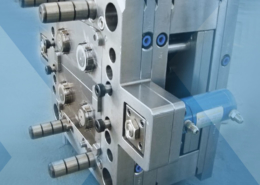
Custom EVA Foam Injection Molding Services - J-CAD Inc. - injection molded foam
Author:gly Date: 2024-10-15
This webinar will provide an overview of new developments in hot runners, controllers, mold components, predesigned molds, process monitoring and mold maintenance equipment. These advancements are designed with the goals of lowering scrap rates, optimizing process temperatures and managing energy consumption. The solutions also aim to support productivity and may contribute to extending the operational lifespan of tooling equipment. Agenda: Innovative undercut and thread-forming components Predesign mold bases and plate control Melt delivery and control solutions Process monitoring and maintenance
Gerardo (Jerry) Miranda III, former global tooling manager for Oakley sunglasses, reshares his complete mold design checklist, an essential part of the product time and cost-to-market process.
When used for conformal cooling in plastic injection, 3D printing opens a wide range of design freedom. This design freedom enables designers to develop highly-efficient thermal regulation networks. However, this blessing also comes at the expense of not only higher manufacturing cost but also higher design cost as the designer could spend weeks to develop optimal cooling channels. This webinar will explore strategies and tools — including SimForm, a front-end thermal simulation app — to help tool designers and tooling managers maximize the benefits of 3D printing while minimizing manufacturing and design costs. Agenda: 3D printing applied to the plastic injection industry 3D printing pros and cons Tools and methods to facilitate the integration of 3D printing
Fig. 4 - At 81-percent filling (left), Cavity 1 is already filled by the skin material, so there is no room for the core material. It must flow into Cavities 2 and 3.
Fig. 6 - Cavity design influences the skin/core distribution in multi-cavity co-injection-molded products. Here, Model 2 shows that if the angle of the 45-degree runners in Model 1 is modified to a more symmetrical design, a more uniform skin/core distribution can be achieved. If a runner structure with a 45-degree angle cannot be revised, a connector can be added between each cavity to ensure better skin/core distribution, as shown in Model 3.
Released earlier, this video remains a valuable recruitment tool and is being re-promoted in celebration of Manufacturing Day 2024.
Steel supplier discusses high thermal conductivity metal powders that also address the skills gaps via user-friendly materials and promote sustainability via durability and higher cycle counts.
Extrusion moulding is used when tubes or linear shapes are needed. The process begins with melting plastic pellets added to a plastic moulding machine. The plastic is poured into a hopper and passed via rotating screws through a heater into the machine’s barrel. The plastic is heated slowly to retain quality and the melting process is further helped by the friction and pressure inside the barrel.
The need for data to track information and the history of the mold-building process is ever-increasing, and mold component solutions can help.
Conversely, plastic injection moulding is ideal for the mass production of automotive parts, construction components, medical tubes, containers and packaging, electronics components, food and drink packaging, toys, bottles and cosmetics packaging.
Gerardo (Jerry) Miranda III, former global tooling manager for Oakley sunglasses, reshares his complete mold design checklist, an essential part of the product time and cost-to-market process.
Diamond compounds, with their varied grades, colors and base options, provide a comprehensive solution for mold builders in need of precise and superior polishing across diverse materials and applications.
Discover how CAD/CAM functionality tailored for the mold industry can significantly enhance the mold design process. In part three of the webinar series, Cimatron will focus on designing waterlines and cooling components. It will demonstrate how CAD/CAM tools can verify drill line depths for water lines and baffles, ensure that minimum steel requirements are met while placing water lines, and provide a complete list of all baffle cutoff lengths. Additionally, it will explore how to confidently design runners and gates using CAD functionality specifically developed for these aspects of mold design. Agenda: Waterlines and verification Conformal cooling Baffles and charts Runners and gates
Join MoldMaking Technology Editorial Director Christina Fuges as she gets the latest news on this mold builder's use of VR for mold design education.
The dynamic behavior of core material penetration in multi-cavity co-injection molding is a complex issue. Core material penetration is sensitive to injection flow rate, material properties and process conditions. In this experiment, flow patterns and core penetration were observed in a forked runner structure during multi-cavity co-injection molding. It showed that leading core penetration with a low-viscosity material is affected by the injection flow rate. Finding the transition point at which the leading core penetration switches from one branch to another is essential for understanding core penetration behavior.
To better manage the skin/core distribution in final molded products, it is necessary to consider the influence of cavity design. In Figure 6, for example, if the angle of the 45-degree runners in Model 1 can be modified to a more symmetrical design, a more uniform skin/core distribution can be achieved, as shown in Model 2. However, if the runner structure with a 45-degree angle cannot be revised, a connector can be added between each cavity to ensure better skin/core distribution, as shown in Model 3. This part of the experiment clearly demonstrates that cavity design does influence skin/core distribution in multi-cavity co-injection-molded products.
