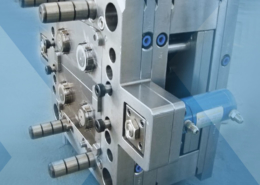
DIY Injection Molding Machine - injection molding at home
Author:gly Date: 2024-10-15
Generally, the undercut injection molding features complicate and in some instances prevent parts injection. Eliminate them if possible. If you find it hard to get rid of them, try sliding shutoffs, pass-through cores, or change the parting line and draft angles to simplify the mold build.
The complete production run for low-volume molding usually takes precisely three days to create the finished parts. For instance, let’s assume the following parameters for a 100 – 200 part run:
It can range dramatically from a few hundred to hundreds of thousands of dollars. Think about the vast application of injection molding. There is a virtually limitless array of products made with them. In such a scenario, it is tough to specify an exact figure as far as the cost of injection molding goes.
DFM (Design for Manufacturing) in injection molding involves creating a part within a client’s stipulated budget and fulfilling the intended purpose. Analysts often consider different factors for DfM based on technology, art, and science to determine the most efficient design. Hence, it significantly reduces the costs of injection molding.
In response to growing environmental concerns, the ABC Plastic Moulding industry is embracing sustainability initiatives aimed at reducing carbon footprint and minimizing waste. From the adoption of biodegradable resins to the implementation of closed-loop recycling systems, manufacturers are actively seeking ways to mitigate their environmental impact while maintaining operational excellence.
Unnecessary features that do not add significant value to your final products will increase plastic injection molding costs. Textured surfaces, for instance, may simply not be needed. This holds true for cosmetic add-ons like bead blasting or high mold polish too. Remember that excess features might also require more mold cavities that further drive costs north.
Generally, the injection molding process has no fixed cost for every application. Custom injection molding cost has a varying value that ranges from thousands to hundreds of thousands. Below are common factors that impact the cost of injection molding.
These machines provide high precision, repeatability, and energy efficiency. Furthermore, they have high initial investment costs and require heavy maintenance since they use electric motors and hydraulic pumps.
Making self-mating parts is one of the most reliable ways of saving injection molding costs and simplifying design. These parts are those that attach to themselves when turned 180 degrees. These parts are ideal because you can use a single half mold to make the whole part. It reduces mold cost, and the injection mold size is half.
These hydraulic injection machines perform injection molding operations with a hydraulic pump. They are usually durable, offer highly consistent ejection and injection, and have economical initial purchase costs. However, they can be imprecise and consume excessive energy.
There is no simple and straightforward answer to this. But broadly, one can say that, while injection molding can be expensive, it need not always be the case. Factors such as production volumes as well as the complexity of the parts being manufactured play a key role in finally determining injection molding costs. When similar items with tight tolerances are made in large volumes, injection molding proves to be an inexpensive process.
3D printing is one of the fastest procedures for making molds for plastic injection molding projects. This method uses a 3D printer and doesn’t necessarily require a skilled operator. Hence, it saves labor and mold costs. However, 3D printed components are often limited in dimensions due to the size of the 3D printer’s build platform. Similarly, printed molds are more likely to experience shrinkage.
However, it may be ideal to outsource to injection molding service providers instead of buying a machine to avoid the high cost of an injection molding machine.
However, it is evident that the injection molding price per part reduces considerably for high-volume production. Hence, high-volume projects offer the best cost advantage for injection molding costs.
Molded parts’ variables, such as design, size, and volume of injection molding components, often decide injection mold cost. You can optimize the cost of your project significantly when you understand how these variables impact the project’s plastic injection molding cost.
WayKen is the right partner for you whenever you need rapid injection molding services, from low-cost injection molding to high-volume production. We offer quality and cost-effective rapid tooling and injection molded parts that meet your requirements.
Different production volumes are also an essential factor in the cost of injection molding. Moreover, the production volume influences the amount of raw material used in injection molding, required machine sophistication, and injection mold properties such as durability, strength, and other properties. Here are the typical types of production volume injection molding:
The injection molding process requires unique equipment. However, the machine’s size and level of sophistication determine the cost and range from small to large machine. Therefore, it would help to consider the following injection molding machine types and how they influence injection molding costs.
Central to the success of ABC Plastic Moulding is the meticulous design and fabrication of moulds. Engineers employ advanced CAD/CAM software and CNC machining to create precise moulds tailored to the specifications of each component. This emphasis on tooling ensures optimal part quality and efficiency throughout the production cycle.
