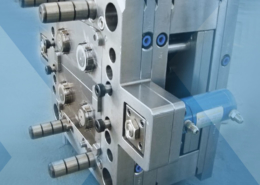
DIY Guide for molding plastic at home in 2021: 3 Simple Steps - molding plastic
Author:gly Date: 2024-10-15
Since polyethylene PE material is a crystalline polymer, the grains have to absorb certain heat when melting, so the barrel temperature should be 10 degrees higher than its melting point.
Increasing the injection pressure is conducive to the melt filling the mold, due to the good fluidity of PE, so in addition to thin-walled slender products, should be fine to choose a lower injection pressure, the general injection pressure of 50 ~ 100MPa. simple shape. After the wall of larger plastic parts, injection pressure can be lower, and vice versa is high.
Solution: Ensure proper drying of the material and optimize processing parameters such as temperature, injection speed, and holding pressure to ensure adequate packing and cooling time.
Post-Molding Operations: Annealing or conditioning parts post-molding can help relieve internal stresses and reduce shrinkage or warping.
The higher the molecular weight, the more difficult it is to process. The melting point of polyethylene PE material is 100-130C, and its low-temperature resistance is excellent. It can still maintain good mechanical properties at -60℃, but the use temperature is 80~110℃.
While PA66's superior properties make it an excellent choice for various applications, addressing the injection molding challenges is crucial for achieving high-quality parts. By understanding and implementing the solutions to common issues such as moisture absorption, overheating, shrinkage, and warping, manufacturers can significantly improve the quality and consistency of PA66 molded parts. Advanced techniques and post-molding operations further enhance the material's performance, ensuring that the benefits of PA66 can be fully realized in the final products.
Polyethylene PE material is a typical thermoplastic, which is an odorless, tasteless, non-toxic, and flammable white powder. Polyethylene PE material for the molding process is extruded and granulated waxy granule material with a milky white appearance. Its molecular weight is in the range of 10,000 to 100,000.
At the plastic injection molding and processing temperature, the melt will also decrease in its kill degree due to oxidation, and discoloration and streaking will occur, so care should be taken during the molding and processing and use process or when selecting materials.
Solution: Optimize mold design with uniform wall thickness and use cooling fixtures or jigs immediately after ejection. Consider the orientation of fibers (in the case of reinforced grades) during the design phase to minimize warping.
Polyamide 66 (PA66), also known as Nylon 66, is a type of polyamide or nylon used extensively in the injection molding industry due to its superior mechanical properties, heat resistance, and durability. However, like all materials, PA66 presents specific challenges during the injection molding process. This article discusses common issues associated with PA66 injection molding and offers practical solutions to these problems.Common Injection Molding Issues with PA66Moisture Absorption:Problem: PA66 absorbs moisture from the air, which can lead to hydrolysis during processing, resulting in molecular degradation and a decrease in mechanical properties.Solution: Pre-dry PA66 pellets before processing. Recommended drying conditions are 80°C for at least 4 hours. A desiccant dryer is preferred to ensure the material is thoroughly dried.Overheating:Problem: PA66 is sensitive to overheating, which can cause degradation of the polymer, leading to discoloration and reduced physical properties.Solution: Optimize the processing temperatures. Maintain a controlled barrel temperature profile and avoid excessive shear by adjusting the screw speed and back pressure.Shrinkage and Warping:Problem: PA66 experiences significant shrinkage, which can lead to warping or dimensional inaccuracies in the molded parts.Solution: Optimize mold design with uniform wall thickness and use cooling fixtures or jigs immediately after ejection. Consider the orientation of fibers (in the case of reinforced grades) during the design phase to minimize warping.Silver Streaks and Splay Marks:Problem: Moisture or improper venting can lead to surface defects such as silver streaks or splay marks.Solution: Ensure the material is properly dried and maintain adequate venting in the mold. Adjust injection speed and pressure to minimize the introduction of air into the melt.Brittleness:Problem: Incorrect processing parameters or excessive moisture content can result in brittle parts.Solution: Ensure proper drying of the material and optimize processing parameters such as temperature, injection speed, and holding pressure to ensure adequate packing and cooling time.Advanced SolutionsMold Flow Analysis: Conducting a mold flow analysis can help predict and address potential issues related to filling, cooling, and warping before the mold is manufactured.Gas-Assisted Injection Molding: This technique can be used to reduce warping and sink marks by introducing a gas (typically nitrogen) into the melt to pack the part during the holding phase.Fiber Orientation Control: For fiber-reinforced PA66, controlling the orientation of the fibers can significantly improve the mechanical properties and reduce warping.Post-Molding Operations: Annealing or conditioning parts post-molding can help relieve internal stresses and reduce shrinkage or warping.ConclusionWhile PA66's superior properties make it an excellent choice for various applications, addressing the injection molding challenges is crucial for achieving high-quality parts. By understanding and implementing the solutions to common issues such as moisture absorption, overheating, shrinkage, and warping, manufacturers can significantly improve the quality and consistency of PA66 molded parts. Advanced techniques and post-molding operations further enhance the material's performance, ensuring that the benefits of PA66 can be fully realized in the final products.
