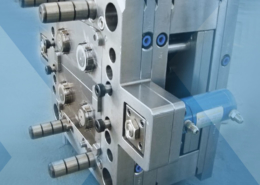
Unveiling the World of Plastic Injection Molding at Home
Author:gly Date: 2024-06-08
The concept of plastic injection molding at home has garnered significant interest among DIY enthusiasts and hobbyists, offering the potential to create custom plastic parts and prototypes in the comfort of one's own workshop. This article aims to explore the possibilities, challenges, and considerations associated with plastic injection molding at home, providing readers with a comprehensive understanding of this fascinating endeavor.
Introduction to Plastic Injection Molding at Home
Plastic injection molding is a manufacturing process that involves injecting molten plastic material into a mold cavity, where it solidifies to form the desired shape of the final product. While traditionally carried out in industrial settings, advancements in technology and the availability of affordable equipment have made it increasingly feasible for individuals to explore plastic injection molding at home. This DIY approach opens up a world of possibilities for creating custom parts, prototypes, and small-scale production runs with relative ease and affordability.
Equipment and Tools
To embark on plastic injection molding at home, enthusiasts require a set of essential equipment and tools. This typically includes an injection molding machine or a manual injection molding kit, molds or dies, thermoplastic pellets, and auxiliary equipment such as a heating system, cooling system, and mold release agents. While industrial-grade equipment can be expensive, there are cost-effective options available for hobbyists and DIY enthusiasts, ranging from desktop injection molding machines to 3D-printed molds.
Materials and Safety Considerations
Selecting the right materials is crucial for successful plastic injection molding at home. Thermoplastic materials such as ABS, PLA, and polyethylene are commonly used due to their ease of melting, molding, and availability in pellet form. However, it is essential to consider factors such as material compatibility, melting temperature, shrinkage, and mechanical properties when choosing materials for specific applications. Additionally, safety considerations such as proper ventilation, handling of molten plastic, and equipment maintenance are paramount to ensure a safe and productive working environment.
Challenges and Limitations
While plastic injection molding at home offers numerous benefits, it also presents several challenges and limitations. One of the primary challenges is achieving consistent results and quality comparable to industrial-grade processes, as home-based equipment may lack the precision and capabilities of professional machinery. Moreover, the upfront cost of equipment, the learning curve associated with mold design and processing parameters, and the time required for trial and error can pose obstacles for beginners. Despite these challenges, with patience, practice, and perseverance, hobbyists can overcome limitations and achieve satisfying results.
Future Directions and Recommendations
Looking ahead, the field of plastic injection molding at home holds promise for further innovation and advancement. As technology continues to evolve, we can expect to see improvements in equipment affordability, ease of use, and accessibility, empowering more individuals to explore their creativity and bring their ideas to life through plastic injection molding. Additionally, educational resources, online communities, and collaborative platforms can facilitate knowledge sharing and skill development, fostering a vibrant community of DIY enthusiasts and innovators.
In conclusion, plastic injection molding at home offers a rewarding and fulfilling experience for DIY enthusiasts and hobbyists eager to unleash their creativity and produce custom plastic parts and prototypes. By understanding the equipment, materials, challenges, and future directions associated with this endeavor, individuals can embark on their journey with confidence and enthusiasm, contributing to the democratization of manufacturing and innovation in the digital age.
GETTING A QUOTE WITH LK-MOULD IS FREE AND SIMPLE.
FIND MORE OF OUR SERVICES:
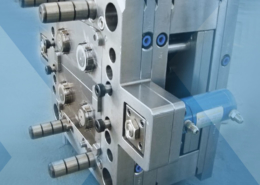
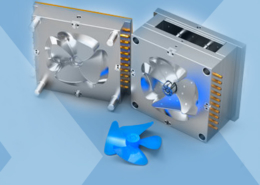
Plastic Molding

Rapid Prototyping
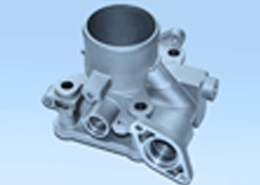
Pressure Die Casting
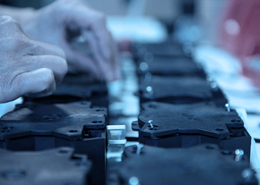
Parts Assembly
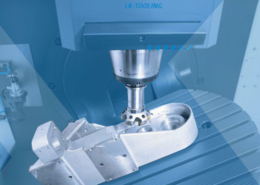