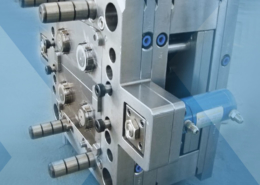
Exploring the Dynamics of Plastic Injection Mold Tooling
Author:gly Date: 2024-06-08
Introduction
Plastic injection mold tooling is a cornerstone of modern manufacturing, enabling the production of intricate plastic components with precision and efficiency. From automotive parts to consumer electronics, the versatility of injection molding has revolutionized various industries. This article aims to provide a comprehensive overview of plastic injection mold tooling, delving into its processes, applications, challenges, and future prospects.
Processes and Principles
Plastic injection mold tooling involves a complex interplay of processes and principles. At its core, it relies on the injection of molten plastic into a mold cavity under high pressure. The mold, typically made of steel or aluminum, is precision-engineered to form the desired shape of the final product. The injection molding process encompasses several stages, including clamping, injection, cooling, and ejection, each requiring meticulous attention to detail for optimal results.
Materials and Selection Criteria
The choice of materials plays a pivotal role in plastic injection mold tooling. Various thermoplastics, such as polyethylene, polypropylene, and polycarbonate, offer unique properties suited to different applications. Factors such as strength, flexibility, heat resistance, and cost must be carefully considered when selecting the appropriate material for a specific project. Additionally, advancements in material science continue to expand the range of options available to manufacturers, opening up new possibilities for innovation.
Design Considerations and Optimization
Effective design is paramount in plastic injection mold tooling to ensure the integrity and functionality of the final product. Design considerations such as part geometry, wall thickness, draft angles, and gating systems directly impact the manufacturability and performance of injection-molded components. Utilizing computer-aided design (CAD) software and simulation tools allows engineers to optimize designs, minimize defects, and enhance overall efficiency throughout the manufacturing process.
Quality Control and Assurance
Maintaining stringent quality control measures is essential in plastic injection mold tooling to uphold product consistency and reliability. Advanced inspection techniques, including dimensional analysis, visual inspection, and non-destructive testing, help identify and rectify defects early in the production cycle. Additionally, implementing robust quality management systems and adhering to industry standards and regulations are crucial steps in ensuring the highest standards of quality and safety.
Cost-Efficiency and Scalability
Achieving cost-efficiency and scalability is a key objective in plastic injection mold tooling. By optimizing production processes, minimizing material waste, and streamlining workflows, manufacturers can reduce production costs while maintaining product quality. Furthermore, leveraging innovative technologies such as automation, robotics, and additive manufacturing holds the potential to further enhance efficiency and scalability in injection molding operations.
Conclusion
In conclusion, plastic injection mold tooling serves as a cornerstone of modern manufacturing, enabling the efficient production of high-quality plastic components across various industries. By understanding the intricacies of processes, materials, design considerations, quality control measures, and cost-efficiency strategies, manufacturers can harness the full potential of injection molding technology. Looking ahead, continued advancements in materials science, design optimization, and manufacturing technologies promise to further elevate the capabilities and versatility of plastic injection mold tooling, paving the way for enhanced innovation and competitiveness in the global marketplace.
GETTING A QUOTE WITH LK-MOULD IS FREE AND SIMPLE.
FIND MORE OF OUR SERVICES:
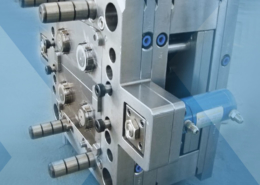
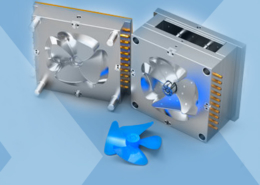
Plastic Molding

Rapid Prototyping
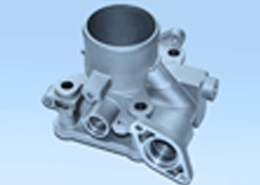
Pressure Die Casting
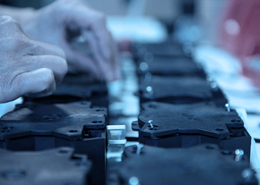
Parts Assembly
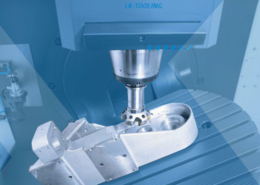