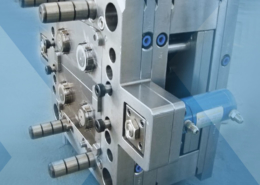
Do-It Essentials Injection Molds for Pouring Soft Baits - soft plastic injection
Author:gly Date: 2024-10-15
When it comes to cold runner molds, the most widely used diameters lie between 4-7 mm and the application of full round sprues and runners. The diameters of a pin gate are set between 0.7-1.5 mm. The depth of edge gating is kept no lower than half of the thickness of the wall.
If combined with other materials such as rubber, polypropylene can create an even stronger co-polymer. It is a customizable plastic used for manufacturing food containers since it does not contain BPA (Bisphenol A), a synthetic compound unsafe for human consumption. With so many versatile applications, PP is well-suited to a broad range of product types including furniture molding, ropes, tape, carpets, camping equipment, twine, upholstery, and so on.
PP is used extensively in household and industrial applications because of its unique properties and ability to adapt to various fabrication techniques. It can function both as a molded plastic furniture and as fiber. One can manufacture it through different methods for various applications.
Polypropylene is typically used by mold makers in refrigerators, housing appliances, hairdryers, lawnmowers, blenders, and automotive appliances (glove compartment doors, interior trim panels, mirror housing, etc), typewriters, etc. For processing it, drying is required for a minimum of 2 hours between 80-90 degrees Celsius and the moisture content should be less than 0.1%.
The chemical formula of pp is (C3H6)n, the density is 0.89~0.91g/cm3, flammable, melting point is 164~170℃, soften around 155℃, the use of temperature range of -30~140℃.
Polypropylene can be produced in both transparent as well as opaque forms. It is useful in applications where the transfer of light is vital or where it contributes to aesthetic value. If high transmissivity is required, plastics such as acrylic and polycarbonate are preferred.
Since polypropylene has high resistance to electricity, it is useful in electrical appliances like automotive plastic components. Because of its ordered molecular structure, PP is semi-crystalline. It results in PP’s stiffer and higher melting temperature compared to PE.
Polypropylene can retain its shape even after a lot of torsions, bending, and flexing. It makes for an ideal choice in making living hinges. It is not prone to stress cracking and can adjust by adding mineral fillers, glass fibers, or thermoplastic rubbers. Moreover, its flow rate ranges between 1-40 which offers better resistance to impact but lower tensile strength.
Polypropylene, abbreviated as PP, is a polymer made from propylene through the polymerization reaction. It is a thermoplastic synthetic resin with excellent performance, and is a colorless, semi-transparent thermoplastic lightweight general-purpose plastic.
Polypropylene is known for its sturdy yet elastic consistency. It acts with elasticity over a range of deflection but also experiences deformation early in the process. This property makes it a durable material which implies that it can deform without breaking.
Despite its weaknesses, PP is still the perfect injection molding material because it has some unique qualities you cannot find in any other material. All these advantages make PP an ideal choice for an extensive range of application projects.
PP injection molding material is strongly resistant to moisture and chemicals like acids, alkalis, and solvents. But it does not offer resistance to aromatic and chlorinated hydrocarbons. And under high temperatures, its oxidation resistance is not as strong as that of PE plastic.
The reason behind its popularity is its durable yet flexible texture which gives any material made out of it strong resistance to fatigue and chemical corrosion. It is a very useful injection molding material typically available in the form of pellets for this purpose.
There are several reasons why polypropylene injection molding is popular as the most efficient form of molding. It is ideal for the consistent and affordable production of a wide range of high-quality plastic components that can withstand any environment.
If combined with other materials such as rubber, polypropylene can create an even stronger co-polymer. It is a customizable plastic used for manufacturing food containers since it does not contain BPA (Bisphenol A), a synthetic compound unsafe for human consumption. With so many versatile applications, PP is well-suited to a broad range of product types including furniture molding, ropes, tape, carpets, camping equipment, twine, upholstery, and so on.
As diluted bases and acids don’t react readily with polypropylene, it is the first choice of the manufacturers in making liquid containers. The material can manufacture the packaging containers of first-aid products, cleaning agents, warehouse plastic box mould, etc.