Fig. 3 - Here, the core material in the branch marked “1” reaches the cavity first when the injection flow rate is at 10 cubic centimeters per second. However, when the injection rate is increased to 16 cubic centimeters per second or higher, the core material in the branch marked “2” reaches the cavity first.
Discover how to enhance your mold design process with the right CAD/CAM tool for parting and cavity design. This webinar will explore CAD/CAM capabilities including how hybrid solid/surface modeling can streamline workflow and improve accuracy. Learn how to confidently tackle parting, runoff, and shutoff, ensuring precision and efficiency in your designs. Agenda: Part analysis QuickSplit techniques Parting and runoff strategies Shutoff solutions
In ISO 9001 quality management systems, the Management Representative (MR) plays a crucial role. While the 2015 version of ISO 9001 no longer mandates this position, having a trusted management member serve as an MR remains vital for streamlining operations and maintaining quality standards.
It’s easy to imagine the advantages automation offers the moldmaking process, but it's challenging to change one’s mindset, develop a plan and invest.
In co-injection molding, the skin material is injected to fill a certain percentage of the mold and then the core material is injected to finish filling the part, at an established ratio of skin material to core material. This study used a skin-to-core ratio of 72-to-28 to validate the change in core penetration behavior.
Join this webinar where Hexagon will explore how state-of-the-art CAD/CAM technology can drive your business forward. Learn how to optimize tool paths, enhance design accuracy and reduce lead times with advanced simulation. Discover the power of automation and real-time data for continuous improvement. Tailored for mold and die manufacturers, this session offers actionable insights to boost productivity and quality. Don’t miss this opportunity to gain a competitive edge in progressive die manufacturing. Agenda: Key challenges in progressive die manufacturing Optimizing tool paths Enhancing mold and die design accuracy Reducing lead times with simulation Automating processes for greater efficiency Leveraging real-time data for continuous improvement
Engineers use properly preloaded bolts, blocks, springs and side-action cores to enhance functionality and reliability in various mechanical systems.
Fig. 2 - These cavity and runner geometries were used for a simulation experiment. Each of the three cavities (marked “1,” “2” and “3”) is 20 mm in diameter and 3.5 mm thick. The 5-mm wide primary runner is 59 mm long, and the three secondary runners are 18.2 mm in length.
Intralox's integration of the Alpha Laser ALFlak has significantly improved their tool room efficiency when it comes to difficult welds and urgent repairs.
A water-based, eco-friendly plastic mold cleaning system helps Rankine-Hinman Manufacturing restore flow rates and avoid big-ticket failures on complex and costly molds.
MoldMaking Technology addresses the complete lifecycle of the manufacture and maintenance of a mold—from design to first shot—by providing solutions and strategies to moldmaking professionals charged with designing, building and repairing molds. About Us
Identify pain points, tackle each one strategically and maintain flexibility to keep your moldmaking business on a path to growth.
Part two of this three-part series explains specific data that toolrooms must collect, analyze and use to truly advance to a scientific maintenance culture where you can measure real data and drive decisions.
Steel supplier discusses high thermal conductivity metal powders that also address the skills gaps via user-friendly materials and promote sustainability via durability and higher cycle counts.
Multi-cavity co-injection molding offers a great deal of flexibility in terms of part development. The ability to combine different materials or colors, for example, makes it an attractive option for the manufacture of automotive components and structural reinforcement products. Process benefits also include reduced material waste, decreased costs and improved part quality.
Extrusion moulding tends to be the popular choice for plastic tubing and pipe products. It is also commonly used for plastic films, thin sheeting and coatings, wire insulation, filaments and fibres. Some examples of applications that suit extrusion moulding particularly well include drinking straws, automotive fuel lines, gas and water pipes, window glazing, glass replacements and ‘blister’ packaging.
After attending IMTS, it's clear that the integration of advanced technologies is ready to enhance precision, efficiency and automation in mold manufacturing processes. It’s a massive event, so here’s a glimpse of what the MMT team experienced firsthand.
Fig. 5 - Validation results show that using high or low flow rate to manipulate core penetration behavior does not work.
Continued training helps moldmakers make tooling decisions and properly use the latest cutting tool to efficiently machine high-quality molds.
Fig. 1 - The distribution of the core and skin materials in this co-injection molded part was affected by the injection flow rate and the characteristics of those specific materials.
Simulation shows that, to be effective, these types of molds must be designed with consideration for how the materials will be distributed throughout them.
