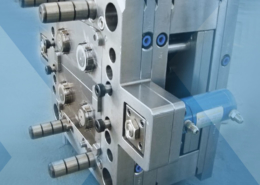
Do-It Essentials Injection Molds for Pouring Soft Baits - soft plastic injection
Author:gly Date: 2024-10-15
With a clamping force of 55,000 kN, a shot weight of 27,500 g and a cycle time of 140 sec, the duo 5500 produces 1100-L waste containers.
Special tools are no longer required for quick and easy melt cylinder changes. Together with the modular nozzle concept of the large injection moulding machine, downtimes are reduced. Our well-thought-out solution saves valuable time.
In simple terms, aluminum injection molding is an injection molding process that uses mold tooling made entirely out of aluminum rather than steel. Companies often use this process for large production runs, and the long-term durability of steel is a common demand. However, advances in tooling creation make the use of aluminum a more viable solution for certain scenarios. There is nothing different about the molding process aside from the tooling material.
The efficient ENGEL ecodrive servo-hydraulics ensure high economic efficiency in the production of large-volume or large-area parts. It is included in the standard scope of the entire duo series. Thanks to the demand-based pump output, the motors are at rest and do not consume any energy when the machine is at a standstill during cooling, for example.
With Reliant Plastics, an injection molding provider with decades of experience, we can help you to make sense of your options and chart a course towards the best production decisions possible. To explore rapid prototyping with aluminum mold tooling or solutions for producing your parts at a larger scale, contact the Reliant Plastics team today for a free quote.
Overall, with aluminum molds, you’ll experience lower initial costs, lower rejection rates and more opportunities to quickly begin production thanks to shorter tooling production times. With steel, you’ll enjoy durability for very high part volumes, less concern about wear and tear, and opportunities to create more advanced parts.
With ENGEL, you get a complete solution for your requirements in the automotive industry. From the machine to automation and peripherals to permanent support for your production from our application engineers.
The efficient ENGEL ecodrive servo-hydraulics ensure high economic efficiency in the production of large-volume or large-area parts. It is included in the standard scope of the entire duo series. Thanks to the demand-based pump output, the motors are at rest and do not consume any energy when the machine is at a standstill during cooling, for example.
Expertise in injection moulding automation at all levels. From the injection moulding machine, to the robot and conveyor belt systems, to third-party peripherals. Everything from a single source.
Internet Explorer is no longer supported. Please switch to a current browser to be able to use engelglobal.com to its full extent.
Let’s turn our attention to the “gold standard” for most molding projects: steel. Why does steel occupy the top spot over aluminum? The answer lies in three specific benefits.
We have positioned our duo series to offer breadth and flexibility. So you will always find the right two-platen injection moulding machine depending on the for your application.
The duo large injection moulding machine features a flexible layout and compact external dimensions. Suitable for various applications: from transport boxes to dashboard carriers to large rainwater tanks. Available with clamping forces from 3,500 kN to 55,000 kN, with more available on request.
Traditionally, injection mold tooling uses steel as the primary material, but it is not the only option. Today, aluminum molds have earned a place in the industry. Let’s explore aluminum injection molding and why it is worth your consideration in some cases.
Our digital solution iQ clamp control automatically determines the optimum clamping force. This reduces mould wear. Mould breathing is always kept within the ideal range and scrap is reduced.
duo speed: The fast duo speed is tailor-made for large-volume containers and similar products with a high flow path/wall thickness ratio.
Injection molding is a common industrial manufacturing process with multiple businesses relying on the technique to produce items for every industry from healthcare to aerospace. However, not all injection mold tooling is the same—and the choice that you make regarding tooling materials for your project could have a significant impact on the outcome as well as your overall costs.
Our digital solution iQ clamp control automatically determines the optimum clamping force. This reduces mould wear. Mould breathing is always kept within the ideal range and scrap is reduced.
Single-step process combining decoration and scratch-resistant surface protection in one production step by means of IMD and PUR coating.
The duo is a large and variable injection moulding machine with a standardised modular principle and compact external dimensions. This saves valuable floor space. With numerous option packages, the concept can be customised from basic requirements to turnkey solutions.
There are several key benefits to using aluminum molds for plastic injection, not only its suitability for prototyping. Consider a few of the perks that make manufacturers choose aluminum just as often as steel.
