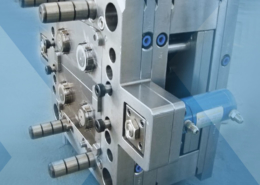
DIY Injection Molding Machine - injection molding at home
Author:gly Date: 2024-10-15
By signing up, you agree to our Terms of Use and Privacy Policy. We may use the info you submit to contact you and use data from third parties to personalize your experience.
Whenever possible, apply a uniform wall thickness throughout your part. If you need to use a greater thickness in some areas, make the transition from thinner to thicker sections gradual. Do not use transitions that are greater than 10% to 15% of the nominal wall thickness. Generally, the recommended minimum wall thickness for HDPE ranges between 0.76 and 3.18 mm.
We exist to eliminate bottlenecks in new product development by integrating the people, processes, and platform you need to source custom parts.
By signing up, you agree to our Terms of Use and Privacy Policy. We may use the info you submit to contact you and use data from third parties to personalize your experience.
HDPE is available in various brands and grades. The table below contains typical physical, mechanical, and injection molding properties of this popular material.
Tolerances are acceptable variations in size for overall dimensions and part features. As a rule, parts with tighter tolerances are more expensive because they have stricter injection mold and processing requirements. In addition, parts with fine tolerances are more expensive to mold than parts with commercial tolerances.
Nylon has good mechanical strength and can be filled with glass fibers for enhanced properties. It absorbs moisture, however, so nylon is not a good choice for injection molded products where there’s continuous contact with water.
Draft is the angle that you apply to the vertical walls of parts so that they eject cleanly from the injection mold. Because HDPE has a low coefficient of friction, parts with simple shapes need very little draft. For more complex HDPE parts, apply draft angles between 0.5% and 1% per side.
HDPE can’t compete with engineering plastics in terms of performance, but it’s an attractive, low-cost option for many applications that require good tensile strength, impact resistance, and overall toughness.
HDPE, a type of polyethylene (PE), is a commonly used injection molding material that is significantly less expensive than specialty plastics and polymer blends. HDPE is readily available and has lower minimum order quantities (MOQs) than specialized materials.
By signing up, you agree to our Terms of Use and Privacy Policy. We may use the info you submit to contact you and use data from third parties to personalize your experience.
Injection molded HDPE might not be the best material for your application. If that’s the case, you could consider polypropylene or nylon instead. Fictiv’s injection molding services work with both of these materials.
Accelerate development with instant quotes, expert DFM, and automated production updates.
By signing up, you agree to our Terms of Use and Privacy Policy. We may use the info you submit to contact you and use data from third parties to personalize your experience.
Access a wide breadth of capabilities through our highly vetted network.
The melt temperature for HDPE is between 246 to 280°C. The mold temperature ranges between 45 and 65°C. Increasing the mold temperature can reduce internal part stresses and produce parts with a glossier surface finish.
HDPE crystallizes fairly quickly. Therefore, thin-walled parts need fast injection speeds. For thicker-walled parts, medium injection speeds are recommended.
By signing up, you agree to our Terms of Use and Privacy Policy. We may use the info you submit to contact you and use data from third parties to personalize your experience.
High-density polyethylene is a low surface energy (LSE) material that is very difficult to bond. Overmolding, an injection molding technique that molds one material over another, is ill-suited for HDPE. Specialized glue and adhesives for HDPE are available, but plastic fusion welding can also be used for assembly.
We exist to eliminate bottlenecks in new product development by integrating the people, processes, and platform you need to source custom parts.
Create high quality custom mechanicals with precision and accuracy.
By signing up, you agree to our Terms of Use and Privacy Policy. We may use the info you submit to contact you and use data from third parties to personalize your experience.
HDPE does not readily absorb moisture. If stored properly, it may not need drying before injection molding. Drying is required, however, if surface moisture has settled onto the material during storage.
The injection pressure for HDPE injection molding depends on the design and size of your part. In general, however, injection pressures range from 5.5 to 10 MPa because HDPE flows readily. Reducing the injection pressure can help reduce part warpage.
HDPE injection molding uses high-density polyethylene (HDPE), a cost-effective thermoplastic with good tensile strength and high impact resistance. This commodity plastic also has strong moisture resistance and is relatively easy to injection mold. HDPE is used in many applications, but it has a high rate of thermal expansion. Consequently, injection-molded HDPE parts are prone to higher shrinkage rates if they’re not designed and manufactured properly.
HDPE is petroleum-based and highly flammable. It begins to burn when exposed to temperatures above 340°C and will continue to burn since it’s not self-extinguishing. For reduced flammability, HDPE grades with flame-retardants are available.
Injection-molded HDPE resists a wide range of chemicals, including strong acids and bases. It also resists some oxidants and reducing agents. HDPE can be attacked by halogenated hydrocarbons, however, and it has limited resistance to mineral oils.
Molds or Moulds service for Injection Molding Machines RobotDigg does Not only produce molds for the standard injection molding machine But also can design and produce the molds for our mini Injection Molding Machines. https://www.robotdigg.com/product/743/ https://www.robotdigg.com/product/1862/ https://www.robotdigg.com/product/657/ https://www.robotdigg.com/product/1900/
Compared with 3D Printing, injection molding is much more suitable for production, Not only because of the production efficiency or capacity But also on the product strength.RobotDigg do provide molds service for our desktop injection molding machine, also we can do molds for an injection molding machine you have.
HDPE has a relatively high coefficient of thermal expansion (143 μm/°C), a property that describes the extent to which a material expands with an increase in temperature. Because heating occurs during injection molding, HDPE parts can expand significantly. In turn, injection-molded HDPE may experience warping when it contracts during cooling.