Injection molding is one of the most commonly used manufacturing of various products nowadays. However, understanding injection molding cost and its estimation helps significantly optimize the manufacturing process. This article has discussed the different variables you must understand to know about costs in injection molding and how to utilize it. Hence, it would help to understand the cost variations in injection mold tooling and mold cost.
The choice of materials plays a crucial role in ABC Plastic Moulding, influencing the mechanical properties, aesthetics, and performance of the final product. Engineers meticulously select resins based on factors such as strength, flexibility, and environmental considerations, ensuring compatibility with the intended application.
Mid-volume quantities in injection molding often range between five thousand to tens of thousands of molded parts. This production type requires mold made from pre-hardened steel or aluminum. You can outsource the mold production and molding procedures for this production scale.
Low-volume plastic molding includes any production of parts between a hundred to a couple of thousand. Manufacturers often make the molds in-house and perform the molding themselves without necessarily using sophisticated machines. Hence, manufacturers produce molds of 3D-printed polymer resin or fast rapid tooling since it is affordable and doesn’t require a long production cycle.
Plastic injection molding is compatible with an extensive range of plastic resins with varying availability, price, applications, and properties. Typical examples of plastic injection materials include PC, ABS, PU, PP, and PE.
The CNC machining process is well-suited for making metal molds from aluminum or steel materials. For instance, CNC machines use cutting tools to remove materials from an aluminum block to machine an aluminum mold. Besides, this machining method produces aluminum molds with high accuracy.
Also, If you need a custom mold, always consider having a CAD model in place prior to commencing the manufacturing process. It will help optimize designs and identify potential problems such as steep draft angles, unnecessary wall thicknesses, complex shapes, etc.
In the medical and healthcare sector, ABC Plastic Moulding plays a vital role in the production of disposable medical devices, surgical instruments, and equipment components. Its ability to meet stringent regulatory requirements, coupled with its cost-effectiveness and scalability, makes it indispensable in the quest for innovation and patient care.
It may be compulsory to use complex molds and additional steps during plastic injection molding due to the complex features of your products. Therefore, removing unnecessary features would be best to lower the injection molding price. At the same time, you can save more money by removing any features that only add cosmetic finishes.
Although manufacturers commonly utilize injection molding for the mass production of thousands of identical parts using thermoplastic and thermosetting polymers, materials such as metals and elastomers are also compatible materials.
Insert injection molding and overmolding are effective technologies that save costs in the long run. For instance, insert molding prevents the need to make threads on the plastic to fasten it to metal parts, thereby making the process economical.
The cost of plastic pellets material used in plastic injection molding technique ranges from 1 dollar per kg to 5 dollars per kg. However, the injected material’s final cost depends on the used amount and the required design.
Electric molding machines utilize an electro-servo motor to direct the machine during injection molding. They utilize less energy, incur low operating and maintenance costs, and are accurate and easy to use. Nevertheless, their initial investment cost is high and requires routine maintenance.
At the heart of ABC Plastic Moulding lies the injection moulding process, a sophisticated technique wherein molten plastic is injected into a mould cavity under high pressure. This process allows for the rapid and cost-effective production of intricate parts with high precision and repeatability.
By integrating resources, we provide on-demand manufacturing capabilities and custom machining services to produce high-quality molds and plastic components. More so, our engineering team offers professional design suggestions and material choices. Please submit your injection molding CAD file, we will provide quick quotes and free DfM analysis.
As technology continues to evolve, so too does the landscape of ABC Plastic Moulding. Innovations in materials science, process optimization, and automation are poised to enhance efficiency, reduce waste, and expand the capabilities of this versatile manufacturing technique.
High-volume injection mold production involves a few hundreds of thousands of molded parts. This procedure often requires steel molds due to their long life expectancy. Likewise, large-volume projects require a sophisticated machine, which adds to the injection molding cost. However, high-volume production offers higher cost distribution per part, ensuring lower cost per part.
In the automotive industry, ABC Plastic Moulding is instrumental in the production of interior and exterior components, including dashboards, bumpers, and trim panels. Its ability to deliver lightweight, durable, and aesthetically pleasing parts aligns with the industry's emphasis on fuel efficiency, safety, and design innovation.
In conclusion, ABC Plastic Moulding represents a cornerstone of modern manufacturing, offering unparalleled versatility, efficiency, and reliability across a diverse range of industries. From automotive to healthcare, its impact reverberates throughout society, driving innovation, enhancing quality of life, and shaping the future of manufacturing. As we look ahead, the continued advancement of technology and sustainability initiatives promises to further elevate the capabilities and impact of ABC Plastic Moulding, ushering in a new era of ingenuity and progress.