The complexity of the applications continues to increase. In the future, we also want to support research work. That is why we have invested for the future. The large duo injection moulding machine is unique in its versatility.
Do businesses always want the durability of steel for a molding project? Not necessarily. Manufacturers choose aluminum most often when they need to quickly produce parts without requiring a very high volume. Since aluminum tools wear out faster, their optimal use is for lower part production volumes. They’re also an excellent choice when you need to rapidly produce prototype parts for testing, modification and redesign.
The first production cell to form three organic sheets of different thicknesses and design plus a high-quality visible surface in the same process step.
Two reinforced and movable platens with linear guides for up to 900 t and sliding guides from 1000 t. Excellent platen parallelism and reduced tool wear.
Thanks to exposed tie bars, the duo large injection moulding machine has a supremely clean and flexible mould area. Large moulds and robots, as well as removal heads, find enough space to work efficiently.
Electric cars often have higher demands on the quality of injection moulded components than combustion models. An application example from the automotive supplier Krug shows how ENGEL machines ensure the quality required for this.
Which should you choose: steel or aluminum? With clear pros and cons to each material, the answer depends on the specific needs of your projects. Partnering with an experienced and highly capable plastics manufacturer offers you the insights that you require to make smart decisions at every step, including in material selection.
Transport boxes with recycled material in the core are produced on a big duo injection moulding machine using the ENGEL skinmelt plasticising process.
As with aluminum, there are some downsides to using steel tooling. It’s crucial to include these factors in your considerations during the project planning stage.
duo combi: The duo combi is the high-performance, multi-component, large-scale machine with a wide variety of different injection unit combinations.
Thinking ahead in plastics processing. Innovative and resource-saving technologies and processes. For every requirement in modern injection moulding.
The CC300 is an innovative machine control system with modern operating logic, self-explanatory navigation and individual configuration options. Robots and peripherals are fully integrated.
Equipped with a customised range of functions, a PP compound with 30 % post-consumer recyclate is processed using standard components.
Special tools are no longer required for quick and easy melt cylinder changes. Together with the modular nozzle concept of the large injection moulding machine, downtimes are reduced. Our well-thought-out solution saves valuable time.
Thanks to sophisticated barrel cooling, the hydraulic injection unit delivers excellent injection performance. Optimised screw geometries guarantee high plasticising performance, too. The ecodrive servo-hydraulic drive saves energy.
Internet Explorer is no longer supported. Please switch to a current browser to be able to use engelglobal.com to its full extent.
duo fast track: Our duo fast track with short delivery time is the choice when you need a quickly available injection moulding machine.
Our customer portal provides ENGEL customers with a wealth of additional information on our injection moulding machines:
We have upgraded our proven duo injection moulding machine to the duo tech: Larger mould space with the same footprint, higher performance of the injection unit and even shorter dry cycle times enable you to further increase your output.
The duo is a large and variable injection moulding machine with a standardised modular principle and compact external dimensions. This saves valuable floor space. With numerous option packages, the concept can be customised from basic requirements to turnkey solutions.
While there are some obvious benefits to using aluminum, there are several reasons why steel molds for plastic injection has remained a dominant choice. Aluminum comes with some disadvantages you must consider, including the following.
GETTING A QUOTE WITH LK-MOULD IS FREE AND SIMPLE.
FIND MORE OF OUR SERVICES:
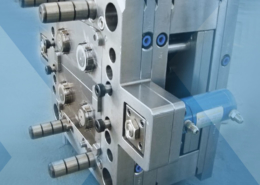
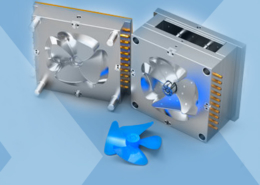
Plastic Molding

Rapid Prototyping
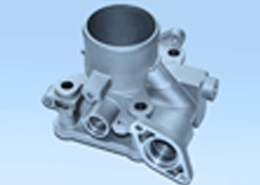
Pressure Die Casting
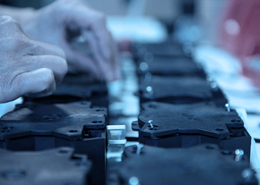
Parts Assembly
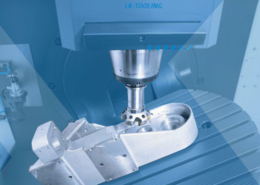