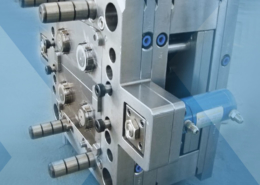
Custom Plastic Moulding - plastic injection manufacturing
Author:gly Date: 2024-10-15
To ensure a high-quality surface finish, ACE's expertise in mold texturing helps clients choose the right texture for their specific application.
2. Gate Design: Proper gate design is the key to controlling flow and pressure during the injection process. Work closely with ACE engineers to determine the ideal gate type and location for your specific project.
To combat warping and shrinkage issues, ACE engineers pay careful attention to material selection, cooling channel design, and the overall mold structure. These factors are vital in minimizing these defects.
The location of the parting line is crucial in preventing flashing and parting line marks. ACE works closely with clients to optimize parting line placement during the design phase.
Plastic thin-wall food boxes are designed to be space-efficient. They can be stacked neatly, taking up minimal storage space, and making them a practical choice for restaurants, kitchens, and food service establishments. In addition to efficient storage, these boxes are ideal for storing leftovers, and since they can be reheated in the box, they promote sustainability by reducing the need for additional containers or wraps. Labeling these containers for easy identification is a breeze, streamlining your kitchen organization.
When it comes to manufacturing plastic parts on a large scale, injection molding is the go-to method. A critical component of this process is the injection molding die, which plays a pivotal role in shaping the final product.
9. Prototype and Test: Before mass production, create a prototype and conduct thorough testing to validate your design. ACE can help with prototyping and assist in making necessary adjustments.
At the heart of Sussex Injection Molding lies a commitment to leveraging advanced technology to streamline processes and enhance efficiency. The company boasts a comprehensive suite of injection molding machines, ranging from small-tonnage to large-tonnage presses, capable of accommodating a diverse range of production requirements. Additionally, its utilization of automated robotic systems ensures precision and consistency in every molded component, minimizing defects and maximizing productivity.
DongGuan Company Room 103,#41 Lian Ma Road,Dalingshan Town,Dongguan City,Guangdong Province,China ShenZhen Company Building 5,Juhui Mold Industrial Park,Tianliao Com,Yutang St,Guangming District,ShenZhen City, China
Injection molding stands as a cornerstone in the realm of plastic manufacturing, with Sussex Injection Molding emerging as a beacon of innovation and excellence within this domain. Founded in 1977, Sussex Injection Molding has carved a niche for itself by consistently delivering high-quality, precision-engineered plastic components across various industries. This article endeavors to explore the intricate workings of Sussex Injection Molding, shedding light on its processes, capabilities, and contributions to the field of plastic manufacturing.
1. Optimized Cooling Channels: Effective cooling is essential to maintain consistent quality. Design cooling channels for efficient heat dissipation to prevent warping or other defects in the final product.
4. Parting Line Placement: Carefully consider the location of the parting line to ensure minimal flashing and parting line marks on the final product. ACE's expertise in die design can help you optimize this aspect.
At every stage of the manufacturing process, ACE conducts quality checks and inspections to ensure the die meets the desired specifications. This includes checks for proper material hardness, dimensional accuracy, and surface finish.
In conclusion, Sussex Injection Molding stands as a testament to the transformative power of innovation and dedication. From its humble beginnings to its status as a trailblazer in the industry, the company exemplifies excellence in every facet of its operations. As it continues to push the boundaries of possibility and redefine the standards of plastic manufacturing, Sussex Injection Molding serves as an inspiration to aspiring entrepreneurs, industry professionals, and environmental advocates alike.
Before handing over the die to the client, ACE conducts extensive testing and validation processes to ensure it performs flawlessly during the injection molding process. This includes verifying the cooling system's efficiency, gate functionality, and overall mold performance.
Material Selection: The choice of material for your injection molding die is crucial. ACE recommends using high-quality steel, such as P20, H13, or S136, to ensure longevity and precision.
The journey from an idea to a functional injection molding die is a well-coordinated process. ACE follows these key steps to ensure the highest quality dies:
ACE injection Moulding Company is an ISO 9001: 2015 certified mould manufacturer, providing services to the global plastic injection moulding industry.
Tolerances are critical in maintaining consistent product quality. ACE's precision tooling and quality control measures help minimize dimensional variability.
6. Tolerance Analysis: Pay meticulous attention to tolerances in your die design. ACE recommends using tight tolerances for critical dimensions while allowing for looser tolerances in less critical areas to maintain cost-effectiveness.
Looking ahead, Sussex Injection Molding is poised to continue its legacy of innovation and leadership in the plastic manufacturing industry. With a steadfast commitment to technological advancement, customer satisfaction, and environmental sustainability, the company remains primed to tackle the challenges and opportunities that lie on the horizon. By staying true to its core values and embracing emerging trends, Sussex Injection Molding is well-positioned to shape the future of plastic manufacturing for generations to come.
7. Mold Texture: The texture of the mold surface directly affects the appearance of the final product. Collaborate with ACE to determine the ideal texture for your specific application, whether it's matte, glossy, or textured.
Quality lies at the core of everything Sussex Injection Molding does, underpinned by rigorous quality assurance processes and stringent adherence to industry standards. From material selection to final inspection, every step of the manufacturing process is meticulously monitored and controlled to uphold the highest standards of quality and consistency. This unwavering commitment to excellence has earned the trust and loyalty of clients across a myriad of industries.