If you do not require a custom mold, consider using the universal mold. These molds are often less expensive than custom molds and can still produce high-quality parts.
However, let’s assume the following injection molding cost calculation for a 5,000 – 10,000 unit volume. These are the same parts made using thermoplastic materials such as polypropylene.
The versatility of ABC Plastic Moulding extends to the realm of electronics and consumer goods, where it facilitates the production of enclosures, housings, and connectors for electronic devices. Its ability to accommodate complex geometries and tight tolerances makes it an ideal choice for manufacturers seeking to optimize product performance and aesthetics.
Electrical Discharge Machining (EDM) is an assisted technique for making molds with complex and precise features. It involves using electrical discharge to melt and form the metal workpiece into the desired size and shape. Although EDM offers excellent accuracy, it is compatible with only metal molds.
The more cavities there are in a mold, the higher the cost will be. Therefore, it is important to minimize the number of cavities in your mold whenever possible.
To make complex parts, you must create a mold with even complexity using manufacturing methods such as 3D printing, CNC machining, or EDM machining. Besides, you need more material to fill the mold to produce complex parts. Consequently, this increases the injection molding material cost. At the same time, complex parts may require extended production time since they may require additional steps in the production process.
Injection molding is a widely used technology for manufacturing multiple parts and components for various applications. So, how much does injection molding cost? This question is important to determine whether the process suits your manufacturing project.
It is expensive to machine the mold and mold base for the products, even though the molding equipment is a one-time investment. Besides, the process used to create the molds determines the cost. The standard techniques used in making molds include CNC machining, electric discharge machining, and 3D printing.
The cost of the preferred material for your parts often influences the overall injection molding cost. Where possible, use lower-cost materials such as ABS or polypropylene. It helps to keep a minimal production cost.
Hybrid injection molding machines combine the characteristics of electric and hydraulic injection molding machines. It uses a servo motor and hydraulic pump to distribute the oil used in producing hydraulic pressure that creates the component in the machine.
In the realm of manufacturing, ABC Plastic Moulding stands as a beacon of innovation and efficiency, offering versatile solutions for the production of plastic components across various industries. From automotive parts to consumer electronics, ABC Plastic Moulding plays a pivotal role in shaping the modern world. In this article, we delve into the intricacies of ABC Plastic Moulding, exploring its processes, applications, and impact on the manufacturing landscape.
One way to reduce the number of cavities is to use a moldflow analysis to optimize the design of your part. Moldflow analysis can help you to identify areas where cavities can be eliminated without compromising the function or aesthetics of the part.
This article explores injection molding cost and the factors to affect it. You’ll also learn about the injection molding types of production volume and how to reduce injection molding costs. Let’s get to it.
Most procedures associated with injection molding are automated and controlled by software systems. However, typical labor costs involved in injection molding include:
As we mentioned above, the simplest trick to reduce the price per piece is by increasing the parts quantity since the upfront costs while machining and designing the mold can be used over more parts. In addition to that, you can also try the following several ways to reduce injection molding costs and help you get the best results for your project.
Creating large molded parts will require more injection molding material, hiking the costs of injection molded components. Similarly, it would be best to use the proper injection molding machine and manufacture the right mold size when handling large parts.
GETTING A QUOTE WITH LK-MOULD IS FREE AND SIMPLE.
FIND MORE OF OUR SERVICES:
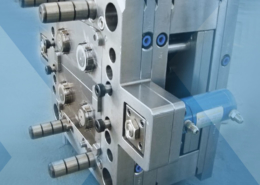
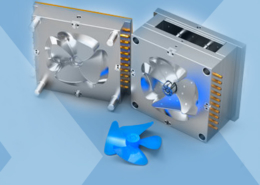
Plastic Molding

Rapid Prototyping
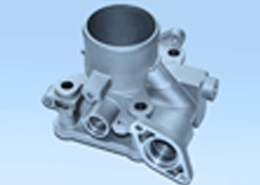
Pressure Die Casting
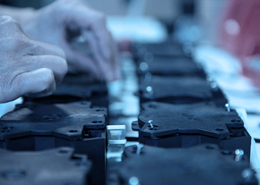
Parts Assembly
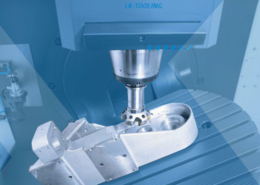