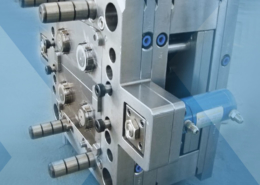
DIY Injection Molding : 9 Steps (with Pictures) - molding plastic at home
Author:gly Date: 2024-10-15
UV Resistant PC: By adding UV stabilizers, the weather resistance of PC for outdoor use is enhanced, reducing discoloration and performance degradation due to prolonged UV exposure.
Transparent PC: Although PC is inherently transparent, specific modifications can further enhance its transparency and optical properties, suitable for optical products and decorative items that require high transparency.
These parameters should be adjusted and optimized according to actual machine conditions, material characteristics, and product design requirements. Correct injection molding parameters are essential for ensuring product quality and production efficiency.
Transparent Casings and Goggles: PC’s high transparency and strength make it ideal for manufacturing various transparent casings and goggles.
Let’s quickly understand the various types of Polycarbonate (PC) and the nature of modified PC. Modified PC refers to the materials obtained by adding different reinforcing materials or additives to the base PC resin to improve or enhance its original properties. Common types of modified PC include:
However, like any process, traditional injection molding has its limitations, particularly when it comes to prototyping. Creating a mold for injection molding can be a painstakingly slow and costly endeavor, especially if modifications are needed in the part design. Moreover, the traditional approach may not be the most feasible option for low-volume production runs due to the potential exorbitant cost per part.
When venturing into rapid injection molding for prototyping purposes, it is crucial to engage with a reputable injection molding company that possesses substantial expertise in this field. The selected company should demonstrate a track record of executing rapid injection molding projects and have the capability to deliver high-quality prototypes that align with your specific requirements. Furthermore, their proficiency should extend to offering guidance on material selection and addressing any design considerations that might impact the injection molding process.
Polycarbonate (PC) plays a crucial role in various injection molding products due to its unique characteristics and is widely used in the following areas:
Glass Fiber Reinforced PC: Reinforcing PC with glass fibers enhances its mechanical strength and dimensional stability, making it more suitable for applications requiring high strength and rigidity.
All in all, rapid injection molding prototyping stands as an exceptional choice for companies seeking to swiftly generate functional prototypes while keeping costs significantly lower than those associated with traditional injection molding. This process enables the creation of multiple design iterations in a short timeframe, facilitating rapid product enhancement. While rapid injection molding does have its limitations, such as unsuitability for large-scale production runs, it proves to be an excellent solution for low-volume production needs and the fabrication of complex parts.
PC/PBT or PC/PET Alloy: By blending with PBT (Polybutylene Terephthalate) or PET (Polyethylene Terephthalate), chemical resistance and impact resistance are enhanced, often used for products requiring chemical corrosion resistance and high impact strength.
These applications demonstrate the widespread use of PC in modern industry and everyday life. Its features, such as high transparency, strength, and flame retardancy, play an important role in many fields.
Casings for Electrical Products: PC is also widely used in manufacturing casings for electrical products, such as electric meter housings. The choice of PC is mainly due to its flame-retardant properties, weather resistance, and high strength and toughness, ensuring the safety and durability of electrical products.
High and Low Molecular Weight PC: High molecular weight PC has longer chain lengths, typically showing higher strength, better heat resistance, and superior mechanical properties. It’s suitable for high-performance applications like bulletproof materials and high-end mechanical parts. Conversely, low molecular weight PC, with shorter chain lengths, is easier to process and mold but usually means lower mechanical strength and heat resistance. This type of PC is more suitable for general consumer products and non-heavy-duty applications.
Moreover, rapid injection molding offers a cost-effective approach. By employing 3D-printed or machined molds, the production cost of prototypes is significantly reduced in comparison to traditional injection molding. Consequently, it becomes an appealing option for low-volume production runs or companies working within constrained budgets.
In conclusion, mastering polycarbonate in injection molding opens up a realm of high-performance applications due to its unique properties. By understanding the right techniques, parameters, and modifications, manufacturers and designers can harness the full potential of PC, ensuring durable, high-quality, and versatile products in a wide range of industries.
Optical Discs: Optical discs, such as CDs and DVDs, are typically made of PC material, benefiting from its excellent optical properties and processability.