50-95C. Higher mold temperatures should be used for wall thicknesses below 6mm and lower mold temperatures for wall thicknesses above 6mm.
The molecular weight over 100,000 is ultra-high molecular weight polyethylene PE material. The higher the molecular weight, the better the physical and mechanical properties, and the closer to the level of engineering materials required.
Because polyethylene PE material has the above qualities and is easy to process and mold, polyethylene PE material recycling is of great value.
Polyethylene PE material under the action of the atmosphere, sunlight, and oxygen will be aging, discoloration, cracking, brittle or chalking, and lose its mechanical properties.
Mold temperature has a greater impact on the crystallization condition of the plastic parts, high mold temperature, high crystallization of the melt, high strength, but shrinkage will also increase. Usually, LDPE mold temperature control at 30 ℃ ~ 45 ℃, while the HDPE temperature is correspondingly higher at 10 ~ 20 ℃.
Gas-Assisted Injection Molding: This technique can be used to reduce warping and sink marks by introducing a gas (typically nitrogen) into the melt to pack the part during the holding phase.
Solution: Optimize the processing temperatures. Maintain a controlled barrel temperature profile and avoid excessive shear by adjusting the screw speed and back pressure.
Problem: PA66 experiences significant shrinkage, which can lead to warping or dimensional inaccuracies in the molded parts.
The barrel temperature is mainly related to the density and melt flow rate of polyethylene PE material, but also to the type and performance of the injection molding machine and the shape of the first-level plastic part.
For LDPE, the barrel temperature is controlled at 140-200℃, and the barrel temperature of HDPE is controlled at 220℃, with the rear of the barrel taking the minimum value and the front taking the maximum value.
Polyamide 66 (PA66), also known as Nylon 66, is a type of polyamide or nylon used extensively in the injection molding industry due to its superior mechanical properties, heat resistance, and durability. However, like all materials, PA66 presents specific challenges during the injection molding process. This article discusses common issues associated with PA66 injection molding and offers practical solutions to these problems.
The cooling temperature of the part should be uniform to minimize the difference in shrinkage rate. For optimal cycle time, the cooling cavity diameter should be not less than 8mm and the distance from the mold surface should be within 1.3d (where “d” is the diameter of the cooling cavity).
DGMF Mold Clamps Co., Ltd mainly offers a wide range of Mold Clamps and Mold Components. Used in processing machinery especially on plastic injection molding machines, and pressure dies casting machines.
Solution: Ensure the material is properly dried and maintain adequate venting in the mold. Adjust injection speed and pressure to minimize the introduction of air into the melt.
Besides the What is the Polyethylene PE material plastic injection molding process article, you may also be interested in the below articles.
Problem: PA66 absorbs moisture from the air, which can lead to hydrolysis during processing, resulting in molecular degradation and a decrease in mechanical properties.
Problem: PA66 is sensitive to overheating, which can cause degradation of the polymer, leading to discoloration and reduced physical properties.
Solution: Pre-dry PA66 pellets before processing. Recommended drying conditions are 80°C for at least 4 hours. A desiccant dryer is preferred to ensure the material is thoroughly dried.
Mold Flow Analysis: Conducting a mold flow analysis can help predict and address potential issues related to filling, cooling, and warping before the mold is manufactured.
Fiber Orientation Control: For fiber-reinforced PA66, controlling the orientation of the fibers can significantly improve the mechanical properties and reduce warping.
GETTING A QUOTE WITH LK-MOULD IS FREE AND SIMPLE.
FIND MORE OF OUR SERVICES:
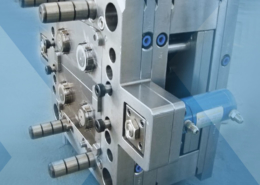
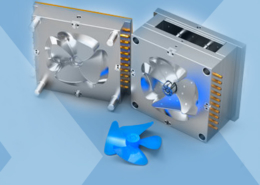
Plastic Molding

Rapid Prototyping
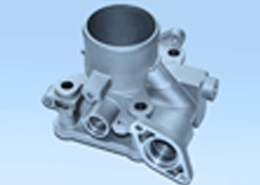
Pressure Die Casting
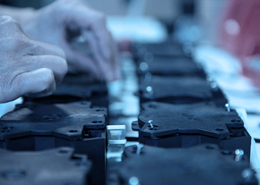
Parts Assembly
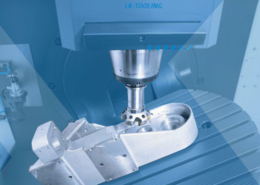