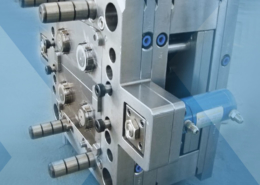
Custom Plastic Moulding Cost | Blog - custom plastic molding cost
Author:gly Date: 2024-10-15
Implantable and bioresorbable materials pose unique preparation, processing, and handling challenges. As a pioneer with these materials, we have expertise and dedicated resources for manufacturing implantable and bioresorbable plastic components.
Based in Melbourne, our plastic manufacturers work according to programmed production schedules, which are often linked to customer Kanban requirements in Australia and overseas.
Forme Technologies are well versed with the concepts of scientific moulding as well as the associated statistical work that goes into understanding a good moulding outcome. We can also perform designed experiments and various in-depth process analyses such as SPC analysis.
Multishot injection molding requires expertise in material interactions and understanding of how to combine multiple materials in one mold. We have the capability to support complex components from concept to production.
Discuss your requirements with the team at Forme Technologies and discover why firms across Melbourne and around Australia and Globally trust us to help them achieve their business goals.
PI – polyimide PEI – polyetherimide PEEK – polyetheretherketone PSU – polysulphone PC – polycarbonate PPO – polyphenyleneoxide PET-G – polyethylene terephalate (glycol modified) PMMA – polymethylmethacrylate (acrylic) POM – polyoxymethylene (acetal) ABS – acrylonitrile butadiene styrene PC-ABS – polycarbonate and acrylonitrile butadiene styrene PP – polypropylene PE – polyethylene
Polyetheretherketone (PEEK) is a high-strength, high-temperature thermoplastic with superior mechanical and chemical properties ideal for injection molding applications.
Our manufacturing processes are mostly injection moulding and associated processes. We currently operate machines ranging from 35 to 450 tonnes. In order to stay abreast of injection mouldings constantly emerging technologies, our most recent machine additions have been all electric, state of the art machines with every bell and whistle imaginable.
Plastic Injection Moulding is the manufacturing process we use to mass produce complex or simple plastic parts. Heated plastic is pressured into a mould to form different parts and products. The process requires a moulding machine where plastic granules are poured into a hopper and are then heated through the machine and injected into a pressured mould, often called a tool. For over 20 years, we have earned an excellent reputation in comprehensive plastic injection moulding services.
We're experience in moulding some of the most difficult and sophisticated engineering polymers on a daily basis with minimal scrap rates.
Injection mold prototyping is the process of developing a tool to expedite a molded part. Spectrum can create your part as close to the intended product design and functionality as possible using your requirements.
As medical treatments become less invasive, medical devices are getting smaller. We have the expertise to do precision micromolding, including specialized equipment, tool designs, and measurement systems.
We are an ISO 9001 and ISO 13485 accredited business. ISO 13485 is the standard required for the manufacturing of medical devices.
Spectrum is the starting point for medical device development requiring critical components. Our off-the-shelf tubing and components are available in our Component Webstore to accelerate the design and development of your next project.
One of Australia’s leading plastic products manufacturers, Forme Technologies has a wealth of knowledge on moulding for electroplated applications. This involves new materials and an even greater level of part scrutiny and control.
Our silicone molding capabilities include liquid injection molding as well as silicone rubber transfer molding, overmolding, and liquid injection molding.
We have built an excellent reputation for achieving superb quality on every project, no matter how unique, unusual, or complex. We are ranked in the top percentile for quality and delivery standards with our local and international customers. We are both ISO 9001 and ISO 13485 accredited business.
Our injection-molded solutions include premium, high-quality components and fully assembled medical devices. We have years of experience with complex molding projects working with highly engineered performance medical plastics.
The cost of manufacturing will depend on the complexity of the project. We go to great lengths to specify and cost manufacturing according to customer budgets and to maximise the product yields and net return on investments.
As a single-source partner, we can support your complex surgical device throughout the product lifecycle, from design for manufacturability to development to validation and manufacturing.
Most products we develop require a high level of engineering input, which means we specify the best engineering materials available. We work with commodity plastics and exotically engineered materials. Some materials are unique to us in Australia. We regularly use and specify materials that are either UL compliant or conform to the ISO 10993 certification for medical and food applications. The materials we use include:
We have decades of experience molding onto metal and other substrates. Combining properties of different materials, such as strength and flexibility, can create more intricate designs for aesthetics, branding, or ergonomics.
We are committed to reducing our environmental impact and making ongoing improvements in the way we run our business. More than half our operation is now powered by solar energy and conditioned by a new power factor correction system.
GETTING A QUOTE WITH LK-MOULD IS FREE AND SIMPLE.
FIND MORE OF OUR SERVICES:
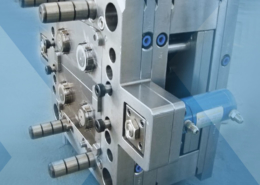
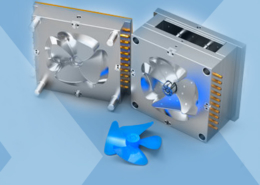
Plastic Molding

Rapid Prototyping
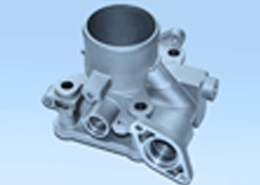
Pressure Die Casting
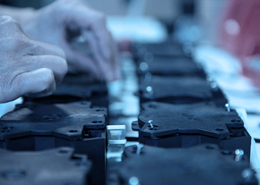
Parts Assembly
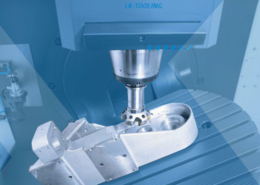