It is resistant to corrosion by acid, alkali, salt liquid and many kinds of organic solvents below 80℃, and can be decomposed under high temperature and oxidation.
Polypropylene can be produced in both transparent as well as opaque forms. It is useful in applications where the transfer of light is vital or where it contributes to aesthetic value. If high transmissivity is required, plastics such as acrylic and polycarbonate are preferred.
Polypropylene can retain its shape even after a lot of torsions, bending, and flexing. It makes for an ideal choice in making living hinges. It is not prone to stress cracking and can adjust by adding mineral fillers, glass fibers, or thermoplastic rubbers. Moreover, its flow rate ranges between 1-40 which offers better resistance to impact but lower tensile strength.
PP is used extensively in household and industrial applications because of its unique properties and ability to adapt to various fabrication techniques. It can function both as a molded plastic furniture and as fiber. One can manufacture it through different methods for various applications.
Compared to other plastics, Polypropylene has a relatively lower density. It results in weight reductions for the producers and sellers of injection-molded products. Because of these reasons, PP can manufacture several applications such as food trays, cups, plates, and toys.
Polypropylene is typically used by mold makers in refrigerators, housing appliances, hairdryers, lawnmowers, blenders, and automotive appliances (glove compartment doors, interior trim panels, mirror housing, etc), typewriters, etc. For processing it, drying is required for a minimum of 2 hours between 80-90 degrees Celsius and the moisture content should be less than 0.1%.
The reason behind its popularity is its durable yet flexible texture which gives any material made out of it strong resistance to fatigue and chemical corrosion. It is a very useful injection molding material typically available in the form of pellets for this purpose.
When it comes to cold runner molds, the most widely used diameters lie between 4-7 mm and the application of full round sprues and runners. The diameters of a pin gate are set between 0.7-1.5 mm. The depth of edge gating is kept no lower than half of the thickness of the wall.
ACIS®, Autodesk Inventor®, CATIA® V5,Creo™ Parametric, IGES, Parasolid®, Pro/ENGINEER®,Siemens PLM Software’s NX™, SolidEdge®, SolidWorks®, STEP
It is resistant to corrosion by acid, alkali, salt liquid and many kinds of organic solvents below 80℃, and can be decomposed under high temperature and oxidation.
Polypropylene is a plastic polymer known for its sturdy consistency. Businesses around the world use this material for manufacturing storage containers such as water bottles and plastic boxes. The material is useful in manufacturing plastic storage containers, kitchenware, piping systems, medical components, outdoor furniture, plastic bucket mold, plastic toy mold, luggage, and even insulation systems.
Despite its weaknesses, PP is still the perfect injection molding material because it has some unique qualities you cannot find in any other material. All these advantages make PP an ideal choice for an extensive range of application projects.
But with advantages come disadvantages as well. Due to the slippery surface of the PP injection mold design, it cannot adhere to the surface of other materials. During times when it is required to form a joint, PP needs welding. This property makes it a substitute for plastics such as Acetal (POM) in low friction applications like gears or as a contact point for furniture.
Though PP is slippery at the molecular level, it has a relatively high friction coefficient and acts as a contact point for furniture. As a result, POM, PTFE, or Nylon are perfect for this purpose.
For custom plastic 3D printing, a fast speed is adopted. It keeps the internal stress at a minimum level. In the case of surface defects, a slower speed is preferred at higher temperatures. That is why machines providing profiled speed are used.
It is a colorless, semi-transparent thermoplastic lightweight general-purpose plastic. Polypropylene pellets are generally melted and injection-molded, and are widely used in plastic products, packaging, and automotive parts.
Polypropylene is a plastic polymer known for its sturdy consistency. Businesses around the world use this material for manufacturing storage containers such as water bottles and plastic boxes. The material is useful in manufacturing plastic storage containers, kitchenware, piping systems, medical components, outdoor furniture, plastic bucket mold, plastic toy mold, luggage, and even insulation systems.
Since polypropylene has high resistance to electricity, it is useful in electrical appliances like automotive plastic components. Because of its ordered molecular structure, PP is semi-crystalline. It results in PP’s stiffer and higher melting temperature compared to PE.