Co-injection molding involves injecting two resins simultaneously through a single gate to form a multi-layer molded part composed of a “skin” and a core material. The skin material is injected into the mold cavity first and is immediately followed by injection of the core material. As the skin material flows into the cavity, that material that covers the cavity walls freezes and the rest of the material flows down a center channel. When the core material enters the cavity, it displaces the skin material in the center of the channel, pushing the skin ahead, where it continues to freeze on the walls.
Formnext Chicago is an industrial additive manufacturing expo taking place April 8-10, 2025 at McCormick Place in Chicago, Illinois. Formnext Chicago is the second in a series of Formnext events in the U.S. being produced by Mesago Messe Frankfurt, AMT – The Association For Manufacturing Technology, and Gardner Business Media (our publisher).
The key to successful multi-cavity co-injection molding is a uniform distribution of core and skin materials throughout the molded part. This is difficult to achieve, however, and is strongly affected by material properties and process conditions. For example, the distribution of core and skin materials in the co-injection-molded part shown in Figure 1 was affected by the injection flow rate and the characteristics of those specific materials. The flow pattern of the core material should be uniform all the way back to, in this case, the “fork” runner structure.
Experimenting with Mold Geometries To find solutions to the challenges of designing an effective multi-cavity co-injection mold, we experimented with injection flow rate and cavity design, using a computer-aided engineering (CAE) tool to simulate and analyze potential molding scenarios. Figure 2 shows the cavity and runner geometries used for this simulation experiment, which were taken from a 2003 study conducted by W.M. Yang and H. Yokoi on the flow behavior of core material in a similar part. Each of the three cavities (marked “1,” “2” and “3”) is 20 mm in diameter and 3.5 mm thick. The 5-mm-wide primary runner is 59 mm long, and the three secondary runners leading to each of the cavities are 18.2 mm in length. The material used in this study for both the skin and the core was a general-purpose polystyrene.
A connected software solution streamlines the moldmaking process by providing a unified source of design data, enhancing efficiency and reducing errors, with five key steps benefiting from this integration.
After attending IMTS, it's clear that the integration of advanced technologies is ready to enhance precision, efficiency and automation in mold manufacturing processes. It’s a massive event, so here’s a glimpse of what the MMT team experienced firsthand.
Understanding and facing the moldmaking industry’s obstacles to growth requires a strategy focused on increased profitability.
There is a wide range of plastic resin and polymer types, each one with its own set of specific properties that render it suitable for different components and applications. For example, the finished plastic parts may need to be flexible or rigid, transparent or opaque, recyclable or single-use etc. Plastic moulding supplies may need to be resistant to corrosion, chemicals, wear and tear and so forth. Packaging and medical plastics must be hygienic. Some examples of polymers that are used in both manufacturing processes are:
Plastic injection moulding is a similar process involving plastic pellets being fed from a hopper into the main injection machine. From there, they are heated and melted into a liquid state. The liquid plastic then enters the mould cavity. This is a hollowed-out shape that has been designed to meet the customer’s bespoke specifications. The molten plastic coats the inside of the cavity and the thickness of the new component’s ‘walls’ is carefully calculated. Once the component is in place, the machine cools the plastic so that it solidifies. It is then extracted from the machine and checked for quality before the process begins again with the next component.
The plastic is formed into a rod and decontaminated before moving towards the die. This has been carefully measured and crafted to enable it to produce a plastic extruded tube of the required diameter. The tubing is then cooled with water and fans before being removed from the machine. Production can be continuous and is normally highly accurate.
Injection moulding advantages include the versatility and speed of the process. Almost any plastic component or shape can be produced, usually with short lead times. This versatility is down to the custom plastic moulding cavities that can be designed to suit almost any specification. The process enables flexibility around colour, material and texture. Costs are relatively low and there is little waste as excess plastic can be used again. Disadvantages include the fact that there are some design restrictions that must be navigated and accurate costing can be more difficult than with extrusion moulding. This is because the process is not continuous and could require multiple mould cavities to be made
Join MoldMaking Technology Editorial Director Christina Fuges as she gets the latest news on this mold builder's use of VR for mold design education.
It is great for producing several components that are identical to factory machinery parts or engine components that must align precisely with other sections of the machine or engine to work correctly. Finally, the process offers excellent versatility with regards to textures, finishes and opacity. So, it is ideal for plastic projects that require branding and attractive aesthetics.
After attending IMTS, it's clear that the integration of advanced technologies is ready to enhance precision, efficiency and automation in mold manufacturing processes. It’s a massive event, so here’s a glimpse of what the MMT team experienced firsthand.
MoldMaking Technology Editorial Director Christina Fuges sits down with Murphy Forsyth, GM – Injection Molding and Director Of Marketing for Zero Tolerance LLC in Clinton Township, MI.
