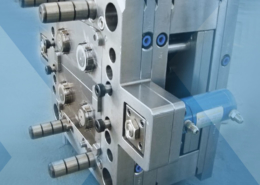
Ford has a McDonald's caffeine fix for plastic parts - mcdonalds plastic molding
Author:gly Date: 2024-10-15
An off-the-shelf product isn’t always best for every application. When you have a complex challenge to overcome, Component Plastics is here to help. Our team can work with you to understand the application and its intended operating environment. From there, we can collaborate on a prototype for testing and validation. Once the final design is acceptable, full-scale production kicks off. Finding a partner to provide injection-molded components reliably may sound challenging, but it doesn’t have to be. As a leading manufacturer of injection-molded ABS parts, we can take your design from print to production quickly and affordably. Our capabilities include:
Some other common materials used for injection molding include polycarbonate, nylon, acrylic, and polyoxymethylene. Each of these materials have their advantages and disadvantages, which is why, when determining which material to work with, you need to think of how the final product will be used. Will it need to be food-safe? Does it need to be heat tolerant? UV resistant? These are some of the things you need to consider before deciding which material to use.
I’m making plastic pliers. mostly needle nose pliers. What material should I use, I don’t need strong heat or chemical resistance in the material used. They should not generate static charges, but they should be electrically non conductive.
After 50 years of servicing the filter molding niche, Component Plastics, Inc. is proud to be one of the leading providers of insert injection molding
Each member of CPI’s team focuses on turning your needs into reality — from their friendly customer service agents to their expert team of engineers. Whether you need a large-scale project or quick delivery turnarounds, CPI is ready to satisfy all your ABS plastics needs, so contact them today.
In addition to our injection molding prototyping and production capabilities, Component Plastics is happy to offer a variety of services designed to bring value to your supply chain. We perform the following operations. Finding the material needed to bring your plastic part design to market can take away from your core goals. Instead, just pass that duty onto us. Our team is happy to acquire the material for your project and turn it into the finished product on your behalf.
You are currently using Internet Explorer 7/8/9, which is not supported by our site. For the best experience, please use one of the latest browsers.
Precision plastic components turned around fast. We’re a leading provider of custom injection molding services to clients worldwide.
These three thermoplastic materials are used all the time. They are cost-effective, durable, and can tolerate the stresses of constant use. You likely use products made from these three materials often, if not every day. For example, ABS is the thermoplastic used to make your keyboard and parts of your phone.
Here is a table of the most common thermoplastic materials used for injection molding with their unique features and most common applications.
CPI has always taken pride in being able to provide the customer with one of the best one-stop shops in the area and can handle any logistic needs with experience shipping to numerous foreign destinations.
Amorphous materials shrink or expand less when heated or cooled because they don’t have a sharp melting point, making the process more forgiving and gradual. Unlike amorphous plastics, semi-crystalline plastics have a much sharper melting point and are known to expand or contract a great deal more when exposed to changing temperature extremes.
Choosing the right material for your project will help to streamline the process, improve your product’s performance, and reduce costs.
As a thermoplastic, ABS can be melted down and reformed or recycled. This trait makes it perfect for companies looking to highlight sustainable practices.
Once you know which material to use, you will be able to decide which material is best for your project. Specifically, you will need to choose between an amorphous plastic or a semi-crystalline plastic. The main difference between these two families of plastics is how they react to heat.
ABS (acrylonitrile butadiene styrene) plastic is one of the most commonly used polymers in injection molding due to its relatively low cost and high durability. The styrene gives the material a shiny, resistant surface, while the polybutadiene makes it extra tough even at the lowest temperatures.
At Component Plastics, client satisfaction is our utmost priority. When you partner with us, you’ll get quality injection-molded ABS components delivered on time and within budget. Even more, you’ll get unwavering customer service. This dedication has enabled us to become the trusted injection-molded ABS parts provider for clients in many industries.
ABS plastic is ideal for making lightweight molded products at competitive prices, and CPI can service any of your demands, as they collaborate with many different industries for myriad applications, such as:
The application of the product will determine the material used. If a product needs to be transparent yet still durable, like an automobile headlight, polycarbonate would be a good choice. What if your product is a container, like a milk jug? Then polyethylene is the type of material you’ll want to use. Polyethylene is often used for food packaging because it is food safe and won’t leach chemicals.
Do you need design-for-manufacturing (DFM) assistance? Or, are you ready for production? We have a full suite of services to offer and a lifetime mold guarantee.
Get in touch with the CPI team. We are located in Elgin, IL, and provide top-tier injection and plastic molding services to a variety of industries.
The blog “Materials Used in Injection Molding” provides a comprehensive overview of the various materials suitable for injection molding processes. The author effectively discusses the properties and applications of common plastics, such as ABS, polypropylene, and polycarbonate, highlighting their strengths and limitations. This information is crucial for professionals in the industry who need to make informed decisions about material selection for specific applications. Thank you for sharing this valuable resource, and I look forward to more informative posts that delve deeper into material science and its impact on manufacturing!
As a premier injection molding service provider, we can deliver the filtration solutions you need on time and at a competitive price.
For an easily formable and machinable food-safe thermoplastic material that doesn’t break the bank, a top choice is acrylonitrile butadiene styrene. Improve your application with injection-molded parts comprised of this polymer by Component Plastics.
ABS is naturally translucent but can be pigmented to display almost any color. It stays hard, rigid, and tough – even at low temperatures – and is available in fire-retardant and heat-resistant grades. As a result, the material is perfect for food processing and storage uses. Other applications include:
Acrylonitrile butadiene styrene, or ABS, is a thermoplastic polymer renowned for its ability to stand up to impact forces, corrosion, and chemical exposure at an affordable price point. Other benefits of this material include:
Materials used in injection molding are plastics, specifically thermoplastics. There are hundreds of thermoplastics, but the most common thermoplastics used in injection molding are:
Component Plastics Inc., an IATF Certified facility, has been one of the top suppliers of filter and injection molding products throughout the nation and abroad since 1969 and is happy to be serving its first-ever customer to this day. Thanks to decades of experience in the industry, CPI specializes in manufacturing products from all types of materials like ABS plastic.
Thermoplastics are plastics that melt when heated and make plastic injection molding possible. Most of the plastic products used today are created using thermoplastics because of how diverse this material is. Some thermoplastics are very sturdy and rigid, while others are flexible and rubber-like. Some are clear and others are opaque. It is this diversity that makes thermoplastics such an appealing material for manufacturers.
GETTING A QUOTE WITH LK-MOULD IS FREE AND SIMPLE.
FIND MORE OF OUR SERVICES:
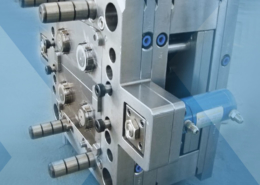
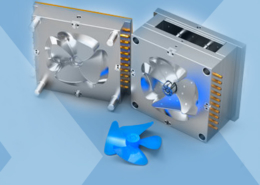
Plastic Molding

Rapid Prototyping
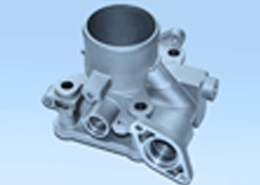
Pressure Die Casting
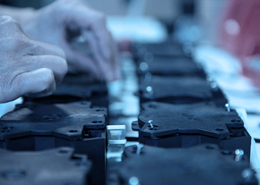
Parts Assembly
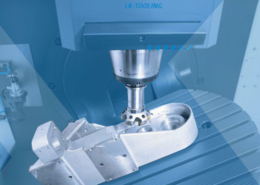