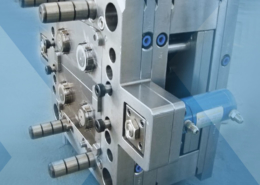
Custom Acrylic Injection Molding Company: PMMA Plastic ... - acrylic injection m
Author:gly Date: 2024-10-15
For more information on materials and machine settings in injection molding, refer to the Injection Molding Material Wikipedia page and the Injection Molding Machine Wikipedia page.
To explore more about efficiency measurement in injection molding, consider visiting the Injection Molding Process Wikipedia page.
My rough process would be: create molds (from unknown material) Manually mix and inject some kind of resin/thermoplastic into mold Repeat as necessary
Clamp Force: Essential for holding the mold closed during injection, clamp force (measured in tons) depends on the size of the mold and the material being used. Larger parts with more complex designs typically require higher clamp forces.
This is in a repair context so it needs to be moulded onto an existing item where the moulding process is the only thing bonding it on. The original plastic parts were POM.
Motor Power: Motor power, generally in the 15 to 50 kW range, is essential for driving the screw and melting the plastic.
Thermal Imaging Cameras: These are used to monitor barrel temperatures, ensuring optimal heat distribution and identifying potential issues like cold spots that can affect material consistency.
Plasticizing’s role in injection molding is crucial. It directly affects the mold filling characteristics and the end product’s quality. Proper plasticizing ensures that the plastic has an appropriate viscosity for even and complete mold filling, leading to products with consistent dimensions and structural integrity. This is vital for shortening cycle times, enhancing production efficiency, and lowering costs.
Data Logging and Analysis Software: This software tracks and analyzes machine parameters like cycle time, temperature profiles, and energy consumption, providing real-time insights into the efficiency of the plasticizing process.
To assess plasticizing efficiency in injection molding, several key metrics and performance indicators are crucial. Cycle Time is a primary metric, typically measured in seconds; the shorter the cycle time, the higher the efficiency, indicating a faster conversion of raw material into a molten state. Energy Consumption per Cycle, measured in kilowatt-hours (kWh), is another critical indicator. Efficient plasticizing processes consume less energy, often below 0.5 kWh per cycle for optimized systems. Material Consistency, evaluated through product quality checks, reflects the uniformity and stability of the plasticized material, directly impacting the final product’s quality.
Viscosity Measuring Devices: These tools measure the viscosity of the molten plastic, a critical factor in determining the efficiency of the plasticizing process. Ideal viscosity ranges are material-specific, but consistent readings are indicative of efficient plasticizing.
The quality of the plasticizing process directly impacts product quality and lifespan. Uniform melting ensures defect-free products, enhancing both aesthetic and functional attributes. Products with proper plasticizing exhibit enhanced mechanical properties and durability.
Screw Design: A crucial factor, where screws with optimal length-to-diameter ratios (around 20:1) provide enhanced melting and mixing.
Barrel Temperature Settings: Precise temperature control is crucial. Inadequate heating can lead to poor melting, while overheating can degrade the material. Most machines have multiple heating zones, each requiring specific temperature settings based on the material used.
Back Pressure: This affects the degree of mixing and melting. Higher back pressure, within a range of 5 to 20 bar, can improve color dispersion and material consistency but may increase wear on the screw and barrel.
Injection Speed and Pressure: These parameters, tailored to the specific material and product design, influence the quality of the final product. Higher speeds and pressures can reduce cycle times but may introduce defects if not properly managed.
For a deeper understanding of optimizing plasticizing processes, you can refer to the Injection Molding Optimization Wikipedia page.
Obviously very new to this field so I'm just trying to gather some info on which avenues to explore so any resources are much appreciated.
Screw Diameter and L/D Ratio: A larger screw diameter, typically ranging from 18mm to 150mm, can handle higher volumes of material, impacting the throughput rate and melting efficiency. The L/D (length to diameter) ratio, ideally between 20:1 and 24:1, is critical for effective plastic melting and mixing.
Efficient plasticizing significantly influences production costs and efficiency. Optimizing this process allows for faster cycle times and reduced energy use, leading to substantial cost savings. A 10% decrease in cycle time can lead to a similar reduction in production expenses. Furthermore, it can minimize material waste, enhancing cost-effectiveness.
Plasticizing capability in injection molding refers to the process of heating and melting plastic resin to make it fluid and ready for injection into a mold cavity, ensuring proper flow and filling.
Plasticizing in injection molding is the essential process where solid plastic pellets are transformed into a molten state, ready for molding. This process depends on a screw mechanism within the injection machine, combining heat and mechanical work to melt the plastic. Its efficiency plays a pivotal role in determining the quality of the molded product, ensuring the plastic’s uniformity and flow properties.
The configuration and settings of the injection molding machine significantly affect plasticizing. Key parameters include:
The choice of material plays a pivotal role in determining the plasticizing capability in injection molding. Different materials require distinct temperatures and pressures for effective plasticizing. For instance, polycarbonate needs temperatures around 280°C to 320°C, whereas polyethylene may melt effectively at temperatures as low as 180°C to 220°C. The viscosity of the material also dictates the required screw speed and back pressure, directly influencing the energy consumption. Materials with higher viscosity often need more power, potentially increasing the motor requirement up to 50 kW or more, depending on the size of the machine.
Energy Monitoring Systems: These systems track the total energy consumption of the injection molding machine, highlighting areas where energy efficiency can be improved.
What can be used to create a mold? It needs to be rigid so the moulded parts are in the correct place, as in silicon would give too much variation.
Barrel Temperature: Precision in controlling barrel temperatures, typically between 200°C and 300°C, is necessary for achieving the desired melt quality.
GETTING A QUOTE WITH LK-MOULD IS FREE AND SIMPLE.
FIND MORE OF OUR SERVICES:
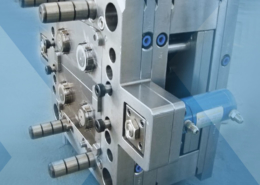
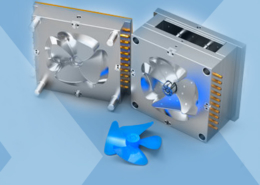
Plastic Molding

Rapid Prototyping
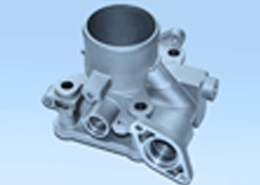
Pressure Die Casting
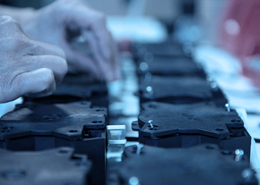
Parts Assembly
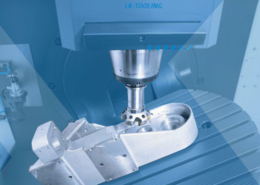