In ISO 9001 quality management systems, the Management Representative (MR) plays a crucial role. While the 2015 version of ISO 9001 no longer mandates this position, having a trusted management member serve as an MR remains vital for streamlining operations and maintaining quality standards.
There are several types of plastic moulding processes that create different types of components and products. A good plastic moulding company will be able to advise on which method is the best suited to any particular project. Two popular methods are extrusion moulding and injection moulding. Both offer advantages and disadvantages when compared against each other. Additionally, both can produce high volumes of quality, cost-effective plastic components for use across multiple sectors. So, what is the difference between each plastic moulding process? let’s find extrusion versus injection moulding in detail.
A focus on electrode design and automation helps toolroom improve efficiency, reduce tooling costs and deliver higher quality products.
Steps to improve data-driven decision-making and key features of a cloud-based system for mold monitoring and asset management.
Overriding the CAM system when milling a series of lifter pockets helps to improve metal removal rate and increase feed rates.
Smart sensors and sophisticated process and measurement data management are driving intelligent moldmaking to new heights.
Discover how to enhance your mold design process with CAD/CAM software specifically tailored for the moldmaking industry. In part two of this webinar series, Cimatron will demonstrate how to intelligently design mold components, such as slides and lifters, using powerful CAD/CAM tools to accelerate the design process. Additionally, it will cover how to avoid errors and ensure design accuracy for ejector pins by checking clearance distances, calculating cutoff heights correctly, and thoroughly documenting all ejector components. Agenda: Slides Lifters Inserts Ejection pins and charts
However, penetration of the leading core material in the runner-filling stage does not guarantee proper skin/core distribution in the final molded product. Figure 4 shows very poor skin/core distribution. At a filled volume of 81 percent, Cavity 1 is already filled by the skin material, so there is no room remaining in that cavity for the core material. It must flow into Cavities 2 and 3. Note that using a high or low flow rate to manipulate core penetration behavior does not work. Figure 5 validates this phenomenon, showing an actual molding result.
After attending IMTS, it's clear that the integration of advanced technologies is ready to enhance precision, efficiency and automation in mold manufacturing processes. It’s a massive event, so here’s a glimpse of what the MMT team experienced firsthand.
Explore the standout articles of September, featuring innovations, expert insights, and strategies to boost efficiency and quality for your moldmaking needs.
Extrusion moulding offers many advantages, not least the ability to continuously produce long tubular components with a high degree of accuracy. This helps to lower production costs and reduce machine downtime. The manufacturing process enables any waste plastic to be gathered up and reused in a future project. Most extruded plastic products are recyclable too, helping companies to be more sustainable in their manufacturing goals. However, disadvantages include the fact that the plastic can swell when extracted from the die, so the distortion needs to be accounted for in initial calculations. It also has more limits on the type and shape of parts that can be created as compared with injection moulding techniques.
Designing these types of molds presents unique challenges, however. The same general guidelines used for developing a single-cavity co-injection mold cannot be fully applied to the design of a multi-cavity co-injection mold.
Figure 3 shows the flow-front penetration of the core material at various injection flow rates. Here, the core material in the branch marked “1” reaches the cavity first when the injection flow rate is at 10 cubic centimeters per second. However, when the injection rate is increased to 16 cubic centimeters per second or higher, the core material in the branch marked “2” reaches the cavity first. Using the low-viscosity polystyrene material and an injection flow rate of 16 cubic centimeters per second (at the skin/core ratio of 72-to-28) reveals a crucial transition flow rate when the leading core material penetration changes from Branch 1 to Branch 2. This transition can be attributed to the high shear stress in Branches 2 and 3, which results in more core material entering the second and third cavities.
GETTING A QUOTE WITH LK-MOULD IS FREE AND SIMPLE.
FIND MORE OF OUR SERVICES:
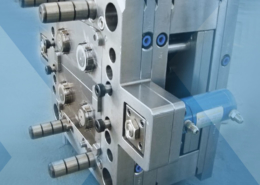
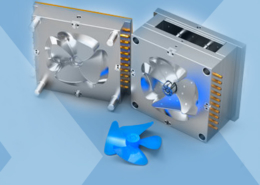
Plastic Molding

Rapid Prototyping
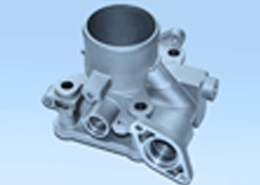
Pressure Die Casting
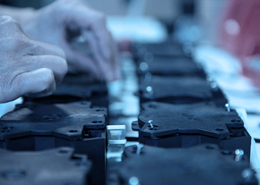
Parts Assembly
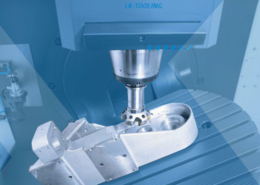