The process starts with meticulous design and engineering. ACE's team of experts collaborates closely with the client to understand the project requirements, material choice, and design specifications. Using advanced software and industry expertise, they craft the initial design, keeping in mind the top 10 tips mentioned earlier.
In this blog, we will explore the world of injection molding dies, specifically focusing on ACE, a renowned injection molding die manufacturer. We will delve into the top 10 tips for designing an effective injection molding die, walk you through the journey from concept to creation, and address common challenges in the manufacturing process and how to overcome them.
Once the prototype is approved, ACE proceeds with manufacturing the actual injection molding die. They utilize state-of-the-art machinery and precision tools to create the die with the utmost attention to detail.
Even with careful planning, challenges can arise during injection molding die manufacturing. ACE has a proactive approach to overcoming these challenges:
After finalizing the design, ACE creates a prototype die to test and validate the design's functionality and efficiency. This step is critical for making any necessary adjustments before moving forward.
ACE, as a leading injection molding die manufacturer, excels in designing, manufacturing, and troubleshooting injection molding dies. By following the top 10 design tips, adhering to a systematic manufacturing process, and addressing common challenges, ACE guarantees top-quality dies that meet the demanding requirements of the injection molding industry. Whether you're in the automotive, medical, or consumer goods industry, ACE is a trusted partner in the world of injection molding die manufacturing.
8. Mold Maintenance: Regular maintenance is the key to prolonging the life of your injection molding die. ACE provides maintenance guidelines and services to keep your die in optimal condition.
The impact of Sussex Injection Molding extends far beyond the confines of its facilities, reverberating throughout the plastic manufacturing industry. Through its relentless pursuit of innovation and excellence, the company has not only elevated industry standards but also catalyzed advancements in material science, process optimization, and product development. Its contributions have not only reshaped the landscape of plastic manufacturing but also empowered businesses to thrive in an increasingly competitive market.
Sussex Injection Molding traces its roots back to humble beginnings, founded with a vision to revolutionize plastic manufacturing. Established in Sussex, Wisconsin, the company embarked on a journey fueled by a commitment to quality, innovation, and customer satisfaction. Over the years, it has evolved from a modest operation into a state-of-the-art facility equipped with cutting-edge technology and a team of skilled professionals dedicated to pushing the boundaries of possibility.
DongGuan Company Room 103,#41 Lian Ma Road,Dalingshan Town,Dongguan City,Guangdong Province,China ShenZhen Company Building 5,Juhui Mold Industrial Park,Tianliao Com,Yutang St,Guangming District,ShenZhen City, China
Inadequate venting can lead to gas traps and burning. ACE ensures that the molds they produce have optimal venting, and they also advise clients on proper maintenance to prevent vent clogging.
One of the key advantages of ACE's Thin Wall Food Box is its lightweight construction. These boxes are specifically designed to be easy to handle, making them a preferred choice for food storage, transport, and service. Their low weight ensures that food remains fresh, preventing spoilage and waste. These boxes are also suitable for meal prepping, allowing you to portion out meals and organize your food efficiently.
5. Venting: Adequate venting is necessary to allow gases to escape during the molding process. Proper vent design is crucial to avoid defects like burning or gas traps. ACE has a long-standing commitment to ensuring optimal venting in their molds.
One of the hallmarks of Sussex Injection Molding is its ability to provide custom solutions tailored to meet the unique needs of each client. Whether it's prototyping, design optimization, or full-scale production, the company works closely with clients to develop bespoke solutions that align with their specifications and objectives. This personalized approach not only fosters strong partnerships but also ensures the delivery of superior-quality products that exceed expectations.
3. Draft Angles: Incorporating draft angles into your design is essential to facilitate easy ejection of the molded part. ACE suggests a minimum draft angle of 1-2 degrees for most applications.
In an era where environmental sustainability is paramount, Sussex Injection Molding stands at the forefront of environmentally conscious manufacturing practices. The company is dedicated to minimizing its ecological footprint by implementing eco-friendly materials, optimizing energy usage, and reducing waste generation. By embracing sustainable solutions, Sussex Injection Molding not only fulfills its corporate responsibility but also sets a precedent for eco-friendly manufacturing practices.
GETTING A QUOTE WITH LK-MOULD IS FREE AND SIMPLE.
FIND MORE OF OUR SERVICES:
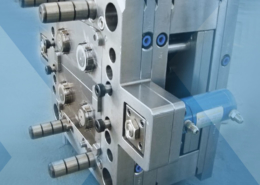
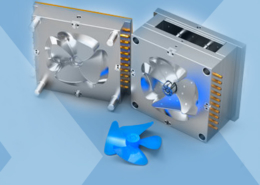
Plastic Molding

Rapid Prototyping
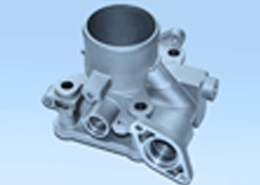
Pressure Die Casting
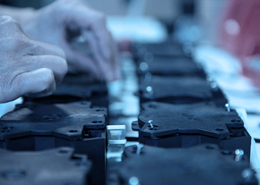
Parts Assembly
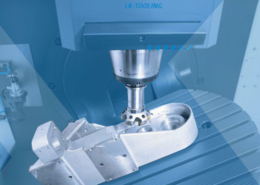