PC/ASA Alloy: Alloying with ASA (Acrylate-Styrene-Acrylonitrile) improves weatherability and UV resistance, suitable for applications that are exposed outdoors for long periods.
These modified PC materials, with their unique combination of properties, find widespread applications in various industrial fields. Through modification, the application range of PC has been greatly expanded, meeting more stringent or specific performance requirements.
Carbon Fiber Reinforced PC: Incorporating carbon fibers improves the material’s strength and thermal stability, suitable for lightweight and high-performance applications in aerospace and automotive industries.
Polycarbonate (PC) is an amorphous thermoplastic material, a high polymer containing carbonate groups (-O-C(=O)-O-) in its molecular chain. It is synthesized through a polymerization reaction involving Bisphenol A (BPA) and Phosgene (COCl2). Known as a high-performance thermoplastic, PC is widely used for its outstanding transparency, heat resistance, and impact resistance.
One prominent advantage of rapid injection molding lies in its remarkable speed. While traditional injection molding often entails weeks or even months for mold creation, rapid injection molding molds can be manufactured in a matter of days. This accelerated timeline facilitates swift iterations of designs, allowing for rapid refinement of the product.
PC/ABS Alloy: Mixing PC with ABS (Acrylonitrile Butadiene Styrene) combines the high strength and heat resistance of PC with the ease of processing and surface smoothness of ABS, along with stress crack resistance. This is widely used in automotive parts, electronic device casings, and more.
Rapid injection molding prototyping emerges as a practical solution to overcome limitations by streamlining both time and cost involved in mold creation for injection molding. It empowers designers and engineers to swiftly produce functional prototypes at a fraction of the expense typically associated with traditional injection molding methods.
Rapid injection molding prototyping is a remarkable manufacturing process that has stood the test of time for well over a century. It revolves around the art of melting plastic pellets or resins and injecting them into a specially crafted mold cavity, resulting in the formation of a solid part. What makes injection molding truly impressive is its ability to consistently reproduce parts with exceptional accuracy and precision. It finds application in diverse industries such as automotive, medical, consumer goods, and electronics, just to name a few.
Understanding the right parameters for injection molding of PC is crucial for optimal product quality. Here’s an overview:
Safety Helmets: The high impact resistance of PC makes it an ideal material for manufacturing safety helmets, which are extensively used in construction, sports, and other fields requiring head protection.
Electronic Device Casings: Including casings for computers and headphones, the application of PC material provides a solution that is lightweight, durable, and aesthetically pleasing.
The process of rapid injection molding prototyping initiates with the development of a 3D CAD model representing the desired part. This CAD file serves as the foundation for fabricating a mold, which can be either machined or generated through 3D printing. Subsequently, the mold is inserted into an injection molding machine, where molten plastic is injected into the mold cavity, resulting in the creation of the desired part.
Flame Retardant PC: The addition of flame retardants improves PC’s flame retardant properties. Unmodified, PC has a V2 flame retardant rating, insufficient for many products. With added flame retardants, it can reach a V0 rating. Flame retardants can be halogenated or non-halogenated.
GETTING A QUOTE WITH LK-MOULD IS FREE AND SIMPLE.
FIND MORE OF OUR SERVICES:
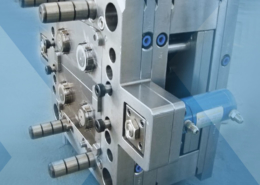
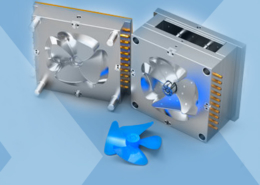
Plastic Molding

Rapid Prototyping
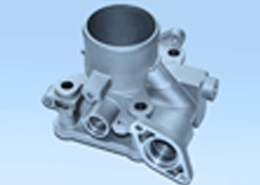
Pressure Die Casting
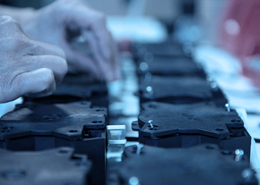
Parts Assembly
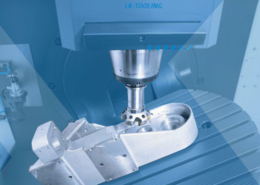