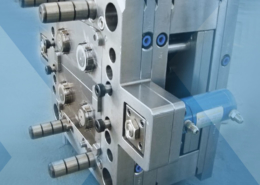
Creating Plastic Prototypes: What Are My Options? - prototype plastic
Author:gly Date: 2024-10-15
Direct processing of regrind in injection moulding requires more than 30% less energy for processing the recyclate, as regranulation is no longer necessary.
The use of recycled materials improves the CO2 balance. At the same time, contamination brings with it odour pollution and fluctuations in quality. With our innovative recycling processes for plastics, we are responding specifically to these challenges. ENGEL enables its customers to operate within a circular economy.
The regranulation of used plastics is an energy-intensive processing step in recycling. With our two-stage plastics recycling process, this step is skipped. Depending on the recyclate used, you save more than 400 Wh of energy per kilogram of plastic. This corresponds to a CO2 reduction of 30%.
Volatile components in the material such as gases or moisture are eliminated with our integrated degassing. Degassing enables a wider range of recyclates to be used, component quality without streaks and less tool build-up. Odour pollution is reduced enormously. Especially with lacquered components, you achieve beautiful surfaces thanks to degassing.
Production is done with one machine and in one cycle using film back-injection and flooding. For an efficient and simple process.
Internet Explorer is no longer supported. Please switch to a current browser to be able to use engelglobal.com to its full extent.
ENGEL is the first supplier to enable thin-wall injection moulding for PET. Realise high recycling rates directly on the injection moulding machine.
Produce thin-walled PET containers in just one process step. This is possible with the powerful injection unit of our e-speed injection moulding machine. This significantly expands the range of applications for PET and rPET.
The regranulation of used plastics is an energy-intensive processing step in recycling. With our two-stage plastics recycling process, this step is skipped. Depending on the recyclate used, you save more than 400 Wh of energy per kilogram of plastic. This corresponds to a CO2 reduction of 30%.
Filter systems reliably remove contaminants from the recyclate. Depending on the design, they protect plasticising, hot runner and mould. Suitable filter systems are offered for different degrees of contamination. This prevents clogging of the mould, hot runner and sprue channels by foreign parts. In addition, the component quality increases.
Take advantage of our expertise, plant engineering and technologies for processing plastic flakes or regranulate. We will be happy to advise you on the selection of the right plastics recycling process.
By integrating degassing, filtration and additivation into the injection moulding process, process-reliable processing is possible - even of contaminated recyclates.
Volatile components in the material such as gases or moisture are eliminated with our integrated degassing. Degassing enables a wider range of recyclates to be used, component quality without streaks and less tool build-up. Odour pollution is reduced enormously. Especially with lacquered components, you achieve beautiful surfaces thanks to degassing.
Filter systems reliably remove contaminants from the recyclate. Depending on the design, they protect plasticising, hot runner and mould. Suitable filter systems are offered for different degrees of contamination. This prevents clogging of the mould, hot runner and sprue channels by foreign parts. In addition, the component quality increases.
Bucket production on a duo speed with two injection units: PCR recyclate is injected in the core and virgin material in the outer skin.
Thanks to the integrated degassing, volatile accompanying substances are eliminated and a better component quality is achieved. Less fogging forms in the mould and the mould service life is increased.
Sandwich components offer a circular economy solution. Recycled plastic waste such as post-consumer waste can be hidden inside the product. The recyclate is not visible on the surface.
Design for recycling can be implemented with a visible high-quality outer skin and recycled material in the background. Our plastic recycling processes in the field of multi-component injection moulding are particularly suitable for this. Provided that the injection moulded part has the same polymer base. Produced components can be recycled again without any problems.
The two-stage injection moulding process enables a circular economy with minimal use of resources. Contaminated regrind is processed directly at the injection moulding machine. The material is degassed and filtered in the process. This eliminates an entire work step: regranulation. This significantly reduces costs and energy consumption.
From 2025, all plastic packaging must have a recycled content of at least 30% and be 100% recyclable. With our plastic recycling process, you meet the required quotas. In addition, they must be 100% recyclable.
Design for recycling can be implemented with a visible high-quality outer skin and recycled material in the background. Our plastic recycling processes in the field of multi-component injection moulding are particularly suitable for this. Provided that the injection moulded part has the same polymer base. Produced components can be recycled again without any problems.
With our injection moulding processes for the Circular Economy, you increase the recyclate content in the component. A recycling content of 50% is achieved with the skinmelt process. The percentage is much higher with the foilmelt process. In the two-stage process, no virgin material is used at all. The component thus consists of 100% recycled material.
In addition to the filtration of the material, the process enables gentle fibre processing. With the help of the high fibre lengths achieved, you can produce components that meet high mechanical requirements.
With our injection moulding processes for the Circular Economy, you increase the recyclate content in the component. A recycling content of 50% is achieved with the skinmelt process. The percentage is much higher with the foilmelt process. In the two-stage process, no virgin material is used at all. The component thus consists of 100% recycled material.
Internet Explorer is no longer supported. Please switch to a current browser to be able to use engelglobal.com to its full extent.
In film back injection moulding, the recycled material is bonded with a film. This happens directly in the mould during the injection moulding process. Only the film is visible on the surface. The product is significantly upgraded.
Post Consumer Recycled (PCR) plastic flakes are processed directly with ENGEL's two-stage process. The company AVK Plastics BV uses the technology to produce new pallets from shredded polyolefins. The customer saves costs and valuable energy through the plastic recycling process.
Foil back-moulding on a duo 350 with a roll-to-roll IML application. The film is fed via a roll, thermoformed on the machine and remains on the component.
GETTING A QUOTE WITH LK-MOULD IS FREE AND SIMPLE.
FIND MORE OF OUR SERVICES:
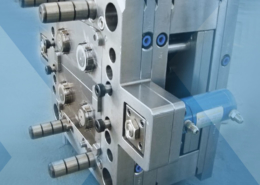
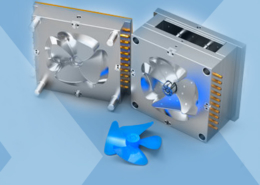
Plastic Molding

Rapid Prototyping
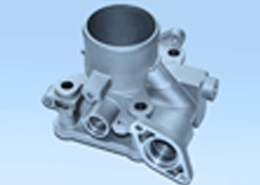
Pressure Die Casting
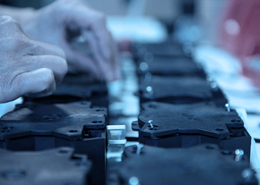
Parts Assembly
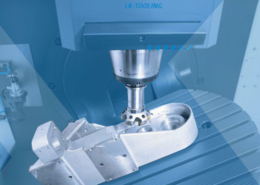