industrial y Logístico Sky Plus, Avenida Mineral de Cinco Señores No.100, del Parque Industrial Santa Fe, Silao de la Victoria, Guanajuato, México
Injection Molding ExpertiseWe'll work with you throughout the course of your project to help you quickly move from prototyping to production, including finishing options and inspection reporting.
Our digital factories create prototypes and low-volume parts fast, while our manufacturing network, offers advanced capabilities and volume pricing.
Because of the initial capital investment in tooling, injection molding makes sense for higher volumes of parts. Our mold cost starts at $1,495 and will vary depending on part geometry and complexity. Other factors that will impact injection molding cost are lead times and material.
Aluminum moldsStandard lead times as fast as 7 daysTolerances of +/-0.003 in. plus resin tolerance (in./in.)Set-up fees apply to each run Consultative Design Services (CDS)Finishing OptionsNo minimum order quantities (MOQ)Quick-turn shipping in as fast as 1 day
No one ever said that designing and manufacturing molded parts was easy. Our goal is to get you through it quickly and with quality parts. A good starting point is our Design for Moldability Toolkit.
4. When this injection molding equipment is closed, the space between the mold core and mold cavity becomes the part cavity, which is then filled with molten plastic to produce the desired component.
We have two unique offers to meet your needs wherever you are in the product lifecycle. Our prototype injection molding process helps you cut product development cycles by weeks—sometimes months—and bridge to production with injection-molded parts within days. Our On-demand Manufacturing process is designed to meet your production needs, and helps you qualify parts quickly to seamlessly transition into production with scientific molding, in-process CMM inspections with GD&T, and a full suite of secondary operations to make sure that your parts show up and perform as expected.
We combine scientific (or decoupled) molding techniques, which optimize and lock in processing parameters to ensure part consistency—with extra attention paid to critical-to-quality dimensions using our proprietary automated CMM process. Plus, with every order you'll get:
The processing of a plastic injection molding machine begins with the injection of plastic into the mold, followed by continuous rotation and heating along the two vertical axes. Under the influence of gravity and heat, the plastic in the injection mold is uniformly covered, melted, and attached to the whole cavity surface. Eventually, the desired plastic shape is then obtained by cooling and setting the material.
1. The injection unit is one of the injection molding equipment. This injection molding device heats and injects the injection molding material into the mold.
Speaking of which, when we talk about plastic injection molding processing, the type of plastic used in this process can also vary from usage to usage and the type/shape of the product you plan to manufacture in the end. Likewise, depending on the type of plastic you use, the processing method and the product’s end result also differ. Below are a few of the most standard types of plastics that are used in plastic injection molding:
This complete reference guide walks you through everything from quoting, design analysis, and shipment to best practices that ensure your model is optimized for molding.
Make the move from prototyping to on-demand manufacturing for affordable, high-quality molded parts within days. Better yet, your prototyping tool is free once you shift to an on-demand manufacturing tool. Working with a single supplier that provides free design consultation services also massively speeds up the manufacturing process, allowing for greater supply chain flexibility, more consistent parts, and making qualification a breeze.
We do quoting a little differently. When you request an injection molding quote, you'll not only receive accurate pricing, but also a manufacturing analysis—within just a few hours. Our online quoting platform also provides you with gate and ejector pin layouts and a price curve tool to help select the best tooling option for your project.
We can also use the plastic injection molding process to build intricate pieces. Significantly, the high pressure incorporated in the plastic injection molding machine helps create complex structures.
2. Second on the list is the clamping unit, which is another piece of injection molding equipment. Before injecting molten plastic into the plastic mold to proceed with the plastic injection molding process, the clamping device must first securely close the two parts of the mold.
Our helpful design aid demonstrates part features that are too thin or too thick, bad bosses, right and wrong ribs, and other considerations to be mindful of while designing parts for injection molding.
Polycarbonates are the best and most popular alternatives when it comes to the most mechanically resistant plastics utilized in the plastic injection molding process. This feature distinguishes this particular type of plastic material utilized in plastic injection molding machines. In addition, it also offers extensive transparency and resistance to impact, electricity, and heat.
Plastic injection molding is a manufacturing process where resin in a barrel is heated to a molten state, then shot into a mold to form a final production-grade thermoplastic part.
Third, polypropylene is arguably the most prevalent form of plastic utilized by plastic injection molding companies – used in items ranging from manufacturing fibers to consumer goods. It is also effective in the production of food and cosmetics packaging, like ice cream packets, ketchup, condiments, shampoos, conditioners, drinking straws, etc.
Liquid silicone rubber molding is a thermoset process that mixes a two-component compound together, which is then heat cured in the mold with a platinum catalyst to produce a final part.
Tough Black (Loctite Henkel 3843) and Ceramic-Filled (BASF 3280) are two new advanced photopolymer materials now available for 3D printing.
We have wide selection of more than 100 thermoplastic and thermoset materials. And if you're looking for alternative material options, check out our guide to resin substitutes for ABS, PC, PP, and other commonly molded plastics.
GETTING A QUOTE WITH LK-MOULD IS FREE AND SIMPLE.
FIND MORE OF OUR SERVICES:
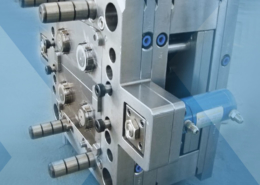
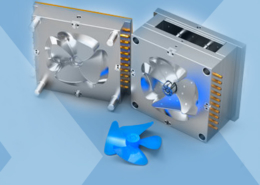
Plastic Molding

Rapid Prototyping
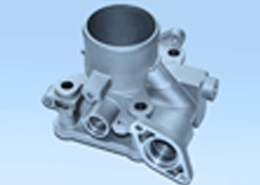
Pressure Die Casting
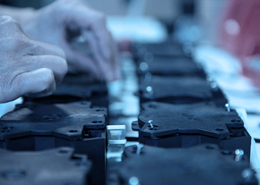
Parts Assembly
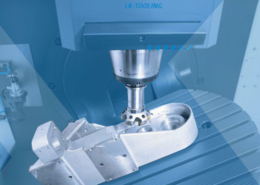