Then, create a free Fictiv account and upload your part drawing. Along with design for manufacturing assistance (DFM) from our engineering experts, you’ll gain access to our carefully vetted network of manufacturing partners. Why search for an HDPE injection molder on your own when you can get expert DFM feedback and leverage the power of Fictiv?
Polypropylene (PP) is a commodity thermoplastic with good fatigue strength, a low coefficient of friction, and excellent moisture resistance. Like HDPE, it’s also cost-effective.
Injection molded HDPE has a relatively high rate of shrinkage (up to 4%). The exact percentage depends on the grade of HDPE that you select, as well as the specific processing conditions. If parts shrink unevenly during cooling, warping may occur. To limit the risk of defects, reduce the wall thickness and the size of the mold gate area.
Our trained employees ensure your parts will be delivered on time and to spec.
If you’re considering HDPE injection molding for your plastics project, keep reading to learn more about high-density polyethylene, including:
Adherence to HDPE processing guidelines is beyond a part designer’s immediate control. Therefore, it’s important to work with an experienced HDPE injection molder. The following processing parameters are especially important:
HDPE can be injection molded for industrial, automotive, and consumer goods applications. Food contact applications are less typical, but FDA grades of HDPE plastic are available.
HDPE parts that are poorly designed are more prone to injection molding defects. When you work with Fictiv, however, you’ll get DFM feedback that can help minimize risk. To learn about part design, download our free “Injection Molding Design Guide” to use as a reference.
RobotDigg Equip Makers Empower Engineers Global Sourcing Supply Chain from Shanghai RobotDigg Shanghai RobotDigg has been professionally manufacturing... >>more
HDPE is an injection molding material with attractive properties, but a manufacturing-ready design and a skilled production partner are critical. Fictiv has the engineering experts and manufacturing network you need to get quality parts fast. From prototyping through production, we’re here to help you succeed.
By signing up, you agree to our Terms of Use and Privacy Policy. We may use the info you submit to contact you and use data from third parties to personalize your experience.
Q: How to start an injection mold? A: It needs to see the injection molding machine you have, the shot volume, and the platen dimensions.The product you want to do by plastic molding. Size, weight, and plastics (PS as default) or a STEP/STP file with dimensions necessary for evaluation. Q: How many cavities can it have? A: The answer is nearly the same as above, it will need to see the injection molding machine and the item needs to be molded out. Q: Do I need a hot runner mold? A: For mini injection molding machines to produce samples or plastic specimens, etc., two plates or three plates cold runner injection molds are adopted because of the cost, and also the plastic waste of sprue is low. Hot runner is more complicated but people use it more because the hot runner system produces less plastic waste (sprue/stem), which can shorten the cycle times to save energy and labor for runner handling, trimming, and regrinding. Q: Why do I choose Injection Molding other than 3D Printing? A: Yes, in recent years, 3D Printing is growing fast, personal or industrial 3D Printers are easy to get and start. But for batch production you still need Injection Molding that the technology is more mature, the product is more reliable and the process is quite faster than 3D Printing. 1. To start with Injection Molding, you may need a testing unit mini injection molding machine and the mold for the prototype. 2. I want to do injection molding on new plastics to check if the material is OK for injection molding purposes and its tensile strength and other features. 3. I just love Injection Molding compared with 3D Printing and want to own a mini Injection Molding Machine. 4. I am an engineering student or professor, Injection Molding is a course of mine.
Create your free Fictiv account and request an injection molding quote today — we mold complex parts at ridiculous speeds!
Plastic specimen for testing purpose RDM001 Plastic or resin developed for extrusion or injection molding, etc, before it heads to the market, we need to do some basic tests on it. The above typical properties are tested Tensile Stress Yield and Break, Elongation Yield and Break, Flexural Modulus and Strength, Rockwell Hardness, R Scale, Izod Impact Strength Notched and Unnotched, and so on properties are tested with special specimen molding out by injector or molder.
By signing up, you agree to our Terms of Use and Privacy Policy. We may use the info you submit to contact you and use data from third parties to personalize your experience.
Some of the molds are easy But most of them need to be modified several times during manufacturing, especially for the mold with a hot runner.
Sharp corners are difficult to injection mold. Therefore, apply radii to both the inside and outside corners of your part. To limit stress concentrations and melt flow, make the radii at least 25% of the wall thickness. For maximum part strength, apply a radius equal to 75% of the wall thickness.
By signing up, you agree to our Terms of Use and Privacy Policy. We may use the info you submit to contact you and use data from third parties to personalize your experience.
GETTING A QUOTE WITH LK-MOULD IS FREE AND SIMPLE.
FIND MORE OF OUR SERVICES:
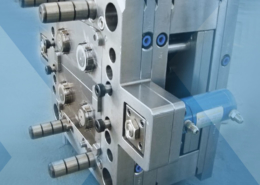
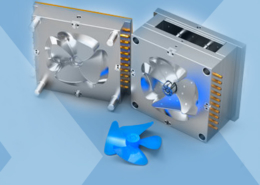
Plastic Molding

Rapid Prototyping
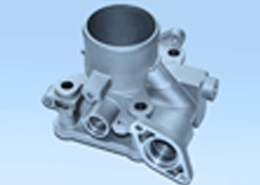
Pressure Die Casting
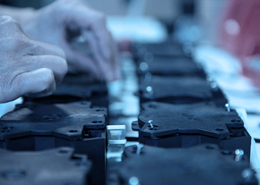
Parts Assembly
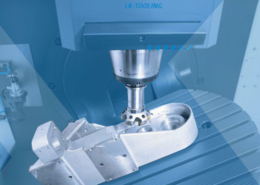