Polypropylene is known for its sturdy yet elastic consistency. It acts with elasticity over a range of deflection but also experiences deformation early in the process. This property makes it a durable material which implies that it can deform without breaking.
For custom plastic 3D printing, a fast speed is adopted. It keeps the internal stress at a minimum level. In the case of surface defects, a slower speed is preferred at higher temperatures. That is why machines providing profiled speed are used.
ACIS®, Autodesk Inventor®, CATIA® V5,Creo™ Parametric, IGES, Parasolid®, Pro/ENGINEER®,Siemens PLM Software’s NX™, SolidEdge®, SolidWorks®, STEP
Compared to other plastics, Polypropylene has a relatively lower density. It results in weight reductions for the producers and sellers of injection-molded products. Because of these reasons, PP can manufacture several applications such as food trays, cups, plates, and toys.
PP injection molding is a thermoplastic addition polymer manufactured by combining several propylene monomers. It features an extensive range of applications such as containers of consumer products and molded plastic products for automotive industries who need auto molds. Since its surface is slippery, it can replace plastics like polyacetal (POM) in some low-friction applications.
It is a colorless, semi-transparent thermoplastic lightweight general-purpose plastic. Polypropylene pellets are generally melted and injection-molded, and are widely used in plastic products, packaging, and automotive parts.
There are several reasons why polypropylene injection molding is popular as the most efficient form of molding. It is ideal for the consistent and affordable production of a wide range of high-quality plastic components that can withstand any environment.
As diluted bases and acids don’t react readily with polypropylene, it is the first choice of the manufacturers in making liquid containers. The material can manufacture the packaging containers of first-aid products, cleaning agents, warehouse plastic box mould, etc.
PP injection molding is a thermoplastic addition polymer manufactured by combining several propylene monomers. It features an extensive range of applications such as containers of consumer products and molded plastic products for automotive industries who need auto molds. Since its surface is slippery, it can replace plastics like polyacetal (POM) in some low-friction applications.
PP injection molding material is strongly resistant to moisture and chemicals like acids, alkalis, and solvents. But it does not offer resistance to aromatic and chlorinated hydrocarbons. And under high temperatures, its oxidation resistance is not as strong as that of PE plastic.
The chemical formula of pp is (C3H6)n, the density is 0.89~0.91g/cm3, flammable, melting point is 164~170℃, soften around 155℃, the use of temperature range of -30~140℃.
But with advantages come disadvantages as well. Due to the slippery surface of the PP injection mold design, it cannot adhere to the surface of other materials. During times when it is required to form a joint, PP needs welding. This property makes it a substitute for plastics such as Acetal (POM) in low friction applications like gears or as a contact point for furniture.
Though PP is slippery at the molecular level, it has a relatively high friction coefficient and acts as a contact point for furniture. As a result, POM, PTFE, or Nylon are perfect for this purpose.
Polypropylene, abbreviated as PP, is a polymer made from propylene through the polymerization reaction. It is a thermoplastic synthetic resin with excellent performance, and is a colorless, semi-transparent thermoplastic lightweight general-purpose plastic.
GETTING A QUOTE WITH LK-MOULD IS FREE AND SIMPLE.
FIND MORE OF OUR SERVICES:
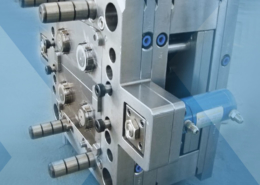
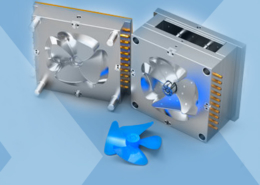
Plastic Molding

Rapid Prototyping
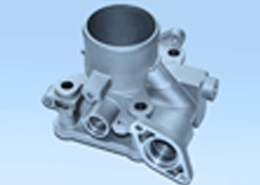
Pressure Die Casting
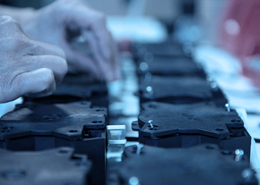
Parts Assembly
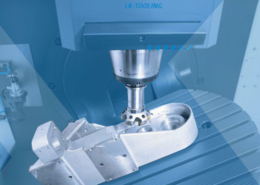